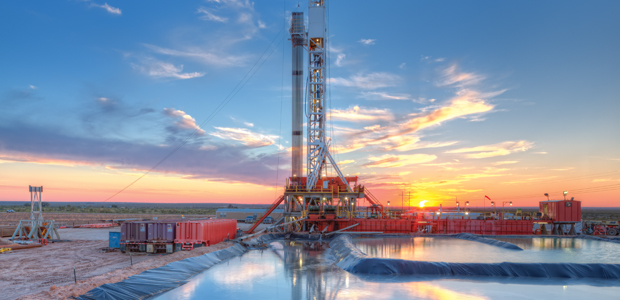
Enhancing Well Bore Stability, Strengthening And Clean-out Focus Of Fluid System Advances
By Ryen Caenn
LAGUNA BEACH, CA.–The fluid system always has been a vital part of drilling engineering, dating back to Spindletop, when a herd of cattle was turned loose in a partially-filled water pit to grind the saturated soil into mush with their hooves. After shooing the cattle out, more water was added to the pit, and presto, drilling “mud” was created.
Today, of course, drilling fluids have evolved into high technology, with industry and academia investing considerable capital and resources each year to develop new component chemistries and engineered systems. Given escalating well costs, especially for long-lateral horizontal wells in onshore resource plays and offshore deepwater wells, mud engineering is more important than ever to manage bore hole hydraulics, maximize drilling efficiencies, eliminate nonproductive time, and get the bit to targeted depth on time and on budget.
The comprehensive selection of fluid technologies now on the market gives operators purpose-designed solutions for any conceivable drilling environment, and new systems continue to be introduced to improve overall drilling performance, economics and environmental compatibility.
The state of drilling fluids technology continues to advance, and the types of fluid systems available include water-based muds (WBMs), high-performance water-based mud (HPWBMs), saltwater mud, polymer muds, drill-in fluids, reservoir drilling fluids, high-pressure and high-temperature fluids, oil-based muds (OBMs), invert emulsion muds, synthetic oil-based muds, synthetic-based mud, and nonaqueous drilling fluids.
No matter what particular system one chooses, however, all these muds continue to perform the primary functions of:
- Controlling bottom-hole pressures;
- Supporting the wellbore and maintaining stability;
- Preventing formation fluid influx and sealing permeable formations;
- Removing cuttings from the bit;
- Carrying cuttings to the surface;
- Suspending solids and keeping the hole clean;
- Mitigating drilling damage to the target formation;
- Protecting the environment;
- Cooling and lubricating the bit and drill string;
- Supporting the drill string; and
- Transferring hydraulic energy to the bottom-hole assembly.
The drillers of the Spindletop well used mud for two purposes: to remove the cuttings from the wellbore and control pressures. To control pressures, however, they allowed the drilled solids to build in the mud to increase the mud weight. Drilled solids can only “weight up” the mud to about 10.5 pounds/gallon before it becomes too thick to pump. This led the development of the first commercial mud product: high-density minerals used as weighting agents.
Countless barrels of mud have flowed through drilling operations since the first mud company, Baroid Mud Sales Company, was formed by the merger of the California Talc Company and the paints and pigments division of National Lead Company. Remarkable achievements in drilling fluids technology have taken place in recent years, including new types of synthetic mud systems, specialty muds for deep- and ultradeepwater drilling, WBM with OBM-like performance qualities, solids-free systems, nonpolar fluids, and wellbore strengthening additives.
Universal Objective
However, all the technological developments within the fluids industry since the first barrels of drilling mud were mixed from dirt and water essentially have sought to enhance the basic properties of the fluid to accomplish the same universal objective: minimize nonproductive time. The truth is, from an operational perspective, the basic elements of the drilling process have not changed that much, but the industry definitely is drilling higher-quality bore holes much more efficiently and much more intelligently through intensive technological research and development.
