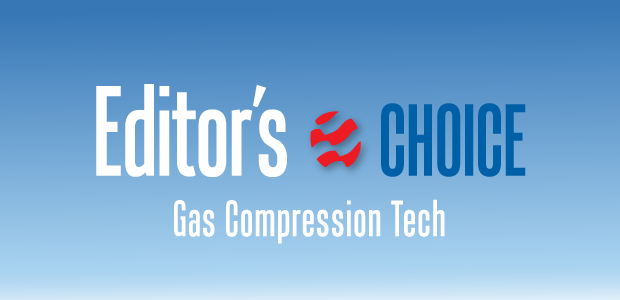
Electric Compressors Bring Numerous Benefits In The Right Applications
By Eric Thode and Brian Green
U.S. natural gas production continues to grow. In the short span between now and 2030, Enverus estimates that total gas production will rise 13% as operators look to market associated gas, supply LNG export terminals, and meet demand from industrial facilities and data centers.
Achieving that production growth will require additional compression for everything from gas lift systems to gathering lines, processing plants and pipelines. Most of the new compressors will continue to be driven by natural gas engines. However, there is increasing interest in electric motor drive compression (EMD) because of its track record of increasing uptime and reducing costs as well as its environmental benefits.
The uptime gain is most noticeable in applications where an engine-driven compressor would run on field gas. That gas is treated before it reaches the engine, but despite improvement to gas conditioning skids, it’s rarely practical to remove every potential concern. As a result, compressor engines often see gas with a higher heating value than they would prefer.
Engine manufacturers are conducting research to increase engines’ tolerance for rich gas and contaminants, but field gas still presents some challenges. For example, its quality can shift rapidly, a reality that complicates conditioning and sometimes leads to unexpected downtime.
Switching to EMD eliminates fuel gas quality concerns. For gas lift compression, we believe that change alone often boosts uptime by 3%-5%. The resulting production gain can add hundreds of thousands of dollars to an operator’s bottom line each year.
In pipeline applications, where compressor engines generally receive high quality gas, EMD compressors rarely deliver a significant increase in uptime. However, some companies are putting electric compressors in compressor stations as part of their commitment to environmental stewardship.
Emissions Reductions
Electric motor drives can reduce the emissions associated with powering compression significantly, but the degree varies based on the electricity source. In Texas, where natural gas, wind, and solar supply most of the power grid’s electricity, EMDs can cut a site’s emissions substantially.
In addition to reducing emissions, driving compressors with electric motors rather than gas engines can increase uptime and simplify maintenance. This is especially true in applications where gas engine-driven compressors would need to rely on low-quality or widely varying field gas for fuel.
In New Mexico, where coal makes up roughly 20% of the power supply, EMD has less of an impact on emissions. Even so, many companies deploy electric compression in New Mexico to comply with current or anticipated emissions limits. For similar reasons, Colorado is another area where EMDs are relatively popular.
Although they have strong environmental leanings, Pennsylvania and Ohio do not have any electric compressors in their oil patch at this time to our knowledge. For now, these states’ power grids do not support EMDs.
Power’s Role
At most oil and gas sites, EMDs are powered by the grid. It’s possible to supply sufficient power with a generator or bank of generators, but that usually only makes sense if the site expects to connect to the grid three to six months down the road.
Even on sites that technically have access to power, it may be wiser to stick with engine-driven compressors if that power is unreliable or full of harmonics. Low-quality power can cause EMDs to heat up and wear out more quickly, potentially impacting one of their biggest selling points: uptime.
Regardless of the power supply’s quality, electric compression should be deployed with harmonics in mind. For example, putting filters between the variable frequency drive and the motor, as well as between the breaker and drive, can significantly improve reliability.
If engineered appropriately, compressors beyond 800 horsepower can endure harmonics that would be problematic for smaller units. The big compressors generally operate with a voltage of 4,160 rather than 480, and it’s much easier for higher-voltage equipment to tolerate the minor voltage variations that harmonics cause.
For some applications, the amount of electricity required can render EMDs impractical. A gas plant or a compressor station that relies on several high-horsepower units would need far more electricity than a well pad that only needs small gas lift compressors.
Hot Spots
While West Texas has a well-known need for more electricity, the Permian Basin’s century of oil field development means it has relatively mature infrastructure. As a result, many of the electric compressors in use today operate there. In South Texas, where electricity often comes from cooperatives with capacity constraints, EMDs are less common. That may change as local power infrastructure improves.
The Permian Basin illustrates the importance of designing compressor packages for the application. As they specify electric motors, compressor engineers need to consider not only the equipment it will drive, but also the environment where it will operate. For Texas, that means accounting for triple digit heat in summer and freezing temperatures in winter. Equipment there must also endure high winds that can cover the equipment with dust.
With experience and care, engineering compressors to withstand extreme environments is relatively straightforward. Like their engine-driven counterparts, EMDs have kept production flowing during the most severe winter storms. EMDs will stop running if power lines get damaged or the utility company shuts off power, but ERCOT has made regulatory changes that have clarified energy production’s importance and dramatically reduced the likelihood of curtailment.
Comparable Costs
EMDs usually have a new-build cost profile similar to the one for comparable engine-driven units. The motors themselves cost less than equivalent engines, but the drive control system and power filtration equipment bring the initial cost into the same ballpark.
Early in their lives, EMDs’ operating costs are lower than engine-driven compressors’ because EMDs require less maintenance, do not need engine lubricating oil, and call for fewer parts to be kept in inventory. However, the EMD owner does need to invest in electricians who have the expertise to troubleshoot any electrical issues quickly. Companies who do not invest in electrical expertise will experience more downtime than they should.
