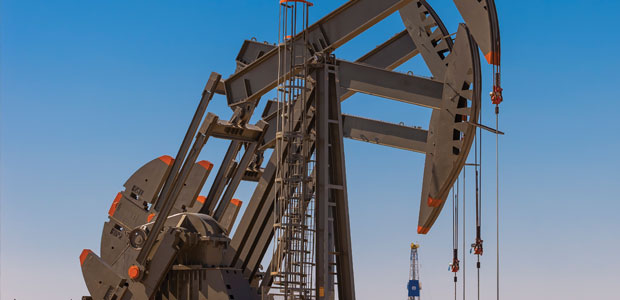
Adding Multiphase Pumps To Gathering Systems Optimizes Artificial Lift
By Sven Olson
ALLENDALE, N.J.–Since its introduction in the oil and gas industry, multiphase pumping has taken giant leaps. With the unique ability to boost both gas and liquids in a single process with a single piece of equipment, multiphase pumping has received recognition in supporting oil and gas production from assets where it was previously impossible.
Subsea boosting in deep- and ultradeepwater fields is a major future driver of multiphase pumping, but the technology also has come of age on shore as a production tool. Both helicoaxial and twin screw pump designs have been installed in a number of onshore production and enhanced recovery projects, and in horizontal resource plays in particular, oil and gas companies increasingly are looking to supplement existing artificial lift systems with multiphase pumps tied to multiwell gathering systems serving one or more pads.
To date, more than 500 pumps have been installed in onshore shale and tight plays, steam-assisted heavy oil production operations, and offshore fields all over the world. This includes limited-size pumps with a few hundred horsepower and large units with more than 1,000 horsepower, with some installed in a parallel operation to boost an entire field. Multiphase pumping has demonstrated great benefits to the operator as a powerful tool for boosting low-pressure reservoirs, minimizing topside facilities, complying with health, safety and environmental considerations, and last but not least, significantly extending and accelerating oil and gas recovery.
Multiphase pumping allows the entire production stream to be gathered and boosted to a central processing facility without requiring separate flowlines, separators, heater treaters, intermediate storage tanks, gas flares, compressors, dedicated oil/gas/water pumping facilities, etc. Eliminating this surface equipment at the well site means substantially reduced facilities and a streamlined production flow that moves the untreated well stream through a multiphase pipeline farther downstream before separation and processing.
Boosting with multiphase pumps is an efficient tool for continuous plateau production and aiding enhanced oil recovery. As illustrated in Figure 1, plateau production is significantly extended and yet the ultimate recovery comes earlier in the life of the well. The liquid production essentially is determined by the capacity of the sucker rod beam pump or electric submersible pump. When a surface-installed multiphase pump lowers the annulus gas pressure, it is possible to make the downhole pumps work under the best possible inlet conditions, thereby improving performance and optimizing a well’s production and ultimate recovery.
Enhancing Artificial Lift
As part of the family of positive displacement pumps, twin-screw multiphase pumps (Figure 2) are especially well suited to enhancing the operation and performance of conventional artificial lift systems, including ESPs, beam pumps and gas lift.
A simple way to illustrate the workings of a screw pump is to compare it with an imaginary piston pump with an infinite piston stroke. The two solid rotors with screw profiles are timed by a set of timing gears supported by oil-lubricated bearings, which are protected from process fluids by mechanical seals. The opposing flow direction in the pump balances axial hydraulic forces, which reduces bearing load and smooths the flow to reduce pulsations and vibrations. Thanks to the timing gears, the rotors run without touching the surrounding housing or any screw profiles. The resulting clearances allow for internal back or slip flow, which is essential for handling and compressing the gas phase of the multiphase flow stream.
The twin-screw pump’s ability to deal with different viscosities–including emulsions, paraffin and solids–while handling as much as 97 percent gas volume fractions (GVFs) makes it ideal for supplementing downhole pumps and gas lift systems.
The pump discharge pressure is not related to inlet pressure or connected to a particular pressure ratio. This is vital for lowering gathering and annulus gas wellhead pressures, which in turn, lowers the bottom-hole pressure accordingly. It has a positive effect on the inflow performance relationship (IPR) by improving well inflow from the formation and creating a higher liquid level in the wellbore to increase the submergence of downhole ESPs or plungers, which has a significant positive impact on downhole pump and gas lift performance.