In 2011, the Freedonia Group, an industrial research organization, estimated that the total oil field chemicals expenditure that year was $18.2 billion. The drilling fluids industry was by far the largest single sector, accounting for 41.9 percent of the total, or $6.8 billion annually (Figure 1).
Another research report from MarketsandMarkets.com projected revenues from drilling and completion fluids through 2018 (Figure 2). As can be seen from the “stair-step” effect of the chart, total revenues were projected to increase each year from 2011 to 2018.
FIGURE 2
Drilling and Completion Fluids Market by Revenue (2011-18)
Source: MarketsandMarkets Analysis
These are encouraging numbers for the fluids sector, but from the oil and gas company’s perspective, drilling operations will always be a cost proposition. The value from drilling a hole in the ground comes from production. As a result, the mindset for operators is understandably to control costs tightly, including drilling fluids, during the drilling process.
Most surveys show that drilling fluid costs range between 5 and 10 percent of the total well cost. So drilling fluids would account for $425,000-$850,000 of a Bakken Shale horizontal well that costs $8.5 million to drill and complete. Considering the criticality of the mud system to a well’s ultimate success, that is an insignificant percentage when looking at delivering a successful wellbore for production or for gathering information leading to the best return on investment for a particular producing zone.
There are some particular drilling fluids that the industry has recognized as adding value to the producing zone, namely reservoir drilling fluids and synthetic-based fluids. These are the most expensive fluid types available, but they impart value by maintaining the integrity of the producing interval or minimizing NPT. These fluids have proven successful in enhancing the return on investment for expensive drilling fluid systems.
Solving NPT Problems
Over the past five to 10 years, the drilling fluids industry has focused on solving problems related to nonproductive time, primarily wellbore stability and lost circulation, driven by the explosion of horizontal and deepwater drilling. This has been an industrywide effort using joint industry projects to develop enhanced testing equipment and operating procedures, as well as sophisticated software packages to better apply mud additives and systems to the drilling process. A third major development has been establishing wellbore clean-out services prior to completing the well.
Consequently, the focus of this article is on these three remarkable technologies: HPWBM for wellbore stability, wellbore strengthening additives, and wellbore clean-out.
Downhole formations that were formed over geological time scales are inherently stable. Drilling a hole into the earth destabilizes the natural layers of sedimentary materials. Given time, a wellbore will collapse. Although some formations are stable over decades, others may be unstable immediately or within a few days. Using the correct drilling fluid system is essential to the integrity of the wellbore, with casing providing a stable conduit for oil and gas production.
Wellbore stability has two components: geophysical and chemical. The geophysical component is managed by maintaining the correct mud weight. Today, by using monitoring-while-drilling downhole components, we can have a fairly accurate measure of the formation’s geophysical makeup and can select the best mud weights to ensure stability. Physical instability also can be caused by unconsolidated formations and tectonically stressed formations, which may require certain mud additives as well as correct mud weights.
The chemical component, however, may require a more detailed analysis of the formations to be drilled. Chemical instability is usually associated with swelling clays in shale formations. The cure for this is to minimize the penetration of water into the shales. For years, nonaqueous fluids have been successful in stopping this water-wetting process. First, the wellbore is coated with oil to form a semipermeable membrane that assists in the osmotic control of water flow into and out of shales. It is now standard procedure to add material to the water phase of a nonaqueous drilling fluid, either a chloride salt or other low water activity material, to minimize clay swelling.
WBMs And Shales
Using a water-based mud ensures that water will be in contact with the shale. Research and development into the mechanism by which water causes clay swelling in shales has shown that reducing the permeability and plugging the tiny pore openings in the shale will slow the uptake of water. The current thinking for additives to make an HPWBM for wellbore stability should control four key properties: clay fixation, accretion, film/membrane forming, and plugging.
