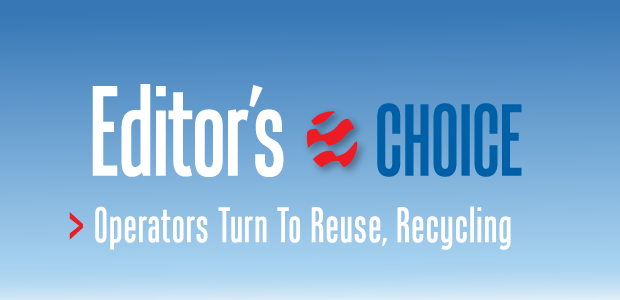
Operators Turn To Reuse, Recycling
By Kari Johnson, Special Correspondent
Producers across all shale gas plays are keenly aware of their water usage and the need for sustainability, both for their own operations and for society at large. In particular, producers are working to reduce the volume of freshwater used in hydraulic fracturing by recycling and reusing frac flow-back water.
A typical well in the Marcellus requires 3 million-5 million gallons of water to fracture stimulate, according to Range Resources, which, the company notes, represents 0.003 percent of the daily consumptive water demand in Pennsylvania. By comparison, according to U.S. Geological Survey statistics, power generation consumes almost 100 times as many gallons a day, while public water systems and other industrial uses each consume more than 25 times that of shale gas operations.
A comparison of water usage per MMBtu of energy output also shows natural gas ranging from 0.6 to 5.8 gallons. This compares with nuclear power at 8-14 gallons an MMBtu, crude oil at 8-20, coal-powered electric generation at 13-32, and biodiesel from soy at 14,000-75,000 gallons an MMBtu, according to a U.S. Federal Reserve report cited by Range. Recycling and reusing flow back further improves this relative efficiency, the company points out.
Water Recycling Pioneer
Range Resources pioneered flow-back water recycling in 2009, and today uses recycled water in most of its completion operations, says Dennis Degner, director of operations for Range’s Southern Marcellus Shale Division. “Reusing flow back and produced water accounts for 30-40 percent of Range’s overall water usage in Pennsylvania,” he reports.
When additional freshwater sourcing is needed, Degner says the company uses approved surface water withdrawals as well as municipal water sources. Typically, these are rivers and reservoirs that are resistant to drought.
The majority of Range’s core operating area is serviced largely by withdrawing and recycling water from the Ohio River, states Degner. The company transports the water through its own infrastructure to well sites throughout its core operating area in southwestern Pennsylvania.
“The infrastructure from the Ohio River is sized so that we can push enough water from the river at the flow rate needed for the frac job, and have essentially no impact on the river,” he says.
Range’s full flow rate from the Ohio River to a frac job is less than 0.001 percent of the river’s seven-day, 10-year low flow, Degner elaborates. Water is transported mainly in trucks or pipeline, through municipal infrastructure, or temporary aboveground pipes. “We prefer a pipeline because it minimizes truck traffic and is a more cost-efficient way to transport the water,” he remarks.
Range is one of a few companies with high volume access to super sources, such as the Ohio River in Pennsylvania, Degner says. “The infrastructure to the Ohio River enables us to utilize a large-volume, drought-resistant source, and allows us to move away from smaller seasonal sources that may be restricted because of seasonal low flows,” he points out. “After fracture stimulation, water returned from the well is collected in a closed-loop system at the surface.”
Freshwater Use by Oil & Gas in Texas
Despite increasing drilling activity, a study conducted in 2011 by the Bureau of Economic Geology at the University of Texas and updated in February this year projects increased use of brackish and produced water in place of freshwater along with flat-to-declining freshwater consumption by oil and gas operators. Graph courtesy of Pioneer Natural Resources
Degner says flow-back treatment depends on the type of completion, geologic formation, and water quality required for the frac design. In most cases, he says, the flow-back water must be settled and filtered to remove total dissolved solids and then treated for bacteria. In some cases, advanced treatment technologies such as evaporation and distillation are needed to fully remove remaining salts.
Water Management Plan
The industrywide trend is toward simple treatment technologies, and finding ways to maximize flow back and reuse produced water. In Pennsylvania overall, Degner reflects, recycling has increased greatly year over year, and that is expected to continue. “A typical well in Range’s Marcellus Pennsylvania operations will yield 20 percent of its flow-back water within the first 60 days of production,” he details. “We expect another 15-20 percent of produced water throughout the remaining life of the well.”
This additional flow back requires very little treatment, Degner adds.
Although actual well completion takes only a few days, Degner says Range puts together an extensive water management plan months before the operation begins. “Our planning examines the needs and location of each unique well site, including its proximity to water storage sites and/or freshwater sources, and takes into account produced and flow-back water available for completion,” he says.
