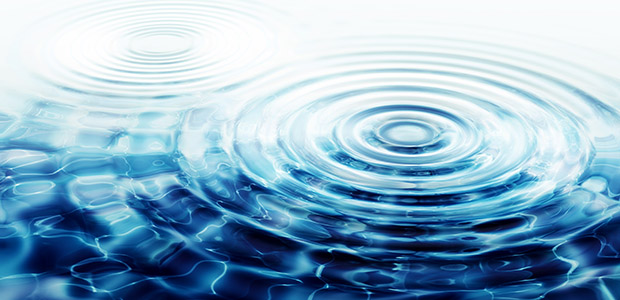
Water Management
Meters Key To Evaporator Technology
By Larry Johnson
HOUSTON–Water management is one of the most persistent challenges facing the oil and gas industry. For operators to get the products they want out of their producing reservoirs, they generally have to deal with substantial amounts of a byproduct they do not want: produced water.
All water that is delivered to the surface through a borehole is considered “produced,” including natural formation water as well as flowback fluids injected during fracture stimulation treatments. In conventional reservoirs, the volume of water produced per barrel of oil or thousand cubic feet of natural gas typically increases as a field matures, and the cost associated with handling and disposing of the water can have a major impact on the economic viability of older fields.
While shale gas and tight oil reservoirs typically do not yield large amounts of formation water, hydraulic fracturing is a water-intensive process and a substantial percentage of the water pumped during the stimulation phase can be flowed back during the production phase, primarily during the first few months.
The compositions and characteristics of produced water vary considerably, but produced water contains soluble and insoluble organic compounds, dissolved solids, production chemicals (corrosion inhibitors, surfactants, etc.) and solid particles. The majority of produced water streams are composed of naturally occurring formation brines. The quality of the water can range from brackish (defined as 5,000-35,000 parts per million of total dissolved solids) to saline (35,000-50,000 ppm TDS) and brine (more than 50,000 ppm TDS).
More and more operators are treating and recycling produced water as a standard best operating practice, but whether it is recovered and treated for reuse or transported to an off-site facility for treatment and disposal, the costs associated with handling produced water can adversely affect the economics of producing wells, thereby discouraging further development and leaving substantial reserves unrecoverable.
A typical producing field can generate tens of thousands of barrels of saltwater each day, constituting a critical waste stream that affects the bottom line for oil and gas companies. The cost of disposing of produced water, including transportation, capital requirements and infrastructure maintenance, can be as high as $10 a barrel. Of course, produced water streams generally have to be treated prior to reuse or disposal, adding to the economic considerations. The capital and operating costs associated with treatment systems can be quite high, underscoring the need for economical management of produced water.
Compounding the challenge is the fact that produced water can be chemically complex, and some of the many constituents in the production streams can be harmful to the environment and workers if not managed properly. With a growing focus on corporate responsibility and sustainability, having strategies in place to effectively and cost-efficiently manage wastewater has never been more important for oil and gas businesses.
New Solution
Consequently, operators are seeking to minimize the need to inject produced water at disposal sites and reduce water trucking costs, while increasing hydrocarbon production at the same time. This requires an effective solution for decreasing the volume of produced water at its original source.
Fortunately, innovations in produced water evaporation technology are providing operators with an efficient, economical and environmentally responsible new option for minimizing wastewater transportation and disposal. Key to this solution is the accurate measurement of the evaporation process provided by electromagnetic flowmeters.
A variety of technologies are available to treat produced water, and more are emerging every day. They range from the traditional approaches such as dissolved gas flotation, plate coalescers and gravity separators, to advanced electrodialysis membrane and evaporator crystallizer systems.
Advancements in evaporation technology have enabled a cost-effective solution for a variety of wastewater treatment and recycling applications, particularly where there are high total dissolved solids. A new breed of produced water evaporator technology has proven effective in solving wastewater disposal problems by reducing the volume of saltwater at or near the well site, and therefore the amount of water that must be hauled away by trucks.
Produced water evaporators employ a proprietary technology known as submerged combustion, which is a method of heating or evaporating liquids and slurries whereby the products of combustion are forced through the solution. In-field natural gas from the producing wells is used to fuel a flame with exhaust gases in direct contact with the produced water in order to evaporate the high-TDS, salty liquid into clean water vapor.
The result of this process is a dry solids cake that is deposited in a roll-off container, and then recycled, placed in a landfill, or used for commercial applications such as road salt or feedstock (Figure 1).
