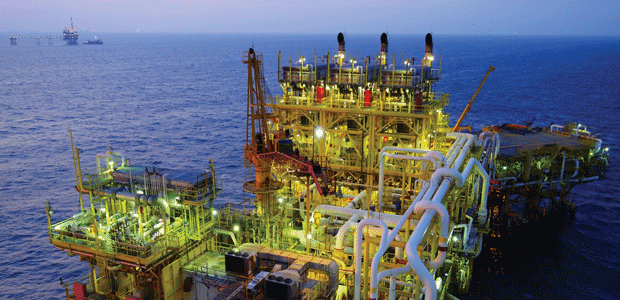
Offshore & Subsea Technology
Subsea Storage And Injection Of Production Chemicals Lowers Costs, Enhances Safety
By Tom A. Gay, Art J. Schroeder Jr. and James E. Chitwood
HOUSTON–Volatility in global oil prices is a constant and harsh reminder to oil and gas companies that they operate in a commodity market and must continually examine new methodologies and technologies to safely manage costs. During the past two decades, companies have spent hundreds of billions of dollars developing and implementing innovative deepwater projects, so it is not surprising that enterprising organizations are looking to mine deepwater solutions for technologies that can be repurposed for Gulf of Mexico Shelf and shallow-water developments.
One such example utilizing deepwater technologies in shallow water is moving facilities and storage from topside decks to the seafloor. Unmanned or not normally manned (NNM) platforms, including unmanned wellhead platforms (UWHP), have been a longtime feature of cost-effective oil and gas developments in shallow-water fields in the Gulf of Mexico and other offshore regions.
The Norwegian Petroleum Directorate commissioned a report on UWHPs in 2016 that concluded “unmanned wellhead platforms can be cost- and production-effective development concepts in the shallower portions of the Norwegian Continental Shelf and that the regulatory framework is open to the concept.” This same report estimated more than 1,000 unmanned platforms had been installed in the U.S. Gulf and fewer than 600 were installed throughout the rest of the world.
With this backdrop of renewed interest in unmanned platforms, the application of innovative subsea technologies to move facilities from the deck to seafloor–and in the process, enabling the demanning of offshore surface facilities–is attractive from an operational management perspective, and also offers significant potential cost savings.
Subsea Transfer Barge
Figure 1 illustrates a subsea transfer barge with usable storage for 3,000 barrels of production chemicals in three large storage tanks built into the barge’s hull. Smaller (~200 barrel) storage tanks for production chemicals utilized in low-dose injection can be included on the barge’s deck. The barge also includes the complete subsea chemical injection unit (SCIU) to inject all the typical production chemicals. The barge’s net payload of facilities and production chemicals totals more than 600 tons, enabling significant deck space and load savings, as well as platform demanning.
The need for subsea chemical storage and injection initially was identified as part of joint industry research in the DeepStar™ consortium group. The technology development requirements were driven by the need for longer and more cost-effective deepwater subsea tiebacks. The subsea transfer barge illustrated in Figure 1 was developed as part of a Research Partnership to Secure Energy for America project supported by both industry and the U.S. Department of Energy.
The current design includes:
- Conventional chemical barge technology, where applicable;
- Double-hull design to protect the environment from potential accidental chemical spills caused by vessel collisions or barge grounding;
- A total of 3,000 barrels of usable chemical storage in three or more separate volumes;
- Dual-barrier containment for the production chemicals;
- Innovative use of engineered fabric as the primary containment;
- The ability to fill the chemical tanks at quayside with optional in situ subsea refill capabilities; and
- Innovative and cost-effective installation and retrieval using two anchor handling tugs.
During the RPSEA project, the subsea transfer barge was subjected to a number of reviews, including industry subject matter experts from operators, service companies and the U.S. Bureau of Safety & Environmental Enforcement. The American Bureau of Shipping performed a review and issued an approval in principle, and a Gulf Coast shipbuilder performed a constructability analysis and issued a fixed-price proposal. The barge deployment/recovery process was modeled extensively with computational fluid dynamics. The modeling results and further dynamic simulations demonstrated very stable and predictable behavior for a two-line installation technique using two anchor handling tugs. The RPSEA project included a complete SCIU on the barge deck.
Following the original design in the RPSEA project, the subsea transfer barge’s in-water behavior has been demonstrated and validated further in a cooperative effort between Woodside Energy Ltd., the University of Western Australia and Safe Marine Transfer (SMT). The work with UWA included both a near-shore demonstration that used a scale model and dynamic simulation studies. This work highlighted the potential to use the barge for cost-effective installation of subsea facilities without requiring large offshore crane vessels.
