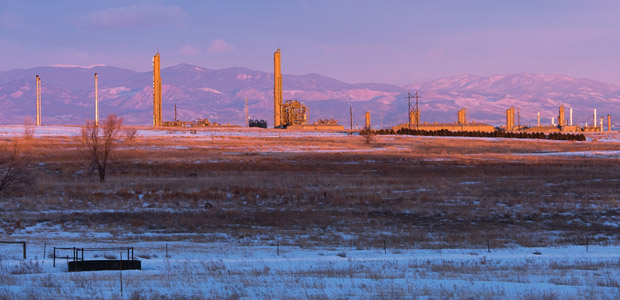
NGL Recovery
Flexible Dual-Train Design Maximizes Processing Flexibility At Anadarko’s Lancaster Plant
By Steven M. Hummell, J. Pat McCann, Joe T. Lynch and Michael C. Pierce
DENVER–Western Gas Partners LP’s Lancaster facility in the Denver-Julesburg Basin was fully commissioned in mid-2015 with two “dual-mode” gas processing trains, each with a capacity of 300 million cubic feet a day. The dual-mode trains are designed to provide maximum operating flexibility, allowing very high ethane recovery when desired, but also maintaining very high propane recovery when ethane rejection is more economical.
This rich-gas process design is based on advanced Single Column Overhead Recycle (SCORE) and Supplemental Rectification with Compression (SRC) licensed process technologies. Since commissioning, operation has been primarily in the ethane rejection mode, with significant positive revenue results achieved by rejecting 99 percent of the ethane to the residue gas stream while maintaining 99 percent propane recovery. In addition, the processing uses significantly less compression horsepower than would be required with an “open-art” plant design.
Western Gas, a publicly traded midstream limited partnership controlled by Anadarko Petroleum Corporation, began the process of designing and constructing a new facility in northern Colorado to process Anadarko’s and available third-party gas in 2011, when ethane recovery was economically favorable, although take-away capacity was limited. Weld County was an ideal location for a new plant, considering Anadarko holds significant producing acreage in the area, and there are nearby pipelines and good access for transporting equipment. The original design called for one 200 MMcf/d train, but quickly grew to two 300 MMcf/d gas processing trains in response to rapid ongoing field development.
Residue gas take-away capacity was available on Kinder Morgan’s Colorado Interstate Gas and High Plains pipelines, flowing either north to Wyoming or south to Denver. However, local natural gas liquids take-away capacity was limited. DCP Midstream was in a similar position, and formed a partnership with Anadarko and Enterprise Products Partners to build the Front Range NGL pipeline with a connection to the Lancaster plant. Front Range would allow Y-grade NGL products to flow to Skellytown, Tx., connecting to the Texas Express Pipeline that delivers to the Mont Belvieu market hub.
Since the Front Range Pipeline could accept all types of NGL products, operational gas processing flexibility for the new facility would be valuable. Subsequent to the NGL transportation projects’ completion, Anadarko dropped its interests in the Front Range and Texas Express Pipeline to Western Gas Partners. Western Gas’s goal was to build a state-of-the-art facility that could achieve high product recoveries and have the flexibility to respond to changes in delivery options and the NGL market. The product specifications are summarized in Table 1. The requirements follow a typical Y-grade specification, restricting maximum content of methane, methane-in-ethane, carbon dioxide-in-ethane, and hydrogen sulfide. When rejecting ethane, the only NGL content concern is the sulfur compounds. However, the residue gas specifications mandate a maximum heating value (which can be a concern when rejecting ethane) and a maximum CO2 content.
Facility Engineering Options
Historically, gas processing plants in North America have not been optimized to reject ethane while maintaining maximum propane recovery. Plants generally have been sized with an emphasis on ethane recovery, operating at lower throughput and relatively low propane recovery levels in ethane-rejection mode. This is an acceptable approach when the primary goal is to recover ethane and rejection capability is a secondary consideration.
The gas subcooled process (GSP) design is the standard for North American NGL recovery plants. Figures 1A and 1B show the GSP design for ethane rejection and recovery, respectively. For the Lancaster plant’s rich gas design basis, the maximum propane recovery for an open-art GSP would be approximately 90 percent when rejecting almost all the ethane, even when using all the horsepower required for the ethane recovery mode operation. This performance level was not sufficient for the Lancaster project.
