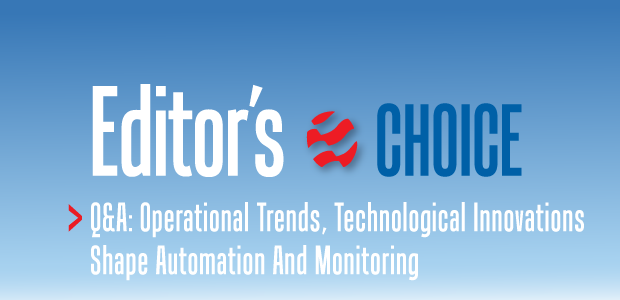
Operational Trends, Technological Innovations Shape Automation And Monitoring
Editor’s Note: Several operational trends are converging to drive the need for affordable, scalable and flexible production automation and remote monitoring solutions. Not the least of these is the proliferation of multiwell pads, concentrating a high density of equipment in a relatively compact area to handle multiphase production streams characteristic of unconventional plays. From each pad, gas and liquids typically flow to a centralized processing and storage facility serving multiple pads, adding even more equipment and complexity to production operations.
At the same time, technologies such as data analytics, the Industrial Internet of Things (IIoT), cloud computing, wireless connectivity and artificial intelligence have matured to the point where they now are starting to be incorporated into all types of production equipment and devices–including pumps, separators, meters, storage tanks, compressors, etc.
For operators, the benefits associated with adopting effective automation and remote monitoring solutions include optimized production, decreased downtime, reduced operating costs and improved bottom-line profitability. But there are a myriad of options available, and the component technologies are evolving rapidly. The American Oil & Gas Reporter assembled a panel of experts to explore the “state of the science” and consider the various technical and operational issues independents must factor into their automation strategies.
Panelists are Mark Peavy, vice president of operations at Windy Cove Energy II LLC, a private equity-backed independent focused on the Permian Basin horizontal San Andres play; Strode Pennebaker, president of Sensorfield LLC, which has developed wireless IIoT microsensor technology that is scalable up to the enterprise level; and Mike Mills, president of Bluetick Inc., which provides cloud-based remote monitoring solutions for the upstream and midstream sectors.
Questions are in italics followed by their responses.
AOGR: As a privately held independent operator, what specific benefits does production automation deliver to Windy Cove Energy II? In what ways does automating production provide savings and enhance revenues for small operators with limited resources? What advice would you offer smaller independents seeking to upgrade legacy SCADA systems to digital technologies?
PEAVY: The main benefits of production automation for WCE II are two-fold: to leverage personnel oversight of the production process, and to minimize downtime. As a small startup bringing up a field in a remote area, our goal was to implement a simple, clean, functional and low-cost data capture solution. Our decision was to capture basic facility data consisting of tank levels, flow rates, and high/low pressures for pressure vessels and pumps. At the well level, we wanted to capture electric submersible pump performance data. Our efforts led to the implementation of two systems, one within the facility, and another for the ESPs. Both of these systems are service provider-supported, resulting in the delivery of real-time monitoring, notifications, and alarming/shutdown capabilities.
Current reporting processes involve a mix of spreadsheet-driven (pumper data collected), and real-time data monitoring facility throughput and ESP performance. These systems have been installed with a view of future supervisory control and data acquisition (SCADA)-driven automation within the facility and for ESPs. Monitoring costs average approximately $450-$500 per well per month. Production data is manually collected and entered in a spreadsheet daily. Future automation of this process is possible using 4- to 20-milliamp transducers installed at each piece of equipment.
We utilize one pumper a portion of the day to service two areas that are 45-50 miles apart, with one field having three central processing facilities and the other having only one. We realized early on that our most significant downtime events were associated with weather. Severe electrical storms come through the area and strike the distribution network, causing electrical surges that take wells out of service. By being able to see this in real time, we have been able to work with our electrical service provider to chase down the problems and resolve them promptly. By utilizing the ESP data capture service, we can monitor and adjust reservoir drawdown pressures to control pressure drop and minimize sand entry into the wellbore.
Regarding advice to others, I would offer that a good solution is to apply a strategic supply chain management approach by aligning their companies with the best service provider they can find for artificial lift, chemical and facilities instrumentation processes.
AOGR: Windy Cove operates some 26,000 acres in West Texas and is focused primarily on the horizontal San Andres resource play. The play targets unconventional “residual” oil from the San Andres reservoir, a prolific conventional formation that has been producing for nearly 100 years. How do you apply automation in your San Andres production operations? How do the characteristics of the wells and play make automation suitable for the San Andres? Please describe the specific operational and economic challenges that can be addressed through automation.