The mechanism to control clay fixation is a salt cation that is able to penetrate the shale and fix the clay in place, slowing or minimizing the penetration of water into the pore openings. The potassium cation generally is considered the best at accomplishing this. Potassium enters the pore openings, displacing the sodium cations normally attached to the clays. Potassium is depleted as drilling continues, and must be monitored and added continuously. Other salts that work well in some shale formations are aluminum and calcium.
Accretion control is provided by amine and/or amide surfactants and wetting agents, possibly as co-polymers with fatty acids. These chemicals also attach to clay surfaces to minimize water wetting. This slows the ability of clays to swell, thereby allowing more time to drill the well and set protective casing strings.
Water-based systems cannot form a semipermeable membrane, as do nonaqueous fluids. Instead, they form what can be described as a “leaky” membrane. Again, the mechanism is to slow water penetration into the shales. In addition, these materials can plug pore openings and microfractures, which effectively reduce the shale’s permeability. Some film/membrane former materials used in drilling fluids to do this are:
- Polymers such as polyacrylamides and starch or starch derivatives;
- Polyols such as glycol and glycerides;
- Synthetic oils; and
- Formate brines (saturated potassium or cesium formate are not exactly membrane formers, but can counteract water wetting because of the very small amount of free water available).
Finally, in regard to plugging, certain polyols, many asphalt and gilsonite additives, graphite and micronized cellulose can plug pore spaces as well as microfractures that develop while drilling. Gilsonite and asphalt have been used for a number of years in tectonically stressed areas to plug naturally occurring fractures as well as to stabilize steeply dipped, fractured shales.
A number of laboratory tests have been developed through the years to analyze wellbore stability, including cuttings analysis, capillary suction timers (CST) and various swelling tests. Cuttings analysis has a drawback in that the clay content may have changed dramatically as it was circulated up the hole, especially in water-based mud. Properly cleaned cuttings reclaimed from an oil mud are better to use for analysis. The CST and swell meter tests use reconstituted shales and clays, but still can be useful for primary screening of additives and systems for water-wetting characteristics.
However, these do not test the in situ fabric of shales. Two tests that use actual shale cores have been and continue to be instrumental in advancing the industry’s knowledge of wellbore stability. These are the pore pressure transmission tester and the wellbore simulator. Both require a significant time to gather data. The shale cores must be put into downhole configurations of temperature and confining pressures.
Wellbore Strengthening
The term “wellbore ballooning” was coined in the 1980s to describe a phenomenon in which the wellbore seemingly loses mud to the formation and then regains the mud later. Many times, the regain looked like the well was flowing. Anytime the well seems to be flowing, rig crews are taught to shut down and check for a formation kick. This can result in significant NPT. It is unfortunate that the term ballooning was used, because it implies that the wellbore is elastic and moves in and out like a balloon, which it does not.
At about the same time, the use of synthetic muds was increasing in deepwater operations. Lost circulation with synthetic base muds was a serious problem that cost a great deal of money, both from lost mud and NPT rig costs. It was felt that even though a fracture initiation pressure was about the same for any mud type, for nonaqueous fluids, the fracture propagation was at a lower pressure. Some joint industry initiatives were established to examine and possibly solve this problem.
In time, these initiatives led to the realization that wellbore ballooning effects actually were caused by the establishment of a number of microfractures up and down the wellbore. In certain pressure incidences, involving equivalent circulating density pressures while drilling, these fractures would take mud and then return the fluid when the pump was stopped. This realization resulted in the development of wellbore strengthening treatments.
The series of diagrams in Figures 3A-3C depict the steps involved in strengthening the wellbore. Figure 3A shows microfractures being induced in the wellbore while drilling. If left untreated, these fractures can open and close in response to ECD fluctuations, and surge and swab pressures.
Figure 3B shows the introduction of bridging materials carried in the mud into the fractures. Figure 3C shows the effect of the bridging materials forming a plug, which compresses the periphery of the wellbore, acting like a keystone in an arch. The compression of the formation, in effect, strengthens the wellbore, eliminating any more fractures.
