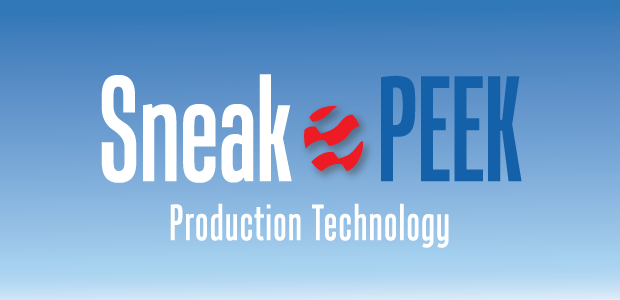
Modular Equipment And Clever Processes Help Shrink Lifting Costs
By Colter Cookson and Tim Beims
As operators and upstream service companies grapple with unpredictable supply chains and a tight labor market, they have had to work both smarter and harder to continue powering the U.S. economy. Add in the desire to reduce environmental impacts and safety risks, and the standards they use to evaluate new ways of doing business can be quite high.
“Everything sold today has to not only cost less, but also work better,” summarizes Larry Richards, executive chairman of VanZandt Controls LLC. “One or the other is not enough for an application to be considered a success.”
Automating equipment is one of many ways operators and service companies are reducing costs while improving performance, Richards observes. “By handling routine situations and providing real-time information on what is going on out in the field, automated equipment lets operators bring in more production with fewer personnel. Because those people spend less time driving to and from locations, it also improves safety.
“There is tremendous potential to continue using automation to limit flaring, reduce emissions and minimize the chance of spills,” Richards adds. “We see automation improving environment, sustainability and governance everywhere from the wellhead and tank batteries to pipeline compressor stations and produced water disposal wells.”
Richards attributes part of automation’s popularity to its growing affordability. “At VanZandt, we often work with customers to retrofit existing sites that are too marginal or peripheral to a company’s core business to justify long-term investments,” he reports. “The key is understanding the customer’s goals and recommending options that balance visibility and control with cost.”
Many retrofit projects are motivated by ever-lower emission limits. “In the Permian, changing regulations have dramatically lowered the amount of total volatile organic compounds that can be emitted not only by location, but by individual devices. These lower limits come with more onerous reporting regulations,” Richards relates.
“To reduce emissions and simplify reporting, it often makes sense to replace pneumatic valve actuators–which vent gas every time they open and close the valve–with electric ones,” Richards advises. “Installing electric actuators powered by a small solar panel can cost less than devoting manpower and time to documenting minor pneumatic leaks, and electric actuators come with the side benefit of tying into computer systems and providing greater visibility.”
For compact locations, instrument air can offer a lower-cost alternative to electric actuators, Richards continues. “Electric power is preferred when a site has access to clean power, but we sold a lot of automated air compressor skids in 2021 and expect that to continue,” he says. “When a site moves to instrument air, the pneumatic components can stay. Only the power source changes, so when a site is small enough for the compression system to distribute air efficiently, pneumatics can be quite cost-effective.”
Vortex Meters For Gas Lift
As automation moves forward, so does the equipment it controls, Richards assures. As a case in point, he cites skids for controlling gas lift injection rates. “Historically, these skids required a meter run behind the control valve,” Richards mentions. “Today, we are replacing the meter run with a vortex meter to save $2,000-$10,000 for each application.”
Skids for controlling gas lift injection rates are one of many areas benefiting from improvements in automation and equipment. VanZandt Controls LLC says the latest skids replace the meter run that traditionally would go behind the control valve with a vortex flowmeter that costs less to install and requires no maintenance.
Richards compares the vortex meter with an indestructible iron skillet. “There are no moving parts and no maintenance,” he explains. “The meter can run for 10 years or more without a significant change in its K value or reliability. There is no need to periodically replace orifice plates and almost no chance of particulate matter or paraffin clogging the line.”
Vortex meters work by measuring the vortices generated by a small obstruction (a stationary shedder bar) in the flow path. Richards says the meters excel in gas and produced water applications. “Once they see how robust the meters are, customers often convert similar applications to vortex meters across the field,” he reports.
The vortex meters work well in sand-prone situations, Richards mentions. The devices also handle wet gas, so when customers began asking for ways to measure the amount of gas captured by vapor recovery units, VanZandt developed a vortex-based metering tube that costs far less than a meter run, he relates.
VanZandt generally recommends vortex flowmeters from Schneider Electric, for which the company serves as the master distributor in the Permian Basin, the Eagle Ford, the Texas Panhandle and Oklahoma. The company’s meter is accurate, reliable and affordable, as well as easy to tie into supervisory control and data acquisition systems, Richards assesses.
