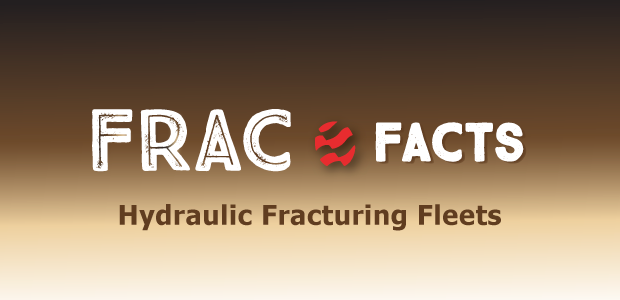
Advanced Equipment Accelerates Completions
By Colter Cookson
To optimize well economics, operators need both an effective completion design and the ability to implement that design quickly and affordably. For completion crews, the quest for efficiency means constantly revaluating proven processes to eliminate even brief intervals of downtime. They understand that faster completions accelerate producers’ ability to generate revenue and deliver energy that is critical to both modern life and U.S. influence abroad.
Smarter completions simultaneously reduce environmental impacts and safety risks by helping operators bring each well on line with fewer trips to and from the pad. These benefits can be hard to quantify precisely, but even the most conservative and straightforward estimates show they are significant. Given these realities, many service companies express pride in helping completion engineers get more for less. Their latest equipment empowers hydraulic fracturing fleets to pump longer, simplifies post-frac sand control and improves refrac economics.
Electrifying frac fleets can help operators improve efficiency and reduce emissions, observes Chris Buckley, president of ST9 Gas + Oil, a subsidiary of Liberty Oilfield Services. To maximize these benefits and reduce the costs associated with building electric fleets, he says ST9 has set out to create purpose-built electric frac pumps.
“A traditional electric fleet uses conventional pumps designed for mechanical drive trains,” Buckley describes. “This lets operators run on natural gas, but the power efficiency can be low. To boost it, we decided to use electric motors developed by the automotive industry, which has invested billions of dollars improving motors’ efficiency, power density and reliability.”
Automotive Technology Transfer
Each of ST9’s digital frac pumps is driven by 10 electric motors, an approach Buckley says has several advantages. “The first is redundancy,” he begins. “If a motor goes down, the pump will keep working with nine. If a second motor fails, the pump once again will recalculate torque requirements and keep pumping. And so on.”
That redundancy should rarely come into play, Buckley assures. “The motors are based on a design that has been installed in tens of thousands of 18-wheelers in Europe, so they are reliable and cost-effective,” he reports.
With pumps driven by electric motors from the auto industry, ST9 Gas + Oil says it can reduce the costs associated with building electric hydraulic fracturing fleets. In addition to offering environmental benefits, the company’s pumps simplify operations by automatically dividing work among themselves to achieve target rates.
Dividing the workload across 10 motors can shrink peak electricity needs, Buckley says. He explains that electric equipment draws the most power when it is turned on (which is why house lights sometimes dim when a cook begins using an electric kettle). By bringing the motors on line in sequence, ST9 eliminates this sudden demand spike, which is called inrush current.
“To account for the inrush current, frac fleets in West Texas may need the capacity to generate 27 or 28 megawatts of power even though the pumps only need 20 megawatts once they stabilize. Because our pumps use small individual motors, we can cut the genset count by about 22%,” Buckley calculates.
The pumps communicate with each other to distribute load and deliver the desired torque. “The crew puts in the desired rate, and the control system figures out how to achieve it while spreading the load across the pumps to maximize each pump’s longevity,” Buckley details. “It’s a push-to-frac system that makes the frac crew’s job easier and gives the company man confidence water is going down hole at the rate the engineers recommend.
“The target rate can be adjusted in increments as small 0.1 barrels a minute,” Buckley adds. “It’s easy to slow the rate to perform a pressure test or to clean out a well that has screened off.”
The control system keeps the pumps running efficiently, Buckley assures. “During field tests, we would often hear crews say things like, ‘that’s the smoothest 14 barrels I have ever seen,’” he recalls.
