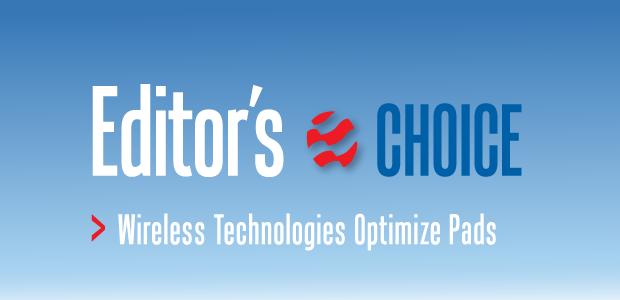
Wireless Technologies Optimize Pads
By Tom Bass
AUSTIN, TX.–Advances in wireless automation technology are driving both immediate and long-term cost reductions and operational efficiency in pad well production, helping oil and gas companies achieve operational excellence in tight oil and natural gas resource plays.
Operators cannot control prevailing commodity prices, but they can create value by changing the efficiency with which wells are brought to production and operated. Leveraging wireless automated solutions is allowing producing companies to achieve significant productivity improvements on their multiwell pads. This shift in operational philosophy and risk tolerance demonstrates the benefits of changing traditional operational strategies.
The willingness to adapt and change has made a positive impact on how production facilities are designed and constructed in shale plays, ensuring more efficient use of capital and reliable operations for the duration of a field development. In fact, based on a study of 34 North American operators, the companies using standardized well pad designs and the latest wireless automation technologies have attained a capital savings of more than $75,000 per four-well pad, while also improving production performance and reliability.
Operators realized significant cost savings during the downturn as a result of reduced rates for labor, material and other market-driven costs, in addition to applying advanced production processes to drilling and completion operations. Through these efficiencies and cost deflation, the breakeven prices for operators across all basins decreased. However, only an estimated 30-35 percent of the cost reductions made during the down cycle can be attributed to repeatable efficiencies. The other 65-70 percent were based on temporary market conditions, and cannot be sustained as commodity prices recover and stabilize at higher levels.
An example of sustainable cost reductions for drilling would be upgraded rigs that reduce cycle times and result in more wells drilled per rig. Alternatively, primary cost inputs such as day rates or drill pipe and drilling mud are cyclical, and are expected to increase significantly as industry drilling activity rebounds.
Sustainable reductions in completed well costs only can be achieved when operators re-evaluate and modernize legacy operating practices and engineering standards. Wireless sensors and remote telemetry units (RTU) provide an automation architecture that enables a standardized well pad design, streamlines construction processes, reduces waste and increases the speed of execution necessary to achieve long-term sustainable results.
Demonstrable Impact
Wireless technologies can have a demonstrable impact on three of the top five lease operating expense (LOE) line-item costs: repairs and maintenance, production chemicals, and labor. Together, these costs account for 45 percent of total LOE on a per-barrel-of-oil-equivalent basis.
Advanced wireless monitoring capabilities enable a lease operator or pumper to focus on the highest-value tasks while on a pad site or central production facility, and reduce safety risks associated with loss of containment. Seamless integration enables operators to access actionable diagnostic information through local or secure wide-area communications without complicated integration work to expand operational visibility and add a layer of protection from manual errors, further reducing safety risk and enhancing productivity.
As part of an overall asset operational excellence strategy, wireless technology helps operators attain measurable performance improvements in facility construction costs and scheduling. The results of the collaborative benchmarking cost analysis of 34 operators showed an average savings ranging from $30,000 per pad in dry gas fields in the Appalachian Basin to more than $200,000 per pad in Williston Basin tight oil plays. Although differences in savings varied based on the type of field, geography and facility, all operators saw sustainable savings by implementing wireless technologies.
Figure 1 compares wireless and wired sensors and associated controllers/RTUs with equivalent functional specifications for wellhead, separation and tank battery facilities. It is based on operator data from the Eagle Ford, Permian Basin, SCOOP and Bakken/Three Forks. Results of the analysis were normalized to a four-well pad design and the median values were used to account for any field, operator, geographic or facility-related circumstances that could skew costs either higher or lower.
