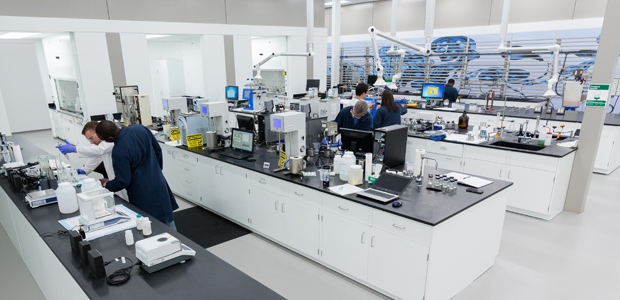
Oil Field Chemistry
Cost Effectiveness, Long-Term Sustainability Drive Chemistry Best Practices
By Kari Johnson, Special Correspondent
HOUSTON–The size and scope of horizontal resource plays, the dynamic nature of multiphase production from unconventional reservoirs, and of course, the relentless drive to enhance efficiencies and profit margins are leading to innovations in the cost, performance and sustainability of both completion and production chemicals, according to Danny Durham, Apache Corporation’s director of global upstream chemicals.
“The newest generation of chemical formulations is more effective and more environmentally friendly than ever before, and at the same time, best practices at the well site are reducing chemical program costs and risks,” he says.
Chemicals are a key element of every production environment, from low-volume mature fields to high-rate horizontal developments. Operators rely on chemicals to solve challenging and recurring problems such as scaling, precipitation/deposition, foaming, emulsion, corrosion, bacterial growth and toxicity. Annually, production chemicals represent about a $2 billion market in North America, says Durham, and are generally among the top five categories of lease operating expenses.
“The chief goal of production chemicals is to keep production flowing unhindered while protecting asset integrity,” he relates.
To achieve this goal most cost-effectively, operators have three primary areas on which to focus optimization efforts: chemicals, manpower and failure rate costs. While many advanced chemistries are available to help operators improve well performance, some of the greatest optimization opportunities for oil and gas companies are in the manpower and failure prevention areas, Durham contends.
“It takes a lot of personnel both on the operator’s side and the vendor’s side to supply and apply production chemicals,” he says. Consequently, oil field automation is key to optimizing chemical programs. “Technology is making it cost-effective to automate even mature assets to remotely monitor and control pumps, tanks, sensors and other production equipment–including chemical injection and metering,” he explains. “Instead of spending time and money driving around ‘finding and figuring,’ pumpers can focus on ‘fixing’ any chemical-related issues.”
In a field with 2,000 wells, Durham estimates that 10-20 percent of chemical pumps and stream flushes require calibration or repair at any given time. The challenge for traditional monitoring is that field personnel must physically travel to each well to inspect it. “If the wells are spread out over hundreds of miles, it takes a lot of people to do proper surveillance,” says Durham. “Monitoring wells remotely allows the pumper to quickly determine which wells he needs to actually visit.”
While production chemicals are required on virtually all wells, they are vital to the performance of mature assets, which represent the vast majority of all producing wells, Durham notes. Many have low oil and gas production rates, high water cuts, and scaling, asphaltene and other challenges.
Reducing Costs And Risks
As automation and connectivity costs come down with the advent of digital solutions, Durham says the technology becomes a viable alternative to traditional treater truck-based well maintenance routines, for example. “These low-cost automation tools are not perfect yet, but they are evolving quickly and getting better all the time. Anytime you can take a truck off the road that would be hauling chemicals or produced water, you have reduced cost and risk.”
Durham notes that automation also often improves the cost effectiveness and performance of chemical treatments. “The frequency of treatment schedules and the amount of chemicals can be tailored to the conditions of each well, and continuous automated treatments also can reduce deferred production caused by dips between infrequent batch treatments,” he points out. “It does not take many failures with traditional periodic surveillance to justify moving to an automated system.”
Through continuous improvement, best practices and green chemistry solutions for production and stimulation applications, Apache Corporation and other operators are becoming more cost-effective and more sustainable while optimizing the performance of oil and gas assets.
As hardware and software costs continue to drop, Durham predicts that most wells will be able to be equipped with automated treatment with no additional cost to existing chemical programs. In fact, he says operators will be able to reduce chemical spending in many cases while also enhancing the effectiveness of their treating programs to eliminate common problems that can lead to production downtime.
Automation and connectivity are already the new norm in horizontal resource plays. “These wells cost millions of dollars to drill and complete, so a small incremental investment in chemical automation is an easy decision,” Durham says. “Wells can be remotely treated in batch or with continuous automated injection to optimize production, balancing deferred production with chemical costs.”
Once automated, wells can be monitored remotely in real time and visits scheduled only when a fix or adjustment is required, raising the value of the pumper’s activity and dramatically reducing overall time on the road for field personnel. “It takes only 10-15 seconds per well to tell if everything is aligned and working right,” notes Durham.
Going forward, the ongoing widespread adoption of automated production operations on onshore horizontal wells and the increased affordability of remote monitoring solutions will increasingly encourage the extension of automated chemical delivery capabilities to all producing wells, according to Durham.
“As the industry has seen with other technologies over the years, once the price points decline to a certain level, the benefits clearly begin to outweigh cost considerations and we will see automated chemical treatment become commonplace for even low-volume wells,” he remarks.
