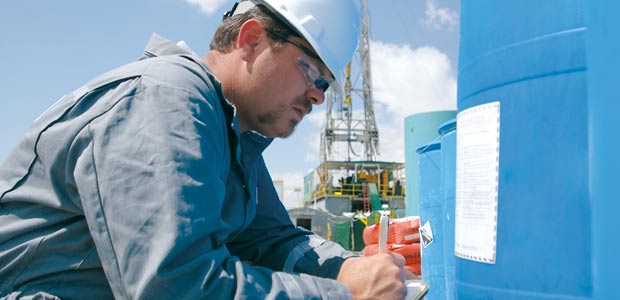
Advanced Fluid Systems Aim To Stabilize Well Bores, Minimize Nonproductive Time
By Jim Redden
HOUSTON–Making new hole as long as possible with no unexpected interruptions has been the mantra of operators since Colonel Drake decided that drilling an oil well in Titusville, Pa., seemed like a swell idea.
It is little wonder that as rig rates–especially those for deepwater semisubmersibles and drill ships–soared in recent years, the call to minimize downhole troubles, which in industry vernacular translates to nonproductive time (NPT), would intensify from mantra to decree. And even though reduced drilling activity has led to a general decrease in day rates in 2009, lower commodity prices and tighter economic margins only underscore the emphasis on minimizing NPT.
The economic ramifications of NPT have reached the point where operators reportedly routinely add 10-20 percent in well authorizations for expenditures to account for anticipated downtime. At the top of an operator’s hit list is well bore instability, which is thought to be responsible for as much as 44 percent of NPT unrelated to weather.
Operators say they can ill afford the estimated $1 billion a year they are forced to spend collectively in the Gulf of Mexico alone to combat severe lost circulation, stuck pipe, collapsed hole, well control issues, and other difficulties that accompany an unstable well bore.
Standing on the front line of defense are the drilling fluid companies, who hold the key to mitigating NPT-related costs by engineering systems to maintain and enhance well bore stability and minimize resulting lost circulation, which despite enormous strides over the past few years, remains among the costliest of all problems encountered in well bore construction.
“If you look at the big three causes of subsurface NPT, it is well bore instability, lost circulation and well control, and each of these has a strong fluid component,” says Eric van Oort, planning and business improvement manager at Shell E&P Americas. “It all comes down to good fluids engineering.”
Talk to a technical specialist at any drilling fluid company and one gets the impression operators are preaching to the choir. For fluids companies, improving well bore stability (particularly in highly reactive shales), the narrow drilling windows intrinsic of deep water, environmental advances and reducing costs in the prolific onshore shale plays have become priorities de jour. Drilling fluids chemists and engineers discuss their work using terminology such as “particle size distribution,” “membrane efficiency,” “flat rheology,” “hoop stress enhancement” and other technical lingo that would have left Colonel Drake and his contemporaries scratching their heads and wondering if they had been dispatched to some parallel universe.
Going On The Offensive
While each mud company has its own strategy on how best to shore up a well bore and keep drilling fluids where they belong, they all share a unifying conviction that the time has come to go on the offensive, rather than build a wall of defense once a loss zone has been penetrated. In fact, M-I SWACO has concluded that the appellation “lost circulation material,” which generically encompasses the wide range of particulates used to plug a permeable loss zone after fluid has escaped into the formation, is antiquated and prefers the less reactionary “loss prevention material” designation.
For Halliburton’s Baroid, the first step in developing its multipronged well bore stability initiative was securing a deeper understanding of the mechanisms that actually trigger instability. “We have looked at it on both a more traditional macro scale and the less traditional micro scale, where we are really trying to understand from a micro level what is going on within the well bore, and if there are things we can identify that will give us an indicator of how the well bore will behave,” relates Nick Braley, director of technology.
One thing that is universally understood is that pre-emptive approaches, which in the extreme extend to using cement or an extra string of casing to strengthen a weakened well bore, renders many a project financially unfeasible. This is particularly true for “brown field” developments where additional reserve replacement nearly always involves penetrating aging and highly-depleted reservoirs.
M-I SWACO has developed what Senior Technical Adviser Fred Growcock says is a more proactive, yet much less expensive option for fortifying a fragile formation, and one that is especially applicable for depleted zones, deviated well bores and deep water. Earlier this year, the company unveiled its integrated methodology combining engineering, chemical and mechanical disciplines to stabilize a well bore during drilling. Ironically, he notes, the process actually uses drilling-induced fractures to its advantage.
