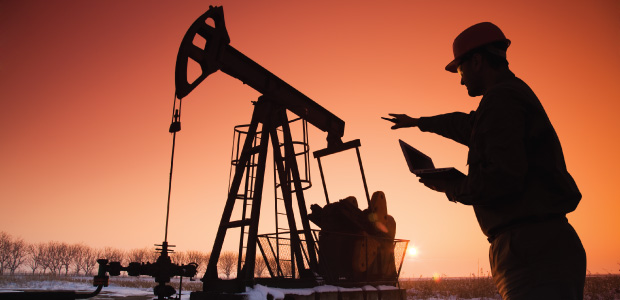
Emerging Technology
Production Technology Still Evolving
By Dan Holder
The oil and natural gas industry has been remarkably successful at finding hydrocarbons, growing total U.S. proved reserves of both oil and gas by 70 percent in recent years, thanks largely to unconventional reservoirs.
However, efficiently extracting hydrocarbons from ultralow-permeability rocks is no small feat. And the challenges are only intensified by the multiphase nature of the production flows, characteristically steep decline curves, low recovery rates, and of course, tight economic margins. Companies are working with each other, bringing in university researchers, and combining new technology and processes to help them overcome those challenges.
Fred Morrow, vice president of engineering for Superod, cites a company’s Southeast New Mexico operation as one vision of what is on the industry’s horizon. The operator is targeting formations with horizontal segments drilled from 10,000-foot vertical wells, managing the field through one control room, with supervisory control and data acquisition architecture monitoring each well.
Morrow says the wells typically have very high initial production rates that may exceed 2,000 barrels a day, but output falls off rapidly. As output declines, the wells move from electric submersible pumps to fiberglass sucker rods from Superod when production falls below 500 barrels a day.
“The key to this is not only the fiberglass, but operators are doing things with variable speed drives downhole card monitoring that is controlled remotely from a central office. As production continues to fall, the pumping unit slows,” Morrow describes. “The operator tries to keep pump fillage between 85 and 95 percent; if it is above 95 percent, the motor speeds up; below 85 percent, it slows. The unit is adjusting itself constantly to maintain the type of fillage that gives maximum production without developing a fluid pound that can cause downhole problems.”
Even though conditions are improving, the industry still is nowhere near where it needs to be economically, assesses Cleon Dunham, president, chief executive officer and secretary for the Artificial Lift Research and Development Council (ALRDC). “Companies are trying to get the most they can out of existing production, and they are focusing on recovering as much from their wells as they can. The investment focus has shifted from drilling to maximizing efforts on existing wells and facilities. There is a big focus on automation, which is a relatively inexpensive way to gain more benefits.”
Many downhole technologies will continue to make oil and gas production possible, and Dunham predicts evolutionary, not revolutionary, improvements over the near term. He points to ESPs as one evolving sector, where technology advances are expanding operational capabilities and reducing application costs.
“One usually thinks of ESPs being used in high-rate wells to produce hundreds of barrels of liquid a day. But they are getting to the point where you can put in an ESP to effectively produce fewer than 100 barrels,” Dunham describes. “We also are seeing smaller-diameter ESPs that work in smaller wellbores. They don’t necessarily have to be 51⁄2- or 7-inch wellbores anymore.”
Developments in the sucker rod field include continuous and fiberglass units, hollow rods that allow operators to introduce chemical treatments directly into the well, and operation techniques to help avoid the effects of excess gas levels, including gas interference, Dunham says. In the gas lift area, he describes industry targeting optimizing operations such as methods to determine the optimal depth to install injection equipment, and the best chemical combinations to deal with oil and condensate mixtures.
Deep Production
Morrow says operators typically put high-IP horizontal Bone Spring wells on gas lift or ESPs until initial rates drop to 400-500 bbl/d, at which point they are moved to rod pumps. “They will be on rod pumping for the next 10 years or better, before they eventually decline to maybe 75 barrels of oil and 75 barrels of water a day,” he says.