For example, he says, if a site is located within five miles of a large surface water source, Range typically can pipe directly from that source to the frac location, which requires minimal storage. “If a smaller water source is used, we could fill tanks slowly or centrally locate water at storage sites over several weeks prior to the operation,” Degner says. “The water then is pumped directly to the well pad for completion.”
Recycled flow back and produced water typically are transported by truck directly to the well location and then are blended with freshwater. If present, microbes are treated with the rest of the frac fluid prior to being pumped into the well bore.
Degner says aeration systems are used throughout the surface storage area to avoid microbial issues. If a microbial problem is found during temporary storage–typically detected by a dedicated staff through water aesthetics–the issue is addressed with biocide products appropriate for surface treatment.
“In 2010, Range became the first company to voluntarily disclose its chemical usage for hydraulic fracturing, posting completion reports on the company’s website,” Degner states. “We are continually exploring new chemical additives for completion operations, and testing greener chemistries for treating produced and flow-back water.”
Texas Sustainability Initiatives
Pioneer Natural Resources has made significant investments to ensure sustainability in its Texas shale gas operations. “We conducted numerous studies to understand area by area what treatment operations were required,” says Michael Dunkel, director of sustainable development.
Pioneer Natural Resources says it has evaluated numerous treatment options for brackish water, including electrocoagulation, membranes, reverse osmosis and nanomembranes. The company is planning two recycling projects this year in the Permian Basin that each will process 5,000 barrels a day. In the Eagle Ford Shale, the company says it is considering a mobile system to treat flow back at a high rate.
He says the sustainability group, which was established two years ago, has reviewed water logistics in depth, including treatment, transport, central storage, and local storage for higher instantaneous withdrawal rates.
Dunkel says water conservation begins with the source. “Depending on where you are, brackish water can be used almost exclusively to avoid using freshwater as our source,” he asserts. “It is not always easy to use (brackish water) because it costs more to drill for it and it produces at a slower rate.”
However, Dunkel adds, Pioneer’s cost of producing brackish water typically is lower than recycling.
To better understand its options for treating brackish source water as well as flow back, Dunkel says Pioneer conducted extensive evaluations. “We piloted 10 or so treatment technologies,” he recalls, “including electrocoagulation, membranes, reverse osmosis, and nanomembranes for removing total dissolved solids.”
He reports the company found produced water typically was too high in salinity for reverse osmosis, but nanomembranes could take out almost all suspended solids and some dissolved solids. That process delivered consistent results.
In addition, the group reviewed desalination options for removing salt. The main issue in desalination, Dunkel allows, is cost. More energy is required and more infrastructure is needed, especially for storage and transport. “If the water is treated to the point it meets freshwater standards, then it can be transported and stored without high risk,” he points out. “If it is transported as brine, then extra precautions are required to prevent leakage and contamination.
“At this point, the majority of industry in Texas uses fresh groundwater,” Dunkel comments. “Only 21 percent is brackish water, and the volume of recycled water used is probably in the single digits.”
Given that Texas has abundant formations suitable for long-term disposal of produced water, Dunkel notes it is financially tempting to simply dispose of flow-back water. Still, he says Pioneer is using brackish water as a source and is finalizing plans for two recycling projects this year in the Permian Basin that each will process 5,000 barrels a day of produced water.
“We are transitioning in the Permian from primarily vertical drilling to a heavier emphasis on horizontal drilling,” Dunkel remarks. “We have been plugged into the need for and importance of water for quite a while now. Water is one of our top two issues and is getting more important.”
Noting that Pioneer has many wells to drill for years to come in the Permian Basin, Dunkel posits, “We are well aligned with the community and other stakeholders, and it is in everybody’s interest that we manage water properly.”
Logistics, risks, water quality, and cost are a big part of the decision on whether to recycle. If a company can dispose of flow-back water for cents on the dollar and it costs more to recycle, the decision is hard. “At some point, you kill your economics,” explains Dunkel. “That has been the biggest hurdle for recycling.”
Treating In The Eagle Ford
Before extensive recycling and reuse, Dunkel says produced water in the Eagle Ford was accumulated at the point of delivery in a tank battery, treated for bacteria, and then trucked to a disposal well. Now, Pioneer is considering a mobile system to treat flow back at a high rate. Very little storage would be required, he points out, because there is very low flow back. The treated water is trucked to the next frac site where it is mixed with freshwater.