GSP is effective at providing moderately high ethane recovery, but has significant limitations for ethane rejection operation. In particular, it is difficult to minimize the propane lost to the residue gas stream. One option for improving the top reflux composition is Ortloff’s Recycle Split-Vapor (RSV) technology. In this design, a small stream of compressed residue gas is cooled and flashed to the top of the column, theoretically allowing close to 100 percent propane recovery while rejecting ethane. Although it requires a taller column, additional exchanger passes and additional residue gas compression, RSV can offer flexibility and high product recoveries. It was evaluated as an option for the Lancaster project, but rejected because of the high compression power requirements for ethane rejection mode.
SCORE technology offered a significantly more efficient ethane rejection process (Figure 2). SCORE is widely deployed internationally for single-mode propane recovery plants, but not in North America, where ethane recovery has been a higher priority. It uses a side-draw vapor stream withdrawn from the column to provide reflux to both the upper and lower sections of the column.
A SCORE column’ size is similar to that of a GSP column sized for ethane rejection, but the reflux system requires a reflux accumulator and a set of cold reflux pumps. However, the residue compression requirement is reduced significantly by the high column operating pressure, while still allowing the reflux stream to be condensed. For the Lancaster project, SCORE was calculated to achieve 99.5 percent propane recovery using 10 percent less horsepower than GSP at the 90 percent propane recovery level, and 40 percent less horsepower than RSV at a 99.4 percent propane recovery level.
Figures 3A and 3B show the supplemental rectification with compression process for both ethane rejection and recovery, respectively. Like SCORE, SRC utilizes a side-draw vapor stream from the column, but it also uses a cold compressor to pressurize the stream, eliminating the reflux accumulator and cold pumps required for SCORE. This arrangement has cost-saving advantages for modularization. In ethane rejection mode, the performance is similar to SCORE. The size and cost of a column for an SRC design is similar to that of an RSV column, but both are taller than a SCORE-only column. The results of the four design options for full ethane rejection are summarized in the top of Table 2.
Ethane Recovery Flexibility
The GSP, RSV and SRC designs also were considered for full ethane recovery mode operations for the Lancaster rich-gas design basis. The bottom of Table 2 summarizes the maximum ethane recovery mode results for the three process design options. Each design had similar refrigeration and front-end exchanger arrangements, so the process design reflux system performance alone was the dominant factor in the overall recovery-versus-horsepower results.
A GSP design could achieve 95.4 percent ethane recovery at 99.7 percent propane recovery with enough residue and refrigeration horsepower. This recovery level required 16,000 horsepower of residue compression and 6,580 HP of propane refrigeration, for a total of 22,580 HP for each 300 MMcf/d train. This became the base line for comparing process design options.
An RSV design could achieve 98.9 percent ethane recovery and 100 percent propane recovery using 23,430 HP. The SRC process could achieve 99.0 percent ethane recovery and 100 percent propane recovery at 23,350 total (residue, refrigeration and SRC compression) HP.
The RSV and SRC designs add a packed bed above the GSP reflux feed to the column. Below the GSP reflux feed nozzle, the columns are very similar for all three designs. If the RSV or SRC top feeds are reduced to zero flow for any reason, the column operates as a GSP column and the top bed is passive.
Because of the way the reflux system operates, SCORE is best suited for full ethane rejection operation. However, a SCORE design also can be operated in an “incidental ethane recovery mode” in which the reboiler heat is significantly reduced from what is required to meet the normal ethane/propane ratio at full rejection, allowing some ethane recovery in the bottoms product. The heat can be reduced until the amount of methane in the bottoms product approaches the pipeline product limit.
For most SCORE designs the incidental recovery level is usually slightly more than 30 percent ethane recovery. However, it is possible to keep the propane recovery very high, even when approaching the methane content limit. In addition, this very high propane recovery can be achieved at much lower compression power than a GSP design, which will still have significant propane losses at 30 percent ethane recovery.
Preferred Process Designs
Figure 4 shows how propane recovery changes as a function of the ethane recovery level over the full range of possible ethane recovery levels for GSP, SCORE and SRC designs with the residue compression power limited to 16,000 HP (the maximum required for 95 percent ethane recovery using GSP) and refrigeration compression limited to 7,000 HP. At 30 percent ethane recovery, the propane recovery for a GSP design falls to approximately 95 percent for the Lancaster design basis. In contrast, the propane recovery for SCORE and SRC is more than 99 percent. This equates to 35,000 gallons of propane a day for each train.
The triangular-shaped area between the GSP line and the SRC/SCORE line illustrates what is given up in propane recovery when a GSP design is used for partial ethane rejection. As expected, the largest difference is at full ethane rejection at the left end of the graph, but there is a notable difference in propane recovery at the graph’s right end.
