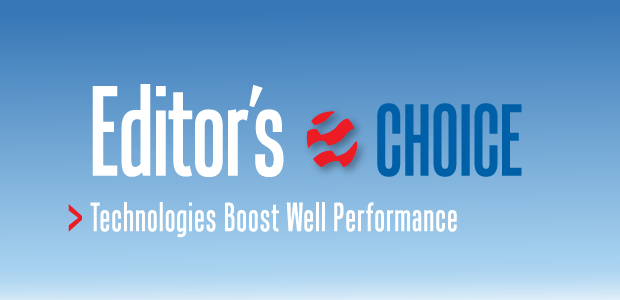
Artificial Lift Technology
Technologies Boost Well Performance
By Tim Beims and Dan Holder
Imagine a doctor trying to treat patients by prescribing the same remedy no matter the ailment. At the very least, that approach would generate highly inconsistent results and lead to untold needless pain and suffering. Now think about that “doctor” holding a petroleum engineering degree and the “patient” taking the form of producing wells equipped with artificial lift.
Would it be any more logical to apply one type of lift system to every well in a field regardless of operational parameters, or use the same universal pump speeds or chemical treatment programs without considering each well’s production history? Absolutely not, according to Franklin Cueto, vice president of artificial lift systems at Weatherford. “The time when everything was ‘copy and paste’ from one well to the next is over,” he declares. “The future is about treating wells like individual patients with unique problems.”
Considering that a grouping of wells in close proximity can have very different fluid, reservoir and mechanical properties, it stands to reason that each well would have distinct artificial lift requirements. As Cueto points out, the producer could avoid a lot of pain by better understanding the characteristic behavior of every well in its portfolio, and then taking prescriptive action in a timely manner based on that knowledge.
The ability to collect high-frequency data and analyze it in real time is driving revolutionary advancements in production management, providing information on a granular level to monitor each individual well’s performance and build the foundation of autonomous well operations. Similar to autonomous cars, autonomous control systems continuously scrutinize data to make decisions and execute appropriate actions to keep artificial lift equipment and producing wells operating at peak performance.
“That is why real-time data is key to where the production world is headed,” he contends, explaining that high-frequency data provides the granularity necessary for a detailed diagnosis of well health. But just as importantly, he says capturing real-time data at frequent intervals makes possible what he calls “the next big step” in production operations: autonomous control.
“With the right data management and computing tools, autonomous decisions can be made every second to maximize artificial lift performance and keep production on line,” Cueto holds.
The positive economic impacts of optimizing production with autonomous control take on particular significance when fiscal margins come under pressure. And as the industry emerges from a period in which pressures have been intensified to the breaking point, he contends that the value of the technology is more compelling than ever.
“With shut-in wells now starting to be brought back, the experience of getting wells up and running again will make it obvious that next-generation well intelligence and automation is the right investment,” Cueto suggests. “Operators have to know how the well behaved before shut in to figure out how to restart equipment and production. One of the hard lessons many companies are learning is that they do not have the historical data to determine that.”
He says restoring shut-in wells can be a complex undertaking, particularly where scaling, paraffin, corrosion and other downhole issues occurred in the past. “Starting an electric submersible pump in an idled well with scale or paraffin buildup can lead to serious equipment damage, which would mean spending a lot of capital to get that well back,” he states. “The risk is typically lower in a rod-lifted well, but the challenges are similar. It gets back to having the data to understand and optimize well operations.”
End-To-End Solution
The solution, Cueto says, is the Weatherford Production 4.0™ ecosystem, an end-to-end production management solution. Anchored by the ForeSite® platform, this solution comprises intelligent surveillance, next-generation automation and networking functionalities that take well control into the realm of autonomous operation. The integrated hardware and software leverage Internet of things, cloud and edge computing, artificial intelligence, and remote monitoring in a low-cost, easy-to-deploy package.
“All of this capability is contained in a small box that can be connected to any well controller or existing communications network,” Cueto explains. “Cutting-edge autonomous well control does not have to be complex or expensive to implement.”