Durham cites the handheld calculator as an example. “In 1974, the first calculators cost $150 for a few simple functions. Now those functions and much more are available for free on every mobile phone,” he states, adding that he sees automation and remote monitoring similarly being “built into” chemical pumps, meters and storage systems as well as virtually all other types of production equipment. “For production chemicals, that translates into improved treatment quality, lower cost and reduced well-site risk.”
Completion Fluids
Durham has a unique perspective on completion fluids technology. He helped develop the first fluid systems specifically designed for hydraulic fracturing in the 1970s while working for Amoco. He says those early systems were licensed to service companies and deployed almost exclusively as part of their broader turnkey well completion services. That same model was carried into the early days of the shale boom, with completion services bundling chemicals, pressure pumping horsepower and proppant.
As more companies entered the market, completion services and goods were debundled gradually, giving operators more options and increased pricing transparency, according to Durham. “The market always moves to be more cost-effective. In the case of the hydraulic fracturing market, bidding horsepower, proppant and chemicals separately lowered the cost of everything,” he states. “Many chemical companies got into the fracturing chemistry business when it became debundled, expanding the range of products and services available while simultaneously reducing prices.”
Consequently, operators now are sourcing their own sand and chemicals and hiring pressure pumping horsepower on a service fee basis, he explains. “This approach helps stabilize pricing and leads to operators better understanding the chemical business,” Dunham says. “Oil and gas companies are hiring people from the chemical industry who understand the benefits of different completion fluid formulations and know what the prices should be.”
Unlike the production chemicals market, which is defined by many different types of specialized chemistries usually ordered at relatively small volumes with high service requirements, completion chemicals is a lower service market with fewer products but very high-volume orders. “Rather than complex chemistries, the focus in fracturing fluids is simplified systems with minimal additives, such as slickwater with friction reducers,” notes Durham. “Both the types of fluids and the volumes required make it easier to commoditize fracturing fluids.”
As lateral lengths grow longer, stage counts increase and operators pump more proppant per well, the amount of fluid required goes up, as do pressure and friction. The toe section of a horizontal well generally takes more friction reducer on a concentration basis, with friction decreasing as completion operations progressively work back toward the heel. With laterals routinely extending to 8,000 feet or more, friction reducer concentrations in the toe section now average 1.5 gallons per 1,000 gallons of treated frac fluid volume or higher.
While low-cost slickwater systems with friction reducers are the clear preference for hydraulic fracturing in tight oil and shale gas plays, hybrid treatments that combine slickwater and cross-linked gel systems are proving advantageous in many completion designs to place proppant out in the formation and keep induced fractures propped open, according to Durham. “Typically, cross-linked gels are tailed in to pump a little larger proppant mesh size toward the end of the stage to ensure an efficient, conductive fracture network.”
Although friction reducers and gels historically have come in liquid form, Durham notes that Apache is using solid powdered forms of chemical additives and gels to reduce overall volumes and the number of trucks on the road, and eliminate the use of solvents. “The dry products work just as well as the liquid versions without the solvent toxicity,” he says. “Chemical vendors also are developing powdered versions of scale inhibitors.”
Improving Sustainability
Mirroring the trend toward higher proppant concentrations (some wells are being completed with 2,000 pounds or more of proppant per foot), operators also are pumping larger volumes of fluid per well. Considering the high percentage of fluid ultimately flowed back during the early production phase, Durham notes that operators are implementing recycling systems as a standard best practice to capture, treat and reuse flowback fluids. Moreover, he says Apache and others are also using chemical and mechanical treatment methods to recycle brackish produced water for use in well fracturing, particularly in areas such as the Permian Basin where freshwater supplies are limited.
Sustainability is a major motivator for innovation in completion chemicals, and Durham says it is imperative for operators and chemical manufactures to continue to work cooperatively to engineer green chemistries and implement environmentally friendly best practices for delivering chemical solutions down hole. One example is the American Chemical Society’s Green Chemistry Institute® Hydraulic Fracturing Roundtable, which Durham chairs.
“Member companies work together to develop and disseminate scientific information related to applying green formulations and engineering principles in the chemical supply chain for hydraulic fracturing,” he states. “The goal is to foster more sustainable practices in hydraulic fracturing.”
The biggest risk associated with fracturing chemicals is accidental releases during transportation, Durham adds. “There has been a lot of misinformation about frac fluids down hole, but many of the general public’s concerns about hydraulic fracturing operations really stem from concerns of materials transport, well construction, hydrocarbon production or distribution,” he contends.
Through internal best practices and external initiatives such as the Hydraulic Fracturing Roundtable, Apache is committed toward being more cost-effective and sustainable over time. “The fact is, you can accomplish both simultaneously,” says Durham. “They actually go hand in hand. The less chemical used, the less cost there will be. The greener the chemicals used, the less risk there will be.
“Our continuous improvement process has helped us reduce frac chemical usage and the levels of toxins year over year,” he concludes. “We are working hard to apply green chemistries and reduce the amount of chemicals used in production and fracturing processes, and that makes wells both more profitable and more sustainable.”
For other great articles about exploration, drilling, completions and production, subscribe to The American Oil & Gas Reporter and bookmark www.aogr.com.