PEAVY: The application of automation within the San Andres is similar in nature to other oil fields. Fluids are produced up the wellbore, separated, metered and placed into storage tanks. Each well utilizes an ESP for lifting higher fluid volumes, along with a variable speed drive for easier startups and pump speed optimization. Peak rates are up to 3,000 barrels of fluid a day per well.
Facilities have separators for each lease, along with test separators for individual well testing. Each facility has a 6- x 20-foot heater treater, 750-barrel gun barrel, three 500-barrel fiberglass water tanks, and three 500-barrel steel oil tanks. Flare and lightning arrestor systems are located within each facility. Turbine flowmeters are used for oil and water volumes. Guided-wave radar fluid level sensors are in the oil tanks. Pressure transducers are located within water tanks to determine fluid levels.
A saltwater disposal system is installed within each field. Two saltwater disposal wells were drilled and completed in deeper formations and permitted for up to 20,000 bbl/d. Our northern field required the construction of 15 miles of electrical line because of its remote location. Instrumentation is placed within each facility to monitor rates, pressures and fluid levels in separators, tanks and pumps. There are 28-47 data points placed within each facility. Associated with these data collection points are 20-22 alerts/alarms. The system is designed so that additional wells can be easily brought into each facility at lower costs.
A few characteristics of the San Andres play in our areas are larger water volumes (2,500-3,200 bbl/d), high hydrogen sulfide gas concentrations (10,000-12,000 ppm), lower oil gravity (27-32 degrees API), and some paraffin within the oil. Large water volumes require the use of ESPs and necessitate on-lease disposal. Higher H2S concentrations require the use of softer metals within tubulars, valves and fittings to prevent embrittlement and failure. H2S safety equipment is located strategically within each facility, and consists of cascade air systems, wind vanes, alarms and signage. H2S safety training is required of all personnel who go into the field. During cold weather, paraffin can become a problem between the separator oil dump and oil tanks, and has required hot oiling to remove it.
In general, automation becomes more suitable as the size of a field grows. This is true of San Andres field development projects as well. Early installation of automation equipment provided WCE II with the ability to more effectively monitor operations and keep field operations lean. SCADA alerts and alarms are sent as texts to key personnel. ESP automation includes data capture of downhole and surface pump information. Real-time monitoring of motor current, voltage, pump intake, motor temperature, motor frequency and amp chart is provided. Run times for 2018 within the northern field were determined to be 97.6%, with 70% of the downtime associated with weather power outages.
AOGR: If you could design the ideal automation system for Windy Cove Energy II, what would it look like? What specific capabilities and functionalities would it have? How would component technologies such as cloud computing, the Internet of Things, data analytics and artificial intelligence, wireless connectivity, etc., fit into that ideal solution? How might it change existing workflows and operating paradigms?
PEAVY: The ideal automation system for Windy Cove would look very close to the system we currently have. All facilities would be similar in design, with equipment using the same components, tanks, valves, fittings and instrumentation. Operational excellence is achieved through simplicity, focus, consistency and repeatability, a similar business strategy pioneered by Southwest Airlines during its early cycle startup, where only one type of aircraft (Boeing 737) was used for all flights. Employees can focus on execution, as they all become more knowledgeable and experienced within these systems. Learnings are optimized and contribute to high run times and lower operating costs.
Our current SCADA system provides the ability to monitor field operations from anywhere on a 24/7 basis using web-based data collection. The SCADA system provides information to lease operators that can redirect them in order to focus their time and energy on the asset that is in need of immediate attention. Others within the organization monitor activities and provide feedback to the field, allowing us to make quick adjustments to equipment as needed. These systems are simple, reliable, and durable and provide sufficient data to achieve operational excellence. As previously stated, one of our keys to success has been aligning with high-quality service providers.
The key driver for Windy Cove, in regard to competent technologies, has been wireless connectivity. These other technologies work for larger, more mature fields. In a large field with hundreds of wells on artificial lift, data analytics and artificial intelligence become a viable way to extract value. In a small, remote field development, basic communication is important and wireless connectivity is huge.
Over the course of my career working for major and small independent oil and gas companies, a fundamental goal has always been doing more with less while focusing on positive net income. I believe that costs and new technology drive change. Revenues can grow with advances in new technology, leading to more oil and gas volumes growth. Cost control is as important as oil production growth and provides a natural tension to the management process. More net income is always the goal. Successful operators identify what makes sense for today, and then execute on it with fierce resolve and a little humility.
