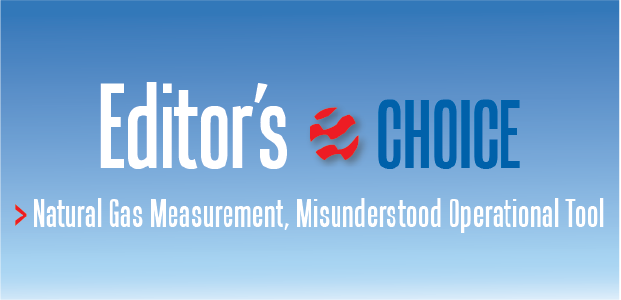
Gas Measurement Technology
Technological Advances Position Gas Measurement As Key Operational Tool
By Dean Graves
OKLAHOMA CITY–Integrating electronics, communications capabilities and other technologies beyond the basic mechanical meter has transformed the gas measurement function into a core component of field operations and performance optimization. Well flow across an entire field can be monitored remotely, along with tank levels and other operating details. Thousands of miles of pipe can be managed from a central control unit, cutting dramatically the need to physically visit production sites and gathering lines.
Bundled with flow measurement are other operational data that improve decision making, moving gas measurement from a single-purpose function to part of a multipurpose operating tool. Now, flow data reporting may be part of the same system used for lease location control, valve control and tank level recording. Changes can be made instantly and dispatch for tasks such as tank offloading can be scheduled most efficiently.
With measurement data presented as part of a computer screen covering multiple wells or lengths of pipeline, it is easy to lose perspective. Measurement can seem like a small detail, a well understood input to the control process. Yet there are many factors that can adversely affect accuracy. These factors are less obvious when measurement data are no longer viewed in close proximity to the meter.
In the midst of new technology adoption, and to a large extent because of it, there is a new drive to teach measurement fundamentals. When the fundamentals of measurement are understood by the personnel monitoring and interpreting data in the control room, better decisions can be made and gas measurement truly can be leveraged as a critical operating tool.
Field To Control Room
While measurement technology certainly has come a long way from when I started in the oil and gas industry 32 years ago, measurement itself is fundamentally the same. The gas flow rate is calculated using a simple orifice, meter tube and sensing equipment (Figure 1). As gas passes through the orifice, gas flow is restricted, causing a change in pressure. The flow rate is calculated based on this pressure change and other details, such as gas composition and temperature.
When I began my career, measurements were taken and recorded on a meter at the wellhead or along a pipeline. The chart reports were analyzed, interpreted and acted on, usually in a very local manner. The speed of action depended on how often a technician could visit the meter and how quickly he could complete an analysis.
The advent of electronic flowmeters and supervisory control and data acquisition technology effectively moved measurement analysis from the field to a central control room. EFM measures flow in the same way, but the measurement data are recorded electronically. They often also consolidate the readings from multiple meters and even from other types of devices and sensors. While most of the data can be accessed at the EFM location, the data typically are communicated remotely to a control room where they can be fully analyzed and archived.
The benefits have been tremendous. It is no longer necessary to dispatch technicians for the sole purpose of meter reading, whether measuring pipeline flows or flow rates from wells in producing fields. Many more readings can now be taken with no additional cost, and readings can be compared and consolidated across a field or pipeline in only minutes rather than days.
Devon maintains a central control room for its gathering and pipeline operations that span Texas, Oklahoma, Louisiana, Wyoming and Montana. Operating 24 hours a day, seven days a week, the control room can show operators the status of every meter, review historical data by meter, compare flow rates across meters, remotely actuate valves, and make other operational adjustments in real time to optimize overall system performance.
Devon maintains a central control room for its gather and pipeline operations that span Texas, Oklahoma, Louisiana, Wyoming and Montana. Operating 24 hours a day, seven days a week, the control room can show operators that status of every meter, review historical data by meter, compare flow rates across meters, remotely actuate valves, and make other operational adjustments in real time to optimize overall system performance.
At Devon, we have a central control room for our gathering and pipeline operations that span Texas, Oklahoma, Louisiana, Wyoming and Montana. Operating 24 hours a day, seven days a week, the control room can “see” the status of every meter, review historical data by meter, and compare flow rates across meters. We also can open and close remotely-actuated valves and make other operational adjustments in real time from the center in Oklahoma City. We can implement both short-term tactical decisions and longer-term actions for optimizing overall system performance.
Production Applications
On the production side, Devon and other operators are equipping vertical and horizontal wells with electronic measurement technology. Horizontal drilling is becoming more prevalent onshore in urban areas, in rough or sensitive terrain, and in producing zones where the nature of the rock makes horizontal laterals the best option. In all these situations, companies are able to reduce their environmental footprint by moving measurement into a central area and away from access roads and sensitive ecological zones. At the same time, they are able to monitor wells more closely, which is particularly beneficial for production planning.