Each implementation has its own subtle differences. For example, the costs for labor or wiring on a unit basis are usually different depending on operator or geography. In addition, facility configuration–including number of tanks, wellheads and separation vessels–can vary based on an operator’s standardized approach and the underlying geological characteristics. Given those differences, a representative sample was assembled and normalized to a common unit basis to demonstrate the impact.
In addition to the savings achieved by using wireless instrumentation on wellhead, separation and tank equipment, adding the scalable functionality of a distributed RTU network generates incremental cost savings to the benchmarking analysis. The analysis suggests that for every $100,000 in completed well cost savings, an operator can expect a 1-3 percent increase in the full-cycle rate of return. Moreover, the operators in the analysis realized a 50-60 percent reduction on average in the time required to automate multiwell pads. The value of earlier production yields five-10 times the increase in revenue than the quantifiable cost savings.
The distributed RTU network is a flexible framework that enables faster completion of a well when the time is right. As compared with a traditional architecture, operators see major reductions from trenching, wiring and infrastructure. The native integration of wireless technologies also greatly reduces the amount of engineering and programming required.
The drag-and-drop capabilities of a distributed RTU network quickly bring new wells onto a reliable communication link to a supervisory control and data acquisition backhaul network as well as other local network nodes. This functionality improves operational efficiency through the addition of wells, equipment, or functionality to a site simply through the scalable nature of the distributed RTU network.
Leveraging wireless automated solutions is allowing producing companies to achieve significant productivity and reliability improvements on multiwell pads while also reducing safety and security risks from the wellhead to the custody transfer point. A study of 34 operators active in various shale plays found that using standardized pad designs and wireless automation technologies saved more than $75,000 on average per four-well pad.
Wireless Sensor Networks
WirelessHART® is the first open wireless communication standard specifically designed for process measurement and control applications. Developed by a consortium of companies as part of a nonprofit membership organization for industrial wireless sensing, the protocol utilizes a time synchronized, self-organizing and self-healing mesh architecture.
With more than 32,000 operational WirelessHART sensor networks now installed worldwide, leading manufactures and producers across all industries have proven the benefits of standardizing on wireless sensors to monitor production parameters. Specifically, oil and gas operators have been able to realize these benefits by monitoring wellhead, separation and tank equipment to reduce the time and resources needed to get wells on line, while also reducing risk by eliminating wiring and loop-checking procedures. These benefits are not achieved through a trade-off in the reliability of the measurement. In fact, WirelessHart has demonstrated at least a 99.9 percent signal reliability in some of the harshest conditions across tight oil basins.
Utilizing wireless sensors to enable well pad automation not only reduces infrastructure costs, but also eliminates common automation failure points such as grounding errors, corrosion, cracked insulation, loose connections, and crushed conduits or broken wiring caused by well workovers or infill operations. One operator in North Dakota was able to reduce the amount of wellsite call-outs by 96 percent by eliminating communication and equipment-related failures through reliable wireless monitoring methods. These savings are harder to quantify, but can be dramatically greater than even the initial savings in capital expenditures.
Fit-For-Purpose Program
To support the need for oil and gas companies to improve financial results and achieve operational excellence in pad well developments, a fit-for-purpose technology and engineering-based program has been developed that focuses on four key areas: improving reliability, minimizing emissions, ensuring safety and optimizing production.
The foundation of this new model is a portfolio of innovative sensors and analytics packages that are easy to install and maintain by converting infrequent, manual collection to real-time data. These packages automate manual tasks and monitoring of corrosion, electrical equipment condition and consumption, and eliminate the need for failure-prone mechanical parts such as pressure gauges and level controls. The technology easily optimizes performance through non-intrusive technologies such as temperature, corrosion and acoustic instrumentation and cost-effective data acquisition using multivariable and distributed/flexible inputs/outputs.
This set of emergent technologies brings real-time visibility into operational performance to analyze and identify operations that could be improved in the areas of safety, reliability, production and emissions.
By monitoring equipment and process variables, producers can reduce safety and security risks, and be alerted to any issues so they can respond quickly. Automated tank monitoring and gauging is a good example. By applying wired or wireless level monitoring, the operator can gain continuous insight into tank levels, minimize high-level alarms and prevent spills in accordance with the API MPMS Chapter 18.2 standard (Custody Transfer of Crude Oil from Lease Tanks Using Alternative Measurement Methods).