AOGR: Windy Cove’s management team has extensive experience in horizontal resource plays as well as in waterfloods and carbon dioxide floods. These are obviously very different production environments, but both mean more complex well operations with greater infrastructure requirements. How do you see this increased complexity impacting production operations? In what ways can automation technology help smaller operators manage the challenges? What do you see as the main drivers for next-generation automation solutions in onshore U.S. fields going forward?
PEAVY: Goals and strategies change as fields move from early to late stages of productive life. Early-stage field development consists of primary production, where wells may flow and subsequently use artificial lift. Mid-stage secondary development utilizes waterflooding to extract more remaining oil reserves. This typically involves more wells as injection wells are required along with infrastructure and pumps to move water out into the field. Later stages of field development utilize tertiary concepts such as CO2 flooding, which requires additional capital to build infrastructure, compressors and possibly CO2 recycle facilities. Conformance monitoring efforts increase as the field moves through the secondary and tertiary phases. The evolution of these steps depends on numerous factors and each step requires additional capital to implement.
Original oil in place is a key variable for scoping the application of these technologies. With larger field sizes come the opportunities to utilize newer computer-related technologies such as cloud computing, IoT, data analytics, and artificial intelligence. Larger fields capture more data, which provides the opportunity for extracting value using more computing technologies.
As these efforts become more mainstream, the opportunity for smaller operators to take advantage of these solutions will occur. These technologies should allow the workforce to make wiser, smarter decisions and lead to a more automated oil field. Perhaps these lessons may provide the foundation for the creative individual to find the next generation of technology to be applied beyond computer-related technology within the industry. As to automation technology for smaller operators, I would offer that it is a step-by-step process. Small producers need to understand their minimum needs and perform a cost/benefits analysis for their specific applications.
AOGR: The IIoT is quickly becoming ubiquitous in automation and monitoring. How would you assess the swift adoption of IIoT devices in upstream oil and gas, and more importantly, where do you see it going from here? What are the features of the latest generation of IIoT sensing devices? In your experience, are there practical limitations to IIoT sensing in general oil field applications?
PENNEBAKER: The IIoT revolution has generated a large amount of press–touting low-cost, high-impact solutions for the oil field. The reality, however, is that very little IIoT technology actually has landed in the oil patch.
The first IIoT products were essentially smaller versions of traditional SCADA equipment. Some brought Internet connectivity and others focused on specialized applications. Most were large and expensive solutions that required trained installation technicians.
Recently, we began to see the emergence of a second wave of oil and gas IIoT devices. These devices feature low-cost, plug-and-play architectures, scalability, and flexible data integration. They depart from the current “wireless SCADA” model and reimagine oil and gas production monitoring.
The latest IIoT systems provide affordable and practical options for oil and gas field monitoring. The newest systems are based on modular, plug-and-play units installed and maintained by untrained field personnel. They look much more like smartphones than SCADA cabinets. These are ultrasmall wireless devices that can be attached quickly to any piece of equipment, vessel or line. These new products are available at a considerable cost reduction. The latest IIoT systems can generate the amount of data equivalent to a typical SCADA system for 20% of the capital expenditure and with a 70% reduction in maintenance.
Power and communication range are key constraints for IIoT sensors. Self-contained products approved for hazardous locations must use relatively low-capacity batteries. This normally limits transmissions to hourly or daily intervals for long-term use. New small embedded solar panels and thermal energy conversion modules break this logjam. They can provide enough power to collect and deliver data in near real time.
Getting data from the field to the cloud is no longer a barrier. On the cellular side, new LTE Cat M1 and NB-IoT transmission standards promise cheaper, lower-power and longer-range data delivery. U.S. carriers initiated these services in 2019. For remote locations, the three major worldwide satellite data haulers soon will be joined by Google, Amazon, Facebook, SpaceX and several small startups.
These multiple technology advances are bringing IIoT devices closer to the full capabilities of traditional SCADA systems.
AOGR: Exactly what types of data can be acquired using these IIoT devices? Specifically in reference to remote monitoring, how is the data being used to analyze and control the performance of production equipment? How are the sensors being integrated with other supporting technologies to create simple, yet comprehensive monitoring and control solutions? In general, what are these supporting technologies? How automated can these systems get?