A larger number of pumping chambers are formed in the twin-screw pump when the two rotors with meshing screw profiles are turning. As shown in Figure 3, the chambers transfer the volume of gas and liquids that are contained in each chamber from the inlet to discharge side of the rotors by the two opposing sets of screw profiles. This configuration neutralizes the hydraulic axial load and eliminates the need for balance drums or thrust bearings.
Handling Liquid, Gas Phases
The liquid phase of the multiphase flow plays a deciding role for compressing the gas. As a result of the screw rotation, the gravity difference between gas and liquid will force the liquid phase to separate from the gas phase. The liquids will remain in the annulus formed between the liner and the tip of the screw profile, while the gas will accumulate along the center at the root of the screw profile. When the flow stream reaches the end of the screw profile, it becomes exposed to the pump backpressure and an almost solid liquid phase develops.
Because of the pump discharge or backpressure, the liquid will flow as an annulus slipstream in the opposite direction of the main flow and subsequently backfill one chamber after the other. The gas in each chamber becomes compressed by the backflow and the gas volume is reduced significantly as the pressure increases at the pump discharge.
In addition, the liquid in the flow stream plays an important role for sealing the screws, compressing the gas and removing the heat of compression. At a very high GVF (98-99 percent) the stability of the liquid phase is no longer assured; the liquid can foam and the backflow can be undefined and turbulent, or simply disappear. If the liquid flow is disrupted, the pump will lose the ability to compress gas and could vapor lock. This may result in overheating, which can damage the pump.
The liquid fraction at the pump suction needs to be kept at a minimum of 3-5% of inlet flow. However, adding a liquid recirculation system (Figure 4) as an integral part of the pump package allows the unit to run on 100% gas at the skid inlet for an extended time. The liquid recirculation system includes a liquid knockout boot or separator, and is designed to retain adequate liquid to compensate for long gas slugs and unstable inlet conditions. It is important for starting up and flowing shut-in, gas-capped wells, where the gas is the initial flow and little or no liquids are produced.
In wet-gas applications, the liquid knockout also can work in conjunction with a gathering compressor where a reduced sized inlet separator becomes the knockout boot, and combining with liquids from the scrubber, the multiphase pump transports all liquids plus carry under gas to a re-combiner downstream of the compressor. The advantage is that only one pipeline is needed for bringing the total production to the gas processing plant and all liquids handling is eliminated at the production site.
Production Challenges
The increasing use of downhole pumps has become necessary, often right from the start of producing a reservoir as operators push to accelerate recovery from shale and tight formations with faster decline rates. In North America, more than 85% of all producing wells are on some form of artificial lift. In addition, multiwell drill centers and pad production are used to maximize operating efficiencies, centralize surface processing and minimize facility footprints.
For all its benefits, pad-based unconventional reservoir development also can lead to complex well architectures with long horizontal legs. The added complexity makes lifting with conventional downhole pumps difficult and can present the operator with a whole new set of problems, including unpredictable production flows with declining revenue streams because of interruptions and unplanned costs for well service, workovers and well interventions.
To overcome this challenging production environment, operators are adding multiphase boosting with twin-screw pumps to existing artificial lift systems. Installing a multiphase pump on a multiwell gathering system offers many advantages for optimizing artificial lift. Reducing the flowing surface pressure reduces backpressure on flowlines, production headers, wellheads, and further upstream, downhole pumps. The lower surface pressure results in lower bottom-hole pressure for improved IPR, better well inflow and increased liquid levels in the wellbore.
Higher liquid levels are important for artificial lift. The deeper submergence of ESPs and sucker rod pumps enhances hydraulic performance by improving net positive suction head. At low wellbore liquid levels, downhole pumps operate in or close to the bubble point region. Gas will come out of solution and restrict the inlet flow, resulting in poor hydraulic performance with an instant production drop and possible damage to the equipment.
