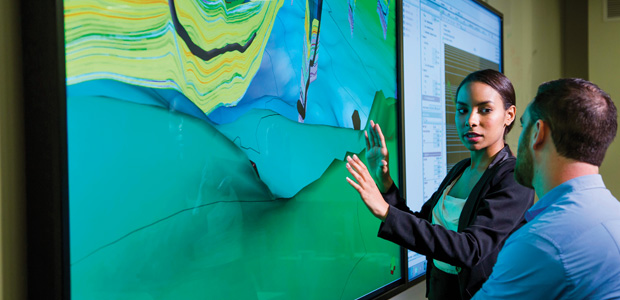
Leveraging Big Data
Analytics, Dedicated Centers Enable Real-Time Optimization Of Devon Energy’s Operations
By Kari Johnson, Special Correspondent
OKLAHOMA CITY–Oil and gas companies understand the challenges associated with dealing with massive quantities of data, as well as the competitive advantages that come from rapidly extracting actionable information from “big data”–whether in the form of 3-D seismic, drilling data, well logs, or production reports.
Given the ever-increasing volumes and variety of data, as well as the complexities of the business and operational challenges oil and gas companies face today, the need is greater than ever to invest in advanced analytical functionalities to produce new insights and optimize operations in new ways, says Kathy Ball, manager of exploration and production analytics and data science at Devon Energy Corp.
According to Ball, Devon Energy was an early adopter of advanced analytics and now is applying the technology throughout the organization, including in human resources, portfolio management and strategic planning, basin analysis, real-time drilling, and asset monitoring and predictive failure analysis. The payoff is measured in bottom-line metrics such as reduced drilling costs and increased production.
Ball joined Devon last year, and says she has benefited from the technological foundation that was put in place by “those who came before.” The projects Ball and her team are working on include predictive, prescriptive and cognitive analysis.
“These are exciting times!” she exclaims.
Operational “Nerve Centers”
Devon’s initiative to leverage the power of data science and analytics began in 2012 when it made the decision to establish real-time “nerve centers” for its U.S. production operations, Ball relates. Soon thereafter, it built a centralized facility to support all its drilling operations.
Decision support centers (DSCs) are located in Devon Energy’s core producing areas, and operate 24 hours a day, seven days a week. Experts analyze real-time data streaming in from producing wells to optimize performance and lower operating costs, according to Ball. Similarly, she says, the well construction (WellCon) center is devoted to optimizing drilling and completion engineering on all Devon wells.
“The premise of having expert support centers for real-time analysis and decision making depends on the ability to gather and analyze data from remote field operations,” she says. “If you are geosteering a well or managing a producing well, the centers have to be able to scrutinize relevant information in a timely enough fashion to impact decisions or avoid a potential problem before it can occur.”
Recognizing that good analysis is predicated on having good data, Ball relates that one fundamental aspect of the analytics effort is a companywide data cleanup and governance initiative Devon began four years ago to ensure that experts in the data centers were provided with high-quality, reliable data.
The quest for improved data quality had been building for years as Devon grew through acquisitions, according to Ball. The first internal disciplinary domain to launch a formal data management process was geology and geophysics, she says. Then a few years ago, changes in greenhouse gas regulation necessitated better data to satisfy new reporting rules.
“From there, it has expanded throughout our exploration and production operations, and now includes drilling; completions; production; planning; land; health, safety and environmental; and other functional areas,” she states, adding that Devon’s management places a heavy emphasis on innovation, including on finding “new ways to do things better through data analysis and collaboration.”
“We are applying analytics wherever it makes sense to Devon’s strategic plan,” Ball relates.
She describes the analysis hierarchy as beginning with business intelligence, where the goal is to visualize what happened in the past through a dashboard. “This level of analysis is useful, but it is a bit like looking in the rearview mirror; it does not help much with driving forward.”
The next level tends to focus on predictive analytics, which help in understanding why something happened and when it is likely to happen again, Ball says. One step up on the hierarchy is predictive optimization and forecasting. “This is where the money is,” she says. “Here we learn what the absolute best outcome is if all opportunities are maximized.”