Moreover, the technology has been advanced by developing adjustable buoyancy in a cooperative effort between Trelleborg Offshore and SMT. The barge’s adjustable buoyancy offers several advantages over fixed buoyancy, including:
- Reusing the buoyancy for multiple installations;
- The ability to adjust buoyancy to use the same barge design for a wide range of payloads;
- Buoyancy adjustment as a contingency for buoyancy damage or deterioration with time;
- Buoyancy adjustment to recover subsea facilities where the weight on the seabed may have changed because of operations, maintenance, marine growth or damage; and
- The reduction or elimination of the need to maintain ballast tanks while the barge is on the seabed.
Small Subsea System
The smaller 200-barrel chemical storage and injection system was developed in response to industry needs for lower-cost subsea tiebacks, including single well tiebacks. As shown in Figure 2, the system includes much of the technology developed for the barge, but the smaller size and weight simplifies offshore installation. The 200-barrel unit is designed with the footprint of a standard 40-foot shipping container. Without a chemical load, the unit is transportable by road, which considerably simplifies logistics.
It can be installed with a conventional offshore multiservice vessel (MSV). The in-air weight of the 200-barrel unit is approximately 55 tons. While the deck weight/space savings are much lower than the 3,000-barrel barge, placing the unit on the seafloor immediately adjacent to a shallow water platform reduces manning requirements since the unit can be operated remotely.
As an additional improvement to the subsea injection system, the 200-barrel system is designed to be all-electric, with the advantages of avoiding a separate hydraulic system and the opportunity to use advanced “health monitoring” to determine pump and valve conditions.
The current design for production chemical storage and injection includes:
- Usable storage capacity of 200 barrels with dual-barrier containment of one chemical (or mixture);
- Suitability for installation/recovery by a standard MSV;
- The capability to operate for as long as five years subsea, with a design life of 10 years;
- 10,000/15,000 psi injection pressure and 10,000-foot water depth ratings;
- All-electric controls and pumps;
- A design that allows for suction pile or mud mat foundations;
- A cost-effective “design one, build many” philosophy; and
- Connection to a subsea injection point or unmanned platform though conventional flying leads using a remotely operated vehicle.
As noted, both the 3,000-barrel barge and the 200-barrel systems store the chemical inside a dual-barrier containment system. This patented system utilizes an engineered fabric as the first or primary barrier and a steel hold or steel tank as a secondary barrier in the event of any failure of the primary barrier.
For the 200-barrel system, the design philosophy includes performing any inspection, maintenance or repair work at quayside. The five-year subsea service life lowers initial costs when compared with a traditional 20- or 25-year subsea service life. With the “repair at quayside” philosophy, the 200-barrel units can be upgraded easily if early experience yields significant design improvements, or if changes are needed in the chemical treatment program.
Technology Step-Outs
The 200-barrel system incorporates technology step-outs in three key areas: engineered fabric as a primary containment for production chemicals, a high-pressure subsea chemical injection pump, and electric valve actuators and pump drivers.
All three areas have been the focus of targeted technology qualification efforts. The storage bladder configuration was selected in conceptual design work that evaluated many options. The selected configuration for the storage bladder then was subjected to scale-model testing, as illustrated in Figure 3.
The compatibility between the stored chemical and the bladder fabric creates an important design issue. The chemical storage bladders are fabricated from chemically resistant engineered fabric materials. To confirm this compatibility, independent third-party laboratory confirmation/testing has been performed for several typical production chemicals. A qualification procedure, needed for different site-specific chemicals that have not yet been tested, also has been developed with input from numerous industry subject matter experts.
Future plans for the 200-barrel system include completing all pump and actuator qualification testing, fabricating a complete unit, conducting in-water system integration testing, and offshore field demonstration. The pump and actuator tests are well advanced and on course for completion in a few months (Figure 4).
Plans call for system integration testing to be performed in an onshore, in-water test tank near Houston. Integration testing is anticipated to be complete by late 2019, with the offshore field demonstration to follow.
It is important to note that the qualification testing of the 200-barrel unit will qualify all the technology needed for larger units, including the 3,000-barrel barge, except for final qualification of the two-line installation and the associated marine installation systems and procedures.
The aforementioned approach of designing one and building many creates an opportunity to offer chemical delivery as a service, with all hardware fabrication, qualification, installation, inspection, maintenance, repair and chemical resupply/refill provided as a service to the operator. This “chemical delivery as a service” approach (which is common on shore, but atypical in offshore operations) can offer operators both cost and quality advantages. Chemical delivery as a service can reduce capital expenditures and make marginal fields more attractive for development.
Although chemical delivery as a service is the long-term goal and advantage of this technology, it is plausible that first subsea units delivered may require a traditional sale of the unit to the operator, who will be responsible for installation and related offshore operations such as chemical replacement/refill.
Cost-Saving Opportunity
Three case studies–one in the Caribbean, one in the North Sea and one in the Barret Sea–show significant cost-saving opportunity for developments in the Gulf of Mexico and other regions where unmanned platforms are being evaluated or are already in use. Figure 5 illustrates an application of the slightly modified 200-barrel system for use with an unmanned platform, such as a small UWHP.