Unlike traditional wastewater management techniques, submerged combustion evaporation can be performed directly at the producing field. This eliminates the need for tanker trucks to remove liquid waste from the well site for injection into a disposal well. The amount of dry solids cake produced by evaporation is much smaller than the volume of produced water that would otherwise require disposal.
Flow Measurement
During the operation of a produced water evaporator, the volume of high-TDS water entering the system is metered, followed by a measurement of the amount of salt crystals or concentrated water exiting the unit. The delta of these two measurements then is used to calculate the evaporation total, which is the basis for a per-barrel service charge billed to the field operator (Figure 2).
In addition, a programmable logic controller can employ flow measurement information to automate the evaporation process and present relevant information on a human-machine interface. This solution allows for remote operation without the need for a full-time operator.
Initially, submerged combustion heating evaporators for high-total dissolved solids applications were employed using different types of flow measurement technologies. However, unacceptable performance was experienced with both ultrasonic and turbine-type meters.
Ultrasonic metering accuracy was difficult to maintain in the submerged combustion heating evaporator environment. Positioning and adjusting of the sensors was frequent, and the accuracy of data generated was always in question. Turbine meters were very accurate, but did not function well because of fouling. The meters became plugged or occluded with debris on a continual basis, and disassembly and cleaning required isolating the units from the storage tanks.
Ultimately, an electromagnetic flowmeter design was selected for the water evaporator system. This measurement technique eliminates the need for moving parts, which can lead to performance and maintenance issues when used in fluids containing high solids content. Electromagnetic flowmeters measure virtually any conductive fluid or slurry, including process water and wastewater. They are known for low pressure drop, high accuracy, extended turndown and excellent repeatability.
The electromagnetic flowmeter used in the first evaporator system is designed to achieve ±0.25 percent accuracy. Its nonintrusive, completely open flow tube design virtually eliminates pressure loss. The meter is relatively unaffected by viscosity, temperature and pressure when correctly specified.
In the first field application, a one-inch electromagnetic flowmeter was installed on the evaporator feed line coming from the storage tank to replace a turbine meter. Once the communications were determined, the electromagnetic meter was brought online and performed flawlessly. A three-inch electromagnetic flowmeter subsequently was installed on the discharge line of the evaporator to replace an ultrasonic meter. Both instruments have been running for more than a year without any problems, leading the manufacturer to design another 1,000 barrel/day unit that will use four-inch electromagnetic meters on all liquid measuring points.
As in other exploration and production processes in which the flow of liquids or gases must be measured accurately during every phase of operation, reliable flow measurement is key for submerged combustion heating evaporator technology. The electromagnetic meters provide precise data on the amount of produced water entering and exiting the evaporator system, and enable secure remote operation to simplify site personnel training and reducing overhead costs. Additionally, improved reliability, increased robustness and reduced maintenance requirements are achieved by deploying electromagnetic meter technology.
Benefits To Producers
A submerged combustion evaporator can help oil and gas companies reduce operational headaches by evaporating up to 95 percent of produced water. A true on-site evaporator represents a desirable alternative to hauling large amounts of produced water off site for treatment and disposal, and can augment on-site treating and recycling strategies. The specific operational, environmental and business benefits of this solution include:
- Fewer logistics for handling produced water;
- Reduced truck traffic to minimize site damage, liability and emissions;
- Less dependence on water haulers to eliminate scheduling delays and fees;
- Reduced flaring and less likelihood of spills or surface water contamination; and
- Reduced injection in disposal wells.
User experience has shown that submerged combustion evaporators that produce a dry solids cake or liquid concentrate byproduct reduce the costs associated with wastewater volume reduction by as much as 50 percent.
Oil and gas operators utilizing a submerged combustion evaporator can expect ongoing annual savings for the life of the well because of greater predictability and control of disposal costs. They also will have fewer regulatory and operational issues while avoiding unnecessary risks. Environmental benefits include a reduced carbon footprint from trucking and less stress on local infrastructure.

LARRY JOHNSON is a Badger Meter strategic account manager in Houston. Prior to joining the company in 2015, he served in sales and management positions at Petrosmith, Turbines Inc. and Kimray Inc. He holds a business administration and management degree from Louisiana State University-Eunice.
For other great articles about exploration, drilling, completions and production, subscribe to The American Oil & Gas Reporter and bookmark www.aogr.com.