The final step is what Ball assesses as the hottest area in analytics right now: cognitive analytics using artificial intelligence, machine learning, and deep learning to make better decisions in far less time. “This is the new frontier in analytics. The key is to think beyond data as a tool for optimization and to see data as a strategic asset,” she offers.
Real-Time Analysis
For oil and gas companies, analyzing data at the real-time speed of a drilling or well completion operation quickly has become a necessity, particularly given the need to improve operational and cost efficiencies. With the right insights at the right times, Ball says it becomes possible for companies to boost asset performance, improve decision making, lower cost structures, and optimize efficiencies across the board.
“The analytics team at Devon is growing in every dimension,” she reports. “We have more projects every day, and with larger and larger scopes. Our goal is to become a center of excellence, helping Devon’s disciplinary and asset teams improve the performance of oil and gas operations.”
Enabled by production automation and digital oil field technologies, Devon has established decision support centers in each of its field offices, which Ball describes as hubs of field operations with collaboration tools connecting to the corporate headquarters in Oklahoma City.
“With the DSC project, we upgraded our field sites with high-speed communications, added thousands of Wi-Fi access points at well locations, and added automation to most of our wells and other production facilities,” she details.
The result is that all Devon assets are highly instrumented and automated, providing the DSCs with a tremendous amount of real-time data. “This project required automation, real-time data, production, and information technology teams to all work together,” says Ball. “We have been able to make measurable production increases and see the inflection points in each of our field offices within six months of completing each field upgrade to the DSC model.”
Specialists at the centers use analytical software and high-performance computing systems to monitor production operations around the clock, including visualizing data on large-screen monitors. “The idea is to search continually for anomalies in the data, and have the expertise immediately available to respond when an anomaly is identified,” Ball remarks.
Analysts are able to see in real time how equipment is performing to ensure all operations are maintained within desired parameters, and to tell operators in the field if, when and what kind of corrective actions may be needed. “Every element of an asset, including its parts and components, can be monitored remotely,” Ball notes. “Because of predictive analytics, we can greatly reduce the risk of nonproductive time caused by a rod pump, electric submersible pump, or other equipment failure.”
The centers generate exception reports to identify wells that need immediate attention, including potential well problems that could cause lost production. In the past, Ball says, field operators had to visit each well site in sequential order to identify any issues. With centralized analytics, problems are caught sooner and field operators can focus on only those wells needing immediate attention, dramatically improving efficiency and productivity.
Devon attributes increases in production from existing wells to automation and remote monitoring. “Predictive asset failure is a great example of the Internet of Things in action,” Ball offers, explaining that the Internet of Things provides a way to understand how all the component parts in a larger system come together to achieve a desired goal.
“With the Internet of Things, we are looking at the entire system–not just drilling, but how drilling effects completion and production–and how it all fits together,” she says. “Then we can figure out how to optimize various aspects to optimize the complete system. If the analytics team identifies data that could improve predictions, the field team can add technology to collect those data.”
Predictive analytics also help Devon maintain its strong environmental performance, she points out. Monitoring equipment for potential failures provides early warnings of risk related to emissions, leaks and spills, allowing field teams to be deployed to mitigate or avert any environmental impacts.
Operational Intelligence
Historically, reservoir simulation has been one of the most advanced applications of analytics in upstream oil and gas operations. Ball says Devon’s WellCon center is taking that to the next level by applying analytics to real-time drilling control and geosteering, as well as completion and flowback operations.
“For geosteering, we need to know exactly where the bit is and where it will be within the next few seconds,” she states. “Predictive analytics helps us keep the borehole within the targeted reservoir sweet spot.”
All data available are streamed through Devon’s real-time network into analytics systems at the WellCon center for analysis and predictive model building, Ball explains, noting that the WellCon team can monitor simultaneously all the rigs Devon has running.
Devon Energy was an early adopter of advanced analytics, and the company is using the technology in various functions throughout the organization, including basin analysis, real-time drilling, asset monitoring and predictive failure analysis, portfolio management, and strategic planning. The payoff is measured in metrics such as reduced drilling costs and increased production.
The results have been game changing, according to Ball. Wells drilled since WellCon was established have seen significantly less out-of-zone footage and fewer sidetracks, resulting in improved cycle times and lower drilling costs. These results coincide with Devon moving to the top of its peer group in 2015 for new wells’ average 90-day initial production rates.
