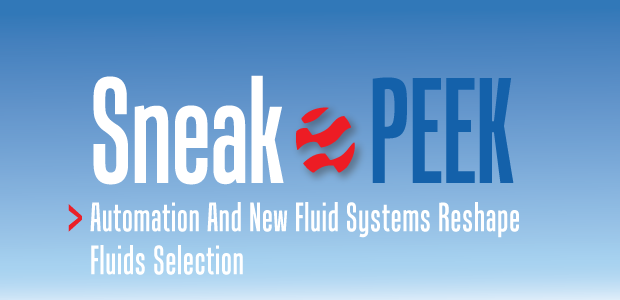
Fluids Chemistry
Automation And New Fluid Systems Reshape Fluids Selection
By Colter Cookson
Selecting the right drilling and completion fluid for a well can have a huge impact on drilling costs and long-term productivity, so fluids providers do everything they can to identify the best fluid for a particular application.
To simplify that process, they are building robust, easily maintained databases of past work, and developing tools that can translate those records into advice for future jobs. Much as Netflix or YouTube draw on personal histories to predict exactly what a specific subscriber will enjoy, fluids providers report they are leveraging these tools to help fluid engineers pinpoint appropriate formulations for a specific well.
“Digital is infiltrating every area of the oil field, not just drilling and completion fluids,” observes William “Billy” Dye, vice president of drilling and completion fluids at Newpark Fluids Systems. “With global databases, we will be in a position to put information from thousands of wells at the engineers’ fingertips and significantly augment their experience and company legacy data.”
By using automatically-collected mud properties to guide simulations, drillers are getting an increasingly accurate view of what is happening down hole, Newpark Fluids Systems relates. For example, the company’s simulation software estimates equivalent circulating density to within a tenth of a pound per gallon of actual measurements taken by downhole tools.
The key to turning vast global databases into safer and more efficient drilling is to expedite finding and analyzing relevant data, Dye suggests. He says Newpark has developed search tools that will enable engineers to quickly identify offset wells with comparable downhole environments and trajectories.
“These tools have the ability to drive step-changes in operational performance,” comments Travis Vordick, one of Newpark’s Midland-based technical sales engineers. “When drilling picks up in an area that has been dormant, it takes only a few minutes to access data from offset wells and other analogs. We can then use that data to model trends and identify best practices.”
Alongside increasingly accurate and efficient simulations, this historical data often reveals potential issues before drilling begins, Vordick reports. “If we cannot eliminate these risks at the design stage, we can at least have a mitigation plan for them, so the operator has a solution on hand if they occur,” he says.
If an unexpected issue arises, Dye says the digital tools help engineers address them by highlighting approaches that have worked in similar wells.
“Eventually, we would like to measure mud properties in real time, send that data to the cloud, and simulate what is going on down hole so the project engineers can predict what will happen in the next 100 feet and adjust if needed,” Dye outlines.
To enable such real-time simulation, the industry will need to automate measurements of key fluid properties. According to Dye, it is moving in that direction. “We cannot yet measure all the properties that would go on an API mud report, but recent advancements in fluids automation are closing the gap,” he reports.
The automated measurements create the potential for accurately calculating downhole pressures in near-real time, Dye says. “For example, when we compare equivalent circulating density values from our simulation software with downhole tool data, they typically are within a tenth of a pound per gallon,” he reports. “This degree of accuracy gives operators the flexibility to continue drilling in the event of tool failure, which saves rig time and money.
“Managing ECD is one of the most exciting applications for real-time measurement and simulation,” Dye mentions. “When ECD goes awry, the potential for a lost circulation event increases, often resulting in nonproductive time. Getting it right more consistently should make a huge difference in overall well economics.”
Better Muds
Dye says Newpark is applying the same zeal to creating new muds as it is to developing digital tools. “For areas that need oil-based mud, we have introduced a non-aqueous fluid system with flat rheology,” he reports. “Because the system’s rheological profile is nearly independent of changes in wellbore temperature and pressures, the fluid delivers measurable improvements in hole cleaning efficiency and barite sag management.”
A cleaner hole allows drillers to achieve faster rates of penetration by improving cuttings removal efficiency and reducing annular pressure losses, Dye notes.
“We also are working on a next-generation, high-performance water-based mud,” says Tom Heinz, Newpark’s Western Hemisphere technical manager. “One of this mud’s key elements is a specialized polymer that performs three functions: building gel structure, encapsulating cuttings and controlling fluid loss. This minimizes the number additives on site.”
That simplification supports safety and environment, sustainability and governance initiatives by taking trucks off the road and letting the crew maintain the fluid with fewer lifts, Heinz says. He adds that it reduces the chance of accidentally applying too much or too little of a specific additive.
“The versatile polymer lays down a unique filter cake that typically is only 1/32 of an inch thick and is extremely slick, which reduces the risk of stuck pipe and improves drilling efficiency,” he says. “The polymer also improves the mud’s resistance to contamination and minimizes its reactivity to calcium or divalent ions, making performance more consistent.”
Dye points out that the polymer is commercially available. As it develops other components of the new water-based mud system, he says Newpark is advancing its sustainability by paying close attention to environmental impacts. “We are using plant-based chemistries that do not sacrifice performance and are characterized as renewable resources,” he says. “We also are optimizing our mud plants, offices and logistics to use power and water more efficiently.”
