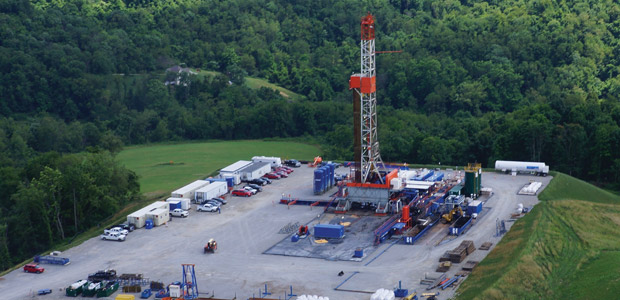
Pad Drilling
Leading Operators Improve Efficiency And Effectiveness Of Multiwell Pad Operations
By Al Pickett, Special Correspondent
As unconventional play drilling activity has ramped up, so has multiwell pad drilling as companies strive to reduce the cost and time of operations. But it is not as simple as merely skidding a rig over a few feet and drilling another lateral.
What is the optimum well spacing and number of wells per pad to minimize cost, maximize productivity and efficiency, and accommodate completion and production equipment? What technical and operational challenges arise when drilling multiple laterals from a common pad? How does one mitigate the risk of wellbore collision during drilling, or production interference during completion? What strategies are operators using to manage the complex logistics of around-the-clock operations? Are there advantages to stimulating multiple laterals simultaneously? What other lessons have been learned to not only reduce cost, but also improve efficiency with pad drilling?
The issues may vary from one play to another, but the challenges of reducing cost, enhancing productivity and improving recovery rates remain the ultimate goals of pad drilling, regardless of the particular horizontal play.
Project Economics
Ray Walker, executive vice president and chief operating officer of Range Resources Corporation, says individual well cost and performance metrics are obviously important, but overall project economics are the most critical factor in horizontal pad drilling.
Range Resources Corporation utilizes zipper fracturing on its Marcellus Shale pad locations. The crew will fracture stage one on each well of a multiwell pad, then move to stage two on each well, etc. Executive Vice President and Chief Operating Officer Ray Walker says Range is able to pump six to eight stages a day, and has done as many as nine.
Range, which has about 1.6 million net acres of stack pay potential for the Marcellus, Utica and Upper Devonian shales in southwestern and northeastern Pennsylvania, has been pad drilling in the state since 2007.
“Early on, we realized we had to do more with less, especially in terms of the surface pad,” Walker relates. “We realized economy of scale matters, and infrastructure matters, whether it is water, roads, pipelines or production facilities. It is helpful if you can amortize expenses over a larger number of wells, but you have to manage the overall economics. You have to balance the number of wells to keep whole project costs as low as possible.”
Those efforts have evolved over time, he states, beginning with Range’s use of top-hole air rigs that have a low day cost to do surface work and set casing to the horizontal section. The larger rig is then brought in to drill the laterals.
“We also have developed a very efficient process for completions,” Walker says, adding that has allowed Range to pump six-eight frac jobs in 24 hours, which is record time.
Range uses one crew per pad, but employs zipper fracturing. For example, Walker says if there are five wells on a pad, the crew will fracture stage one on each well and then move to stage two on each well, etc. He says Range’s crews are able to pump six to eight stages a day, and have done as many as nine.
He also notes that the first walking rig that can literally walk itself from one well to the next on the pad–now standard in the industry–was designed for Range to use in the Marcellus.
“In southwestern Pennsylvania, we are drilling 114 percent longer laterals at 60 percent less cost on a per foot basis, compared with 2011,” Walker claims.
He says Range averages 6,000-foot laterals, compared with the industry standard of 2,000-3,000 feet in 2011.
Walker says Range has standardized production facilities as well. “A lot of our equipment is prefabricated,” he offers. “All our engineering is done in-house. It not only is cheaper, but it also is more efficient because the production equipment on every pad is prefabricated and brought to the location for assembly.”