Optimizing the drilling operation and keeping wells in zone also creates benefits that are harder to quantify, but are certainly no less impactful, Ball suggests. For example, she points out, drilling a high-quality borehole that stays in target allows the subsequent completion operation to maximize the amount of interval that can be stimulated, which ultimately improves productivity and recovery per well.
“Analytics is the key driver to drilling a good well,” Ball insists. “We use big data to figure out where to drill a formation while looking across an entire basin, and make sure the well stays in the formation while it is being drilled.”
During stimulation, WellCon experts use analytics to optimize hydraulic fracturing operations, including analyzing microseismic information to detect subtle patterns the human eye cannot see, Ball adds. “The centers also predict the effect of simultaneous operations so that drilling and completions work can be done in parallel with the least risk of interference to ongoing production operations,” she says. “We also can use analytics to select the best vertical and horizontal candidates for refracturing.”
Yet, despite the rapid evolution of data science technology, the most powerful source of analytical capabilities in any company is the human mind, Ball emphasizes. “Experienced engineers, scientists and technicians have learned what signals and conditions can be used to predict performance or future problems, and they know how to tune systems for optimal performance,” she reasons. “We are acutely aware that we could lose valuable insights without an explicit program to capture the knowledge these individuals possess.”
Consequently, Ball reports that Devon has an active analytics program to capture the knowledge base of its seasoned professionals and transfer key learnings to the next generation. “We document how they approach different problems,” she explains. “We seek the unwritten rules they use to predict performance and failure. Then we automate and create analytical routines.”
Ball says she sees further enhancement of this knowledge transfer process as Devon incorporates video analytics, machine learning, and natural language processing. “There is so much we can do today and even more that is just over the horizon,” she comments.
Vetting Projects
According to Ball, every potential project at Devon begins with a request for analytical services. Each project is vetted by the analytics team, often beginning with an investigation into the underlying question or problem to be solved. Critical early steps in any project are defining a clear objective, delineating how to capture the required data, and specifying what valuable insights can be obtained, she notes.
To be approved, an analytics project must show a tie to Devon’s strategic plan. “If it does not, what is the point?” Ball asks. “It also must pass what we call the ‘so what’ test. If the project owner cannot articulate the value, then how can we be sure to achieve it?”
If a project proposal makes it over those first two hurdles, it then faces a final triad of criteria to ensure it is actionable, data-driven, and has a measureable monetary impact, she goes on.
Analysis is about finding patterns, whether singular or a pattern over time, notes Ball. Her team focuses on pattern seeking with a reference point. “We usually start with a defined problem to solve, because if we wait to see what the data tell us, we can end in analysis paralysis,” she says.
A central part of Devon Energy’s strategy to implement analytics and real-time digital technologies is dedicated “nerve centers” to monitor and support production and drilling operations on a round-the-clock basis. The company has decision support centers in all its field offices that serve as real-time hubs for production operations, and a centralized well construction facility devoted to optimizing drilling on all Devon wells.
There also are patterns in human behavior that must be accounted for, says Ball. “Humans operate differently from machines and from one another,” she observes. “The same equipment in the same environment interacting with different people can have different results. The analysis must be informed by human behavior.”
All data are replicated and stored in a “reservoir” that connects disparate data from disparate systems. “The data reservoir represents the truth for us. It is refreshing constantly so that data are always up to date,” she explains, adding that Devon also has some vendor data in cloud and hybrid cloud configurations. “This level of data integration makes data readily available to support decision making. Users can slice and dice data any way they want.”
Analytics Infrastructure
Before embarking on an analytics project, Ball says Devon’s team considers the four “V” characteristics of the associated data: volume, variety, velocity and validity. The largest sets of data Ball’s team has encountered were terabytes in size, occasionally approaching an exabyte, but she says datasets normally are sized in gigabytes.
Using fit-for-purpose infrastructure and open-source technologies allows the team to cost effectively analyze the full dataset, storing data and running applications on commodity hardware clusters.
