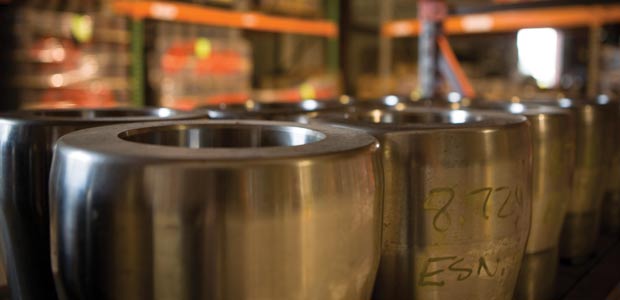
Evolution Of Expandable Tubulars Solidify Isolation Solutions
By Greg Noel And Jerry Fritsch
HOUSTON–Novel and unique installations of solid expandable tubulars illustrate how the technology can minimize the risk and maximize the efficiency of operations. Significant enhancements and the fundamental adaptability of the technology further solidify expandables as a viable solution for isolation challenges.
Successfully isolating zones is imperative for most drilling projects, whether to mitigate problematic areas while drilling or to enable production from selected formations. The quandary lies in selecting the best solution for the particular formation characteristics and defined objective.
The most equitable answer may lie in utilizing enhanced technology, applying different processes, or a combination of both. Technology, systems and procedures, such as expandable pipe, swellable elastomers, hydrajet perforating, and fracturing methods attest to the benefits of more efficient means of zonal isolation.
Solid expandable tubulars have evolved to effectively address reliability, increase their realm of application, and facilitate ease of use and operations. Notable refinements include a more compact launcher (the chamber housing the cone during deployment), improved and more drillable launcher shoe, and flapper-style floats. Connections have attained higher torque capacity, better seal engagement, and improved protection from physical damage during deployment.
A high-performance solid expandable system also employs thicker-wall tubulars to improve pipe properties for applications requiring a more robust system.
Expandable systems provide an efficient means to isolate trouble zones and preserve hole size when well-bore tapering hinders completion. Operators have maintained casing points when pore pressure/fracture gradient issues, sidetrack operations, and loss of circulation jeopardize or compromise adequate hole size at total depth.
Older wells often experience casing leaks with long-term exposure to shallow corrosive waters or saltwater flows. Complete sections of the casing can become so thin that mechanical integrity is lost. Expandables used to repair the casing have extended the life of these wells without compromising the necessary hole size.
The success of these elemental applications continually motivates companies to go beyond using expandables as enabling tools to including them as dynamic solutions.
Attaining Isolation
An operator with a drilling campaign in Robertson County, Tx., authorized solid expandable technology to optimize its well bore. By doing this, the company realized a 20 percent savings on overall well construction costs, which equated to a massive step change in the field development cost and overall project economics.
In an ongoing effort for continual improvement, the company assessed options to reduce rig days on the wells. Considering the hard rock in which the wells were drilled, the opportunity existed to apply swellable elastomer technology to attain zonal isolation in the area of the well bore where a solid expandable liner had been used.
The initial well bore design called for installing the solid expandable liner over a lost-circulation zone to accommodate the higher fluid density required to drill to the reservoir below. The design required under-reaming the hole to 71⁄2 inches for an adequate annular area to place the cement to isolate the lost-circulation zone. Under-reaming and cementing operations averaged between five and seven days a well.
The well bore logs revealed reasonable gauge hole just below the loss zone, which led to redesigning the solid expandable liner to an optimum size, and positioned swellable elastomers immediately above the shoe of the expandable liner (Figure 1). A conventional liner hanger (anchor), run at the top of the solid expandable liner, would seal in the 75⁄8-inch base casing.
The operator ran a 6- by 75⁄8-inch open-hole liner and set the expandable elastomer anchor with swellable elastomers (the shoe of the expandable system) in a competent shale formation. An oil-based pill pumped and displaced around the shoe activated the swellable elastomers.
As the expansion progressed, the swellable elastomers compressed into the formation just above the solid expandable liner shoe. The remainder of the liner was expanded, compressing the standard elastomers on the liner hanger, enabling the liner to be successfully pressure tested.