He says Range has drilled Marcellus and Upper Devonian laterals off the same pad, although it doesn’t have any such dual-zone pads planned this year. That is not a matter of efficiency, however, but a byproduct of low prices. “We literally are pursuing only the very best opportunities and what we need to do this year to optimize our capital efficiency in this price environment,” Walker states. “We have cut our capital budget 45 percent for 2015, but we still plan to grow our production by 20 percent. That is a testament to our efficiency, the quality and diversity of our assets, and the exceptional performance and track record of our team. In this environment, you have to pay attention to every penny.”
He says Range has a diverse position in Pennsylvania, including super-rich liquids, wet gas, and dry gas, giving the company the flexibility to shift with the economics as commodity prices change. Although the infrastructure required varies depending on the type of production, Walker says the company’s standard pad design is the same, regardless whether Range is exploiting wet or dry gas, and is focused on the most efficient use of available technology.
Better Efficiency, EUR
“It is not often that you can improve operational efficiency and get better estimated ultimate recovery at the same time,” reflects Joey Hall, executive vice president for Southern Wolfcamp operations for Pioneer Natural Resources Company in the Permian Basin. “But with pad drilling, the improvement in efficiency combined with the complex fracture networks created by zipper fractures adds significant value. It is a win-win: You are saving money and getting better production.”
Pioneer Natural Resources Company, whose DL Hutt pad is shown here, employs batch drilling in its Southern Wolfcamp operations in the Permian Basin. Executive Vice President Joey Hall says that reduces downtime by enabling the company to drill the surface and intermediate sections of multiple wells with one fluid system before returning to drill the lateral sections with a different mud system.
Pad operations enable batch drilling, Hall points out. “If you are using a water-based drilling fluid for the intermediate string and an oil-based mud for the lateral, for example, you can skid the rig over and in a short time drill all the surface and intermediate sections with one fluid system, then come back and drill all the lateral sections with a different mud system,” he explains. “That means less downtime.
“The only downside to pad drilling is the delay in starting production from the first well,” he allows. “You are delaying the cash flow stream until all wells are ready to commence production.”
Before moving to Pioneer’s Southern Wolfcamp operations, Hall headed the company’s Eagle Ford Shale efforts in South Texas. He says the development and drilling processes are essentially the same in both plays.
“You start trying to nail down the leasehold and appraise the field,” he outlines. “You are appraising broadly to get as much information as possible. A single well without any interference from nearby wells is the best base line. When you start well spacing tests and zipper fracs in pad drilling, the number of variables that can impact performance goes up significantly.”
Although Pioneer has drilled both four- and six-well pads in the Wolfcamp and Eagle Ford, Hall says he believes three is the optimal number. “The efficiency flattens when you put more than three wells on a pad,” he observes. “It extends the ‘spud to placed-on-production’ time. If a well takes 30 days to drill and complete, a fourth well just means 30 more days before the first well can contribute to cash flow.”
Pioneer uses zipper fracs, but Hall says it is not always fracturing stage one in each of the three wells and then moving to stage two. Pioneer has experimented with variations of traditional zipper fracs by lagging stimulation of stages on one of three wells to see whether that enhances the fracture network and improves performance.
Need To Plan
Hall emphasizes that there is not a single recipe. Pioneer has almost 800,000 acres in the Permian Basin, and in some cases it is drilling stacked pays in multiple zones, which makes the process that much more complicated.
Pioneer Natural Resources employs zipper fractures on its Permian Basin and Eagle Ford Shale wells, such as this Three Sisters pad in the Eagle Ford. But Executive Vice President Joey Hall says the company has experimented with variations of traditional zipper fracs by lagging stimulations of stages on one well to see whether that enhances the fracture network and improves performance.
“In some cases, we have four or five pay zones in the same acreage,” Hall relates. “We can predict from modeling how wells in the same zone will react. But when you are drilling in multiple zones, it gets more complex. Predicting how a well will react and how multiple laterals will react to each other is challenging. We still have a long way to go in understanding that aspect.”
Preplanning is important also for designing the surface layout of a multiple-well pad, according to Hall.
“You have to know what your artificial lift needs will be,” he points out. “If you are using pumping units, you don’t want the wellheads too close. You also want to consider the workover scenarios. If you have stacked pays, odds are you will drill more wells in the future, so your pad layout has to take that into consideration as well. You also have to consider anti-collision practices because the wells are drilled so close together in a field with thousands of vertical wells.”