PENNEBAKER: Most basic oil field measurements such as tank level, pressure and equipment health can be captured with IIoT sensors. Newer devices can handle situations that are difficult or impractical for SCADA. Examples include frac pond level sensors with very long reaching cables, quick-connect high-temperature sensors for wellheads and process vessels, and highly customized sensors for artificial lift and equipment health applications.
Several factors have converged to accelerate the emergence of this new wave of products. They include:
- Considerable processing power using extremely low-cost modern microprocessors;
- Advances in ultralow-power, low-cost embedded sensor chips similar to those used in cellphones, fitness trackers, heart rate monitors and other consumer products;
- The ability of smartphones to serve as sophisticated display devices, which eliminates the need for local display units to significantly reduce both cost and failure points;
- Field personnel’s universal acceptance of smartphones that can display real-time sensor data and receive updates and alarms;
- The emergence of open standards such as MQTT for data formatting and delivery;
- The ability to apply data encryption directly at the sensor level, which enables full data security from the source to the customer’s firewall; and
- Major advances on the data storage side. In fewer than five years, we have seen the emergence of cloud services from major players including IBM (Azure), Amazon (AWS), Microsoft (Azure) and Google (Cloud). Each have platform support for IIoT devices.
IIoT data can be used to optimize production just like legacy SCADA systems with far greater flexibility. With lower costs, operators can now economically monitor more functions than a SCADA budget may allow.
Ultimately, there is no limit to the level of automation, but practical constraints are cost and criticality.
AOGR: How configurable and adaptable are IIoT-enabled digital automation and monitoring systems? With traditional SCADA systems, cost increases in direct proportion to the level of customization. Can off-the-shelf, standardized solutions designed for plug-and-play applications be quickly and affordably customized to meet the specific requirements of a given wellsite or equipment installation site?
PENNEBAKER: Most IIoT providers are focusing on specialized single-application products. Examples include artificial lift optimization and special-purpose sensors for pressure, temperature and flow measurements.
Emerging systems are versatile, highly adaptable and scalable. These new “do it yourself” products allow field personnel to hot-swap a new sensor module or transmitter unit via a quick-connect port. The transmitters recognize the sensor change. They autocalibrate the new configuration, change the processing program, and start transmitting the new sensor data immediately.
Some IIoT devices allow remote configuration to set alarms, sampling rate and special program parameters. Powerful microprocessors allow customized measurements with onboard processing on the fly. Customers are discovering novel applications with the new ability to process multiple local IIoT sensor inputs using customized onboard software.
The IIoT ecosystem rapidly is moving toward direct-to-cloud communication. Emerging international IoT cellular standards and microsatellite data services give IIoT sensors the ability to communicate with virtually limitless scalability and no additional local infrastructure. This is a significant game-changer for remote monitoring, especially in the oil field. Bypassing local infrastructure brings lower cost, faster data delivery, easier installation and maintenance, simpler integration of multiple vendors, and increased security.
AOGR: Speaking of traditional systems, how challenging is it to infuse existing legacy automation and monitoring systems with the new capabilities? What recommendations and best practices would you offer smaller oil and gas companies seeking to cost-effectively upgrade their older systems on an enterprise level? What should the first step be when upgrading existing systems to lay the framework for building a fully digital production operation?
PENNEBAKER: Operators, especially the larger ones, are not enthusiastic about “rip-and-replace” upgrades. The newer IIoT systems can offer gradual migration pathways. These allow phased integration into cloud and back-office database systems. The operator can access the vendor’s real-time server via an application programming interface (API) and control the orderly migration of data into legacy systems.
The major barrier to widespread IIoT adoption is the difficulty of integrating a fragmented market of IIoT sensors into a production environment. While SCADA architecture is standardized and compatible, most IIoT products are designed as stand-alone, proprietary products. Each has its own software package, data formats and phone apps. As the IIoT ecosystem develops, industry standards will emerge to drive tight data integration across multiple IIoT providers. With open standards, operators will be able to take advantage of the competition. Operators will not care about the various sensor configurations and form factors. They will just need accurate, reliable and secure data delivered to their cloud servers at the best price and service.
There are several steps to ensuring success. The first is for management to ensure that it has identified key internal champions to onboard the new IIoT technology at both the field and corporate IT levels. The vendor must be able to work with both groups. They speak totally different languages, so the vendor needs to be fluent in each.
Installation and maintenance are key cost factors. Self-installed systems are best, but if the vendor requires a trained installer, be certain that personnel are available locally.
