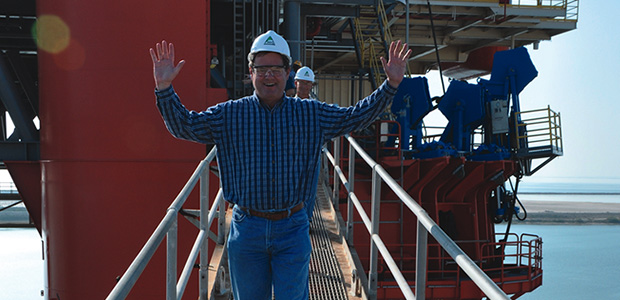
LLOG Achieves Several ‘Firsts’ In FPS-Based Development Of Deepwater Who Dat Field
By Rick Fowler, Eric Zimmerman, Jay Cole, Ed Nagel, Harris Knecht and Eldon Robison
HOUSTON–The Who Dat deepwater development represents a number of firsts, including the first private-company-owned floating production system (FPS) in the Gulf of Mexico, the first use of the OPTI-EX™ semisubmersible design in the Gulf, the first FPS built on a speculative basis, and the first time a Gulf field progressed from the concept selection phase to installing a new FPS in less than one year. The project’s accelerated schedule created challenges since numerous items were on the “critical path,” including numerous items that typically are not considered critical.
The Who Dat Field is primarily oil and consists of 10 stacked amplitude-supported reservoirs in a salt withdrawal minibasin in Mississippi Canyon blocks 503, 504 and 547. The OPTI-EX semisubmersible has a daily capacity of 60,000 barrels of oil and 150 million cubic feet of natural gas. Four wells have been drilled to date, penetrating more than 1,000 feet of net pay in nine distinct reservoirs at depths between 12,000 and 17,000 feet true vertical depth.
The field is being developed with 12 subsea wells flowing to three subsea manifolds tied to the FPS through two flexible riser infield flow loops. The project includes a 10-inch gas export line and a 14-inch oil export line, which also use flexible risers.
A number of amplitudes (bright spots on the seismic data) had been identified previously in the Who Dat area. The objective section–the Lower Pliocene though Upper Miocene–had been drilled in offset blocks (MC 460/502/546) from 1985 to 1998, and found thin and/or poor-quality, hydrocarbon-bearing sands. Operators presumably assumed that the results of these wells meant that all of the amplitudes in the area were thin and uneconomic, which is the likely reason the previous operator allowed MC 503 to expire without drilling a well.
With TGS NOPEC’s release of the Mississippi Canyon Revival™ Kirchhoff prestack time migrated 3-D dataset over this area in the spring of 2004, the poor placement of these wells and the thin pay results were clarified. This did not eliminate the risk of finding thin pays in other wells, but LLOG felt it could explain the poor historical drilling results.
Testing The Prospect
LLOG originally identified the prospect as three stacked objectives with amplitude and amplitude-versus-offset support, and a moderate downdip fit to structure (indicating the possible presence of a hydrocarbon/water contact). An inaugural well could test three objectives: the 4,000-, 4,200- and 4,800-millisecond sands (ms). All three objectives were Class III AVO anomalies (meaning the amplitude was bright in all offsets in the offset stacks). The trap for these potential reservoirs was located on the south side of a salt feature, and all three targets exhibited both a structural and stratigraphic component with some evidence of aquifer support.
Because of the presence of gas in the few wells drilled in the area at the time and the amplitude strength exhibited on each objective, LLOG projected gas was the most likely hydrocarbon type. The three objectives ranged in size from 244 to 315 acres, and using the seismic to estimate a gross sand thickness, net thickness using a net-to-gross ratio was estimated at 60-80 percent. For final predrill reserve estimates, LLOG made some additional assumptions (30 percent porosity, 20 percent water saturation, etc.), which resulted in a predicted recovery factor of 2,100-2,300 Mcf per acre/foot.