Hall says modern rigs that can walk themselves to the next well site have improved efficiency greatly and cut the time needed to drill multiple wells.
Paradigm Shift
Drilling multiple wells off the same pad may seem like a paradigm shift from traditional single-well sites employed by the industry for decades, but Kurtis Hoffman takes it one step further.
“We don’t talk primarily about the number of wellheads per pad,” says Hoffman, general manager of completions for CONSOL Energy, which is drilling Marcellus and Utica shale horizontal wells in a pair of joint ventures with Noble Energy and the Hess Corporation in Pennsylvania, West Virginia and Ohio. “We talk about how many lateral feet we have per pad. If we drill four to six wells per pad that average 8,000-foot laterals, we are talking about 32,000-40,000 lateral feet per pad. We even consider construction cost per foot of lateral. Not everyone does that, but we talk only in terms of the number of lateral feet per pad.”
CONSOL Energy reckons its Marcellus and Utica shale drilling and completion economics based on lateral feet of wellbore, rather than number of wellheads per pad. “We even consider construction cost per foot of lateral,” comments Kurtis Hoffman, general manager of completions. “We talk only in terms of the number of lateral feet per pad.”
He says lots of economies of scale can be realized when drilling multiple wells, which allows CONSOL to split containment and completion costs, for example, across multiple wells.
“Service costs actually are lower because the service companies don’t need as much manpower,” Hoffman illustrates. “But there are a lot of things to consider. We call it project management similar to that of a factory. You are not making money when you are rigging equipment up and down.”
CONSOL has settled on a standard of four-six wells per pad. “Beyond that, there is a lag time in cash flow,” Hoffman reasons. “Fewer than that, and you aren’t gaining the cost advantages of drilling multiple wells on a pad. You have to find that sweet spot.”
Surface and subsurface spacing is important also, according to Hoffman. He says CONSOL utilizes 20 feet between wellheads. In the subsurface, it uses about 750-foot spacing between laterals in the dry gas window and 600- to 800-foot spacing in wet gas areas. Like the optimal number of wells per pad, he calls spacing a balancing act.
“It depends,” Hoffman muses. “If you move the laterals closer, you could have interference. The amount of drainage dictates that. You want minimum interference with maximum recovery.”
He says CONSOL typically fractures two wells at a time, preferably wells going in opposite directions. “Technically, they are stacked laterals,” Hoffman describes. “On the surface, personnel appear to be doing zipper stimulation operations, but underground they are stacked fractures. It is all geology driven. You have to balance operational efficiency with getting the most bang for the buck.”
Driving Efficiency
Although CONSOL has drilled Marcellus and Upper Devonian laterals off the same pad, Hoffman reports that this spring, the company plans, for the first time, to stimulate a pad in Monroe County, Oh., that includes both Marcellus and Utica laterals. He says that forces some adjustments since each horizon has different pressures (about 10,000 psi in the Marcellus and 15,000 psi in the Utica).
“We have gone to a standard gas production unit in the dry gas window of the Marcellus,” Hoffman reveals. “In the Utica, there is some variability, such as how much condensate you are producing. Will you truck the condensate or pipe it? Some of that is a midstream issue and some is pad design. In the dry gas Marcellus, we have a homogeneous solution, but it is not one size fits all in the wet gas areas.”
Five years ago, Hoffman says, CONSOL was happy to drill a 4,000-foot lateral. Today, it is targeting 8,000-foot laterals, and will drill longer when it can. The company has exceeded 10,000-foot laterals, he says.
Perhaps the biggest lesson in pad drilling that CONSOL has learned, however, is that “time is money,” according to Hoffman.
“Every day you are not efficient costs you additional money,” he emphasizes. “We are scrutinizing down to 15 minutes how long it takes to do something. If we can reduce rig-moving time, use dual workover rigs, or run multiple separators parallel, we can move the revenue stream forward. Every minute is important. Much of our equipment is daily rentals. If we can shrink that time, we don’t just delay the cost, we don’t have to pay it.”
Vendor selection becomes important, too. Hoffman says it is critical to select vendors that not only have the same safety values as CONSOL, but that also will work with the company on project cost management.