Growcock explains that the well bore strengthening methodology provides various solutions to buttress depleted and fragile zones at or near the fracture gradient. The process includes an engineering software package (Figure 1) that allows operators to ascertain fracture width for various rocks under myriad downhole conditions. The proprietary software calculates the width of the stabilizing shallow fractures that actually are induced during treatment, and then determines the blend of particulates required to fill and hydraulically seal those fractures. This serves to isolate the fracture interior and prevent the further propagation of an unstable fracture.
“This process enables the drilling of many previously undrillable formations, while optimizing casing string design and reducing the costs associated with lost circulation,” Growcock offers.
Primary Design Criterion
For Baker Hughes, the line of attack actually begins in the development phase of a proposed fluid system, says Robert Peresich, drilling fluids product line director. “Well bore stability is at the heart of almost every drilling operation. Consequently, it is one of the primary design criteria of our fluid systems,” he states.
Many of the well bore strengthening schemes adhere to the so-called stress cage mechanism that BP coined to define the process of adding specially designed proppant material to the fluid before raising its pressure above the fracture gradient. Also known as “hoop stress enhancement,” the aim is to induce short tensile fractures in the vicinity of the well bore wall. By blocking the fractures from spreading, the mechanism essentially creates a stress cage to provide near-well-bore strengthening of a weak and permeable rock.
Del Leggett, marketing director at Newpark Drilling Fluids LLC, says that while mechanical strengthening mechanisms such as stress caging play a vital role, Newpark’s research focuses primarily on the interaction between reactive shales and drilling fluids.
“We continue to work on osmotic controls, and the tack we have taken is to achieve controlled activity in drilling fluids using a substitute for (environmentally suspect) salt. We have built advanced tools for measuring fluid transfer from the fluid to the shales, and vice versa. For instance, we use a downhole simulator cell (Figure 2) that can actually quantify how much fluid is going back and forth. We use it as a measuring device to see how effectively we are controlling it so we do not alter and weaken the shale,” Leggett remarks. “Of course, we also look at the mechanical factors, such as stress cage and hydraulics monitoring.”
Jim Friedheim, M-I SWACO’s corporate director of fluids research and development, points out that the success of its integrated program notwithstanding, research continues on developing novel ways to strengthen the well bore while drilling. “What we always are looking for is a new mechanism for strengthening the well bore in a variety of zones, both chemically as well as mechanically. The current approach is to use particulates to help bridge and shut off pressure transmissions,” he says.
The approaches to achieving a stress cage vary widely, as do opinions on what constitutes ideal sealing materials. “Some contend that we need hard, robust spherical materials, so there is a real push in some corners for very hard calcium carbonate types of materials. Others prefer graphites and similar products that are elastic and resilient to provide a material that rebounds. We know the well bore will have to pressure up and relax over time. If you have particles that can adjust when the fracture changes, that should maintain the seal and keep the fracture from reopening,” Baroid’s Braley contends.
Engineering Software
Over the years, acceptance of the techniques directed at artificially strengthening a well bore during drilling has had as many starts and stops as a crash-riddled auto race. Well bore strengthening concepts were conceived in the early 1990s, before becoming sidetracked in the latter part of that decade. The practice experienced a resurgence earlier this decade, perhaps coinciding not so coincidentally with rig rates and overall drilling costs that jumped exponentially.
However, Braley says he believes the industry’s renewed acceptance was generated not so much by economics, but renewed confidence in the engineering principles behind it. “We reached a point where we were able to effectively use software to show the customer that there was sound engineering behind this. It became a reality when we were able to put in rock parameters and show the customer the fracture width, the particle size distribution and all the supporting data. I know when Baroid introduced its lost circulation treatment software, it increased customer confidence because of the sound engineering applied,” he holds.
“The engineering we have put into well bore strengthening also has led to improvements in managing lost circulation. Our conclusions from research into well bore strengthening led us to look at things differently. We are now looking at better sizing, narrower particle size distribution, and bimodal distribution in some of our lost circulation material,” Braley adds.