As wells decline and switch to secondary recovery, operators must consider physical factors such as depth, temperature and pressure in choosing their artificial lift techniques. Morrow says combining fiberglass sucker rods and beam pumps is a good choice for Bone Spring wells. For deep wells, the weight difference between a one-inch steel rod (2.9 pounds per foot) and a one-inch fiberglass rod (0.8 pounds/foot) is significant.
“In an oil well, the surface pumping unit may be 10,000 or 12,000 feet from the downhole pump,” he describes. “That pumping unit not only is lifting the load at the pump, but also the weight of the rods themselves. In a 10,000-foot well with fiberglass rods, the pumping unit has 10,000-15,000 fewer pounds of rod weight that it doesn’t have to lift every stroke. The big thing is the weight reduction, which allows the operator to use smaller equipment and less power to lift a given amount of fluid.”
Advances in fiberglass sucker rods also mean less concern about corrosion in wells with hydrogen sulfide and carbonic acid, Morrow notes. Fiberglass rods installed 30 years ago still are working, he says, estimating that as many as half of all rod failures are caused by corrosion.
Superod is working to expand the temperature range for its products, Morrow says, pointing out that current fiberglass sucker roads can work in up to 200-degree downhole environments, while many fields, including those in South Texas and the Bakken Shale, can see temperatures top 275 degrees. While some resins used in the fiberglass can handle 275-degree environments, Morrow says the high temperatures compromise their strength, lowering rod loads and thus oil production.
SCADA advancements also promise to change operational costs for operators, Morrow says. Typically, lease operators have to drive to every well on a regular basis to monitor conditions and check for problems. With remote instrumentation, the well equipment sends its data to a central location, and field workers can be dispatched on a well-by-well basis to handle incidents.
“It is a much more efficient way to operate producing wells. Instead of having workers drive around acquiring data manually and looking for problems, the automated system monitors and reports production data, and notifies the operator if there is a potential problem,” Morrow concludes.
Academic Involvement
ALRDC’s Dunham points to the Tulsa University Horizontal Well Artificial Lift Project as one example of academia involvement in production technology research. The ALRDC-sponsored program brings more than 15 companies and university researchers into a consortium that seeks to improve artificial lift equipment and practices for horizontal wells in shale plays.
“The consortium has been going for four years now,” he describes. “The university has facilities where it simulates production in horizontal wells, and uses that to test the effectiveness of ESPs, sucker rod pumping, gas lift, chemical injection, and other technologies.”
As operators continue drilling longer laterals, production technology is evolving to make those segments more productive, he offers, with sucker rod pumping one of the more popular options. He notes that sucker rods can be installed in deviated horizontal sections of a well.
“A big choice now is chemical lift, injecting chemicals that lighten the crude enough to allow it to be produced,” Dunham describes. “You can inject chemicals really anywhere in a well, as long as you get the chemical down there. Operators are using capillary tubes and similar equipment to inject chemicals, sometimes even out to the toe of the well, but certainly down in the deviated and horizontal parts, to help reduce fluid density.”
Most lifting is done in the well’s vertical or deviated segments, he says. Operating wells with long horizontal legs requires moving production to those sections where lifting is effective. “Whether it is a long horizontal is not so much the issue,” Dunham poses. “It is a matter of how you get the fluid to flow.”
Operators continue to seek new and better ways to employ varying types of artificial lift, and ALRDC’s workshops offer an excellent forum for new ideas, Dunham says. “We always get good ideas out of those workshops. There is a lot of focus these days on using various kinds of drive systems for ESPs. The idea is to keep people aware of what is happening in the industry, and aware of new technologies and new training approaches,” he offers.
Properly training workers continues to be a concern for well owners, Dunham says, noting that capital spent to install new technology will be ineffective investments if the personnel on site cannot operate it correctly.
“There now is a focus on training and developing people, providing the tools that operators can use to better understand their wells and artificial lift equipment, and programs for detecting and solving problems,” Dunham says. “These technologies have been around for a long time, but I see them continuing to evolve.”
A fully integrated hydraulic fracturing pump system from EPIX, a joint venture between Weir Oil & Gas and Rolls-Royce Power Systems subsidiary MTU, helps operators run longer laterals in horizontal wells. According to the company, the system consists of a SPM® QEM 3000 hydraulic fracturing pump, ZF 8 TX transmission system from ZF Friedrichshafen Group, and an MTU Series 4000 engine.