The brutally cold winters experienced in the Northeast the last two years have exposed yet another advantage to pad drilling. “It is cheaper to run tarps and indirect heaters on multiple wells on a pad rather than on a single well,” Hoffman reports, noting that CONSOL uses brine to avoid freeze-ups.
Although CONSOL hasn’t done it yet, Hoffman says he believes the industry will increasingly use produced natural gas to fuel its pumping equipment in an effort to decrease costs and reduce its environmental impact. CONSOL is beginning a project at the Pittsburgh International Airport in which it will utilize diesel engines that meet Tier 4 final air quality specifications.
“They actually will have lower emissions than dual-fuel engines,” he praises.
Lessons Learned
David Elkin, senior vice president of drilling and completions for EQT Corporation, says pad drilling has become an integral part of his company’s drilling and completions process in the Marcellus, Utica and Lower Huron plays, yielding many cost and operational advantages.
Not only has pad drilling increased the speed and efficiency of EQT Corporation’s Appalachian Basin operations, but it also reduces the amount of community and surface disturbance. Senior Vice President David Elkin points out that drilling only one well per location would add 50-70 truck trips over area roadways each week.
“We are able to produce reservoirs efficiently while limiting the number of required locations,” he states. “During the drilling and completion phase, having multiple wells on a pad allows the drilling rig and completion crews to stay on one location longer. This not only allows us to drill and complete the wells faster and more efficiently, but also reduces the amount of community disturbance and wear and tear on roads, and results in less surface disturbance for our landowners.”
He notes that if EQT was unable to drill more than one well on each pad, 50-70 truckloads (drilling rigs and completion crews) would be moving on roadways weekly.
Through the evolution of multiwell development from a single pad, there have been several lessons learned, according to Elkin.
“We have discovered that drilling as many wells, and as long a lateral as technology or land constraints will allow, is the most efficient and economical way to develop our reservoirs,” he imparts. “We have stacked target formations in some of our plays, which allow us to double the number of wells on a pad. The optimal well spacing varies by formation and area. We have learned that some areas require closer spacing to drain the reservoir effectively, while other areas are more economical to produce at wider spacing. The reservoir and rock qualities of a particular play will vary throughout the reservoir, and as we continue to develop and test each one, we determine the optimal spacing for that area.”
Pad Dimensions
Elkin says EQT has a team that determines the dimensions of the pad. “The total number of wells and the associated surface equipment play a large role in determining pad size,” he says. “From there, the team plots and plans how the rig will be constructed on the pad, the order in which the wells will be drilled, how the completions crew’s equipment will be placed on location, and where the permanent production facility will reside. Preplanning all phases of the operation allows us to plan each operation efficiently, so the correct equipment can be put in the best spot and pad infrastructure can be placed properly.”
Determining pad size is a team game at EQT Corporation, where Senior Vice President David Elkin says team members consider such factors as number of wells and associated equipment, the position and sequence in which wells will be drilled, how completion equipment will be placed, and where the permanent production facility will reside.
The sequence in which the wells are drilled also factors into the efficiency with which the pad can be developed, according to Elkin.
“Wells usually are positioned in a straight line when developing a pad,” he explains. “This minimizes the amount of equipment that must be moved when repositioning the rig for the next well. We plan to drill a straight hole first, to gather information about our target formation. Once that information is obtained, we will start drilling in each direction outward from our point of best control. This allows us to land our laterals on target and stay in our target more effectively.
“We also have learned that it is best to drill the wells in order from one side to the other,” Elkin adds. “If wells need to be drilled between one another, it incurs additional costs to ensure the well does not affect the wells on either side.”
Although pad size typically limits simultaneous stimulation efforts, Elkin says that under optimum conditions–typically with a minimum of three wells–perf-and-frac zipper work can lead to increased efficiencies.
“The key to success is proper planning,” he emphasizes. “Functional rig-ups as well as coordinating water and sand logistics are critical. Multiple unit drill-outs and flowbacks have decreased overall pad completion times dramatically. This typically has been more effective on pads with more than five wells.”
Elkin also notes that a rig with a “walking package” can save a lot of time moving from one well to the next.
