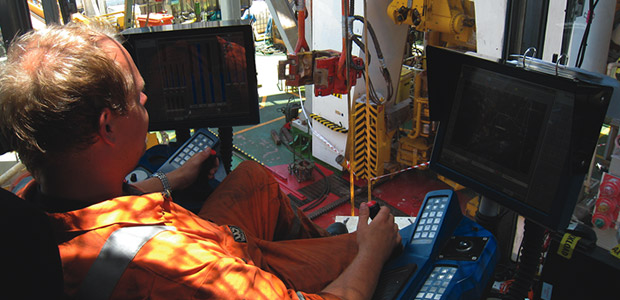
Automation Of Downhole, Surface Components Optimizes Drilling Process
By Tony Pink, Andrew Bruce, Hege Kverneland and Brad Applewhite
HOUSTON–After substantial industry research, an automated drilling system has been developed to improve operational safety while drilling a faster and better well. The significance of this technology is potentially vast to the oil and gas industry. Automated drilling can deliver huge performance improvements to the well construction process, help fill competency gaps, and enable new downhole technologies and surface solutions to be introduced much more rapidly.
The technology incorporates an open architecture for both downhole and surface components, and is designed to ensure economic viability in the onshore unconventional drilling market. The system is customer configurable, and allows the rig’s surface equipment to be controlled in response to downhole data streamed through wired drill pipe, mud pulse or electromagnetic (EM) telemetry methods.
Data are prioritized and distributed to appropriate applications as they enter the rig control system. The open architecture allows any party to create applications to control any specific part of the drilling process.
A case in point is an initial drilling optimization program that uses an advanced “auto driller” application controlled by downhole (rather than surface) data to optimize surface weight-on-bit, flow and rotations per minute by utilizing downhole WOB, torque and RPM. Sophisticated applications will be developed subsequently for vibration management, hole cleaning, equivalent circulating density (ECD) management, managed pressure drilling (MPD), kick detection, directional drilling, drilling efficiency, etc.
Increasingly, the challenge for operators is figuring out how to access resources and produce them in the shortest and most cost-effective way to maximize returns and expand the amount of economic reserves. Automating the well construction process has the potential to significantly reduce well costs by improving performance and increasing consistency while simultaneously enhancing rig safety.
Well optimization is an important process that all producers must perform in order to increase the efficiency of operations from the early planning stage to final production of the well. There is always a need to improve performance and reduce nonproductive time (NPT). Process optimization of the entire well construction process has a clear benefit for the future economics of oil and gas projects. The automated system was engineered to drill and produce a safer, faster and cheaper well while helping to maximize production.
Real-Time Optimization
The goal is to link surface and downhole data and information in an automated, intelligent way for real-time drilling optimization and other operations related to the well construction process. With current systems and services, critical and expensive downhole equipment can be several miles from the rig floor (especially with long laterals), making it impossible to know with any degree of accuracy their behavior and the surrounding bottom-hole conditions. Vibration, poor weight transfer and poor torque transfer typically reduce drilling performance by 40-50 percent.
Initial applications of integrated drilling automation are targeting onshore unconventional resource plays, but the technology has vast significance both onshore and offshore. The quantifiable benefits of real-time optimization through drilling automation include faster penetration rates, reduced risk of downhole problems such as fluid loss and stuck pipe, improved kick detection, increased ability to manage pressures and control ECD while drilling, fewer on-site personnel with related HS&E benefits, and a better well bore with less torque for easier completions.
In addition, harmful vibrations negatively impact the life of the drill string, bottom-hole assembly components and surface equipment, which in turn, can result in premature and catastrophic failures and costly downtime.
A great deal of effort is dedicated to understanding and mitigating vibration, but in most cases, engineers do not have sufficient data speed to understand what is occurring down hole in real time. This creates a clear real-time gap between downhole and surface data while drilling, which hinders a holistic optimization solution. Automating surface equipment using surface data can produce significant improvements in penetration rates, but the potential exists for a significant jump in performance when surface machine control is augmented by high-speed downhole data.