By reducing flowing wellhead backpressure with a multiphase pump, the resulting higher liquid level will keep the gas in solution and allow the downhole pump to operate above the bubble point. A downhole pump running at its optimal efficiency point on the curve will improve its gas handling ability and substantially reduce the risk of vapor locking and head loss caused by entrained or free gas.
As shown in Table 1, after a multiphase pump was installed in one field application, the higher liquid level associated with the lower bottom-hole pressure added significant submergence of both ESPs and sucker rod pumps. The reduced hydraulic work improves service life, reduces electric loads on ESPs, and lessens wear and tear on beam pump rods, couplings and connectors.
TABLE 1
Examples of Increased Submergence of Downhole Pumps with Multiphase Pumps
Source: 2018 Multiphase Pump Users Roundtable South America
An additional advantage manifested itself in a situation where there were problems maintaining constant production flow and pressure in test lines from wells during testing. Placing a multiphase pump down stream of the test separator facilitates well testing by managing test line flow using the pump’s speed control. The flow is directly proportional to speed and largely independent of backpressure from the production separator.
Wells on gas lift also can improve production and total recovery substantially when multiphase pumps are used to reduce backpressure. Gas-lifted wells, which have a tendency to liquid load and can experience very unstable flow because of lift gas supply or underperforming gas lift valves, will be supported by the reduced backpressure created by a multiphase pump. In wet-gas wells, the reduced wellhead backpressure will assist in unclogging the liquids trapped in the wellbore much faster than is possible with conventional plungers, quickly bringing wells back to production.
Additional Benefits
Multiphase pump-assisted downhole pumps will perform more efficiently when facing flow assurance challenges that relate to handling viscous oil, oil/water emulsions, and high gas-to-oil ratios. Unpredicted events in a producing formation can result in gas pockets or gas breakthrough can start to develop. Equally possible are flow assurance issues in wells subject to EOR production when emulsions occur with variations in water cut.
Any of these conditions present difficult operating challenges for any type of downhole pump. Studies have shown a significant drop in hydraulic performance when an ESP encounters higher gas fractions with transients and gas slugs. Performance setbacks also can be caused by high flowing viscosity or paraffin-rich crude oils, where startup after a shut in can lead to blockages or flow restrictions.
Operators looking for simplified gathering systems with minimum surface infrastructure and facility footprints, and observing increasingly stringent emission and health, safety and environmental standards, can be helped by incorporating multiphase pumping in their field production operations. While fewer well interventions and longer periods between service and overhaul reduce workover-related costs, the increased production and added recovery are the principal benefits to the artificial lift system.
A multiphase pump skid can be installed on a gathering system with little or no production disturbance when configured in a “kidney loop” or as a bypass layout. Drag skid and portable natural gas-fired units are available for facilities with minimum infrastructure and no utility service.
An electric motor- or natural gas engine-driven multiphase pump is self-supported with automatic pump speed control, instrumentation and safety shutdowns. It is designed for unmanned operation with standard communication protocols and supervisory control and data acquisition for real-time monitoring and remote access. With operators and asset managers focusing on optimizing production from facilities on artificial lift, a multiphase pump offers a simple way to achieve improved bottom-line results.
On the business side, when operating in a volatile commodity price market, production assumptions and predictions play an important role in satisfying investors and other stakeholders. Multiphase pumping brings an extra level of security by adding more flow control to the operation of downhole pumps and gas lift systems. Today’s new and more sophisticated downhole sensors make it possible to run multiphase pumps based on real-time downhole information. That will one day make it possible to fully digitize the process and optimize the entire flow stream from downhole pumping to the first-stage separator.
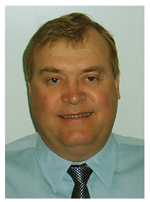
SVEN OLSEN is a senior consultant for Leistritz Advanced Technologies Corp. in Allendale, N.J. His 33-year career at Leistritz includes serving as chief executive officer and president. Olson was involved in testing and introducing multiphase pumping technology to North America, and he actively participates in applying and promoting the technology in both the onshore and offshore sectors of the oil and gas industry. He holds a degree in process engineering and an M.B.A. from the University of Lund in Sweden.
For other great articles about exploration, drilling, completions and production, subscribe to The American Oil & Gas Reporter and bookmark www.aogr.com.