“Another advantage to a walking rig is that it can move to any well on the pad,” he offers. “This allows us to set 90 percent of the equipment on location, and we can develop the wells on the pad in any order.”
Responsible Exploitation
A number of leading producers in North Dakota’s Williston Basin have formed a consortium with the support of the North Dakota Industrial Commission’s oil and gas research program, called the Bakken Production Optimization Program. John Harju, associate director for research at the Energy & Environmental Research Center (EERC) at the University of North Dakota, which works in conjunction with its industry partners, says the consortium has focused on a single 14-well pad, the Hawkinson pad, drilled by Continental Resources.
The Energy & Environmental Research Center at the University of North Dakota works in conjunction with industry partners to improve oil recovery from the Bakken Shale while reducing its environmental impact. EERC Associate Director John Harju says the consortium’s goals include better understanding of Bakken-Three Forks reservoirs, reduced road-maintenance and wastewater-disposal costs, less freshwater use, and increased revenue from added product streams.
“The notion is to better understand the resource and how to exploit it to ultimately do a better job on the surface,” Harju explains. “The early focus in the Bakken was a single well on 1,280-acre spacing. Now, there are 16-20 or more wells in a single spacing unit. Obviously, that means greater recovery, but there also are challenges in coordinating that.”
The goal of EERC and the consortium’s three-year research program is to simultaneously improve the Bakken system’s oil recovery while reducing its environmental footprint. It claims its results will include better understanding of the Bakken-Three Forks reservoirs and subsequent increases in recoverable hydrocarbons; less truck traffic, resulting in decreased diesel emissions, road dust and spills; reduced road maintenance costs, wastewater disposal costs, and freshwater use; reduced surface impacts; and increased revenue from added product streams captured earlier in the well life cycle.
As an example, Harju comments, when a producer has 18 wells on one site, it brings myriad other challenges, such as how to manage drilling waste. He says a full turnkey facility is being installed by Nuverra Environmental Solutions near Watford City, N.D., to recycle drill cuttings. The drilling waste will be separated and recycled for a variety of purposes, including reclaiming diesel for reuse in drilling mud, for road base, or for deicing roads in winter, he says.
Handling Associated Gas
Since the Bakken Shale is primarily an oil play, Harju says much of the consortium’s early work has focused on how to handle the associated gas that is produced along with the crude oil.
“Trying to get a gathering system to keep up with gas production is a challenge,” Harju allows. “There has been considerable flaring in the Williston Basin. How do you bring on 20 wells on a single pad, and what does the gas profile look like–now and two years from now? Do you overbuild the gas infrastructure or do you stage the completions to bring the wells on line slowly? Do you bring one well on every month or one every two weeks?”
A turnkey waste management facility being installed near Watford City, N.D., will recycle drill cuttings. Among its services is reclaiming diesel for reuse in drilling mud, for road base, or for deicing roads in winter.
He says the consortium always is looking for multiple solutions because what works best for one operator at one site may not be best for another producer at a different location. “We have looked at remote capture systems deployed for a short period,” Harju mentions. “The cost is easier to bear if you are capturing natural gas liquids on site.”
Noting that producers now must file gas capture plans with their applications for permits to drill, he says the consortium has worked with producers and gas gatherers to improve communications between the two and to develop plans to gather the gas. It also is doing modeling to understand peak rates and technology, thus allowing producers to stage completions at the most efficient rate.
“Every producer has a different appetite,” Harju reflects. “We are bringing tools to the key Williston Basin producers so they have a better understanding of the resource in order to maximize production over the lifetime of the unit, and not just production on any given day.”
Multiwell pad drilling also presents a design challenge for sizing and placing separation tanks and treaters, Harju points out. “The same challenge in handling the gas flow off a single pad exists for handling fluids,” he attests. “Do you bring 18 wells on at one time or bring them on in stages? Ultimately, you want a cohesive program for the optimal footprint.”
As the consortium continues its work, Harju says it will turn its focus to lateral lengths and optimal lateral spacing, as well as simultaneous stimulation of multiple wells and other issues associated with multiwell pad drilling.
For other great articles about exploration, drilling, completions and production, subscribe to The American Oil & Gas Reporter and bookmark www.aogr.com.