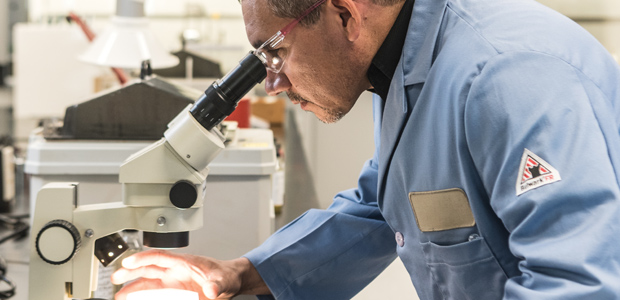
Oil Field Chemistry
Digital Technologies Enable Intelligent, Real-Time Chemical Management
By Paul Gould
THE WOODLANDS, TX.–Chemistry is as fundamental to oil and gas operational success as drill bits and pumpjacks. From drilling mud formulations to stimulation fluid friction reducers, enhanced recovery solvents and flow assurance inhibitors, chemicals are integral to every phase of well life–drilling, cementing, completion, production, treating and even gathering and transportation.
While advancements continue to take place in oil field chemical engineering, including new generations of “green” chemical compounds that are more effective, more economic and more environmentally compatible across a range of applications, one of the biggest areas of technological improvement is the science of optimizing the management of production chemical treatment programs.
New capabilities in chemical management are being enabled by the same digital field, Internet of Things sensing, big data, artificial intelligence, automation, cloud computing and control networks trends that are revolutionizing many other aspects of oil and gas operations, whether they be geophysical analysis or production facility operations. Through the adoption of these intelligent technologies and skill sets, oil and gas producers are able to leverage opportunities to increase efficiencies and operational performance substantially.
This extends to dramatically improving oil field chemical management, which traditionally has been a very hands-on process and has remained essentially unchanged for decades–until now, that is. Digitization is creating powerful new intelligent management solutions that give producers the ability to manage their producing assets smarter and more efficiently, cut costs and enhance field productivity by optimizing chemistry programs.
And it all can be accomplished remotely, mitigating exposure to potential hazards associated with well site tasks. Predictive capabilities and data analysis also can be accelerated, with software front ends (i.e., “dashboards”) delivering usable, real-time information and analysis to field technicians, production engineers, department managers, and service and supply partners all along the chemical supply chain.
Production Chemicals
Production chemicals are specialty formulations that are used in comparatively small volumes and serve very precise purposes, such as inhibiting the formation of scales, corrosion or hydrates and paraffins. Inhibitors injected into the well to prevent mineral scale deposition on downhole casing, tubing and other equipment are among the most common production chemicals. Inhibitors that suppress the formation of gas hydrates and waxy or asphalt-like deposits are injected for similar reasons, keeping the well and its fluids free from materials that could hinder recovery.
Despite its proportionally small expense, a chemical program can have a significant impact on the performance and profitability of producing wells. In the field, intelligent chemical management technology is reducing risk, increasing uptime and optimizing economics. In the lab, near real-time analytical data are offering new insights into the performance of chemical maintenance programs. In management and accounting offices, the technology enables new levels of control over all aspects of chemical servicing, supply and billing.
Corrosion inhibitors reduce the effects that flow-stimulating acids may have on downhole equipment and aboveground components, while oxygen scavengers serve to mitigate corrosion in water injection equipment. Other important production chemicals include demulsifiers, clarifiers, foamers, defoamers and biocides. Enhanced oil recovery chemicals and well service additives can be used to improve flowback and extraction from mature reserves and difficult formations.
The mix of chemicals applied usually is designed specifically for each field and well, and the mixes are used either in larger batches for single interventions, small regular batch additions, or are continuously dosed. As the volume of produced fluid and other operating conditions change, the selection and amount of chemicals used must be adjusted accordingly, and well conditions must be monitored closely in order to assure optimal flow.
When compared with other economic factors, oil field chemicals and related services make up only a very small part of total lifting costs. In fact, according to industry estimates, the cost of chemicals and chemical services averages from $0.20 to $0.40 per lifted barrel, depending on the field.
