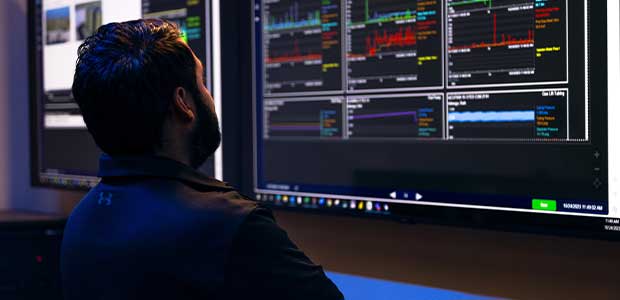
Devon Energy Stays Ahead Of Technology Curve
By Danny Boyd
OKLAHOMA CITY—The concept of artificial intelligence has been around for decades, fascinating humans with never-ending “what-if” possibilities and sparking every conceivable imagining of the futuristic scenarios—some good, some not so good.
But ready or not, the age of AI has already dawned. The “ghost in the machine” is sentient computer programming that simulates the workings of human logic and reasoning, and it is growing more capable every day. Science has caught up with fiction.
In the world of oil and gas, artificial intelligence applications are everywhere—from geophysical processing and interpretation to well drilling and production operations. Like the early days of desktop computing, AI-infused applications are quickly becoming ubiquitous for both big and small tasks in every oil and gas discipline. It is a tool like any other, but it has capabilities unrealized until now, and the implications are far-reaching.
The state of the art in AI has evolved in distinct phases, starting with rules-based systems capable of only doing what their programming allows (i.e., staying in the fairway). The adoption of machine learning made it possible for AI to identify patterns in datasets and make predictions, and then incorporating neural network-based deep learning techniques and large language models (LLMs) allowed AI to more closely mimic the functioning of the human brain and decipher complex data.
The latest evolutionary turn is multimodal generative AI (GAI), which uses generative models to learn underlying patterns and structures in a training dataset to create new relevant content and data points.
Differentiated By Technology
Where does it go from here? As a first mover on technological innovation, Devon Energy Corp. is already en route to the future of AI in upstream oil and gas applications. The company is leveraging AI as part of its broader digital strategy to enhance employee productivity, boost bottom-line efficiencies, and drive value creation across its operating footprint encompassing 1.52 million net acres in five premier onshore basins.
“We view technology as a differentiator,” says Chief Technology Officer Trey Lowe. “It continues to be a focus for us to make sure we are separating ourselves from the pack. We have made significant investments, and that has brought us to where we are today as the world rapidly changes with the adoption of AI across many domains.”
Empowered by AI solutions such as ChatDVN, productivity among engineers, software developers and geoscientists performing daily tasks has improved between 15% and 30%, Devon says. The next move with ChatDVN is expanded analysis of infrared and standard video. Devon maintains cameras across its U.S. operations, and through a proprietary application, runs analytics in which computers view images and compare them to data streams to identify potential anomalies. Next year, the company intends to begin using AI to convert video to data and determine best-fit end uses.
Technology made unconventional plays, and as a pioneering force in horizontal resource development, Devon has a rich history of adopting technology and making it its own through ingenious yet deliberate application. In short, few can go toe to toe with Devon when it comes to technical proficiencies.
For example, in the Delaware Basin, the company’s utilization rate for simulfracs is up to 60% this year, with completion efficiencies improving 12%. In the Powder River Basin, Devon is drilling three-mile Niobrara laterals into a deep stratigraphic column in fewer than 10 days.
In every aspect of its business—whether exploration, drilling, completion, production, or midstream—Devon’s goal is to continually improve and perform every project and every task better than the one before. That is where technology comes in, according to Lowe. But it’s not just technology; it’s understanding and perfecting its application to maximum effect. After all, even the most proprietary technology can only be as good as its application allows.
With an eye on continuous improvement and maintaining a competitive technological advantage, the company is forging ahead with work this year on a business optimization plan overseen by Lowe that includes ongoing investment to standardize wellsite sensors and equipment to support expansion of AI across the organization.
