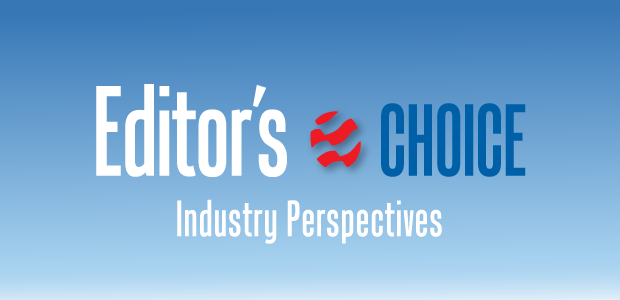
Industry Perspectives: Oil Field Chemistry And Nanofluids
By Amr Radwan
BERWYN, PA.—The paraffin content in produced U.S. crude oil can range from as low as 1% in South Louisiana to as high as 50% in the Altamont Field in Utah. Although paraffin-related production challenges are common and experienced by a majority of operators, there historically has not been a lot of innovation focused on effectively solving problems associated with paraffin deposition in producing wells, facilities and gathering systems.
The most common methods of removing paraffins in wells are wax cutting, pigging, hot oiling, solvent dissolution and inhibitor treatments. These methods require long production downtimes, frequent treatments and significant capital investment. However, advancements in nanotechnology-based solutions promise to revolutionize paraffin treatment and improve oil recovery.
Nanoparticles are solids sized between 1 and 100 nanometers (nm) that are dispersed in a liquid. Several characteristics of the nanofluid are influential in oil field applications—including size, type, charge, pH and stabilizing chemistry—but treatment effectiveness improves when the nanofluid can be tailored to specific crude oil chemistries and rock mineralogy.
A new tailored, nontoxic and non-hazardous, water-based nanofluid is demonstrating success in multiple U.S. basins at effectively remediating paraffin deposits by removing organic damage in well tubulars and altering near-wellbore wettability. This paper describes some of the production results of implementing a tailored nanofluid solution in 24 wells in seven U.S. basins to remediate paraffin/asphaltene issues and modify wettability.
The technology is a dispersion that contains one or multiple types of metal-oxide nanoparticles with stabilizing chemistry. The fluid is tailored and engineered to be effective against different crude oil types. The size of the nanoparticles can be as small as three nm, providing the maximum surface area for interacting with organic deposits and rock materials. The fluid is delivered to well sites in tankers or totes to simplify the entire application process.
The nanofluid disperses organic deposits through a mechanism called structural disjoining pressure or “uplift pressure.” The nanoparticles form a wedge beneath the deposits and allow them to disconnect from the surface. The shear forces of the producing fluids are used to remove the deposits from the system. This mechanism is unique to nanoparticles and does not translate to conventional chemical-based solutions.
Near-wellbore wettability alteration can be demonstrated through spontaneous imbibition of the nanofluid into an oil-saturated rock. A low capillary pressure is required for successful imbibition of the nanofluid and the shape of the extruded oil can describe the wetting nature of the rock pre/post fluid treatment. A low contact angle (more spherical drop shape) represents a water-wet state while a moderate contact angle (flat drop shape) represents moderate-wet state. The nanoparticles contained in the dispersing fluid can be adsorbed on the rock’s surface and provide a longer-term wettability alteration effect compared with surfactants (which can be desorbed).
Field Case Studies
The technology was applied to 24 wells that were experiencing consistent productivity declines. Operators assigned the decline to paraffin deposition or asphaltene damage in well tubulars and the near-wellbore regions. As opposed to expensive and recurring conventional treatments such as hot oiling and solvents, the operators of these wells sought a water-based solution to remove blockages in tubulars and alter rock wettability to a more water-wet state. Nanofluid treatments were an excellent candidate for these wells because of their environmentally friendly nature, ease of treatment characteristics and low cost.
The nanofluid was bullheaded with water at a predefined concentration and allowed to soak for one or two days. The volumes of the nanofluid pumped ranged from 700 to 1,500 gallons per well. In certain jobs, packers were used to spot-treat damaged zones with vertical depths between 3,000 and 13,000 feet. The treatments were conducted at wellbore temperatures of 65-212 degrees F and crude oil gravities of 19-46 degrees API. After treatment, the fluids were produced back with the production stream, making this implementation simple, cost-effective, nontoxic and universally applicable.