Despite their proportionally small expense, however, oil field chemicals can have a very large impact on costs and profitability when their supply and application are not optimized. Failure to treat wells efficiently against corrosion or hydrate blockage, for example, can result in periods of downtime that cause substantial loss of revenue as well as unnecessary repair and workover expenses that can erode profit margins.
Even when not leading to outages, the small decreases in flow rate caused by scale, wax or other deposits can translate into large losses of produced fluid over time, which ultimately may determine the viability of operations. Insufficient chemical management and supervision also can lead to malfunctions, leaks and spills that result in environmental or contractual fines.
The various associated activities involved in chemical management also have the potential to add up if not executed in the most efficient manner, especially in large fields. This can apply to the long “windshield” hours that chemical truck drivers and field technicians spend behind the wheel on service rounds, but also applies to many other routine activities such as documenting deliveries on paper or computer spreadsheets, or processing orders and invoices at the office.
If they want to remain viable, chemical service companies have no choice but to pass on such costs to customers. In addition, the potential risks for staff and the environment inherent in the logistics of supplying a large network of wells with chemicals, as well as the manual labor involved in injecting or restocking them, can increase with each visit to a site.
Measuring Success
For oil and gas producers, the complexity of chemical maintenance and order fulfilment results in the need for highly competent personnel trained to constantly monitor and verify the performance of chemical services. Lack of visibility into these services not only can give rise to trust issues that stand in the way of fruitful partnerships with chemical service providers, but also makes it harder for field managers to measure the success of chemical programs.
Given the challenges, decision makers in oil field chemicals management are looking to innovation and technology to improve efficiencies and economics. Using low-cost sensors, big data analytics, cloud computing and other technologies, companies increasingly are adopting innovations that range from digital fleet management and predictive maintenance to production enhancements.
The International Energy Agency estimates that oil and gas companies could lower their production costs by 10-20 percent simply by making more widespread use of the digital technologies already in existence. The IEA bases this projection on assessments shared by upstream operators and service providers, and sees potential for even bigger cost reductions if technologies that only now are emerging (especially those enhancing connectivity and monitoring) prove effective and find general acceptance.
The benefits of digitalization are already clear across various aspects of upstream oil and gas operations. However, oil and gas producers trying to resolve a multitude of interconnecting issues across the value chain by investing in a digital alternative that provides better efficiency, control and transparency, often are faced with a perplexing myriad of separate hardware and software solutions that are difficult to integrate into existing systems. The traditional approach of selectively adopting a set of technologies and unsystematically implementing digitalization is neither technically nor economically suitable for most operators, particularly smaller independents.
Intelligent Solution
The solution for these companies is intelligent chemical management technology that gives oil and gas producers unparalleled connectivity to their fields while automating the entire chemical process–from injection to inventory restocking and production performance analysis–in a fully digital workflow. But it goes beyond chemical programs by integrating the intelligent management hardware and software with smartphone and IoT technology to create a holistic system that helps digitize and optimize all field production processes.
By integrating all essential elements of production surveillance, field processes, control and analysis into a fully digitized intelligent system, the technology optimizes processes at every level of oil field chemical management, significantly reduces total operating costs, and substantially decreases production risks caused by breaks in chemical dosing. Incorporating more than 600 processes, a comprehensive system has been demonstrated to reduce well failures and increase total oil field performance by up to 15 percent.
The system is used to schedule, monitor and report all aspects of chemical services. This includes the scheduling and performing of well site deliveries and the posting of analytical tests, in addition to multiple other types of reporting. To fulfil its many tasks, the system uses sensors and telemetry equipment installed at the well in combination with highly sophisticated software for data entry, processing and distribution, which can be accessed using smartphones and other cloud-connected devices. The security of the cloud-stored data is managed by a third-party service provider to safeguard against cyberrisks.