Following drill-out of the liner shoe, a successful shoe test conducted to 16 parts-per-gallon equivalent mud weight indicated the compressed swellable elastomers effectively had provided a seal and isolated the loss zone behind the solid expandable liner.
Planning and implementing the use of solid expandable liners with swellable elastomers eliminated the need to under-ream the hole and cement the liner. The value of eliminating these two operations was a reduction of five to seven rig days, which translates to $300,000. With the success of the initial application, this operator has continued to use this isolation design.
Extending The Shoe
An operator in the Gulf of Mexico leveraged existing infrastructure and sidetracked through both 133⁄8- and 117⁄8-inch casing. After setting 95⁄8-inch casing, the shoe was extended using solid expandable tubulars with swellable elastomers, enabling access to deep Shelf target zones with adequate hole size.
Reaching the potential pay intervals, which were located below an existing field development, required addressing a high-pressure/high temperature environment where the bottom hole static temperature exceeded 325 degrees Fahrenheit and the well bore experienced pore pressure of 19,000 psi.
A 75⁄8- by 95⁄8-inch solid expandable, open-hole liner–a record 6,935 feet long–was installed and anchored to the 95⁄8-inch casing (Figure 2). This system featured an expandable, open-hole isolation anchor with swellable elastomers (to ensure a successful leak-off test). Five water-activated, swellable elastomer seals located on the expandable anchor directly above the shoe achieved immediate compression against the formation as the liner was expanded.
The swellable elastomers ensured a successful leak-off test, which eliminated the need for remedial shoe squeeze operations. This design approach resulted in substantial savings and facilitated discovery of a 150-foot deep natural gas pay zone.
Isolating Gas In Oil Wells
Water cut in barefoot completion wells can be reduced by deterring a water-producing interval with a solid expandable system. The same principal applies to oil wells where gas is breaking through.
For a major operator in the Middle East, the challenge often occurs when intermediate casing is set short of planned depth and fails to isolate the potential gas production zone. To address this challenge, the operator used the elastomer/solid expandable system combination to extend the casing shoe beyond the zone of concern.
Since the required length often is short and the hole has not been enlarged, the low cement volume leads to higher probability of poor isolation. The solution is running an open-hole liner with swellable or regular elastomeric seals to isolate the formation in the open hole.
Frac Placement Value
A multizone isolation completion system provides a means to obtain a discrete set of separated fractures along the entire length of a horizontal well bore to precisely control fracture placement. Some multizone isolation completion systems include perforation and plug systems run in a cased well bore.
Before swellables, inflatable packers with mechanical-shifted sliding sleeves were used for isolation, as well as to provide a frac and then production flow path. These systems typically require multiple trips in and out of the well bore, and tie up both rig and frac equipment, adding to higher project economics.
In the past few years, an assortment of single-trip, multiple-zone isolation completion systems (i.e., modified production packers coupled with ball-actuated frac sleeves) have been developed. With these systems, the rig creates the well bore, installs the completion, and then is freed to move to the next well. This approach allows the perf and frac operations to be performed without the rig, significantly enhancing project economics.
More recently, the application of a solid expandable system realized another step in adding value and further bolstered project economics. In conjunction with an operator in Canada, two solid expandable liners utilized multiple swellable elastomer sections (Figure 3). When each liner reached total depth, displaced fluid activated the swellable elastomers. The liners then were expanded and the swellable elastomers compressed between the liner and the formation.
The advantage of running swellable elastomers on solid expandable tubulars is the immediate seal gained by compression (as opposed to several days of waiting for elastomers to swell). The swelling of the elastomer over time serves as a backup seal if an irregular well bore internal diameter is encountered.
With the liner expanded, the operator had a well bore across the reservoir with a 5.4-inch ID to fracture through versus the prior conventional design with only a 3.8-inch ID. The increased inside diameter across the completion allowed use of a larger coiled tubing-conveyed hydraulic jet perforating assembly and the frac fluid was able to be pumped down the CT/casing annulus at rates higher than could be attained with the former design.