Integrated Fracturing Unit
As operators design longer laterals in their horizontal wells–with requirements for higher pressures and flow rates, and continuously operating service equipment–their mechanical equipment has to be capable of meeting those challenges. One possible solution is a fully integrated hydraulic fracturing pump system from EPIX, a joint venture between Weir Oil & Gas and Rolls-Royce Power Systems subsidiary MTU. The EPIX power system consists of a SPM® QEM 3000 hydraulic fracturing pump, ZF 8 TX transmission system from ZF Friedrichshafen Group, and an MTU Series 4000 engine.
According to EPIX, the Series 4000 offers a power output from 2,250 to 2,600 horsepower with more low-end torque and improved acceleration, while the ZF transmission system has a maximum input torque of 7,744 foot-pounds.
The unit is the first product from EPIX, announced in May. Douglas Schwedland, EPIX’s chief executive officer, says the company is in the process of incorporating and plans to begin commercial operations early this year.
“EPIX ultimately will be able to optimize how the components work with each other,” Schwedland describes. “When the transmission senses certain inputs from the pump or engine, it is able to make decisions on the fly. Since we have access to the development of all three components, we are able to write codes that do that logic and system management.”
The MTU engine meets U.S. Environmental Protection Agency Tier 4 final emissions standards without additional control technologies, he points out, which is a substantial savings in terms of costs, weight, and overall complexity of the exhaust design.
In addition to an integrated warranty for the entire unit, the FracPack system will lower service costs for users, Schwedland says. With a 3,000-hp pump and 2,600-hp engine, operators will need fewer pumps on job sites to satisfy their fracturing requirements. One service location will handle all three components, and maintenance schedule concerns are minimized.
“One of the key selling features customers have picked up on is that EPIX is aligning the maintenance schedules of all three components,” Schwedland says. “Coordinating the pump, engine and transmission maintenance schedules and service intervals is a huge savings for customers. It reduces the number of times they have to bring the system in for maintenance.”
Weir Oil & Gas global service centers will handle the maintenance and service work, he adds.
Schwedland says the MTU FracPack is but the first step in EPIX’s integrated drive line, with the stage integrating the monitoring and controls of the three components. Without revealing too much of the playbook, he reports that EPIX is looking for on-the-trailer monitoring and control systems that actually make decisions based on the input of the three components. “That is what you want to get to: a very logical and smart system that is able to help you run your business,” he says.
Liquid Assistance
When an operator kicks off production from a well, the well typically is full of heavy completion or formation fluids. Often the solution employed is to inject gas down hole to lighten the fluid column, decrease bottom-hole pressure, and unload the well using gas lift.
Craft & Hawkins Department of Petroleum Engineering at Louisiana State University is evaluating a system that uses a gas/liquid mixture to increase the density of the injected fluid above that of the single-phase gas to allow lower injection pressures for the same bottom-hole pressure requirements.
Paulo Waltrich, assistant professor in the Craft & Hawkins Department of Petroleum Engineering at Louisiana State University, says Royal Dutch Shell funded work with LSU researchers to advance developing liquid-assisted gas-lift (LAGL) technology. The LAGL concept uses a gas/liquid mixture to increase the density of the injected fluid above that of the single-phase gas to allow lower injection pressures for the same bottom-hole pressure requirements, Waltrich says.
He points out the lower injection kickoff pressure minimizes compression costs associated with gas-lift systems and increases gas-lift technology reliability by decreasing the number of unloading valves, and thus potential leak points.
“The standard in the industry is to inject pure, single-phase gas to do this unloading. What Shell was proposing and started investigating at LSU is injecting a mixture of liquid–say, water or oil–with natural gas. That decreases the power required for the compressors injecting the gas and liquids into the well,” he outlines.
A major advantage of LAGL is that it can be deployed in operating gas-lift systems without significant modification or costs, he adds. The major modification is adding a liquid injection system that connects to the single-phase gas lines. “The system probably will add some intangible costs, but nothing significant,” Waltrich says. “When you are decreasing the injection pressure that much, the footprint and the horsepower of the compressors required will be reduced significantly.”