In shale gas fields, for example, horizontal wells typically have high initial production rates that drop quickly over the first months of production, followed by long periods of sustained production at much lower daily volumes. Monitoring production across wells at frequent intervals with EFM can improve planning and field development operations.
In the offshore environment, there are typically many wells with control equipment spread across several floors on a platform. Electronic measurement technology allows the operator to gather measurement data at one central location to monitor and control production operations.
On offshore platforms, if storm evacuation is required, control can be transferred to another remote location, allowing operations to continue even after the workers have left the platform. If conditions reach the point where they mandate shutting in production, this also can be performed automatically by the automation equipment.
Of course, regardless of the type of application, the value of EFM depends on the quality of the original data. If the readings are inaccurate, everything that follows will be wrong. The old adage of “garbage in, garbage out” certainly applies to gas measurement. All technology does in that case is supply more inaccurate data at a faster rate. From an automation and control standpoint, the more automation the better. From a measurement standpoint, accuracy is everything.
Accurate measurement depends on a reliable flow leading up to and following the orifice. If there is turbulence or other flow problems, the measurement readings will be incorrect, and over time, measurement data inaccuracies can become very costly. To ensure accurate measurement, it is critical to adhere to American Gas Association and American Petroleum Institute standards for measurement equipment and installations (Figure 2).
Ensuring Integrity
Entry gas flow is affected by anything that can disrupt it, including piping, valves and uneven welds. Industry standards require a straight section of pipe of a minimum length, depending on volume, in order for the gas to flow smoothly. Similarly, there are also standards for the exit piping configuration. Even when the standards are carefully followed, abnormalities may arise over time, making preventive maintenance crucial for avoiding problems as much as possible.
Sensing taps must be carefully placed to ensure that their readings are correct. For example, they must be equidistant from the orifice and at a standardized location. A buildup of salt, the presence of fluid in the gas stream, extreme temperature and other flow issues also can significantly impact EFM sensor readings. Finally, flow characteristics such as density, composition and temperature affect gas volume calculations.
With all the benefits from electronic measurement that accrue to the operator, the growing distance between the gas being measured in the field and the technician in the control room does impact to some degree the risk that measurement abnormalities will go unnoticed. A man in the field can see a problem with his own eyes, while a technician in the control room must be able to recognize the problem from the acquired data. One effort to guard against the “blind acceptance” of EFM data is software programs that are designed to delineate out-of-bounds data that are outside the range of normal parameters. By programming preset parameters into the software, potentially anomalous data can be automatically flagged for further review.
The newest generation of measurement technicians are more familiar with computers than field work, but operating companies should guard against assuming data are accurate. False confidence in the data is a common problem. A prevalent mistake seems to be assuming that “if it has four digits of detail, the EFM data set must be right.”
To address the issue of measurement integrity, the American School of Gas Measurement Technology and other industry measurement schools dedicate a significant portion of their programs to teaching and reviewing measurement fundamentals. This gives students a solid footing from which to look for and recognize anomalies in measurement data before they are used as input to decision making. This emphasis was well received at this year’s school, as it has been in the past.
Leveraging The Data
As the advantages of automation technology continue to come to more and more fields and operations each year, the time is quickly coming to fully leverage the measured data. We now have faster data access and many more data points. With this capability, companies have achieved cost reductions and moved data to centralized control rooms for fast and effective analysis.
While there will no doubt be more innovations in electronics and automation, the real advances in the next few years will be in how the data are analyzed and used to improve performance.
Beyond well monitoring, production managers can use measurements across the field and across time to do sophisticated analysis on overall production and trends in the data. With a better knowledge of the real-time state of each well, they potentially can increase production for faster payback or make changes to maximize overall field production.
Farther downstream, pipeline operators can manage at smaller time increments, and potentially set rates based on these increments, moving from daily prices to hourly, for example. This concept is already in place in some end-user distribution markets, where electricity and gas usage is measured and reported at frequent intervals, allowing the provider to offer different rates for peak and off-peak usage. The same idea could be implemented at the distribution stage.
With a firm understanding of measurement fundamentals, the industry can leverage automation and electronic measurement to make significant advances in operating efficiencies and improve bottom-line business performance from the wellhead to the burner tip. This is where I believe the big news will be in the next few years.
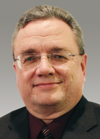
DEAN GRAVES is corporate measurement administrator for Devon Energy Corporation in Oklahoma City. He has more than 30 years of industry experience in gas and liquid measurement. Graves participates in measurement committees of the American Petroleum Institute and the Gas Processors Association, and serves as the general chairman of the 2010 American School of Gas Measurement Technology. He holds a bachelor’s from Texas A&I University.
For other great articles about exploration, drilling, completions and production, subscribe to The American Oil & Gas Reporter and bookmark www.aogr.com.