On the compressor side of the package, there is no difference between an EMD and an engine-driven one. The maintenance that needs to be performed and the issues that need to be monitored are the same.
In field applications, an electric motor generally lasts five to seven years before it needs to be replaced. Proper maintenance can extend motor life, but there is only so much it can achieve since the bearings and other parts inside the motor wear out and cannot be replaced.
Smart compression companies are converting some of their engine-driven compressors to EMDs. For example, they may replace a legacy 3516 engine drive with a 1,250 or 1,500 horsepower motor to reduce emissions. Such conversions require some engineering and repackaging, but they can be done economically.
Automation
Aside from the reliability and emissions benefits, one reason to convert to electric is the increased potential for automation. Although both engines and EMDs can adjust their speed, EMDs can adjust their speed instantaneously and hit any point within their operating range. In the field or other dynamic situations, that instantaneous adaptability can be valuable.
Even on traditional engine-driven compressor packages, investing in sensors, automation and remote monitoring has tremendous benefits. By monitoring the compressor package and alerting technicians about subtle signs of trouble ahead, increasingly sophisticated machine health algorithms can transform maintenance. Instead of conducting preventive maintenance by following time-based schedules that are based on general trends rather than a specific unit’s history, technicians can concentrate on addressing real problems before they lead to downtime.
The Permian Basin is one of the areas where electric motor drive compression has seen great success. EMDs are also popular in Colorado, where their environmental advantages can be particularly compelling.
The move to predictive preventive maintenance benefits every stakeholder. For the customer, reducing unnecessary maintenance and catching potential problems early helps maximize uptime. For the fleet owner, it reduces costs by limiting unnecessary trips to site and preventing failures that tend to have cascading effects. It costs less to replace one part before a failure than it does to replace several parts that took damage during an unexpected event.
For technicians, predictive maintenance has a dramatic impact on work-life balance and safety. Instead of driving to a remote site overnight or on the weekend to troubleshoot a unit that went down, technicians can plan most of their work, get it done during daylight hours during the traditional workweek, and more often spend their evenings and weekends with their family and friends.
Parallel Progress
While EMDs have a track record of improving uptime and slashing emissions in field applications, most compressor packages being built today remain engine-driven. That is likely to stay true for a long time, given EMDs’ need for high-quality power.
Although engine-driven compressors continue to improve their emissions profiles, their emissions may never be as low as those of an EMD running on electricity from renewable energy or a natural gas plant. However, those emissions are falling as engine manufacturers continue to optimize combustion.
Other technological advances apply to compressors regardless of their driver. For example, as materials science and engineering make compressor rod packing more reliable and effective, the risk and severity of leaks is going down. Additionally, thanks to improvements in leak detection technology and remote monitoring, any premature leaks that may still occur can get noticed and addressed much faster.
Leak detection has come a long way from the traditional optical gas imaging cameras long used in leak detection and repair surveys. Operators can enlist drones, planes or satellites to survey vast areas quickly, strategically deploy sensors or cameras to watch certain sites constantly, and equip their field teams with user-friendly tools for finding leaks during site visits.
One example of how powerful handheld tools have become is a laser-based methane scanner that is affordable enough to give to almost every technician and rugged enough to endure daily use. When the technicians get to a site, they can sweep the scanner across it to detect methane leaks from a safe distance. As they troubleshoot equipment, they can use the scanner to quickly identify areas with leaks, which can speed up diagnostics and repairs.
Even with the best packing and the most diligent maintenance program, some leaks still occur through the packing. Our company has developed and patented a Quad Ob-compliant gas capture system that traps fugitive emissions from the packing vent and drain, then redirects this gas to a suction header, engine fuel line, heater-treater, or other low-pressure line.
The system can also collect the gas that normally vents to the atmosphere during blowdowns. In total, it can reduce the methane emissions from an engine-driven compressor by about 33% and the carbon dioxide equivalent (CO2e) emissions by about 13%.
To minimize deployment and operating costs, the closed-loop system requires no on-site power and has no rotating equipment. A single skid can collect emissions from several compressor packages. While the technology is new, we estimate that it can eliminate methane on a CO2e basis for less than $8 per ton.
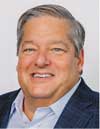
ERIC THODE is the senior vice president of operations for Archrock, which operates a rental fleet that contains more than 4 million horsepower, including more than 800,000 horsepower of electric compression. Before assuming his current role, Thode served as vice president of operations. Earlier in his career, he was the vice president of operations for Archrock’s South Texas business unit and director of the Barnett business unit for Archrock Services, an operating subsidiary. He has worked with Archrock and its predecessor subsidiaries, Exterran Energy Services and Universal Compression, since 2004. Thode holds a B.S. in economics and a master’s in public administration from Texas A&M University.
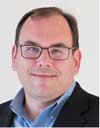
BRIAN GREEN is vice president of the electric motor drive business unit at Archrock. He joined the company in July 2024, when it acquired Total Operations and Production Services LLC (TOPS), a provider of contract gas compression services that focused on electric motor drive units in the Permian Basin. Green joined TOPS in 2006 as vice president and operations manager before becoming chief operating officer in 2021 and then chief executive officer in 2023. He holds a B.A. in economics from Baylor University and an M.B.A. from the University of Texas Permian Basin.
For other great articles about exploration, drilling, completions and production, subscribe to The American Oil & Gas Reporter and bookmark www.aogr.com.