Likewise, Peresich says Baker Hughes’ comprehensive suite of engineering software packages has been critical to the entire stabilization process, especially when it comes to monitoring premium fluids in extreme environments. “Our software accurately predicts the hydraulic forces that can be optimized to maintain well bore stability, even in extreme high-pressure/high-temperature conditions or the wide temperature ranges in ultradeepwater wells,” he states.
Managing ECD
In deepwater operations, it is almost an inevitability that mismanaging equivalent circulating density (ECD) will propagate an unstable well bore. This is an environment where temperatures and pressures can change in a heartbeat, and in so doing, completely alter the rheological properties of the premium synthetic drilling fluids employed almost exclusively to cope with the narrow mud weight windows (Figure 3).
In response, all the major mud companies have their own versions of a “flat rheology” SBM engineered to deliver a constant rheological profile independent of temperature and pressure. That is all well and good, but M-I SWACO’s Friedheim insists that the industry should aspire to develop a fluid that genuinely delivers almost methodical performance, similar to a mechanical tool, he says.
“The flat rheology systems have been great, but they can possibly be improved in terms of being flatter, so you literally have a fluid that performs like a tool,” Friedheim comments. “We are still looking at how to simplify and manage them better. In line with this, we are also always looking at ways of preventing (barite) sag. Today, for instance, we use micronized barite to prevent sag and minimize ECD fluctuations. It all comes down to finding chemical solutions to engineering problems.”
Baroid’s Braley adds that efforts to make thinner fluids must come with a caveat. “The focus has been on developing thinner fluids, but if the fluid is too thin, in some of these smaller well bores being drilled today you may see a change in flow regime. This can have a huge impact on ECD, so that any benefit you get from a thin fluid design is offset by flow regime transition. Now, all of a sudden, you are looking at running flatter rheological profiles in a laminar flow regime, while still trying to minimize the ECD impact,” he says, adding the two primary technology gaps center on improving the gel structure and low-end rheology.
Peresich points out that ongoing Baker Hughes research efforts reflect the importance being placed on ECD and all other issues that impact deepwater drilling. “The pace of change within our product development and research groups has increased greatly over the past 12 months,” he says. “Through continuous improvement measurements in deep water, we recently, for example, extended the temperature range of constant rheology SBM up to 300 degrees. This more robust formulation provides improved resiliency to contaminants along with lowering the HP/HT filtrate.”
The Holy Grail
Regardless of the approach taken, drilling fluids experts say any discussion must begin and end with the time-worn examination of shale inhibition. Considering that shales are directly responsible for upward of 70 percent of all drilling problems, according to the University of Texas Center for Petroleum & Geosystems Engineering, the issue remains both relevant and prevalent (Figure 4).
“We are constantly looking at different ways to stabilize shales. From the water-based mud side, you obviously have chemical instability (issues), while on the oil-based side, you have hydraulic instability,” says Friedheim, adding that the newest generation of M-I SWACO’s proprietary hydraulics monitoring software will include a well bore stability module.
Both shale inhibition and environmental issues figure prominently in the industry’s seemingly never-ending quest for its true holy grail: an aqueous-based fluid that will mimic precisely and consistently the performance characteristics of a premium invert emulsion system without the resulting environmental headaches and costs. Like constant rheology SBM systems, nearly every company has its own brand of a high-performance water-based drilling fluid, but their creators say much remains to be examined.
“We basically are going back to some of the basics of the shale inhibition mechanism. We are looking at some novel chemistries and applications of those chemistries, and trying to get away from the traditional amine or synthetic approach. As these things pan out, they certainly may prove to be game changing,” comments Friedheim.
Paradoxically, Braley says he believes the biggest steps the industry has taken in developing high-performance, water-based fluid systems was when it decided to look beyond a singular fixation on inhibition. “The drilling fluid industry made some interesting steps earlier this decade when it came to realize that ‘high performance’ was more than simply looking at shale instability. Those were huge steps because previously it had all been about inhibition, inhibition, inhibition. In reality, when you are talking about mimicking the performance of an oil-based mud, you also need to look at lubricity and other parameters,” he notes.
“For example, there was a great deal of focus on silicates over the years, which even today are some of the most effective inhibitors, but they do not necessarily give the performance operators are looking for,” Braley adds.