Chemical service and field technicians are equipped with smartphones and other mobile devices that help manage job lists and activities. When chemical deliveries are made or services performed, the smartphone records date, time, GPS position and user identification, as well as details about the treatment and associated metadata such as the well’s API number. For each site visited, metering devices on delivery trucks measure the exact amount of chemicals delivered.
This information is saved and added to the delivery record for verification purposes, and also provides the field operator the respective invoices. In the past, all these activities had to be performed manually using paper and spreadsheets, which increased the risk of errors and missed deliveries.
Chemical tanks used for continuously dosing wells are fitted with special sensors so the system can monitor their inventory levels. As the tank empties, the system automatically places orders for replenishment and generates the corresponding invoices. All chemical deliveries, including batch deliveries injected into pipelines or dosing points, are scheduled automatically by the system, which continually calculates the most efficient job lists and itineraries. Alerts can be configured individually and interact intelligently with the recipient.
Dosing pumps also can be operated remotely by controllers through the system’s Web interface. Besides chemical needs, the system also manages service requirements such as pump repair and calibration. Real-time remote control and pump monitoring enable constant monitoring of chemical dosing pump health and of charts that accurately correlate the chemical program with other production data.
Sending updated information every five minutes to the cloud, customers can access data in real time over an intuitive Web browser specifically developed for chemical management. The system also integrates the analytical testing performed on well fluids in order to determine the need for chemical adaptations and anticipate potential well failures.
Field technicians attach a bar code to each sample they take at a wellhead, pipeline or oil and gas separator, and enter the sample into the system by scanning the code and other data such as photos or comments. Samples then are tracked to the laboratory, with test results and analyzable reports made available to both technicians and customers using the intuitive dashboard interface.
Increased Production
By digitizing the entire delivery and monitoring of chemical management programs, the intelligent system is able to tangibly provide operators with increased levels of consistent production through increased uptime, while also reducing maintenance costs and lowering overall risk.
The comprehensive real-time and near-real-time reporting the system provides gives oil and gas producers an unparalleled level of transparency into all the daily field operations that are carried out on their assets, directly and unfiltered from the IoT devices and digitized processes. Formerly, this information was made available only through manually prepared reporting provided on a weekly or monthly basis.
Easier monitoring also reduces the risk of leaks and spills, and the potential environmental, regulatory and contractual consequences they can have.
As part of the digital solution, an intelligent risk management system also has been developed that focuses on the needs of offshore operations. Logging incoming data and processing them through a series of key performance indicator evaluations in real time, the risk management solution provides a comprehensive and immediate overview of the risk profile for subsea wells, chemical handling facilities and export trains. This frees skilled personnel to focus on problem resolution and optimizing operations rather than collecting data.
Digital transformation is changing the way industries operate on a scale comparable to major industrial revolutions of the past, and it has tremendous potential to benefit the oil and gas industry. To unlock its full value, however, companies need to work with experienced and trusted partners with proven digital solutions that can be integrated as totally new systems or added onto already installed digital equipment.
In the field, intelligent chemical management technology is providing new levels of monitoring and transparency. The system reduces risks and increases uptime while minimizing the economic and environmental hazards associated with leaks, blockages and equipment malfunctions.
In the laboratory, it is providing near-real-time analytical data and production histories that offer unprecedented insight into the effectiveness of chemical maintenance programs. In management and accounting offices, the solution affords a new level of control over all aspects of chemical servicing, supply and billing that puts chemical service provider/oil and gas company client relations on a more transparent, mutually profitable basis.
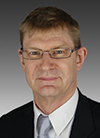
PAUL GOULD is global head of digital strategy at Clariant Corp. Throughout his 30-year career, he has been responsible for designing and implementing complete industrial automation systems, specializing in chemical systems to optimize the performance of continuous production and water treatment processes. Gould’s expertise includes implementing cloud, edge, automation, networking, predictive analytics and expert systems to create technological solutions such as Clariant’s fully digital VERITRAX™ intelligent chemical management system.
For other great articles about exploration, drilling, completions and production, subscribe to The American Oil & Gas Reporter and bookmark www.aogr.com.