That smooth operation reduces pump wear and tear, Buckley points out. “Given the pumps’ longevity and the amount of data we can collect on motor conditions, we think we will be able to reduce repair and maintenance costs by 10%,” he says.
Noting that vibration is a sign of wasted energy, Buckley adds that the pumps reduce noise. “The pumps are quiet enough people can have a conversation next to them,” he says. “In fact, people will barely hear the pump unless they are near one of the gensets, and even those are quiet.”
Powering the generators with field gas can slash fuel costs, Buckley remarks. “The exact savings will depend on the price of natural gas and how much field gas the operator can use,” he notes. “For a fleet powered entirely by field gas, the estimates range from $12 million to $16 million a year.”
Buckley adds that an electric fleet using ST9’s pumps will have an upfront cost comparable to a fleet of pumps driven by Tier IV Final dynamic gas blending engines. “A conventional electric fleet generally costs 50% more than a DGB fleet, putting the price tag around $60 million,” he contrasts. “We can eliminate that premium and allow the industry to switch from dual-fuel engines to electric fleets that combine environmental benefits with efficiency gains.”
Accelerating Completions
By developing an integrated completion system, SEF Energy’s Downing brand aims to speed completions, says Tim Marvel, the company’s vice president of business development and technology. “Our goal is to make completion operations so efficient a crew can pump 24 hours a day, every day. We already have eliminated transition time between stages, and we are testing a technology that should get rid of downtime associated with pump maintenance,” he says.
According to Marvel, those advances can shave several days off completion times. “Today, most fleets plan on pumping about 16 hours a day, with the exact time depending on the basin,” Marvel reports. “By eliminating transition time between stages, the integrated system enables them to consistently pump 20-plus hours a day. As we get rid of maintenance-related downtime, they will be able to pump nearly 24 hours a day as long as the pad has sand and water.”
That 24-hour target is not idle speculation, says Brian C. Wiesner, Downing’s president and chief operating officer. “Our system has helped companies pump 24 hours a day several times, and we have pumped as long as 68 hours,” he reports.
By using pressure-equalizing valves to collapse the transition time between stages, SEF Energy’s Downing brand says its integrated completion system is enabling hydraulic fracturing fleets to pump 20 or more hours a day. To unlock even greater efficiency, Downing reports it is testing equipment that allows fleets to pull pumps for maintenance while the others continue putting water down hole.
The extra productive time adds up, Wiesner assures. “For one of the system’s early adopters, an operator in the Delaware Basin, we were able to complete a 17-month work plan in only a year,” he illustrates. “In addition to reducing costs, this had a huge impact on the operator’s environmental footprint and safety because it burned less fuel, required 300 fewer crew changes and reduced personnel exposure hours.”
The key to collapsing transition time between stages is an automated valve with three chambers that sits on top of the frac stack. When it is almost time to move to the next stage, the valve automatically equalizes the pressure between the surface and wellbore so it is safe for wireline to enter the well, Marvel describes. He points out that this eliminates the need to pressure down and conduct pressure tests between stages.
“As a stage concludes, we slow the pumps down and press a button to move to the next stage. The computer responds by opening the next well, transitioning the zipper to it and closing the first well, at which point we can ramp the pumps back to treatment pressure,” he relates. “The entire transition takes 20-30 seconds.”
The pressure-equalizing valve eliminates the need for a gate valve and the unplanned downtime associated with cutting wireline, replacing or greasing gate valves, and chasing leaks, Marvel mentions.
Because the system is integrated, a single controller oversees the zipper valves, pump down valves and flowback valves, he adds. “This integration lets the operator and fracturing company see exactly what is going on in the pad during the operation. The system timestamps each event and sends collected data to the cloud, which can enable remote operations and aid with post-job analysis,” Marvel says.
Every time a valve actuates, the system automatically greases it, Marvel continues. “By monitoring grease cavity pressure, the system can tell when the void is full,” he says. “This keeps us from injecting too much grease, which cuts consumption 50%-90%.”
Hot-Swapping Pumps
Having addressed post-stage transition time, Downing has turned its attention to pump maintenance, Marvel relates. “Today, frac fleets generally have to stop pumping every so many stages to pull pumps out for maintenance. In the Haynesville, this happens after almost every stage,” he says. “To get rid of that downtime, we have designed equipment that lets operators knock pumps out for maintenance and put them back in without stopping the frac.”