Damaging downhole vibrations, such as stick-slip and bit whirl, are not always detectable at surface. Stick-slip is an extreme form of torsional vibration that occurs when the bit digs into the formation, causing it to stick, which in turn, leads to drill string windup. Eventually, the drill string breaks free, overcoming the shearing force, and causing drill string rotation to go from zero to high instantaneous RPMs. Bit whirl is a form of lateral vibration that causes the bit to move off center and roll around the well bore. These are only two of a number of events that can cause NPT, and damage to the bit and drill string components.
Although memory-based multipositional vibration subs have captured such damaging events, the resulting analysis only brings value to subsequent wells if the well profile, design and parameters are similar to the benchmark well.
A downhole automated control system enables operators to react by changing drilling parameters in real time to reduce vibration and optimize the weight and torque parameters being applied to the bit. Industry research has documented numerous cases where real-time downhole measurements (provided by wireline in a test environment) were different than those at the surface, and also illustrate how drilling parameters can be modified in real time to increase efficiency.
There is a clear difference between drilling equipment mechanization and automation. Drilling equipment mechanization consists of an enabled rig capable of automating repetitive tasks on the drill floor, such as pipe handling and tripping. Automation of the drilling process, however, is defined as having an automated protocol fed directly by on-bottom and surface data to increase uptime and efficiency.
Requirements And Benefits
Before designing the automated well construction system, substantial research was conducted to define the major requirements. Various representatives from operators, drilling contractors and service companies were surveyed to determine the need for improving operational efficiencies, reducing NPT and increasing the overall quality of wells drilled. Everyone interviewed echoed a desire for collective improvements that would result in a significant increase in drilling performance, with some mentioning a benchmark of 30 percent. Table 1 ranks generalized categories of drilling issues in order of importance from the responses received.
The quantifiable benefits through a real-time, integrated optimization service can be grouped under four general categories:
- Improved ROP;
- Reduced risk (i.e., hole cleaning, stuck pipe, surge/swab, losses, kick detection, and managed pressure drilling assistance);
- Fewer personnel with related travel costs and health, safety and environmental benefits (remote directional drilling, cementing, mud logging, etc.); and
- A smoother, cleaner well bore with less torque for deeper, longer sections and less breakout for better ECD control and easier-to-run completions.
Part of the development strategy was to ensure that the technology would be economically viable in the onshore unconventional drilling market with the understanding that if the system could pass the tough financial hurdle of providing clear economic benefits on land in unconventional resource plays, then it was sure to deliver substantially greater well cost reduction in the high-day-rate offshore world. Accordingly, it was decided that the early prototypes would be built for the land market, where safety risks during the early phases are substantially reduced, and designed so that it would be capable of being retrofitted onto existing land and offshore rigs, as well as new builds.
System Design
One of the keys to automated drilling technology (Figure 1) is the ability to use a common control system platform on every type of rig so that crews do not have to be retrained when moving from rig to rig. The control system also enables any party to easily plug into the system and provides a uniform environment for others to deliver applications that run on it. The look and feel of the user interface is the same for all rigs to help with rapid familiarization of the controls.
In the long term, and when safe to do so, the system will make it possible to have fewer personnel on the rig. A substantial change in personnel roles and responsibilities may be required as the technology is adapted. The person controlling the rig may be very different from the driller of today, and the industry needs to start thinking about how to develop these personnel. The long-term goal is for an autonomous rig with remotely controlled operations.
As noted, the open architecture for both downhole and surface operations enables any company to build tools that plug into the bottom of the system, and allows third parties to develop and provide software applications that run on the surface operating system.
Because the technology is designed to follow a planned well project, it is essential that it is configurable for all parties involved. For example, one operator or drilling contractor may have a totally different set of operating procedures than another operator or contractor. The system is being designed so that each customer can upload the well design and procedures into the rig operating system, and the rig will follow that plan until deviation from the plan occurs or is desired.
The system is being designed to operate in three main ways, providing a triple level of redundancy to the operator. First, it will be able to run with high-speed surface automation where all five surface processes (hoisting, rotating, pumping, power and safety) are controlled and prioritized by the control system. Second, the system will perform surface automation with downhole verification using slow-speed telemetry systems such as mud pulse and EM. Third, it will provide full automation, integrating both surface and high-speed downhole data transmitted on wired drill pipe to maximize performance. The benefit of this design is that if downhole tools and equipment fail, the system will still be able to function at a higher performance level than systems that are not automated.