Vordick emphasizes water-based muds’ ability to improve many wells’ economics. “Drilling with oil-based muds generally makes more sense in wells with high temperatures, reactive formations or contaminants such as carbon dioxide and hydrogen sulfide, but in more benign areas, water-based muds can greatly reduce drilling costs,” he reports.
As a case in point, Vordick cites the Midland Basin. In an analysis contrasting 30 wells drilled using modern water-based muds with 30 wells drilled using second-generation oil-based muds and 30 wells drilled with first-generation oil-based muds, the water-based wells had 16% lower total fluid costs and were ready for completion an average of 4.5 days sooner.
“The water-based muds enabled faster ROPs in the laterals, but that is not the only reason they sped well construction,” Vordick says. “Drilling the entire well with a water-based mud also eliminates the need to switch from a water-based mud to an oil-based mud between the vertical and lateral sections, which saves time and pit cleaning costs.”
Vordick adds that water-based muds simplify cuttings disposal and reduce rental costs for some tools. “From conversations with Midland Basin operators, we think replacing oil-based muds with water-based translates to significant per-well savings.”
Progress Offshore
The demands placed on drilling and completion fluids in the Gulf of Mexico are growing, notes Samy Helmy, vice president of fluids and completion services at TETRA Technologies Inc. “As producers go into deeper waters and plan longer step-outs, managing pressures and circulating densities has required more creativity and collaboration,” he reports.
This TETRA Technologies Inc. facility in Port Fourchon, La., delivers clear brine fluids, specialty fluid blends and chemical additives, as well as lube oils and drilling fluids. The company says it is improving its manufacturing processes and pushing the envelope on which fluids can be reclaimed as part of a broader effort to help operators reduce costs.
To reduce capital and operating costs, operators increasingly share production facilities, Helmy adds. He says this trend has helped create a need for more environmentally friendly completion fluids.
“The production facility likely will comingle fluids from the fields it serves, so if any of them contain something that imposes an environmental restriction, that restriction will apply to all the fluids. For example, if one of the wells uses zinc, a priority pollutant that cannot be discharged, all the produced water will need to be either treated–if feasible–off shore or more likely shipped on shore for treatment,” he warns.
Zinc bromide completion fluids are still used despite zinc’s status as a priority pollutant because they offer the high densities needed to hold back extreme pressures, Helmy says. “Cesium formate can deliver those high densities with a more benign environmental profile, but because it is mainly produced in one facility and has been mined for decades, it is almost depleted and therefore expensive,” he says.
To offer a more affordable alternative to zinc bromide, TETRA worked with an operator in the Gulf of Mexico, where the use of zinc bromide was not feasible on a challenging project, to develop a new fluid that contains neither zinc nor formate. “We are really proud we were able to come up with an innovative fluid system that has never been used before,” he says.
The fluid was commercialized in 2015. In the Gulf of Mexico, the first-generation iteration was applied seven times, Helmy relates. “We are on the fourth generation,” he shares. “Today, we can offer both divalent and monovalent versions, including an extremely dense divalent fluid that can go above 17 pounds per gallon.”
For Europe, Helmy says TETRA is designing and validating variants that are stable from minus 40 degrees F to 375 degrees F, enabling their use in both winter and summer and during HP/HT projects. “Our novel fluid has the capabilities for almost every offshore application, but we believe we can always do something better,” Helmy says. “Much of our attention is on finding ways to reduce the fluid’s cost and improve performance.”
Saving Money
While cost savings can come from optimizing completion fluids’ design and manufacturing process, Helmy stresses that it is critical to look at ancillary activity as well. “Time is money,” he notes. “If we can improve those activities’ efficiency, we can provide value to our clients and help make their fields viable, which will create wealth for the country.”
One process on which TETRA has focused is displacing drilling mud from the well and replacing it with clean brine for the completion. “This involves using displacement fluids between the drilling mud and clean brine,” Helmy notes. “In an ultra-deepwater well, the interface between the mud and brine may have 800-900 barrels of contaminated fluid.”
In response, Helmy says TETRA developed an alternative displacement system. “This system uses radical chemistries that shorten the interface and cut waste by 50%-70%, which saves rig time and reduces overall costs,” he says.
Optimizing logistics is a key part of controlling costs in deepwater wells, mentions Joey Detiveaux, TETRA’s area manager for U.S. offshore completion services and fluids. “A deepwater well may require 10,000 or 15,000 barrels of fluid, 10 times as much as a shelf job,” he says.
To shrink required fluid volumes, Helmy says TETRA is modifying its manufacturing process to produce more concentrated additives. “The other key is maintaining the on-site fluid without losing rig time,” he relates. “A few years ago, if a well required completion fluids to be pumped at 40 barrels a minute, no filtration unit would have been able to keep up. We have created filtration units that use a unique design to handle twice the volumes with a small increase in rig footprint.”
Recycling fluid from one job to the next is vital to controlling costs, Detiveaux adds. “At our onshore facilities, we can restore fluids many in the industry would consider beyond use, which helps us offer attractive prices to customers,” Detiveaux says. “We are keeping our eyes open for ways to miniaturize equipment so we can bring some of those capabilities offshore and reduce shipping.”
For other great articles about exploration, drilling, completions and production, subscribe to The American Oil & Gas Reporter and bookmark www.aogr.com.