“Schneider has been a fantastic partner,” Richards praises. “When supply chain issues come up, as has often happened during the past two years, they work with us to solve problems and take care of customers.”
Vapor Recovery
With operators of all sizes zeroing in on managing emissions from production operations, vapor recovery units have quickly become a standard component on the lease site, particularly in new pad developments where production from multiple wells is aggregated at central tank batteries, according to John Senor, product manager at SCS Technologies in Big Spring, Tx.
“The greatest demand for VRUs is on multiwell tank batteries in greenfield projects,” he says. “If there are a lot of wells tied into a tank battery, the vapor volumes provide good economics for capturing and compressing the gas, and justify routing gas sales pipeline infrastructure to the area.”
The ability to eliminate fugitive emissions and minimize flaring while capturing an otherwise lost revenue stream makes VRUs a strategic fit for companies looking both for improved financial metrics and ESG performance. SCS VRUs are turnkey systems that integrate digital solutions such as programmable logic controllers and variable speed drives with engineered mechanical components to achieve high run times and compliance with U.S. EPA “Quad-O” emission regulations (40 CFR 60 Subpart 0000a).
Senor says the systems are technology and brand “agnostic” and can use rotary screw (Leroi, Howden, Mycom, Sullair or Gardner Denver), rotary vane (Roflo or Mattei) or reciprocating (Corken, Blackmer or Ariel) compressors matched with a PLC-controlled bypass/recycle valve, oversized scrubbers and filters, and a dual-fan aftercooler to achieve run time targets well above industry averages.
“Our VRUs primarily use screw compressor technology, but rotary vanes and recips definitely have preferred applications based on the gas composition, flow and pressure ratios required,” he explains. “Rotary vanes are good for sour gas, saturated streams and other critical service applications. We recently sold a rotary vane package with 316 stainless steel process piping and coolers along with corrosion inhibitors in the lube oil to run on up to 8% hydrogen sulfide.”
SCS Technologies’ goal for any VRU is to achieve a run time of 98% or greater. “Run time is everything,” Senor emphasizes. “If a VRU is down, the gas has to be flared instead of going to the sales line.”
Typically, VRUs must be periodically shutdown for scheduled maintenance tasks, such as changing the lube oil. But run time is so critical that Senor says operators are devising solutions to maintain the equipment without shutdowns and restarts. “One of our customers prefers to use a lube oil makeup system external to the VRU; our packages come standard with redundant filter manifolds, allowing the VRU to run without having to stop to change lube oil and filters,” he points out.
For new projects, Senor advises that operators install a vapor recovery tower (VRT) to optimize vapor recovery flash gas at a higher pressure than storage tanks. “A facility designed without a VRT will operate at very low pressures making oxygen ingress a major concern,” he relates. “Feeding the VRU off the VRT alleviates oxygen ingress and helps consolidate gas before it enters the sales line.”
Tank battery VRU applications typically try to maintain the highest possible pressure so that oxygen cannot be pulled in through thief hatches or fiberglass piping, he goes on. “If you operate too close to 0 psi, there is greater potential to pull in oxygen. The gas sales meter has a shutdown valve and an O2 meter, so if any oxygen is being pushed into the sales line, the pipeline will reject it.”
Monitoring And Control
Senor describes the VRU as “the most automated piece of equipment on a production site.” As opposed to a wellhead compressor that has a suction range measured in pounds of pressure, a VRU at a tank battery operates within the margin of ounces of pressure, although he says one trend that is quickly gaining traction is tankless battery designs. “Instead of having tank gas pressure held at a few ounces, end-users have production vessels holding several pounds of pressure.
The ability to eliminate fugitive emissions and minimize flaring while capturing an otherwise lost revenue stream makes vapor recovery units a strategic fit for operators looking to improve both financial and ESG performance. SCS Technologies describes its VRUs as turnkey systems that integrate programmable logic controllers and variable speed drives with rotary screw, rotary vane or reciprocating compressors matched with a bypass/recycle valve, oversized scrubbers and filters, and a dual-fan aftercooler to achieve run time targets of 98% or greater.
“For tank applications, the VRU must precisely control the bypass valve’s opening and closing to maintain pressure in the range of a few ounces,” Senor states. “Multiple PID loops run simultaneously, and there must be a smooth handoff between them so it doesn’t create sudden bursts of gas going to the scrubber to send the VFD out of control to pull all the vapors down. You cannot pull a vacuum on a storage tank or it could collapse the tank, so it is mission critical to keep pressure positive. Maintaining that narrow window requires a lot of monitoring and control.”