This application offers a number of significant advantages, including reduced topside weight and area for the unmanned platform, reduced operating personnel exposure (no handling of chemicals on the unmanned platform or on a host platform), and the opportunity to obtain production chemical injection as a service with the chemicals and storage.
Because the unmanned platforms are usually very small, with minimal facilities, the weight and area savings from placing chemical storage and injection on the seabed adjacent to the platform can be very significant. The savings on installed platform cost depends on many factors, but in some cases, it can be 30 percent or greater.
For some unmanned platform installations, an umbilical will be used for power, control and chemical injection from a larger manned host facility. The much smaller power and control umbilical required for the subsea unit lowers umbilical manufacturing and installation costs significantly, trimming overall installed umbilical costs as much as 80 percent. The 2016 Norwegian Petroleum Directorate report estimates an installed cost of $800,000 a mile for a conventional umbilical connected to a wellhead platform, so the savings for a long umbilical can be substantial.
Subsea chemical storage and injection also offers the opportunity to extend step-out distances for unmanned platform developments that are too distant from a host to inject chemicals through a conventional umbilical.
Although most existing applications of unmanned platforms are relatively small, shallow-water platforms, future applications of unmanned platforms may be larger and in deep water and harsh environments (including Arctic waters).
The startup last fall of the Equinor-operated, unmanned wellhead platform, Oseberg H, is an example of an unmanned platform in a harsh environment. The first unmanned platform on the Norwegian Continental Shelf, Equinor notes that Oseberg H is “probably the simplest platform on the Norwegian Continental Shelf.” Its topside weighs only 1,100 tons, and the platform does not have processing equipment, living quarters, a drilling plant or helideck. For future harsh environment applications of unmanned platforms, subsea chemical storage and injection will offer significant cost reduction advantages.
Although Figure 5 shows a bottom-founded platform, the concept can be equally applicable to a floating system or a deepwater unmanned platform, such as a small tension leg platform, spar or semisubmersible system.
Personnel Safety Advantages
With subsea storage and injection, platform production operations personnel do not handle the production chemicals. The refill (along with chemical storage and protection) of the 200-barrel unit is done by personnel trained in chemical handling either quayside or with special supply boats/equipment. Avoiding personnel exposure to chemicals such as xylene or toluene provides operators with a significant health, safety and environment advantage. In harsh environments, subsea chemical storage and injection can minimize the frequency of refills in harsh conditions with associated personnel exposure.
Figure 6 illustrates the installation of the 200-barrel subsea storage and injection system with an unmanned platform. The philosophy of designing one and building many is equally applicable to unmanned platform applications. For larger deepwater and harsh environments, or longer-distance tiebacks using an unmanned platform, the larger storage and flexibility offered by the subsea transfer barge may be appropriate.
The subsea chemical storage and injection technology promises significant cost savings for both new green-field developments and for upgrading mature brownfield assets of unmanned or not-normally manned platforms. In the brownfield case, avoiding the space and weight for chemical injection on a small platform may allow an existing unmanned platform to continue in operation with additional production or extended life-of-field production.
Subsea chemical storage and injection enables long distance subsea step-outs, significantly reduces costs on shorter tiebacks, offers versatility and cost savings, and may enable platform demanning in shallow-water applications.
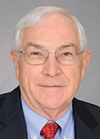
TOM A. GAY is a senior adviser with Safe Marine Transfer LLC. He has 40 years of industry experience, including 31 years with ExxonMobil in upstream roles in research, project engineering, commercial and facility integrity. Gay served as BG Group’s technical authority for floating production systems and represented BG in several DeepStar projects. His experience includes assignments in the United States, Norway, the United Kingdom and France. Gay holds a B.S. in mechanical engineering from Oklahoma State University and an M.S. and Ph.D. in mechanical engineering from the University of Texas at Austin.
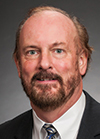
ART J. SCHROEDER JR. co-founded Safe Marine Transfer LLC in 2013 and previously worked in upstream operations, engineering and construction for major operators. Schroeder also has served on numerous professional, corporate and civic boards, and is the recipient of numerous awards, including the Offshore Technology Conference’s Special Citation and SPE’s Management and Information Award. He holds several patents and a B.S and an M.S. in chemical engineering from the Georgia Institute of Technology, and an M.B.A. in finance and international business from the University of Houston.
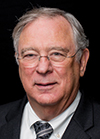
JAMES E. CHITWOOD co-founded Safe Marine Transfer in 2013. He has 48 years of industry experience in offshore engineering and research and development, working both domestically and internationally. His principal project from 1991 to 2014 was the Chevron-led DeepStar Project, where he managed joint industry R&D undertakings. Chitwood has worked for various engineering, manufacturing and production companies both as an employee and as a consultant throughout his career. He holds 14 patents and has an M.S. in mechanical engineering from Texas A&M University.
For other great articles about exploration, drilling, completions and production, subscribe to The American Oil & Gas Reporter and bookmark www.aogr.com.