In the Williston Basin, two vertical and three horizontal wells were treated in a mixed sandstone and limestone lithology. The crude oil gravity was between 19 and 23 degrees, and oil viscosity was 47-68 centipoise at ambient conditions. These five wells had total vertical depths between 2,900 and 4,600 feet and lateral lengths of 2,000-5,000 feet. Figure 1 shows the production data of these aggregate wells before and after the nanofluid treatment. The treatment added a 79% increase over the decline curve over the following 18 months. Also, the data showed consistent month-over-month production, indicating a long-term wettability alteration of the near-wellbore region that allowed crude oil to be produced easily.
In the San Joaquin Basin, the nanofluid was used to treat four vertical wells completed in a mix of sandstone and shaly layers. One of wells was spot treated at different intervals and had the best response. Oil gravity was 28-30 degrees and TVD was 6,600-12,000 feet. Again, the wells demonstrated sustained improved production trends during the 18 months following treatment.
Four vertical wells in Delaware Basin required restimulation. The well’s lithology was carbonate with a TVD of 3,500-5,000 feet. Monthly production data indicated an increase of 111% on aggregate over the decline curve through two years after treating (Figure 2).
In another Delaware Basin application, four carbonate wells at 3,500-5,000 foot depths were restimulated using the nanofluids. A sucker rod artificial lift system allowed the production of the 35-degree API crude. The well’s water cuts were increasing over time, and were at 80% at the time of treatment. In the 12 months after treating, the average water cut was reduced to 65%-75% and the four wells produced an additional 19,000 barrels of oil compared with the decline curve).
The solution also was applied in two horizontal wells in the STACK play in the Mid-Continent targeting limestone and sandstone, respectively. The wells’ TVDs were 9,300-11,700 feet with 5,000-foot laterals. Over a 20-month period post-treatment, the wells experienced an aggregate 88% production increase over the decline curve (Figure 3).
A final example is from the Powder River Basin, where three horizontal wells with shale and sandstone layers were treated. The TVD of the wells ranged from 11,100 to 13,300 feet and lateral lengths averaged about 8,000 feet. In these wells, total production increased by 80% over the decline curve over the 10 months after treatment (Figure 4).
New Remediation Option
Organic depositions create a significant production issue for operators around the world. Implementing a tailored, water-based metal-oxide nanofluid technology to disperse paraffins and alter near-wellbore wettability is proving successful in a diverse range of applications in both vertical and horizontal wellbores. As illustrated in initial applications in 24 wells in seven basins, the nanofluid can be implemented with different rock mineralogy, crude oils, damaged zones and well histories. In all cases, oil production improved vastly over the 24 wells’ decline curves. Moreover, well productivity was immediately improved and sustained for at least 10 months after treatment, with some wells reporting productivity improvements up to two years after injecting the nanofluid.
These results underscore the potential of using low-risk nanofluid to remediate wells, giving operators a nontoxic, nonhazardous, and cost-effective new alternative to capital-intensive conventional treatment options such as pigging, hot oiling, solvent dissolvers and inhibitors.
Editor’s Note: The preceding article is adapted from URTeC 3722922, a technical paper originally prepared for presentation at the 2022 Unconventional Resources Technology Conference, held June 20-22 in Houston.
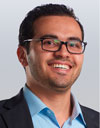
AMR RADWAN is co-founder and chief technology officer of TenEx Technologies. Throughout his career, Radwan has been focused on chemistry and materials science technologies. Before launching TenEx, he managed North American technical sales and business development for Sahara Petroleum Services and served as vice president of technology and innovation at Preferred Sands. Earlier in his career, Radwan held engineering roles related to drilling, completion, production and workover operations. He has authored or co-authored several patents related to oil field chemistry, and he received a B.S. and an M.S. in petroleum engineering from Cairo University.
For other great articles about exploration, drilling, completions and production, subscribe to The American Oil & Gas Reporter and bookmark www.aogr.com.