Also important is the difference in compression power for these three process designs. The total compression horsepower numbers have been added to the graph for full ethane rejection and 30 percent recovery to indicate the savings that can be achieved when using a more effective SCORE or SRC process.
From full ethane rejection to 30 percent ethane recovery, SCORE or SRC were the preferred process designs with much higher propane recovery than GSP. At similar total horsepower requirements, SRC propane recovery was 99.4 percent at 30 percent ethane recovery and 100 percent at 99 percent ethane recovery, compared with 95.1 percent at 30 percent ethane recovery and 99.7 percent at 95.4 percent ethane recovery for GSP.
Table 3 shows the final options and performance data for the Lancaster design basis. It was obvious that an efficient propane recovery process design should be selected for the low ethane recovery end of the operating envelope, but options for the high end of the ethane recovery range also needed to be considered.
Final Lancaster Design
Based on the options developed specifically for the Lancaster application, the final physical plant for the two trains combines SCORE and GSP designs. A SCORE design was selected for full rejection mode and incidental ethane recovery, and SRC was selected for the future full ethane recovery mode. Western Gas decided to defer the SRC compressor purchase to save on capital costs. In the interim, it opted to operate in GSP mode for ethane recovery above 30 percent until the SRC compressor could be justified by ethane/propane product pricing. All equipment was specified and designed for future SRC mode operation, including the demethanizer column with a packed section above the GSP feed.
Both trains include the equipment necessary to easily upgrade to SRC for maximum ethane recovery in the future. The column has fractionation stages optimized for full rejection, and diameters sized for both operating modes at the full inlet gas rate of 300 MMcf/d per train.
Variable-speed electric motor drives were selected for the residue and refrigeration compression to better accommodate the 100 psi difference in column operating pressure between the optimized recovery and rejection modes and changes in the refrigeration loads. This allows Western Gas to take full advantage of the lower compression power when operating between full rejection and 30 percent ethane recovery.
The CO2 removal requirements shift with the ethane recovery level. CO2 freeze is not a concern in full rejection mode, but is limiting during ethane recovery because of the much colder temperatures. Two 50 percent amine units were specified for each train. While H2S must be removed for both modes of operation, not all of the CO2 must be removed while rejecting ethane.
Operating History
The first train at the Lancaster facility was ready for commissioning in April 2014. The amine treaters were tested first for CO2 removal. The removal performance was adequate, although there were control loop tuning issues typical of new facilities. This was a particular concern, since the inlet gas was very close to the hydrocarbon and water dew points. Erratic control led to foaming and liquid carry-over, resulting in contamination of the molecular sieve dehydration media, and ultimately, premature replacement of the dehydration unit’s media. This continues to be a concern that requires close monitoring to prevent amine unit upsets that can result in amine foaming and carry-over to downstream equipment.
After the amine treater commissioning was complete, the molecular sieve dehydrator beds were brought on line using a closed-loop gas flow through the beds with the dehydration unit’s regeneration gas compressor. After each of the three beds went through a sufficient number of regeneration heating cycles and the bed switching schedules were adjusted, dry gas then was directed into the NGL recovery unit.
A closed-loop gas flow procedure through the NGL recovery unit minimized dry-out time. One of the residue compressors was used to circulate gas through the dehydrator beds (which continued to go through their normal regeneration cycles), then through all the cryogenic unit’s paths, and finally back to compressor suction. During this procedure, pressure drop through the NGL unit was minimized with a bypass control valve upstream of the cold exchangers, rather than controlling flow with the Joule-Thompson valve, to minimize cooling.
Circulation of the lower-pressure dry gas through the unit was limited to approximately 30 percent of design flow to minimize additional expansion cooling. Using this procedure, the dry-out gas temperature was kept relatively warm by also using the residue compressor discharge cooler controls.
Western Gas Partners LP’s Lancaster facility in the Denver-Julesburg Basin was commissioned in two phases in 2014 and 2015 to process gas produced by Anadarko Petroleum Corporation as well as other operators in the region. The plant’s two 300 MMcf/d “dual-mode” processing trains are designed to provide maximum operating flexibility to enable very high ethane recovery or reject 99 percent of the ethane while maintaining 99 percent propane recovery.
As noted, the SCORE design includes a cold reflux accumulator, cold reflux pumps, and a condenser that operates at column pressure. Because the reflux generation system is outside the normal residue gas flow path, it was difficult to force adequate dry-out gas flow through this section without specific dry-out gas tie-in points. This was a problem for the first train at Lancaster, and improvements were made on the second train.