Nor does it require high-output wells. In fact, the cost-versus-benefit proposition of the technology is so powerful that Cueto says it can pay for itself in only a few days’ worth of saved downtime on wells producing as little as 20-30 barrels a day. “It’s almost like having a person sitting on the well looking at the data and making the right decisions every single second to optimize performance,” he describes.
The value of real-time data analysis and autonomous control is magnified when installed on multiple wells on a pad or in a field. “When you do the math barrel by barrel, we are talking about a huge return on investment by keeping all the wells lifting oil,” he relates. “Autonomous capabilities will be a true differentiator.”
To illustrate the point, Cueto references a pilot project consisting of fewer than 100 wells in which Production 4.0 and ForeSite solutions were installed. “The total savings were on the order of $17 million annually,” he reports. “The investment in the technology becomes minimal compared to the savings provided by maximizing performance and minimizing downtime.”
Integrating autonomous well operations with high-frequency data also has several secondary benefits, including improved equipment reliability and enhanced safety and environmental performance. Moreover, the insights delivered give operators big-picture perspectives on critical operational questions, such as determining the optimal lift solution for every stage of a well’s life. “This technology is all about answering those kinds of questions and taking the most effective action,” Cueto avers.
He envisions autonomous well control evolving similar to autonomous vehicles. “The technology will continuously make optimal decisions in real time to ensure uptime and safety,” Cueto remarks, adding that autonomous workflows one day may be combined with advancements such as Weatherford-patented rigless intervention techniques. Just as an autonomous vehicle makes a decision to turn a certain direction to reach a designated destination and then executes that action, autonomous well control systems could identify the right time to change out a downhole pump and then seamlessly program that task's execution.
“That is the path forward,” he envisions.
Filling The Gap
With prices making a gradual recovery since bottoming out in late April, producers across the country are looking at the economics associated with restarting wells. As they do, they also are re-evaluating the possibilities of more fully leveraging existing technology to drive as much value as possible to the bottom line. There is no better case in point than fiberglass sucker rods, asserts Russ Rutledge, chief executive officer at Superod.
According to Rutledge, operators are taking advantage of the unique weight, strength and elasticity attributes of fiberglass rods to not only lower production costs, but also expand the application wheelhouse of beam pumping to higher-rate wells. Specifically, he says fiberglass rods provide a new option for wells in which rates have declined below the levels where ESPs achieve maximum efficiency, but above the operating range of beam pumps equipped with conventional steel rods,
“Fiberglass rods allow beam pumps to fill a significant gap between ESPs and traditional beam pumping technology,” he remarks. “These are wells that have declined to between 500 and 1,000 bbl/d of fluid. Fiberglass rods are lighter and stronger than steel, so they can move more fluid using the same or smaller size pump, and they do it at much lower cost than an ESP.”
The material properties of fiberglass rods–including light weight and high strength–allow them to move more fluid than steel rods with the same size of pump, giving operators a new option for filling the operational gap between electric submersible pumps and beam pumps as initial IPs decline. Operators in the Permian Basin are successfully using Superod fiberglass strings in horizontal wells producing up to 1,000 bbl/d, saving cost and minimizing potential downtime.
In Permian Basin tight oil wells, initial daily production rates as great as 5,000 barrels require an ESP, but production declines quickly, and wells invariably cycle through different ESPs before ending up on rod lift, Rutledge notes. “Fiberglass rods let producers move to beam pumping sooner, which saves money, reduces downtime and recovers more oil,” he remarks.
Installing fiberglass rods in Permian horizontals that previously produced with ESPs has kept Superod busy the past few months, Rutledge reports. “Now, as operators start to figure out which wells to restart and how to accomplish that, they are recognizing that there is no better nor more efficient way to move fluid to surface than fiberglass rod pumping.”
Getting the fluid column lifted off the perforations as quickly as possible can be important when restoring shut-in wells, Rutledge adds. “Because the wells have not been produced for some time, they have high fluid levels that need to be produced to restart production. The faster water can be moved off, the sooner they can get to oil,” he says.