This allows workers to stay off the top of tanks, eliminating safety risk from manual tank gauging, while also reducing measurement uncertainty. Operators can also detect oil/water interfaces to prevent oil losses to the water tank.
With respect to reliability, wireless sensors automatically detect conditions that can lead to equipment failure, replacing periodic manual readings with online insights into equipment health. An example is pressure gauge replacement on wellhead tubing, casing and bradenhead pressure measurements. With this technology, operators can monitor casing and tubing pressures along with chemical tank levels with wireless pressure gauges.
Wireless pressure gauges improve reliability and reduce traditional gauge failures by eliminating mechanical bourdon tubes. Harsh process environments such as vibration, overpressure, extreme temperatures and corrosion can cause bourdon tubes to stretch, freeze, break and experience issues from unexpected damage. State-of-the-art digital pressure gauges reduce gauge failures and ensure better accuracy and performance.
Optimizing Production
Increasing the amount and type of information coming from field assets gives producers predictive analytics to reduce deferred production by optimizing tasks with more accurate, reliable and timely information. An example of this is improper separator temperatures, which can reduce separation efficiency by not allowing emulsions to break up and inhibit reaching correct vapor pressure limits for transportation requirements, or boil off valuable natural gas liquids reducing crude quality. Adding wireless temperature measurements to a well pad heater treater helps achieve optimal separator temperatures in existing and new assets.
Another example is optimizing production chemical usage by monitoring the chemical tank level and correlating changes in chemical levels to production data. One operator that implemented this additional monitoring reduced chemical usage by 180,000 gallons a year. An existing WirelessHART sensor network allows operators to easily add the additional level sensor and integrate the data through existing methods without expensive wiring or a “one-off” monitoring solution.
At the same time, wirelessly monitoring emergency relief valves and tank levels ensures a quick response to upsets, minimizing emissions and improving the safety of storage tanks. This is critical, especially as tank emissions regulations continue to increase. Pressure vacuum relief valves and emergency vent/vacuum relief valves prevent tank damage caused by abnormal situations and pressure surges. By monitoring the activity (opening/closing) of relief valves, operators can ensure a quick response to upsets.
Bringing It All Together
Beyond drilling and completion operations, a wireless sensor network can improve reliability as well as health, safety, security and environmental risk mitigation through cost-effective, real-time asset monitoring. Gaining visibility into the condition of a producing asset can reduce overall LOE, improve cash flow and ensure more predictable operations.
A seldom considered hidden profitability lever is the opportunity cost of deferred production related to infrequent or unreliable tank inventory management. An Eagle Ford operator realized a 6,600 boe/day production increase throughout the course of a year simply by monitoring in real time the inventory levels in its tank batteries, reducing shut-in events. This timely information also can optimize transportation service costs by increasing the confidence in inventory levels and dispatching transportation service providers only when necessary.
In addition, wireless monitoring of continuous and high tank level conditions reduces one of the largest safety hazards to company and contract employees in production operations: exposure to vapor during manual gauging and fluid transfer operations.
Increasing well productivity is undoubtedly the largest lever for improved well economics, but wireless technologies can provide operational efficiency and true sustainable cost savings. Wireless solutions enable operators to reduce their cost basis through efficient facility construction and a scalable architecture, delivering future flexibility for field developments and production optimization.
Operators that standardize on wireless capabilities can improve production, reliability, emissions and safety, and when economics dictate further field development, a wireless infrastructure gives them the ability to be more responsive than their competitors.
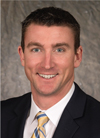
Tom Bass is the wireless business development director at Emerson Automation Solutions Rosemount, headquartered in Shakopee, Mn. Since joining Emerson in 2006, he has served in several industry focused business development roles. In his current capacity, Bass is responsible for leading business development for Rosemount Wireless and manages the Plantweb™ pervasive sensing application portfolio.
For other great articles about exploration, drilling, completions and production, subscribe to The American Oil & Gas Reporter and bookmark www.aogr.com.