“We used to have to look at data samples because of size limitations,” Ball recalls. “With the new framework, we can look at entire basins with no trouble. We pull in the data, create an analysis, and output the results in a form that can be consumed easily.”
One of the keys to Devon’s success with data analytics has been the support from its information technology group, Ball says. “My sense is that there generally is not a high level of comfort in IT departments with using open-source technologies, but in our case, we are collaborating–first and foremost–on the mission to find and produce oil and natural gas.”
The variety of data the team works with continues to broaden, and includes a range of geological and geophysical data (including seismic, petrophysics, geology and reservoir measurements), completions and production data, and business and financial data. The data come from different sources and in different formats, from numerical and text to images and video.
“We analyze text, for example, for potential improvements in nonproductive time,” she illustrates. “Or we may analyze images and associate them to temperature and pressure changes as part of a predictive asset failure program.
“Our challenge is to tie all these data together and run an analysis that produces meaningful, strategic and actionable results,” she continues. “We use a range of analytical techniques, including clustering analysis and supervised learning. The choice of technique depends largely on what is known about the data.”
Velocity has two considerations: How fast data are needed, and how fast decisions must be made. One of the key questions to end-users is what real time means to them. “We get answers ranging from once a week to once every second,” replies Ball. “It is important to define what you really need and really can act on.”
In critical dynamic operations such as drilling or fracturing in which real-time decisions are needed, in-memory and in-database technologies are preferred. “This takes the analysis to the data, rather than dragging the data to an external tool,” she explains.
Validity refers primarily to data quality control, particularly the ability to screen noise and bad data, Ball reveals. “With machine learning and artificial intelligence, if the model does not know there are bad data, then the model is going to deteriorate,” she reasons. “You have to be able to test data quality in real time to determine whether it is within the bounds of reasonable.”
Learning New Languages
Devon’s cross-functional analytics team consists of members with specialization in data science and embedded IT, as well as representatives from oil and gas disciplines. “I have a drilling engineer and a reservoir engineer being trained as data scientists,” she remarks. “These folks are bridges between us and the subject matter experts in Devon’s various departments.”
Analytics requires learning many languages, according to Ball. “And not all of them are computer languages!” she quips. “The biggest surprise to me was how rarely a data scientist spoke the same language as a geoscientist or engineer. A lot of translation is required. Geophysicists and reservoir engineers go straight to the applied mathematics. They see everything through the discipline of their science, so we have to meet them where they are. A good data scientist is insatiably curious and wants to know why. We strive to hear the story the data want to tell, not what we expect to hear.”
Rather than analyzing data in a more natural dynamic state, oil and gas companies traditionally have examined them “at rest,” Ball points out. “The data were captured at a given point in time, entered into a storage system, processed, and then the interpreter looked for an answer,” she says. “The process may have taken a day, a month or a year or longer.”
In contrast, streaming in-memory analysis allows almost instant answers. “End-users are increasingly able to see real-time analysis in three dimensions in a collaborative space, and even in motion,” Ball concludes. “The analysis itself and the results are reflecting the reality of the operations from which data are collected, in that they are becoming increasingly dynamic and moving in real time.”
Ball points out that data science is regarded by many experts as the most critical skill set required across all industries going forward. In oil and gas, specifically, the business case for analytics is powerful already. Looking toward the future, Ball assess the defining role technologies such as analytics, data mining, big data and self-learning machines ultimately will have on the geosciences and petroleum engineering.
“It is exciting to see the next generation embrace analytics and data science as a complement to physics-based engineering,” she enthuses. “Just imagine the leaps our industry can make with that powerful combination!”
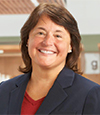
KATHY BALL is manager of exploration and production analytics and data science at Devon Energy Corp. Describing her work as “part data whisperer, part data detective,” Ball is focused on collaborating with subject matter experts to solve complex oil and gas issues using advanced analytics and big data. She previously served in systems engineering, data science and energy analytics roles at SAS®, and as business development manager at Progress Energy. A certified project management professional, Ball holds a B.S. in geology and civil engineering from Guilford College, and an M.S. in management and operations management from Purdue University.
For other great articles about exploration, drilling, completions and production, subscribe to The American Oil & Gas Reporter and bookmark www.aogr.com.