Integrating old and new systems is not easy. SCADA and cloud-based data stores rely on very different protocols. Consider two options: Pulling new data into an old historian or importing old data into a new cloud. Which is better? The newer commercial data import and visualization tools may help.
Also, operators should ensure that the vendor has a robust API that allows seamless integration to their own databases, and adopt a preference for vendors that use open standards. Oil and gas companies do not want to get locked in to a single vendor.
I recommend incrementally moving old data systems to new ones with APIs for external tools to access data. This allows data to be pooled and ensures data is not trapped in a single, proprietary database.
Finally, operators need to ignore IIoT buzzwords and trends and instead focus on products that solve real problems, not necessarily those that use the most exotic technology.
AOGR: Automation was once a high-cost technology reserved for only the largest producing companies or for select applications. How is technology continuing to level the playing field when it comes to accessing advanced automation and monitoring tools? What supporting technologies do you see as most important? What does a good automation system look like today?
MILLS: Many of the largest producing companies used to produce much of the high-cost automation technology in house. They had the staff, equipment and money to develop most of the tools they needed, but at a cost. Today, oil and gas companies are benefiting from everyday technology developments that are coming out of many different industries. Some of these developments–such as the IIoT, cloud services and wireless technologies–are being developed by companies such as Bluetick to provide more affordable automation and level the playing field for smaller companies who need to take advantage of these opportunities. However, focusing on affordability does not necessarily translate into the best system for a smaller company’s needs.
A good system will gather data from multiple points in the field to provide the information necessary for various people within different levels of the organization to make informed decisions affecting their day-to-day operations. This system would consist of the proper combination of sensors in the field, coupled with an effective data transport system to bring back information that can be analyzed on backend software. This system would provide user-friendly tools that permit easy interpretation of that data. This kind of system would provide enough real-time data to improve predictive modeling efforts to direct changes in field management. In addition to data analysis, the system should be reliable and offer mobile applications to keep field personnel apprised of changing conditions on the ground in real time.
AOGR: Putting all the pieces of an automation and monitoring system together can be a daunting task. But the operator first has to understand exactly what its automation needs are. How would you advise oil and gas companies with respect to assessing their operations? What suggestions do you have for them when it comes to finding solutions to address their identified needs?
MILLS: Many of our customers already have a good idea of what they want to monitor when they engage us, and we help them engineer the most effective way to do that. In many upstream and midstream operational activities, there is always a balance between the right amount of information needed and cost. We help them evaluate their operational needs and budget. Many of our suggestions simply come from experience working with a large variety of applications. If customers would like to experiment with a new application or sensor they would like to beta test, we are always willing to work with them. We have the flexibility and know-how to make it work. Most important is the ability to scale the system as the operation grows or technology changes and keep it all integrated on a single platform.
AOGR: In your experience, what automation system capabilities and features are most important to independent oil and gas companies? How do automation needs and potential solutions vary for unconventional versus conventional fields? How important are compliance and health, safety and environmental factors in terms of driving automation needs?
MILLS: The easy answer would be the most important system capabilities and features are the ones that keep production running smoothly, efficiently and profitably.
It is difficult to pinpoint the most important capabilities and features because there are so many different applications that can be monitored and controlled in the field. It is highly dependent on the needs of the company from one week to the next. In most cases, they want to keep their operating costs as low as possible. In my experience, either type of operation–conventional or resource play–is equally important to the company operating it.
With the ever-changing regulatory environment today, automation has become increasingly important not just with data collection for reporting purposes, but also for companies to monitor the health and safety of their personnel and the environment.
AOGR: Please describe your vision of what’s to come in oil field automation and monitoring. How can operators be confident that the component technologies they install today will have the adaptability and longevity to continue meeting their needs over the long term? When will the digital oil field concept become a practical reality?
MILLS: My vision of what’s coming in oil field automation is simply based on the concept that we must continue to innovate tools to help customers make better decisions. We all hear and read the daily technology buzzwords, but you have to consider who is putting those ideas to work.
Many operators cannot afford to employ a full technology staff to keep up with new technology concepts, nor should they have to. Working with a technology partner allows them to reap the benefits from the latest technologies, discuss their automation strategies, and focus on what they do best. Operators should let their technology partners keep up with evolving technologies and focus on having their partners provide great systems and services to them.
The digital oil field is here! Smart companies are using technology today to move from reactively managing “situations” to proactively managing their assets and operations.
For other great articles about exploration, drilling, completions and production, subscribe to The American Oil & Gas Reporter and bookmark www.aogr.com.