That is where PLCs and VFDs come into play, helping extend turndown capacity and automate operations for consistent performance. “A VRU with a VFD and recycle/bypass valve has more turndown capability and can run a lot longer than a VRU with just a simple on/off or lead/lag control,” he adds. “It has more flexibility to adapt as conditions change over time.”
One of the challenges for sizing any piece of equipment in tight oil plays is varying production rates, and the possibility that gas percentages and compositions will change as wells mature. To engineer around that challenge, Senor says SCS units are sized using a fieldwide “worst-case scenario” approach to account for all potential conditions that may be encountered in the future.
“We make performance runs using, say, a pure methane for the lube oil section and perhaps a 1.6 specific gravity heavy gas for the gas section of the cooler to design the widest possible operating range into the system for flexibility and to allow field shuffling,” he explains, noting that SCS VRUs are packaged on heavy-duty skids and paired with NEMA 3R control panels.
Emissions-Free Gas Lift
Improving facility design at gas lift sites can be one of the most effective and profitable ways for producers to address fugitive emissions, including methane, VOCs and hazardous air pollutants, suggests B.J. Ellis, president of Liftrock Integrated Lift Services. He says the company has developed a skid-mounted gas lift control system that is proven to eliminate 100% of methane emissions from gas lift operations.
“Conventional gas lift systems dump scrubber liquids into an atmospheric tank where they can flash off as gas and be emitted into the atmosphere. By contrast, this advanced control skid recirculates the liquids within a closed-loop system,” Ellis explains. “When any liquids flash into methane, that gas is repurposed to fuel the engines or is injected down hole through the compressor.”
There are additional benefits associated with the use of this gas lift control skid. “Today, it can be difficult to find experienced crews to properly set up gas lift facilities,” says David Stone, Liftrock’s sales manager. Stone points out that inexperienced crews often make mistakes that lead to downtime or safety risks. “For example, I have often seen dump lines that dump into a vessel that is too far away, or that lack proper insulation, which can cause them to freeze frequently.”
To simplify the field work, the gas lift control system is fabricated in a controlled environment with rigorous quality assurance, Ellis relates. “Once the control skid reaches the well site, all the crew needs to do is join the interconnected piping. While this key feature can shorten construction times 30%-40%, the real benefit is consistency. The crew needs to know far less to set up a prefabricated control system for optimal uptime.”
Ellis says Liftrock drew on decades of compressor experience as it designed the skid. “Among the most common causes of downtime we found was freeze-ups in the dump lines leaving compressor scrubbers and heading to atmospheric tanks,” he notes. “These issues can begin occurring in temperatures around 60 degrees Fahrenheit because the pressure drop from the compressor scrubbers to the flowline, or to the associated atmospheric tank, causes the gas to expand and cool.
“Through the process design of this control system, we regulate the pressure drop such that we eliminate the freeze up potential,” Ellis says. “This design stops liquid-level shutdown events and eliminates the cost associated with injecting methanol, the traditional technique for mitigating freeze-ups.
“When we had the deep freeze in Texas in February 2021, none of the facilities equipped with these skids went down because of a liquid level freeze from compressor scrubbers,” he reports.
The gas lift control skid is equipped with instrumentation that measures the amount of gas it repurposes and sends a monthly report to customers. According to Ellis, the repurposed gas generally covers the skid’s rental cost. “Add in the operational benefits of eliminating liquid-level freeze-up events, and the skid becomes a revenue generator for customers rather than an expense,” he says.
This gas lift control skid from Liftrock Integrated Lift Services has been engineered to reduce emissions, ease equipment setup and improve reliability at gas lift sites. By capturing and reusing any liquids that flash into methane, Liftrock reports, the skid eliminates methane emissions.
Ellis adds that the skid is designed for ultimate reliability. “We are gas-lift compression facility experts who have spent the majority of our careers working in this area. When designing the skid, we spent more than a year addressing every variable we knew that was associated with compressor downtime, developing answers to prevent these issues–whether through the process design, control valve placement, insulation, heat tracing or telemetry,” he says. “In fact, the skid’s telemetry is robust enough that it generally can identify a potential problem and notify our operations personnel and our customers before it leads to downtime.”
Summing up, Ellis says, “This skid-mounted control system is the only methane emissions mitigating solution on the market today that reduces operational burdens and downtime from gas lift facility operations while eliminating methane emissions. Because of this, the installed system generates a positive return for our customers, as it was designed.”