This works well for 10,000-20,000 barrels of water per fracture, Dunkel says. But lower volumes do not provide the critical mass required to get a good per-unit cost. “We are trying to find the sweet spots where we can spend a little money for the best impact,” he attests. “Fortunately, this is a collaborative effort between industry and government–both state and national.”
Unlike lease information that is proprietary, he notes, the economics for using water in a sustainable fashion require a ‘we’ solution. As companies go to pad drilling, Dunkel says they may be able to separate flow-back water at the pad, treat and deliver it to the next well. The issue is whether there is enough water to supply the need.
“We need an unmanned system so that the cost per barrel can come down enough to make it economical to treat small volumes,” Dunkel reasons.
In the future, Dunkel says he anticipates more and more water to move through pipelines. “Trucks on the road are a community concern, so anytime we can reduce trucking, it is good for everybody,” he surmises.
“We are doing a lot to reduce water usage per well: recycling, using brackish water where we can, switching to cross-linked gels, and preventing evaporation,” Dunkel concludes.
Since evaporation is a big concern in Texas, he says Pioneer is looking for economic ways to cover its pits. “This should be an economical way to save water when we figure it out,” he predicts, adding that in the short term, none of Pioneer’s water conservation efforts are likely to save money. But these are early days, he acknowledges. In the long run, sustainable operations are good for everyone.
Reuse In The Cana
Devon Energy Corp. has made a major commitment to reusing water in its Cana play in west-central Oklahoma’s Anadarko Basin, installing a 500,000-barrel pond for flow back to service wells within a concentrated area, reports Jim Heinze, operations engineering manager.
He says the company typically uses 150,000-180,000 barrels of water per well. Fracture flow back within the first 60 days is 20,000-30,000 barrels. No foreign water is produced from the Woodford; only water used in the fracture treatment comes from the well, Heinze says, and Devon uses as much recycled water as possible, augmenting with freshwater as needed. Some of the company’s wells in the area already have been fracture stimulated with 100 percent recycled water, he notes.
Devon Energy Corp. has constructed a 500,000-barrel pond for flow back to service its Cana play wells in Oklahoma’s Anadarko Basin. The company typically uses 150,000-180,000 barrels of water per well and recovers 20,000-30,000 barrels of flow back within the first 60 days of completion.
The quality of flow back in Devon’s Cana play is higher than in any other basins that Devon has worked, Heinze reports. While the Barnett Shale often exhibits 60,000 parts per million total dissolved solids, he notes, the Cana-Woodford has only 20,000 ppm. “It’s a different world from Pennsylvania, or West Texas or the Eagle Ford, for sure,” he avers.
As a result, Heinze says Cana-play flow back is easy to treat and reuse. No processing is required, other than settling and adding biocide for bacteria. “It is less expensive for us to reuse flow-back water than to buy freshwater from landowners,” he states.
Original source water for hydraulic fracturing comes from surface water and the Canadian River, and goes directly to the wells where it is mixed with flow-back water, Heinze says. Temporary piping and flexible hose are used to transport the source water.
Heinze notes Devon is developing the Cana in a concentrated area (eight wells per section) and is running two frac crews. Consequently, he says, there is a tremendous need for water over very short periods.
Travis Dean, facilities engineer at Devon, reports the company built an elaborate pipeline system to service its wells. Flow-back water enters the pipeline and is directed to the large storage facility or to the next completion, depending on need.
The flow-back water initially is sent through a separator and storage tanks on the well site. From there, Dean says, the water is transferred to the pipeline. At the recycle facility, the water enters a settling basin and then is transferred to a series of storage tanks to remove suspended solids. By the time the water reaches the pond, enough settling has occurred to remove all suspended solids.
Devon uses fiberglass pipe rated to 450 psi and 200 degrees Fahrenheit for its water gathering and distribution lines. It is a permanent system designed to be in ground for 30-plus years, Dean points out. In most cases, he adds, pipelines are laid in the same rights of way as Devon’s natural gas pipelines.
Heinze says Devon worked closely with the Oklahoma Corporation Commission to design its large water storage facilities.
“Other operators are replicating this concept,” he reports. “If an operator has concentrated drilling and the regulatory environment is conducive, it makes a lot of sense to put in this type of system. It is a win-win for everyone involved: regulators, farmers, ranchers and operators.”
In its first nine months of operation, Heinze says Devon recycled more than 4.2 million barrels of water. Truck traffic was reduced, including eliminating 7,400 truckloads of water for disposal in the first three months alone. Water disposal costs were reduced, as was the volume of freshwater consumed.
“Nobody wants to use freshwater if we can find alternatives,” Heinze concludes.
For other great articles about exploration, drilling, completions and production, subscribe to The American Oil & Gas Reporter and bookmark www.aogr.com.