To develop its lease sale economics, LLOG assumed a total of three wells would be drilled (one to the north and one to the west after the inaugural well), and would be developed using a long subsea tieback to a host platform on the Shelf.
The MC 503 lease became available in March 2005 for the first time since 1994, when it had been leased by Shell and then farmed out to British Borneo. LLOG expected competition on the block as a result of the amplitudes and the new data providing an explanation for the thin sands drilled in the area.
Based on LLOG’s prelease sale work, management decided to bid $6.7 million for this block. When the bids were read, LLOG’s offer was the highest among seven other bids, with a total of 11 companies bidding on the block. LLOG was awarded MC 503 in May 2005. LLOG also was the high bidder at $2.55 million on MC 545, in which several Miocene-aged, amplitude-supported prospects have been identified.
While LLOG bid on the MC 503 without partners, to diversify risk, the company’s intent was to drill the first well with partners at no more than a 50 percent working interest. Since the objective reservoirs crossed lease line boundaries to the east (MC 504) and north (MC 459 and 460), it made sense to attempt to jointly develop the four-block area. ENI owned 100 percent of all three of those blocks, which were close to lease expiration. LLOG and ENI negotiated for some time and agreed to form a unit to hold all the blocks and allow continued negotiation after each company drilled its first well in the area. Without securing a suitable partnership offer, LLOG decided to drill the inaugural 503 well at a 100 percent working interest.
Drilling The First Well
The MC 503 No. 1 exploration well spudded on Nov. 1, 2007, after anchoring the Diamond Ocean Victory in 3,100 feet of water. Management was eager to drill the prospect prior to an upcoming Central Gulf lease sale, since nearby blocks would be available. The original well was planned with a measured depth of 16,700 feet (16,070 feet TVD) to the three Pliocene/Upper Miocene targets. As the well was drilled, the geology and geophysics group adjusted its seismic depth correlations and changed the well plan trajectory to hit the amplitude bright spots, which were coming in shallower than expected.
As drilling progressed and the 4,000-, 4,200- and 4,800-ms horizons were encountered, the zones were found productive and thicker than expected. These discoveries prompted a “while drilling” review of additional potential in the area. A significant outcome of the review was the further evaluation of deeper potential at the well bore, with the 5,100-ms horizon recognized as an additional target for the well.
From a geophysical perspective, the 5,100-ms horizon is different from the other discovered horizons in the field, which have Class III classic bright spot amplitudes. Instead, the deeper horizon is in a Class II environment, meaning the amplitude is dim in the near offset ranges, but bright in the far offsets. Further complicating the decision was the fact that the well bore was nearing the lease line and the well would have to drop angle to vertical to avoid crossing into a lease that was not controlled by LLOG. After seeing the success in the shallower zones and getting positive feedback from the drillers about the ability to test the section, it was determined that deepening the well to test the Class II 5,100-ms horizon was worth the risk.
The full-stack time data in Figure 1A clearly show a bright spot at the 4,800-ms horizon, but also a nonanomalous event at 5,100 ms. The image also illustrates the need to drop the angle of the bore hole to vertical to avoid crossing the lease line. The far-stack time data in Figure 1B show an anomalous event at both the 4,800- and 5,100-ms horizons, with the increase in amplitude indicative of a Class II event.
The primary targets were cased and cemented with a 97⁄8-inch liner at 15,737 feet MD/14,050 feet TVD. An 8 1⁄2-inch x 97⁄8-inch open hole was drilled and logged, dropping inclination in the well from 47 degrees to vertical to a final depth of 19,050 feet MD/17,624 feet TVD.
The expertise of the well planner (LLOG utilized Baker Hughes on this well) was critical during the multiple adjustments of the directional plan. Once drilled, the well encountered 53 feet of oil in a laminated section on top of 130 feet of high net-to-gross wet sand. The zone was expected to be near the water contact in the horizon at the 503 No. 1 well; a future well is planned to test the section in an updip position. The additional, unplanned hole section yielded valuable information for the G&G group to tie in similar amplitudes seen in the southwest corner of MC 503, in addition to the potential on open MC 547 directly to the south. A 75⁄8-inch liner was run and cemented in place, the well was temporarily abandoned and the rig was moved off and released.