Preventing Paraffin
Magnetic fluid conditioners (MFCs) are a reliable and affordable way to prevent paraffin, scale and emulsions, says John White, the president of Flo-Rite Fluids Inc. “Magnetic fluid conditioning alters the production fluid’s molecular structure mechanically, so the paraffin and scale molecules that normally come together to create solids realign and repel from one another,” he outlines.
The MFCs can be placed down hole in both horizontal and vertical wells, as well as in pipelines, saltwater disposal wells and water treatment systems. “In oil and gas wells, we put the magnets at the bottom of the hole because that is where the problem starts,” White says.
These photos show a paraffin-filled line behind (left) and directly in front of (right) a magnetic fluid conditioner. Flo-Rite Fluids Inc. says magnetic conditioners offers a low-cost way to clean out and prevent paraffin and scale formation at surface and downhole.
According to White, the magnets cost much less than periodically hot oiling and chemically treating a well. “The monthly rental cost for our magnets generally is less than or comparable to the cost of a single hot oil job, and the operator may have to do hot oil jobs quite frequently,” he explains.
The magnets work well enough to extend pump life without paraffin-oriented chemical treatments, White reports. “In the United States, we often go into wells where rod pumps fail every year from fouling or paraffin buildup,” he says. “Each failure can cost $15,000-$20,000 by the time the operator buys a replacement, pulls the old pump and installs the new one. Generally, we are able to add two-five years to the pump’s life.”
To demonstrate magnetic fluid conditioning’s efficacy, White recalls a couple wells in West Texas with production streams containing 38% asphaltene. “Whenever the wells stopped flowing, the downhole equipment got plugged. Chemical treatments proved ineffective, so the operator constantly had to pull the tubing and spend money steaming it out,” he says.
“When we put our magnets down hole, the operator no longer needed to work on the pumps and could sell every bit of oil. The operator had no trouble for two years and ultimately managed to sell the field,” he relates.
The tools have been deployed in 12 U.S. states, such as Wyoming and North Dakota, and several countries, including Canada. White says Flo-Rite is growing rapidly in cold regions where snow often makes getting trucks to site hazardous or impossible.
The magnetic fluid conditioners originally were developed to treat water, notes Brandt Poulin, Flo-Rite vice president of operations. “H2O is highly polar, so it has a strong reaction to magnetism,” he comments. “We have had great success using MFC to clean scale from all wells, including saltwater disposal wells, and to eliminate and prevent future build up.”
The magnets also excel in oil pipelines, White says. “These pipelines move 99.2%-99.5% oil, and we are able to keep paraffin from forming inside them so they can be pigged without the risk that the pig will get stuck,” he relates.
High-Pressure Gas Lift
High-pressure gas lift gives operators a way to produce high volumes without reliability headaches, says Victor Jordan, an artificial lift specialist with Estis Compression. “HPGL involves injecting down the tubing string at the lowest possible point in the well and flowing up the annulus to lighten the entire hydrostatic column of fluid and reduce bottom-hole pressures,” he describes. “This approach combines the benefits of gas lift with the deliverability associated with ESPs.”
To enable single-point gas lift, an artificial lift technique that combines reliability with high fluid volumes, Estis Compression has designed and built booster compressors rated for high pressures. The company mentions that these compressors also excel at unloading wells after frac hits and supporting enhanced oil recovery pilot projects.
Many operators are lifting 8,000-10,000 barrels of liquid a day using HPGL, Jordan says. He says the technique approaches a cradle-to-grave solution, noting that it has worked with volumes as low as 250 barrels of liquid a day. Initially, gas is injected down the tubing to lift the fluid up the annulus because the annulus’ higher cross-section flow area reduces friction. As production declines, injecting down the annulus and producing up the tubing becomes more efficient.
HPGL also is called single-point gas lift. Because the gas enters the annulus or tubing at the bottom of the well, there is no need for gas lift mandrels and valves, Jordan explains. “This makes HPGL a great tool for producing sand-laden wells,” he says. “In fact, we have heard of an operator flowing five-six gallons of sand an hour with HPGL.”
HPGL has exceptional reliability, Jordan assesses. “As long as they are supported by a strong corrosion control program, HPGL wells should never need to be pulled for failures associated with the artificial lift system,” he suggests. “By eliminating valves, HPGL can make corrosion control easier; operators can use oil-based corrosion inhibitors that are extremely effective but would be a poor fit for conventional gas lift because they can plug valves.”