For wells with fiberglass rods, the restart process is enhanced by the rods’ inherent corrosion resistance and high lifting capacity. And once they are back on line, those same attributes reliably keep production flowing to the tank battery. “The composition of the fiberglass rod body and the patented steel end fitting creates a product that will last longer and handle more load than any other sucker rods on the planet,” he claims.
Failure-Proof Design
The life cycle cost and performance metrics of fiberglass rods have been further augmented by new automated assembly procedures that ensure “every rod is perfect every time,” as Fred Morrow, Superod’s vice president of engineering, puts it.
“What is an acceptable failure rate? Is it 1%? How about 0.1%? At 0.1%, one in every 1,000 rods fail,” Morrow observes. “If wells average 100 rods apiece, every tenth well will have some type of rod failure. That is unacceptable. We have to be 100% failure-proof, 100% of the time. That was the goal in investing in automation.”
The biggest step change at Superod’s manufacturing facility is computer-controlled installation of end fittings, which had been a labor-intensive manual process. As Morrow describes it, automated machines apply aerospace-grade adhesive to the fitting before it is installed onto a cleaned rod and rotated at a precise increment to seat on the rod end. Then, heat is applied to the assembled rod to harden the thixotropic adhesive and create an integral bond.
“The consistency from one rod to the next is outstanding,” he reports. “We literally go weeks without having a bad fitting.”
Similar to the design principle that allows tubing slips to grip tighter as weight increases, Morrow says the end fittings and adhesive work in concert to provide compressive strength, so that the harder a rod is pulled, the stronger the bond becomes between end fitting and rod body. “A 1-inch fiberglass rod weighs 0.82 pounds per foot compared with 2.9 pounds per foot for a 1-inch steel rod, yet a fiberglass rod is much stronger and more stress resistant,” he summarizes.
The lighter weight and enhanced strength mean a 20% smaller motor can achieve the same production rate using a fiberglass rod string, which slashes power costs. That is largely because of the “stretch” of fiberglass weighted at bottom with steel rods or sinker bars, which effectively increases downhole pump stroke by as much as 25%, Morrow explains, noting that the standard Permian string design uses 90% fiberglass rods and 10% sinker bars.
“Unlike a steel string, which typically has a significantly shorter downhole stroke than surface stroke, we are taking 2 pounds per foot out of the rod string’s weight, yet moving more fluid per stroke,” he relates.
The ability to move more fluid than their steel counterparts is the key to expanding fiberglass rod applications. Citing the example of high-IP, high-decline curve Wolfcamp wells in the Delaware Basin, Morrow says operators initially install a high-horsepower ESP, but within a few months are forced to change to a smaller ESP and then to a beam pump as fluid volumes decline.
“One customer asked about using fiberglass rods in wells making 800-1,000 bbl/d. The idea was to eliminate the smaller ESP and go straight to rod lift,” he recalls. “We design rod strings for almost infinite life, so we were not real comfortable with it at first. But the company said it would consider six months of service life acceptable, so we agreed.”
The operator’s thought process, according to Morrow, was grounded in economics. If replacing an ESP has a price tag of $150,000-$200,000 and a fiberglass rod string can be installed for $40,000, replacing the rod string after six months still represents only half the cost of replacing an ESP. “Rod pumping is the cheapest lift solution, and the customer was going to have to switch to rod pumping at some point anyway as production tailed off,” he reasons.
Some of the first installations of those rod strings have now been in service for more than six months without a failure. “That tells us that the rods are even stronger and more durable than we thought,” Morrow offers.
And that’s saying something given that the same fiberglass strings have been in service in some Permian wells for 25 years and counting. According to Morrow, Superod launched a two-year warranty program in 2011 under which it guarantees to pay the pulling cost if a rod causes well failure. “The rods manufactured since then have pumped billions of cycles and there has not yet been a single failure claim,” he concludes.
Lift Optimization
XSPOC 3.0, the latest release of Apergy Corp.’s artificial lift optimization software, uses physics-based diagnostics and artificial intelligence to monitor, control and optimize rod lift, gas lift and electric submersible pump systems. It updates the XSPOC platform to enable set point optimization of rod lift wells and AI-driven classifications for ESPs to allow users to better use their production assets with less resources and time, the company says.