Basic Processes
The basic system processes are shown in Figure 2. The rig’s surface equipment is controlled by surface and downhole data streamed to surface through wired drill pipe. The bidirectionality of the wired drill pipe network is an enabling element in automating the machines with downhole data. Field tests in Oklahoma have demonstrated that high-speed, reliable, pressure- and temperature-compensated downhole weight-on-bit (DWOB) was required to run a downhole auto drilling application. Slower update-rate tools will be able to provide only offset information and verification of downhole parameters, and are not capable of providing data at a fast enough rate for full machine control.
Surface optimization is accomplished using advanced auto driller logic coupled with high-speed downhole and surface data. Surface WOB, surface torque and surface RPM will be optimized using DWOB, downhole torque downhole RPM (DRPM), and eventually, vibration data. An intelligent application can be loaded onto the rig control system to make the BHA and drill string visible on the user interface.
A downhole data point such as DRPM can be generated by a downhole drilling dynamics sub (Figure 3). That data point then will be subjected to downhole processing in the tool and the application of certain calibrations, depending on the variable. It will pass from the drilling dynamics sub into an interface sub, and then into the wired pipe, where it is transmitted through a series of booster subs to surface. On the surface, it will pass through the wired pipe top-drive swivel and be transmitted to a server.
The server then will distribute the data point to the rig control system. On receiving the data point, the rig control system will distribute it initially to an application running on the system, which will apply any required corrections or algorithms. The application will pass on a command or data point to the control system, which will then decide whether any surface machine adjustments are required and whether it can safely perform that adjustment.
The control system will prioritize tasks appropriately. For instance, if the DRPM data point has identified the presence of stick-slip, it may adjust the surface RPM or decide to switch on an active stick-slip prevention system. The control system may have identified already that there is a hole cleaning issue, and may decide from its logic system that the hole cleaning RPM being used takes priority.
The high-speed downhole data enables the system to identify inefficiencies that occur in the drilling process in real time. The root cause of these inefficiencies is typically identified incorrectly or is not identified until after the assembly is pulled out of the hole. The automation system will be able to identify harmful vibration-related harmonics and adjust parameters to remove vibration. This energy then will be fed back into the drilling system, allowing significant improvements in penetration rate.
The system will drill ahead automatically using downhole weight, torque and RPM. This means the drill bit will be run with optimum parameters in a stable environment, thereby minimizing mechanical specific energy. In the future, the system is expected to be open to any downhole and surface equipment, and applications will be able to be loaded onto the surface system.
Key Components
The drilling dynamics sub provides real-time and memory data of downhole WOB, downhole torque, lateral/angular acceleration, Z (axial) acceleration, external pressure, temperature, and RPM. Whirl and stick-slip capabilities are under development.
These data are extremely valuable to the drilling process, and consistent performance improvements of 20-30 percent have been demonstrated already (with occasional improvements of 100 percent). The tool is extremely compact at four feet in length, enabling it to be run both in the BHA and drill string.
High-speed, wired-pipe telemetry allows bidirectional data flow along the drill string. It is also possible to measure temperature as well as bore hole and annular pressures along the string of pipe. BHA interfaces exist for communicating with most major service providers.
The wired pipe platform is composed of several main components:
- An interface sub that connects to measurement-while-drilling/logging-while-drilling and rotary steerable tools to allow bidirectional communication of logs and commands;
- Wired pipe booster subs to enhance the signal to improve the signal-to-noise ratio and communication efficiency between subs (first-generation measurement subs positioned along the drill string measure bore and annular pressure, as well as electronics board temperature);
- A wired pipe “broadband network,” which is the heart of the system and allows high-reliability data transmission through the drill pipe; and
- A top-drive swivel that allows data to be extracted to the surface system while the drill pipe rotates.
In its current state, the wired pipe network is capable of providing data at a sufficient telemetry speed (57.6 kilobits per second) to automate all parameters except vibration data. Faster telemetry speed is required to achieve full high-speed, vibration-related optimization.