When the system was tested at LSU’s test well, the compression required was reduced 75 percent in the best case, he says, pointing out that by adding liquids to the injected gas, a well injecting at 1,300 psi would need a compressor capable of 400 psi.
“One of the big advantages of gas lift is if you have highly deviated wells, a gas lift is pretty much just injecting fluids. So, it really does not matter if a well is horizontal or vertical. This applies to both,” he says. “Also, there are no restrictions with horizontal wells that are very long.”
LSU researchers also are focusing on how bottom-hole valves that have been subjected to injected gas only may be impacted by handling a liquids/gas mixture for long periods, Waltrich says. “When you are doing the standard gas lift practice, you have some sort of liquid in the well anyway, so this valve already handles liquid and gas. We have not seen erosion problems by adding liquid to the valve,” he reports.
The university is looking for operators interested in conducting field trials of the technique, Waltrich says.
Stuart Scott, who is working with Waltrich, points out that getting university staff involved in industry research brings in talented personnel who often have new ideas or approaches to problems. Stuart, director of technology for PetroleumETC in Houston, adds, “University research, while it may be on a slower pace than some of the alternatives such as professional laboratories, costs much less.”
Those transactions have consequences beyond the immediate research, Stuart says, with students gaining knowledge useful when they join the oil and gas industry.
Cooperation between companies and universities depends more on industry need rather than general research, Stuart says.
“U.S. industry has been struggling with this for decades,” he assesses. “European governments provide tax incentives for research. Norway is a good example. The same thing is happening in Brazil, where 1 percent of gross production has to be spent on research. Universities in the United States don’t compete on an equal playing field, but truly on capability, talent and prices.”
Field Productivity
To help improve operational productivity and reduce requirements for field personnel to regularly visit production sites, Clariant has released its VERITRAXTM intelligent chemical management system to automate well monitoring and dosing, the company says. It combines field-level sensors, cell phone technology, and cloud-based data collection, using sensors powered by batteries that can go three to five years with minimal intervention by field technicians.
Clariant’s VERITRAX™ intelligent chemical management system improves operational productivity and reduces requirements for field personnel to visit production sites. The company says it combines field-level sensors, cell phone technology, and cloud-based data collection.
According to Clariant, the VERITRAX system optimizes chemical management tasks and reduces labor costs by using automation and cloud-based technologies to optimize the chemical supply chain and give producers better control over their chemical spending.
Clariant’s chemical tank level sensors maintain a constant watch on dosing tank levels, and the system sends alarms when a tank nears preset levels. A field technician monitors all the wells in his charge using the Clariant Chemical Dashboard, which allows him to focus his in-field activity only on wells that need attention.
VERITRAX can be fully integrated into production setups such as SCADA and distributed control systems, providing continuous real-time data flow directly to laptops and smart phones, Clariant says. The system allows customers to monitor a number of data streams, including well production figures or chemical injection rates, while also supporting inventory management. The company points out that the unit automatically coordinates chemical deliveries.
The system’s data analysis and chemical pump control allow operators to provide optimized dosages for individual wells, and its online surveillance capabilities provide fieldwide production data rate streams using analytical results uploaded from the field or laboratory, the company describes.
“The priorities for oil and gas companies are risk management, production efficiency, and cost optimization,” reflects Jon Rogers, global head of Clariant Oil Services. “Information technology is playing an increasingly important role for oil and gas companies as they look for ways to optimize all aspects of their operations. VERITRAX technology can deliver both cost reduction and increases in operational efficiency.”
Smaller ESPs
A new, small-diameter electric submersible pump system from Baker Hughes Inc. holds the potential to revive older wells through lower lifting costs, while allowing operators more options in placing ESPs in smaller-diameter wellbores, says Nathan Holland, the company’s product line director for artificial lift.
The CENtrilift PASSTM 300 series slim-line ESP system extends the benefits of Baker Hughes’ 400 series, which employs a 4.5-inch motor and 4.0-inch pump. The 400 system has an operational range from 50 to 6,000 barrels a day, Holland describes.