Exceeding Predrill Estimates
The results of the MC 503 No. 1 well far exceeded the predrill estimates from the total pay to the net-to-gross to the condensate yields of 45-90 bbl/MMcf. The 4,000-ms sand had 72 feet of net pay with a net-to-gross of 90 percent, a condensate yield of 40 bbl/MMcf and post-drill reserves of 63 billion cubic feet equivalent. The 4,200-ms sand also had a high net-to-gross, plus it is a gas reservoir with an oil rim. The post-drill reserves were assessed to be 58 Bcfe and 4 million barrels of oil. The 4,800-ms sand had similar results with post-drill reserves of 45 Bcfe.
The deeper 5,100-ms sand was also productive with oil on water. With the penetration at the 5,100-ms horizon roughly 700 feet downdip from the crest, it proved up a 600-acre reservoir. An additional well is planned to further delineate this reservoir.
The drilling of LLOG’s initial well and development drilling by ENI in MC 459, 502 and 546 proved that the seismic could properly place wells to achieve high-to-net gross sands with sizeable reservoirs.
After the 503 No. 1 well was drilled, LLOG and ENI resumed negotiations. The companies agreed to swap acreage to allow the ownership to conform to the reservoir boundaries, thereby avoiding competition. Competing in a deepwater reservoir can be wasteful, with a single well costing $70 million or more to drill and complete.
As the LLOG team performed additional geologic work, it located numerous other potential reservoirs. Additional objectives on the north and west side of the block have been identified, with the 4,600-ms sand the largest. This sand is roughly 5,000 acres in size, but the majority of the reservoir is on MC 547, which happened to be available for first time since 1997 at the March 2008 Central Gulf lease sale.
In addition to a gas scenario at MC 547, an oil case was run because LLOG’s geologic interpretation tied the reservoir to a British Borneo well drilled in 1998 in the block to the west. That well had logged oil pay, but it was poorly positioned up-thrown to a fault that separated it from the reservoir. However, it did give LLOG encouragement that both sand and hydrocarbons were present in this reservoir. LLOG was high bidder on MC 547 at $23.6 million, and the lease was awarded in July 2008. With the key pieces of the development in place, the delineation phase could begin.
Refining The Geologic Model
LLOG acquired the TGS NOPEC Kirchhoff PSDM data volume in March 2008. This migration features an anisotropic velocity estimation and subsalt tomographic inversion method that was calibrated to 247 wells in the survey area to generate high-quality, properly positioned data.
LLOG determined that the primary influence on sedimentary patterns during the Late Cenozoic in the Mississippi Canyon area is salt withdrawal and the subsequent creation of withdrawal minibasins. The regional depositional framework during this time at blocks 503/547 was classified as a prograding, unconfined turbidite system traveling along a northwest-to-southeast axial thoroughfare created by salt withdrawal. As the 503/547 fan complex prograded, the deposits evolved from the prograding wedge deposits of the 5,100-4,400 ms sands, which are more laterally extensive, sheet-like sands; to the channel overbank deposits of the 4,200-3,500 ms sands as the fan advanced farther into the basin.
Characteristics of the sands comprising the distal fan deposits of prograding wedge include reservoirs that are very broad, disconnected sheet sands with fair to good net-to-gross. Similarly, medial fan deposits are laterally extensive, amalgamated sheet sands, but with high net-to-gross reservoirs. The proximal deposits of the fan complex, which include reservoirs in the 4,200-3,500 ms sands, are composed of narrower channel-levee complexes with high net-to-gross and possible vertical connectivity.
After LLOG’s geologic team finished its detailed review, the development team (geology, drilling, reservoir and completions) generated well plans to produce all the reservoirs in the field and optimize the wells into two drill sites. These were the existing 503 No. 1 surface location and a location to the southwest of MC 503. Drilling from the fewest number of locations would reduce risk and facility installation cost.