AI-supported efficiencies are expected to play a major role in achieving an additional $1 billion in additional free cash flow this year, Lowe says. Already, all production locations are equipped with digital cameras, automated equipment and high-speed internet for dispatching more data to the cloud for analysis. Installing the same sensors and systems is crucial to providing clean, uniform, high-quality data for engineers, geoscientists and analysts to use with AI to find new solutions, he says.
“The cherry on top is whenever somebody finds a new solution or an idea based on that data, you can scale it across the entire organization,” Lowe explains. “If an engineer in South Texas comes up with a new way to do gas lift, because all our systems are the same, you can just copy, paste and apply it across all gas lift locations, whether in North Dakota, Wyoming or New Mexico.”
Proprietary AI Platform
The company’s internal AI development team built its proprietary system on an AI platform that includes AI tools, machine learning, and large language models that generate and understand human vernacular. An incorporated system called Data at Devon gives employees access to information accessible by typing in natural language.
Devon Energy views technology as a differentiator to help the company separate itself from the pack. The company is leveraging AI and other cutting-edge digital tools as part of a broader strategy to enhance productivity, boost bottom-line efficiencies, and drive value creation across its 1.52 million net acres in five premier onshore basins.
The advancements mean Devon’s team can now apply AI to subsurface characterization, drilling, completions and production domains. It also contributes to efficiencies in back office and support functions.
With a top-down and bottoms-up commitment from the executive team on down, the company has undergone complete digital training for all company leaders using an AI-101 training regime that is part of the system. By the end of June, some 1,000 Devon employees had completed the program.
Results have come quickly. One Delaware Basin location included a centralized compressor to operate gas lift across dozens of wells. Using real-time, physics-based models at scale, Devon’s operations team optimized the centralized gas lift compression across many wells and improved oil production by 5%, Lowe reports. In the next phase of the project, the engineering team began scaling optimization algorithms across the broader company, he goes on.
“The engineers have done a great job coming up with an innovative solution that no one was thinking about in terms of how they can use this system,” he says. “They are using that scalable physics-based model to help them indicate where they should put more of the gas from centralized gas lift compressors to optimize oil production rates.”
In only a few hours, a Devon engineer used AI to optimize simulfrac operations by coordinating sequences of pumping stages and wireline deployment across multiple wells. Performing the task manually would have taken much longer, Lowe states.
Empowered by AI, productivity among engineers, software developers and geoscientists performing daily tasks has improved between 15% and 30%, Lowe adds.
Although managers can choose to automate the same AI recommendations offered consistently over time, humans are in the loop, overlooking any recommendations and approving them, Lowe says.
“At Devon, we are looking at this as a way for our employees to be more empowered, not as a way to replace jobs,” he comments.
The next move with ChatDVN is expanded analysis of infrared and standard video, Lowe previews. Devon maintains cameras across its U.S. operations, and through a proprietary application, runs analytics in which computers view images and compare them to data streams to identify potential anomalies. Additional development has been temporarily paused as the team focuses on other LLM and AI applications, but Lowe says Devon plans to begin using AI in 2026 to convert video to data and determine best-fit end uses. AI can use video to enhance location safety, identify hazards, detect spills and emissions, and assess images of pumps and other production systems to identify appearances of substandard operation or equipment issues, he details.
“Our drilling contractors have had a lot of success using cameras to identify and mitigate potential safety incidents,” Lowe comments. “There is probably an easy analog for us to apply the same solutions into other parts of our business, including production operations.”
The bottom line, Lowe concludes, is that AI makes employees’ lives easier, more productive, and hopefully, more innovative. “With these AI-based tools, our employees can come up with creative solutions that are better than what they would have been able to do manually. And because of the way we are organized as a company, they can quickly transfer those solutions to another engineer working on another set of wells and repeat it again,” he states. “That is the real power of AI for us today.”
For other great articles about exploration, drilling, completions and production, subscribe to The American Oil & Gas Reporter and bookmark www.aogr.com.