“Baker Hughes has moved that technology into the 300 series,” he reports. “The system has a pump with a flow range from 50 to 3,000 bbl/d; a boost pump that condenses the gas to a liquid; and a gas mitigation intake, which basically is an advanced intake system/gas separator, combined into a single technology, the niXit™. The unit also has an improved electrical connection to the motor, and an enhanced profile that is more accommodating in tight casing applications.”
The niXit technology combines gas mitigation intakes with a gas separation device, and allows the unit to operate in a well’s vertical, inclined or horizontal segments, Holland says. The system orients the intake ports to open or close, based on the location of the equipment string. He says all ports are open if the unit is in the vertical section, opened or closed if the unit is at an angle, and all top ports are closed in a lateral leg to allow liquid production from the bottom side of the casing and gas to pass on the top side.
The CENtrilift PASS™ ESP system from Baker Hughes includes a new high-performance FLEXPumpER™ series electric submersible pump with a flow range from 50 to 3,000 barrels a day. It provides operators with the flexibility required in dynamic well conditions to minimize ESP system change-outs and nonproductive time while reducing operating expenses. The pump is designed for maximum production and ultimate reserve recovery from conventional and low-flow mature oil fields, and unconventional resource plays with changing production rates.
“If we have an intake that can orient based on the setting of the equipment, it gives us the ability to produce the liquid and naturally separate the gas,” he says.
Production engineers working on wells with high gas-to-liquid ratios typically want the largest casing size available for maximum flexibility in selecting downhole gas separation equipment, Holland observes. They also want pumping units with good gas-handling capabilities that provide a range of depths at which they can be set to provide the best intake pressure and maximum production, while providing for flexibility to accommodate well changes.
“Historically, ESPs have been a ‘period-in-time’ solution in a well’s life cycle. We are doing everything we can to ensure ESP can be applied throughout the entire well life cycle by extending the production range and being able to set ESPs deeper while also handling the gas,” he says.
The CENtrilift PASS system helps operators by reducing the number of equipment change-outs as well production varies, Holland says. Instead of switching ESPs as output declines, the Baker Hughes unit’s flow range provides hands-off operations as production drops, and its smaller size allows more placement options as operators pursue optimal setting depths for maximum hydrocarbon inflows.
Like the 400 series units, Holland says the 300 ESP system provides natural separation of gas slugs and production liquids through the CENesis PHASETM multiphase encapsulated production system, which encases the entire ESP system. The design also protects the motor lead extension during installation in deviated or horizontal wellbores, and reduces motor overheating by diverting fluid past the ESP motor, Holland says.
“Encapsulate the ESP system inside a shrouded unit, and you have a really interesting flow path for the liquid and gas to take,” he says. “The PHASE system is a very unique gas separation tool. The PHASE system’s limitation was the well casing size. By creating the PASS system technology, a new PHASE system was developed for slim casing design. Now, there are two great technologies that, when combined, literally can handle any gas-to-liquid ratio or any slugging combination that an asset can give.”
Rigless Interventions
The industry is only in the beginning stages of seeing what small-diameter ESP equipment can do, Holland goes on. Baker Hughes has unveiled its TransCoilTM rigless-deployed ESP system, which he describes as a unit that delivers the production and reserve recovery enhancements of a traditional ESP while eliminating the need for a rig during installation.
“That means you don’t have to kill the well, saving time and money while drastically reducing risk. And using a coiled tubing-deployed ESP lets the operator leave the production tubing in the well during installation,” Holland says. “But eliminating the rig is half the battle. By connecting an inverted ESP system directly to powered CT, the TransCoil system eliminates the conventional ESP power cable-to-motor connection and an in-well wet electric connection, removing the weakest link in ESP systems.”
The TransCoil system uses a CT setup at a well location to deploy its ESP unit through tubing or in a cased well environment, he says. It can be set in a range of completion systems, but Holland points out, “If an event comes around where that well needs to be worked over, whether the operator wants to change out the equipment and move it somewhere else or whatever the situation may be, no rig will be needed. The CT setup gets over the well, pulls the string out, and deploys another unit, getting wells on production faster.”
The system, which is effective to 12,000 feet, is being used in pilot projects in the Middle East and the Asia/Pacific region, he says.