Wiesner predicts this capability will save time and shrink pump counts. “After a lengthy pump run, pumps often have costly damage that will take several hours to repair,” he says. “With this system in place, fleets will be able to avoid that damage by pulling pumps out one at a time for preventative maintenance. The extra reliability also may allow them to bring fewer backup pumps on site, increasing fleet utilization. For example, a 20-pump fleet may only need 18.”
Wiesner stresses that the automated connections improve safety. “When the pump needs maintenance, the system isolates the missile and the truck, then disconnects the truck so it can pull out. There is never a need to put anyone in the red zone,” he says.
Headache-Free Desanders
As proppant loadings have increased and 100-mesh proppant has gained popularity, removing sand from produced oil, water and gas has become more important, says Anthony Sisto, vice president of U.S. sales for Specialized Desanders Inc. “When sand comes to surface during flowback without proper controls, it can damage surface equipment and facilities,” he warns. “In extreme cases, this damage can present safety risks. It also causes downtime that reduces initial production.”
To remove sand from flowback at the wellhead, Sisto generally recommends a horizontal gravity desander. “The beauty of our gravity desander is its simplicity,” he says. “Instead of generating an external force to separate the sand, the desander temporarily reduces the fluid’s velocity and allows the sand to settle out of suspension through gravity.
The horizontal desanders in front of these pumpjacks protect downstream facilities from sand-induced damage by temporarily slowing the production stream’s velocity so gravity can force the sand to settle out. With no moving parts or consumable components and a large storage capacity, Specialized Desanders says the gravity desanders are reliable and easy to operate.
“The temporary reduction in velocity occurs in part because the vessel is larger than the pipe that flows into it,” Sisto describes. “I often compare the process to whitewater rapids. When the stream is narrow and filled with rocks, the water is extremely turbulent and therefore capable of carrying sand downstream. Once the stream widens and deepens, the water calms and sediment sinks to the bottom.”
In addition to allowing sand to settle out, the horizontal desander has significant sand storage capacity between cleanouts, Sisto reports. He adds that the pressure drop across the separator is miniscule.
“The only pressure drop comes from the typical friction introduced by the piping that brings the fluid in, so it is in single digits,” Sisto details. “In low pressure environments, minimizing the back pressure on the wellhead can boost production. In higher-pressure applications, operators no longer need to worry about an inconsistent pressure drop upstream of their choke, which gives them more precise choke control.”
According to Sisto, Specialized Desanders’ equipment rarely needs maintenance. “There are no wearable or moving parts since the vessel slows down the fluid too much for sand to damage its walls,” he says. “In fact, we still have units out in the field that we built when we started the company 20 years ago.”
The desander’s reliability and efficiency can free operators to produce wells according to reservoir and production engineer recommendations, Sisto says. He explains that they no longer need to choke the well back to limit how much sand comes to the surface.
“We also measure how much sand enters the desander so our clients know how much sand they are producing in real time,” Sisto says. “Instead of looking at wet sand outside the vessel, we weigh dry sand inside it and use specific gravity to calculate how much is there. This approach is more accurate.”
Sisto says this technique mirrors the one operators use to measure sand as it goes down hole during the frac job. This simplifies comparisons across processes and makes it easier to evaluate how variations in the completion design or flowback process affect sand production, he comments.
The measurements let the operator confidently remove the desander once it’s no longer needed and predict when the vessel will need to be emptied while it’s on site, Sisto adds. “Each unit has a sand storage capacity of several hundred pounds, and we know exactly when that capacity is full, so instead of blowing the unit down every 30 minutes or every hour, the operator only needs to clean it as needed. This reduces intervention and manpower requirements.”
Lengthening blowdown intervals also mitigates fugitive emissions, Sisto says. “When a blowdown does occur, the amount of gas released is small,” he assures. “With the right equipment, the operator could capture those emissions and get to ‘net zero.’”