The control system under development features an architecture that facilitates automating drilling-related activities that would otherwise require human interaction to accomplish. Working seamlessly on control system installations, the goal with this system is to provide a single platform for automation solutions on all rig floor activities, equipment and services, including making connections, optimizing drilling, well bore stability, rig maintenance procedures, etc.
Through separate control system applications, analogous to applications for smart phone devices, operators and drilling contractors can tailor the level of automation desired and the types of drilling solutions that best suit their needs. The control system will manage and prioritize concurrent application requests for safe tool actuation and closed-loop feedback, and provide “apps” with access to safe and encrypted surface and downhole data as necessary. The data and control screens will be visualized using a uniform user interface.
The fundamental premise of the automation system is that it is an open system that allows any proprietary or third-party application to be plugged in either down hole or at the surface. Applications fall into two main categories: well optimization and equipment optimization. Examples of internal and third-party applications include real-time surface drilling optimization, downhole drilling optimization, directional solutions, real-time torque and drag control, MPD and well bore stability, nonproductive time optimizers, and remote monitoring/control/maintenance/diagnostics.
First Application
The first application written for the new control system is the real-time surface optimization software. The application consists of two key functional components. First, it contains the logic for continuous, real-time selection of optimum set points for drilling control parameters, which can be bit weight, surface RPM and mud motor differential pressure. It also contains an automated, quality-controlled performance evaluation process.
The application searches within user-specified ranges for control parameters and safe operating limits. These search ranges can be entered in real-time or preplanned by formation and depth intervals. This allows the application to optimize without previous knowledge or utilizing prewell engineering.
The application can send the recommended set points to the driller through a popup on a visual display for implementation by the control system. Alternatively, it can send the recommended set points directly to the control system for integrated or retrofit rig controls, with the driller acknowledging each set point change or simply monitoring the overall operation.
Components of the automated drilling system have been successfully field tested, including six field tests of the drilling optimizer application in Arkansas, West Texas and Oman. In one field test, the application achieved a 17 percent reduction in rotating hours compared with the previous well.
The high-speed drilling dynamics sub was used on a test well in Oklahoma. It transmitted high-speed data up the wired drill pipe to the rig system, where the data were visualized as three-dimensional images and in log format. The field test demonstrated that the pressure/temperature-compensated data points coming from down hole were of sufficient quality and frequency that they could be combined with surface data and used for machine control.
The next steps in the process of building the automated well construction system are to develop the downhole auto-driller application and test it with the advanced control system.
TONY PINK is vice president of automated drilling applications at National Oilwell Varco in Houston. He has 20 years of drilling expertise and has played a vital role in developing automated drilling applications. Pink joined NOV in 2006 as the director of advanced drilling solutions, where he contributed to developing the advanced drilling solutions business. He was promoted to his current position in 2011. Pink is a graduate of the University of Wales, Aberystwyth.
ANDREW BRUCE is vice president of controls for National Oilwell Varco’s instrumentation, monitoring and optimization group. He has an extensive background in developing and designing innovative control systems. He also has experience in business and new product development. Bruce joined National Oilwell Varco in 2008 as vice president of controls. He holds a B.S. in computer science from the Worcester Polytechnic Institute.
HEGE KVERNELAND is corporate vice president and chief technology officer at National Oilwell Varco. She has more than 20 years of engineering and product management experience, contributing to quality assurance, research and product development. In 1991, Kverneland joined FluScan, which was acquired by Hitec three years later, and she then moved to NOV after its 1999 acquisition of Hitec. Kverneland previously served as corporate R&D manager. She has authored two textbooks on offshore hydraulics. Kverneland holds an M.S. in mechanical engineering from the Norwegian University of Science and is a graduate of the general management program at Harvard Business School.
BRAD APPLEWHITE is the project director for drilling automation applications at National Oilwell Varco. With an extensive background in finance, supply chain management, and business and new product development, he began his career working as a chemist and transitioned to supply chain management, finance and marketing. Applewhite previously served as director of business unit marketing for two business units at the fourth largest healthcare system in the United States. He joined NOV as the director of global account development. Applewhite holds a B.S. in biochemistry, and cell and molecular biology from Texas Tech University, and an M.B.A. from Texas Christian University.
For other great articles about exploration, drilling, completions and production, subscribe to The American Oil & Gas Reporter and bookmark www.aogr.com.