Through these R&D efforts, a variety of materials has been found to bridge and help strengthen the wellbore while drilling, including:
- Deformable graphite;
- Small-sized calcium carbonate;
- Small nut shells;
- Micronized cellulose; and
- Fibers.
Particle size distribution is important to effectively strengthen the wellbore. A laboratory test was developed using the American Petroleum Institute standard particle plugging apparatus (PPA) and slotted metal disks (the PPA is used to determine the ability of particles in the drilling fluid to effectively bridge the pores in the filter medium). Many service companies have developed software that inputs real-time data from measurement-while-drilling services to design the correct particle sizes needed to strengthen the wellbore.
Education And Information
The new metrics of horizontal drilling in unconventional resource plays and improved drilling efficiencies are allowing each active rig to drill more footage/wells per year. The result is that more wells are being drilled in North America, mainly in the United States, than in the rest of the world combined. As in other areas of exploration, drilling and production, the increased drilling activity over the past several years has resulted in a shortage of drilling fluid technicians and technologists.
Historically, mud service companies have trained mud technologists in their own schools. Much of the training has focused on the proper use of each company’s proprietary products. However, there are now several independent mud schools in the United States and elsewhere that do an excellent job of providing basic mud training.
Independent basic mud schools include Odessa College in Odessa, Tx. (www.odessa.edu); Midland College in Midland, Tx. (www.midland.edu/ppdc); Redlands Community College in El Reno, Ok. (www.redlandscc.edu); DFETech in Tyler, Tx. (www.dfetech.org); MudTech Laboratories in Houston (www.mudtechlabs.com); and Ace Mud School in Rancho Cucamonga, Ca. (www.acemudschool.com).
That said, however, it must be noted that as with drilling engineers, reservoir engineers, geophysicists, geologists, or any other technical discipline, good mud engineering skills are developed with experience in the field and may take a number of years. Even the very best school can train people only in mud testing protocols and how to conduct various drilling and drilling fluid calculations. There is no substitute for experience.
In addition, there are a number of sources available to both novice and experienced drilling fluid technologists. This, of course, includes local and national technical meetings that present the latest technology. Another source of information and assistance has developed on the Internet’s social media sites. In particular, social media business sites such as LinkedIn have a number of petroleum-related groups, including drilling fluids technology and drilling fluids engineers.
The American Association of Drilling Engineers holds a monthly fluids management group in Houston (www.aade.org/chapters/houston/fluids-management-meetings) in addition to a two-day national fluids technology conference (www.aade.org/2014-fluids-technical-conference-and-exhibition).
Finally, API Subcommittee 13 (SC13) of the Committee on Standardization of Oil Field Equipment and Materials develops and maintains 12 standards on drilling fluids, drilling fluid processing systems, heavy brines testing, and completion and fracturing fluids. SC13 meets twice a year to conduct business. The group is composed of operator, service company, manufacturing and consultant personnel. The meetings are open to anyone with an interest in helping set standards for the industry. The next meeting is scheduled for Jan. 20-24, 2014, in Dallas (www.api.org).
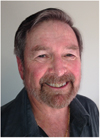
RYEN CAENN has 47 years of experience in the drilling and completion fluids industry, beginning his career as a mud engineer at Baroid Drilling Fluids. He has been a member of the API drilling fluids standards committee since 1974. Specializing in drilling and completion fluid technology transfer, Caenn is principal of TekRite Communications, which has consulted oil companies, fluid service companies and chemical manufacturers in the U.S. and international drilling and production chemicals industries since 1981. He is also founder of drillcompfluids.com, a wikibase website that provides the fluids industry with a repository and database to facilitate technology transfer, including new product development and applications. Caenn also regularly teaches schools and courses on drilling and completion fluids. He holds a B.A. in chemistry from Oklahoma State University.
For other great articles about exploration, drilling, completions and production, subscribe to The American Oil & Gas Reporter and bookmark www.aogr.com.