Shale Play Challenges
According to Leggett, Newpark may have found the answer with a new water-based fluid developed specifically for the Haynesville Shale, where horizontal lateral sections generally are drilled in the shale zone with low permeability and equally low clay content, making issues such as fluid loss control less important. The original driver behind the soon-to-be-introduced system, he says, was to help operators reduce the exorbitant disposal costs of cuttings generated by the invert-emulsion fluids used in horizontal, extremely hot Haynesville wells. Many operators were forced to transport cuttings to Oklahoma for burial at approved disposal sites, Leggett notes.
Moreover, he says many of the prevailing downhole and environmental issues in the Haynesville are also present in the Marcellus Shale, which spans some 600 miles northeastward from West Virginia to New York. Newpark started from the ground up with the intention of designing an entirely new system that could handle the unique rigors of shale with cuttings that would be suitable for land farming and other cost-effective and environmentally benign disposal options, Leggett recalls.
“The new system is stable to 400 degrees Fahrenheit and impervious to carbon dioxide contamination. What we also have built into the system is extreme lubricity with a lubricant that stands up to those temperatures. We also developed a polyglycerin product that replaces salt as an activity control agent, making the system more suitable for land farming,” he explains. “We think it is going to be huge and we really are excited about it.”
Leggett adds that from all appearances, operators in U.S. shale plays appear motivated to embrace promising new fluid technologies. “Producers are using a lot of mud systems–saturated calcium chloride saltwater systems, PHPA systems, synthetics, etc.–looking for the right answer,” he states. “This is a classic situation where these shales are new plays, and technologically, operators are trying to get their arms around what is happening down hole.”
Peresich says Baker Hughes also has advanced its water-based fluid technology and has a system that can handle the multitude of technical and environmental issues in the Haynesville and other extreme application environments. “We have a flexible system that can be customized as a viable alternative to oil-based fluids, even in high-temperature and high-mud-weight areas. This technology also offers superior environmental and economic value,” he details.
According to Friedheim, M-I SWACO also has taken notice by re-engineering an earlier designed paraffin-based drilling fluid that will be designed to handle both the operational and environmental constraints. Much of the original work on the system was undertaken at the company’s greenhouse–the only of its kind in the industry–designed to examine the impact of drill cuttings on plant growth, he says.
Ultra HT/HP Applications
In addition, the new shale frontiers have had a hand in accelerating the industry’s efforts to design fluids for ultra HT/HP applications, which can account for as much as 20 percent of additional costs related to mud losses. Braley notes that operators once considered HT/HP wells as having bottom-hole temperatures of 350 degrees, requiring 15 pound/gallon fluid density. Today, he says, the HT/HP barometer is between 400 and 500 degrees, dictating mud weights to 19 pounds/gallon. However, developing a system to address the high temperatures poses environmental limitations.
“Operators are really pushing the HP/HT envelope,” Braley observes. “We have spent a lot of time getting away from biopolymers that generally are stable up to 275 degrees. However, the synthetic polymer additives that can make a fluid more thermally stable also can make it less biodegradable. We have made a step change around high-temperature polymers for water-based mud. We have done lab work that shows it stable to 375 degrees, and we now are conducting drilling cycle testing to 450 degrees.”
Although ever-tightening environmental restrictions, coupled with progressively more technically demanding drilling applications, easily justify the technology explosion within the drilling fluids industry, Leggett says companies should not underestimate the value of well site engineering. That is particularly true in the current business environment, he relates, with dramatically reduced rig counts slashing the collective market share for all service companies and making sound well site engineering a prime differentiator.
“So much of the value any fluid company can bring to any project is related to well site management, which, of course, is about drilling and drilling fluid practices at the rig site,” Leggett concludes. “The nuts-and-bolts fluids issues and the day-to-day management of what we do at the rig site are huge.”
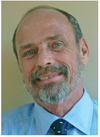
JIM REDDEN operates Houston-based Point Blank Communications, specializing in marketing communications for upstream oil and gas companies. He has 37 years of communications experience, focused primarily on the upstream industry. Redden has an extensive background in drilling fluids, having served as technical communications supervisor for M-I SWACO, following a tenure as senior technical writer for Hughes Christensen. In addition, he was an editor for a petroleum industry trade journal and an award-winning reporter and editor for newspapers in Ohio, Florida and Texas. Redden holds a B.A. in journalism from Marshall University with post-graduate work in communications arts.
For other great articles about exploration, drilling, completions and production, subscribe to The American Oil & Gas Reporter and bookmark www.aogr.com.