Train 1 was operated in GSP mode for the first year, processing inlet gas with a heating value greater than 1,300 Btu/cubic foot (7.0 gallons/Mcf), much higher than the 1,265 Btu/cubic foot (6.5 gallons/Mcf) design. Ethane recovery during that time was 93 percent and propane recovery was >99 percent. Train 1 was shut down briefly after the second train was commissioned to replace the dehydration molecular sieve and to perform a more complete dry-out of the reflux system, then was restarted in SCORE mode.
Commissioning of the second train in June 2015 generally was smoother because of the lessons learned on train 1. This was particularly true for the control systems, and especially the level control loops. This allowed a quick startup and subsequent increase in the daily inlet flow rate from 200 MMcf to more than 300 MMcf in only a few days. Train 2 generally has operated in SCORE mode from the start, although there have been brief periods when it was in incidental ethane recovery operation.
Key Consideration
At the time the Lancaster plant was conceived, ethane and propane recovery margins were consistently favorable. Since then, however, low prices have made ethane margins negative. The facility’s ability to reject ethane is an excellent example of why flexibility should be a key consideration when designing an NGL recovery plant.
With low ethane prices, both Lancaster trains initially operated in full rejection mode, each processing as much as 325 MMcf/d of feed gas with propane recovery typically greater than 99 percent. However, when the Front Range Pipeline requested Western Gas recover approximately 25 percent of the ethane to fulfill market orders, the flexibility of the process allowed that commitment to be met easily by operating both trains in incidental ethane recovery mode without reducing propane recovery.
All startup and operational issues have been addressed, and the operation of both plants is smooth and reliable. Anadarko and Western Gas are in the process of consolidating operations of other nearby facilities into the Lancaster facility’s control room, maximizing the entire complex’s value.
Overall, the performance of the Lancaster facility has been exceptional. Despite a richer-than-expected feed gas composition, product recoveries are better than designed. The facility’s flexibility has been the key to maximizing profits, enabling ultrahigh propane recovery to be maintained at minimum compression power levels even when some ethane must be recovered. This capability is what differentiates the Lancaster plant.
Uncertainty in product pricing makes efficient long-term operation in ethane rejection mode more important than ever, providing the operating flexibility needed to meet varying market conditions. Reduced emissions, electrical costs and installed compression capital cost favor more efficient process designs. It is now possible to build new plants, such as the two trains at Western Gas’s Lancaster Facility, capable of high recovery dual-mode operation at minimal additional cost.
STEVEN M. HUMMELL is process engineering manager at Anadarko Petroleum Corporation in Denver, where he supports the company’s midstream assets. Before joining Anadarko in 2011, Hummell worked 23 years as a process/project engineering adviser at El Paso Corp. and its affiliate companies. He holds a B.S. in chemical engineering from Kansas State University.
J. PAT MCCANN is manager of the midstream operations services group supporting facility design and operations for Anadarko Petroleum Corporation’s onshore developments. Before joining Anadarko, McCann worked in gas processing and facility operation and design for several companies, including Amoco, Ortloff and Mitchell Energy. The bulk of his career was spent with Hess as manager of gas plants and global process engineering adviser in Hess Corporation’s major project group. McCann holds a B.S. in chemical and petroleum refining from the Colorado School of Mines.
JOE T. LYNCH is a principal/gas processing licensing manager at Midland, Tx.-based Ortloff Technology Group LLC, which holds the licenses on the proprietary SCORE, SRC, GSP and RSV processes. With more than 40 years of gas processing experience, he has completed the process designs on dozens of projects using Ortloff technologies. Lynch has extensive experience in training operators, starting up processing plants, troubleshooting, managing plants, and evaluating process performance. He holds a B.S. in engineering science and an M.S. in engineering mechanics from the University of Texas at Austin.
MICHAEL C. PIERCE is a senior consulting engineer at Ortloff Technology Group LLC. He has more than 20 years of experience in cryogenic process design and development for liquids recovery from natural gas. Current responsibilities include process simulation and optimization of new and existing gas plants, equipment design, hazards review, and plant startup assistance. Pierce began his career as a process control systems and facilities engineer at Shell Oil Company and then ARCO before joining Ortloff. He holds a B.S. in chemical engineering and petroleum refining and a B.S. in mathematics/computer science from Colorado School of Mines.
For other great articles about exploration, drilling, completions and production, subscribe to The American Oil & Gas Reporter and bookmark www.aogr.com.