“We are looking at wells that are really deep, and some with very high temperatures. This technology changes the spaces that we can play in,” Holland concludes.
Nanofluidity
Nanofluidity is the quality or state of being fluid at the atomic, molecular and supramolecular scales. Revelant Nanofluidity Technology stabilizes nanofluidity downhole using nanophysics to drive better oil chemistry during production and transport.
Paraffin, asphaltene, scale and heavy oil case history graphs show stabilization and increased production at the end of standard workovers after installing the Enercat™ downhole tool from Revelant Nanofluidity Technology.
Monte Swan, Revelant’s chief scientist, says the company’s EnercatTM tool manipulates fluid chemistry, stabilizing viscosity and minimizing or preventing paraffin crystallization, asphaltene flocculation and scale precipitation. Using the tool can “reduce and even replace traditional mechanical, chemical and thermal mitigation methods,” Swan says. “This tried and proven innovation stabilizes and increases production, and reduces operating expenses while minimizing environmental and regulation costs.”
Brian Herman is the inventor and developer of Enercat for the oil and gas industry. Swan says Herman first installed the tool in a Northwest Canadian well experiencing paraffin pour-point problems. The tool’s implementation produced significant paraffin, asphaltene, and heavy oil reduction, resulting in overall production benefits. After the tool’s initial success, Swan says Herman began global sales, “with more than 4,000 units installed in 23 countries.”
Revelant was formed to bring the tool to U.S. oil customers and to expand the technology for industrial applications in water, energy, agriculture and health. Domestic oil industry sales began in June 2016 after its technology became patent pending, Swan says.
The Enercat tool is a material composite that is not magnetic or radioactive, and requires no external power source other than the ambient heat and pressure from the oil reservoir, according to Swan. It has no internal restrictions, and needs no maintenance or servicing.
The installed tool is placed below the paraffin and/or asphaltene deposition and below the depth at which oil viscosity begins to increase up the wellbore, typically below the pump intake or above the pump discharge, or as a tail joint at the end of the tubing string, Swan says. For scale problems only, depth is not an issue. The tool also can be installed in series to handle high oil production rates. Swan notes that the tools work in virtually any well that experiences deposition, including dual completions, and directional, horizontal, steam-assisted gravity drainage, water source and water injection wells.
According to Swan, the Enercat comes in two versions. The TubingTool is designed for downhole installation in the production tubing string. It is installed during a completion operation or workover as an industry-standard 1.2-meter (four-foot) pup joint that meets required installation specifications. Handling capacities vary by tubing size: 2⅜ inches at 30 barrels a day, 2⅞ inches at 35 bbl/d and 31⁄2 inches at 70 bbl/d. The TrimTool version is installed without pulling the tubing string by attaching the tool to the bottom of the pumping assembly on a producing well. This allows installation during well servicing, independent of workovers, making it ideal for low-producing wells, he says. The 12-inch version handles as much as 10 bbl/d, and the 28-inch version handles 15-20 bbl/d.
Revelant is partnering with both the research and application ends of the spectrum to refine the technology for maximum benefit, Swan says. The company is working with the faculty at Colorado State University under the direction of professor Amber Krummel, Revelant’s technology officer. Her research team is working out the details of the physics and chemistry underpinning the Enercat. A refined ability to measure, tune and focus the technology will allow Revelant to address specific problems with fluid stability in the oil and gas industry by expanding the tool’s application to target specific molecules, such as barium sulfate, and to solve even larger problems associated with water.
In terms of the tool’s application, Revelant has partnered with 4B Production Enhancement, according to Swan. Their downhole tool, the Stinger, is a tubing-conveyed tool designed to clean the inside of the casing and perforations of oil, gas, disposal or injection wells. “The Stinger cleans it and the Enercat keeps it clean, resulting in less production downtime and smoother operations,” Swan says.
Reliable long-term benefits are the end result of Enercat implementation. “In more than 80 percent of the installations, the tool’s performance has been successful. Some tools have been in wells for more than 10 years and still are working,” Swan points out.
For other great articles about exploration, drilling, completions and production, subscribe to The American Oil & Gas Reporter and bookmark www.aogr.com.