Refracturing’s Benefits
Refracturing is becoming increasingly attractive, suggests Alfredo Sanchez, chief executive officer of MorphPackers Ltd. “The industry’s understanding of what it takes to do a successful refrac is growing on both the candidate selection side and the execution side,” he assesses. “In many cases, a refrac can generate a higher return on investment than drilling a new well.”
According to Sanchez, the data to which he has access indicates a refrac can get approximately 70% of a well’s original production for 40% of the original cost. “For a very old well with a low stage count, a refrac even may be able to exceed the original production by bringing the completion to today’s standards,” he comments.
“Over time, we have seen a shift in candidate selection,” he adds. “Historically, refracs often targeted wells that had poor initial results, which can mean throwing good money after bad. Today, refracs tend to be done on strong wells that merely experienced the rapid production declines common in unconventional plays.”
New interest in refracturing is driven in part by the environmental benefits, Sanchez reports. “Refracturing can let operators achieve production goals with fewer wells. In the short term, drilling three wells instead of five means they can build fewer roads, clear less land and burn less fuel. In the long run, it means they have fewer wells to plug and abandon.
“By a conservative estimate, a refrac will save 150 tons of carbon dioxide emissions. This estimate is based entirely on emissions from fuel savings from drilling fewer wells. We have heard much larger projections that consider other factors,” Sanchez says.
“There are discussions underway about whether a refrac campaign can allow an operator to book additional behind-pipe reserves,” Sanchez adds. “If that pans out, refracs will give operators a way to bolster their balance sheets at a low cost or discount cash flows from future reserves.”
As refracturing techniques continue to mature and operators’ familiarity with refracturing grows, Sanchez predicts that refracturing will become commonplace. “Today, every refrac is a project that requires numerous meetings and approvals. In the future, refrac campaigns will be almost as routine as normal completions, and new wells will be planned and evaluated with a refrac in mind,” he suggests. “When they decide whether to invest in a well, engineers will look at not only the initial decline curve, but also the costs and benefits of a refrac.
“Like all completion techniques, refracturing has a learning curve,” Sanchez says. “The more operators do it, the better the results.”
Refrac Packer
According to Sanchez, the cost to refrac a well is shrinking as technology improves. He says MorphPackers’ expandable steel packers are one of many tools that are lowering costs and risks.
“When we talk to operators, they often tell us refracs generate attractive returns as long as they do not have any operational hiccups,” Sanchez says. “With that in mind, we have invested millions of dollars and years of research creating a packer that is easy to run and robust enough to minimize the chance something will go wrong.”
The packers are deployed by liner. As the liner is run in, the packers are added to it at the spacing required by the frac design. Once the liner reaches total depth, it is hung from the casing and a ball is dropped from the surface. “When that ball reaches the bottom, we pressure up and expand all the packers hydraulically,” Sanchez relates. “We do not have to burst any barriers, shift any sleeves or rotate the string. All we do is pump water.”
After the packers have expanded, the operator can proceed to frac using conventional plug-and-perf techniques, Sanchez reports. “We think the simplicity and familiarity of this approach is one of the big appeals of our technology,” he says.
According to Sanchez, the packers provide strong isolation at an affordable cost. “As we developed the packers, our goal was to offer a middle ground between high-tech but expensive and operationally complex solutions and pump-and-pray or bullhead refracs,” he describes.
The packers preserve much of the well’s inner diameter. “In 5 1⁄2-inch casing, a traditional refrac liner would have an inner diameter of 3 1⁄2 inches unless the operator was willing to use a potentially unreliable isolation technique, such as cementing. Our refrac liner for 5 1⁄2-inch casing has a 4 1⁄2-inch inner diameter, enough that the refrac can be pumped at the 50-, 60- or 90-barrel-a-minute rates many refrac engineers prefer.”
Sanchez says the expandable steel packers have been deployed five times: twice in the Permian, twice in Oklahoma, and once in the Bakken. “In the Bakken, we used the packer not for a refrac but to provide isolation when leaks occurred during the original frac. Our packers were very successful,” he reports.
For other great articles about exploration, drilling, completions and production, subscribe to The American Oil & Gas Reporter and bookmark www.aogr.com.