XSPOC is used to optimize 125,000 wells across the world. The 3.0 update also includes further development of XSPOC’s physics-based diagnostics for ESP and gas lift wells, including additional flow models and equipment specifications, Apergy says.
“The latest release addresses key challenges faced by our customers,” notes Terry Treiberg, general manager of Apergy’s Theta Oilfield Services business. “Our field trials with our rod pump set point optimization have been well received and yielded real results. Our customers are pleased with the direction XSPOC is moving–full autonomous control for all methods of artificial lift.”
XSPOC’s AI automates processes that are performed manually, Apergy describes, making decisions based on specified parameters to optimally control lift performance. The software communicates with field devices, and performs both control and data acquisition tasks using its own polling engine. XSPOC also integrates with all major SCADA platforms, and works with third-party software such as Wellview and Open Wells. It can be visualized in tools such as Spotfire and Tableau.
Paul Mahoney, president of Apergy’s production and automation technologies segment, says the XSPOC 3.0 release is the culmination of multiple facets of the AL business.
“Our core artificial lift competencies of service and field excellence, system design prowess, and optimization expertise come together to transform disparate data into meaningful insights for our customers. The result is enhanced production efficiency with lower costs for our customers.”
Pumps For Many Applications
According to GR Energy Sercives, hydraulic jet pumps (HJP) have many unique advantages. Compared with conventional lift systems, HJPs can handle the large concentration of solids and high gas volumes often seen in today’s unconventional wells. In the GR Energy Services Flex Flow system, the jet pump partners with the company’s horizontal pumping unit (HPS), which features variable speed drives, surface controls and automated reporting capabilities.
The trailer-mounted horizontal pumping system that GR Energy Services uses in its Flex Flow system combines with hydraulic jet pumps to offer a unit that can handle the large concentrations of solids and high gas volumes often seen in unconventional wells. The horizontal pumping unit features variable speed drives, surface controls and automated reporting capabilities.
The company says the flexible system can be configured for many scenarios, including conventional, reverse circulation and concentric, and can be combined with gas lift to optimize production. The reliable combination of the HJP with the HPS lowers operators’ lease and operating expenses by reducing costly well interventions and maintenance downtime.
“Our goal is to lift higher volumes and reduce operating costs by eliminating the common issues of gas locking and solids handling, maintaining production over a wide range of rates and reducing well intervention and maintenance downtime,” says Barry Donaldson, sales and marketing director at GR Energy Services.
He goes on to describe the trailer-mounted horizontal pumping system, which can be used to power fluid for single or multiple jet pumps, includes a centrifugal pump; a 480-volt, 3,500-rpm motor with three horsepower options–100, 300 and 500 hp; a thrust chamber to carry the thrust load developed by the multistage pump; a dual pot filter system; and a charge pump for suction, which supplies power fluids from tanks to the system.
The GR Flex Flow hydraulic jet pump consists of a nozzle, throat and diffuser. High-pressure fluid is pumped down the tubing through a nozzle, where the fluid velocity increases, causing a low-pressure differential that pulls in production fluid from the formation. The mixed fluids pass through a throat and into a diffuser, which converts the stream into a low-velocity/high-pressure fluid.
Donaldson says the hydraulic jet pump’s features enhance its suitability for challenging oil field environments. It operates efficiently in vertical, deviated and horizontal wells, can handle multiple well pad applications, and can be designed to sustain a wide range of production rates. “It has excellent gas and solids handling, and can handle returns up the casing in conventional applications or up the tubing for reverse flow,” he describes. “No workover rig is required for pump change-out, there are no moving parts down hole, and it can be retrieved easily by wireline or hydraulics for on-site maintenance.”
Both the jet pump and pumping units can be monitored remotely, allowing the operator to adjust them for optimum efficiency. Since it is digital cellular and satellite enabled, Donaldson says the system can be accessed with most tablets, mobile phones and computers.
For other great articles about exploration, drilling, completions and production, subscribe to The American Oil & Gas Reporter and bookmark www.aogr.com.