Pinpoint Perforating
Another advantage in the Canadian job included the ability to accomplish pinpoint perforating at any location between the swellable elastomers because there was no limitation dictated by a previously installed shifting sleeve, etc. Fracs pumped between each of the swellable elastomers on the liner had a distinct pressure profile, indicating that the swellable elastomers had provided a complete seal/isolation with the formation.
After the final frac was pumped and the well bore reversed out to total depth, considerable value was realized because nothing remained in the well bore to drill out. When the coiled tubing was retrieved, the full 5.4-inch ID liner was across the reservoir, fully perforated and all stimulations complete.
This solid expandable solution had no mechanical complexity associated with packers and sleeves, and no cementing operations–virtually eliminating operational risk. The solid expandable liner provided the largest possible well bore across the reservoir to accommodate maximum frac rates and attaining maximum frac volumes, all with less surface horsepower.
Because this system has no reduced ID or restrictions for re-entry/intervention, it provides the largest full-bore flush ID. With solid expandable systems that employ swellable seals, there also are no limits to the number of zones or intervals that can be isolated and individually perforated and fractured within a well bore. The swellable seal elements allowed the elastomers to be positioned anywhere along the expandable liner.
Combining solid expandable liners with swellable elastomers for isolation, hydraulic jet perforating on coiled tubing, and fracturing down the CT/casing annulus, plus the bonus of nothing left in the well bore to drill out, significantly enhanced project economics and added unquestionable value to the operator.
Covering Faults
An independent operator increased oil production after installing a solid expandable system in a waterflood injector well that was losing water into a depleted zone. The operator needed to isolate the thief zone and preserve hole diameter in the open-hole, horizontal water injection well to restore lost production from a nearby oil well. The well had been converted to a 61⁄8-inch horizontal barefoot water injector nearly a decade earlier. Acid gel stimulation resulted in direct communication with the neighboring well, reducing oil production by 90 percent.
Installation accuracy was very important. Multiple water flow/caliper logs had identified a specific thief zone at 6,168 feet, which was taking about 75 percent of injected water. Installing an expandable liner across the interval and isolating the depleted zone increased the amount of water going into the productive zones, thus increasing production and eliminating noncontributing injection into the depleted zone.
Maintaining adequate hole size throughout the well bore is critical to maintaining viability. Too often, the inevitability of zonal isolation comes at the expense of the “right-size” hole. Whether a solution requires isolating zones in the open hole or cased hole, the objective remains fundamentally similar: seal off a particular area to continue operations and achieve a viable well.
Expandable technology has evolved from a last-ditch answer for deepwater issues into a front-line solution for many common land and offshore wells. The “planned-in” approach enables a proactive design rather than reactionary installation. Asset managers are able to create higher net present values and higher returns on investment by combining solid expandable systems with advanced drilling, completion and production techniques.
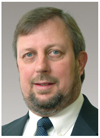
GREG NOEL manages product development and commercialization for Enventure Global Technology. He has 25 years of experience in the oil and gas industry. He joined the company in 1999 from Halliburton Energy Services, where he spent time as an engineer in the surface equipment design group and as a field operations engineer. Noel is a member of the Society of Petroleum Engineers and the American Association of Drilling Engineers. He earned his mechanical engineering degree from Texas A&M University.
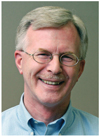
JERRY FRITSCH is the global solutions manager for Enventure Global Technology, where he oversees a staff of engineers that helps analyze and propose solutions for operators using solid expandables. Additionally, his group provides SET® application engineering, reliability analysis, and operations and sales support. Fritsch has 35 years of engineering and operations management background. With a career focus on well construction and operations, he has worked in the Gulf of Mexico, Rocky Mountains, West Coast, Alaska North Slope and U.K. North Sea. Fritsch earned a B.S. in mechanical engineering from LeTourneau University.
For other great articles about exploration, drilling, completions and production, subscribe to The American Oil & Gas Reporter and bookmark www.aogr.com.