HPGL has a long history off shore, but its recent use in onshore horizontals kicked off in 2017 with a Society of Petroleum Engineers’ paper by David Elmer, Bill Elmer and Larry Harms, Jordan recounts. “EOG Resources approached us and asked if we could build a compressor capable of achieving the necessary injection pressures,” Jordan details. “The first deployment happened in early 2017. From there, HPGL took off. In 2019, we had more than 500 applications and 300 HPGL compressors built.”
Growth halted in 2020 but has recovered, Jordan reports. He credits the technique’s growth to its reliability and simplicity. “HPGL simply injects gas at one point in the well with nothing but tubing in the wellbore to lift high volumes. What is there not to like about that, especially in crooked, tight holes?”
Enabling HPGL
According to Jordan, HPGL has had great success in the Permian Basin, the Mid-Continent and the Bakken. He says typical applications involve injection pressures ranging from 1,200 psi to 5,000 psi, with 5,500 as the ceiling.
“Our HPGL booster compressors are powered by a 145-horsepower engine that has proven itself in thousands of lower-pressure environments,” Jordan describes. “However, the compressor cylinders have a higher pressure rating. We also need to use a more robust oil when pressures exceed 4,500 psi, as well as higher-rated piping.”
In addition to supporting HPGL, the high-pressure compressors can help wells recover from frac hits. “The units are extremely mobile, so we often get them on site much faster than a swabbing unit,” Jordan says. “They also unload the wells quickly. For the simplest jobs, it may only take six hours.”
Jordan adds that the compressors are more affordable than unloading a well with nitrogen or compressed natural gas. “The monthly rental cost for a compressor often is less than the cost of using a nitrogen unit for two days,” he says.
The high-pressure compressors also have been deployed in enhanced oil recovery projects. “We are assisting projects in the Eagle Ford and the Permian, and we are preparing to work on one in the Williston,” Jordan details. “The compressors give the operator a chance to confirm that the EOR project will succeed before it invests in buying larger, more efficient compressors.
“We are taking operators’ efforts to improve ESG seriously,” Jordan assures. “This year, we are introducing electric versions of our HPGL compressor. We also are finding other ways to reduce emissions, such as using instrument air rather than gas to actuate our dump valves, minimizing compressor blowdowns and eliminating crank case gas.”
Modular Facilities
As automation has become more complex and extensive, getting people with the right technical skills to install and program automation systems on site has become more challenging, says Earl Basnett, vice president of business development for Crimson Engineering Inc. In response, Crimson launched Matrix Modular Technology to provide factory-built, fully-automated equipment.
“When we do most of the work in the Dallas-Fort Worth metroplex on predictable schedules that allow employees to watch their kids’ ball games and cheerleading competitions, it’s much easier to attract and retain talent,” Basnett acknowledges. “Because we work in a controlled environment, we also have stronger quality control and more opportunities to improve efficiencies from job to job.
“In the field, it can be challenging to avoid rework or delays because there are so many variables that can affect how quickly and reliably jobs can be performed,” Basnett contrasts. “When dust storms come through a site or the temperature exceeds 115 degrees F for two weeks straight, even the best welder’s work is going to slip.”
According to Basnett, modular construction can reduce time on site by 20%-50% while improving quality and reducing long-term operating costs. He adds that the technique cuts the amount of vehicle traffic to and from the equipment’s ultimate destination, which reduces safety risks and emissions.
“We use modular construction for everything from metering systems and oil well tank batteries to small compressor stations and separator packages for multiwell pads,” Basnett reports. “It can also be applied to larger facilities, such as cryogenic plants.”
Matthew Bargholz, one of Crimson’s automation engineers, emphasizes that modular facilities can be much easier to automate consistently from project to project. “How much we automate will depend on the customer’s needs, but our base package is a turnkey solution that includes everything from transmitters on the skids, vessels and equipment to a cloud SCADA system that can integrate into clients’ back-end production accounting system,” he comments.
The cloud-based SCADA system was designed to monitor facilities ranging from a well pad with a single pumpjack to a gas plant handling 300 million cubic feet of gas a day, Bargholz says. “The data display is extremely visual,” he adds. “For example, when production engineers look at pumpjack data, they will see a picture of a pumpjack with real-time data shown in the appropriate places, including the dynacard and information from the controller.
“When we deploy the SCADA software, we integrate it with the customer’s production accounting system and other tools,” Bargholz continues. “The goal is to push data to those systems automatically rather than requiring the operator to manually import it, which takes time and can lead to mistakes.”
For other great articles about exploration, drilling, completions and production, subscribe to The American Oil & Gas Reporter and bookmark www.aogr.com.