The team decided that two wells on the west side of the block would be best to delineate the field, since they could test key unpenetrated reservoirs and best narrow the uncertainty of field reserves. The 503 No. 2 well was planned to test five new objectives (4,000 ms West, 4,200 ms West, 4,400 ms, 4,600 ms and 4,700 ms). The No. 3 well was to bottom hole on MC 547 and test the 4,600-ms sand reservoir, which had the highest reserve potential.
Delineation Drilling
Noble’s Lorris Bouzigard was anchored in 2,460 feet of water at the second drill site to drill one well to targets in MC 503 and the other to targets in MC 547. By using a common drill site, it was possible to batch drill the riserless sections and reduce rig time, changing from water-based to synthetic muds. In addition, batch setting allowed jumping the blowout preventors from one well to the next without pulling between for maintenance. This opportunity saved eight rig days and $6 million.
The 503 No.2 and 547 No. 1 wells spudded in February 2010. The 503-2 well reached TD at 18,204 feet MD/15,598 feet TVD, successfully proving up the amplitudes to the south of the discovery well. The 547-1 well reached TD at 18,800 feet MD/15,974 feet TVD, successfully proving up the amplitude in the 547 block. The production intervals were cased with 97⁄8-inch casing and cemented.
Table 1 shows drilling data for all three wells, with an improving average drilling cost per foot. Much of the nonproductive time (NPT) included weather and shoe squeezes of the intermediate (135⁄8-inch) casing shoe. The casing depth on subsequent wells is being changed, based on some of the ongoing rock property studies.
The No. 2 well was drilled in March 2010 and found hydrocarbons in all of the objectives. With the exception of the 4,000-ms sand, all sands were oil-bearing. LLOG also confirmed its confidence in the seismic depths with projected depths of the penetrated sands closely matching predictions. The No. 3 well was drilled in May 2010 to test the 4,600-ms sand in a downdip position. This well also was oil productive and proved up a substantial reservoir. With the new well information, LLOG’s confidence level in the amplitudes increased and opened several additional reservoir targets. LLOG performed a number of studies on the pressure, fluids and rock compaction that further increased reserve assessment in the field.
The new reserve range from the success of the three wells, and additional mapping and potential reservoirs, ranges from 238 million to 333 million barrels of oil equivalent. Figure 2 shows the reserves have increased at each stage of the project.
LLOG intended to immediately drill a fourth well to further narrow the reserve uncertainty in the field, but the temporary deepwater drilling moratorium in 2010 forced a change in plans. Although the development concept was not yet selected, LLOG felt certain that the reserve range would warrant development. The company had subsea trees available for completion because of its strategic relationship with its subsea alliance partner, FMC. LLOG also had downhole completion equipment available. Consequently, the company decided to immediately move into completion mode and use Noble’s Lorris Bouzigard rig to complete the 503-2 well, which had four zones LLOG intended to ultimately complete.
LLOG prefers to work “bottom up” and complete no more than two zones at a time to reduce mechanical risk. As a result, the well was frac packed successfully in the bottom two zones with a smart selective completion. The 547-3 well was completed next, but the rig was swapped to Noble’s Amos Runner, since it could more quickly satisfy the post-Macondo BOP recertification requirements. The No. 3 was completed as a single frac pack in the 4,600-ms sand.
Development Concept
LLOG had envisioned developing the field as a subsea tieback to a newly built platform on the Shelf. The presence of low-gravity, high-viscosity oil in the largest reservoirs made a floating production system a necessity. Fortunately, the new reserve range was more than adequate to justify the cost of an FPS.
LLOG considered a number of options for the host facility, including a purpose-built FPS using various proven technologies: a third-party owned, new-build spar that would allow co-development with a nearby field; an unproven new concept; relocating an existing FPS; and using the OPTI-EX platform that had been built by Exmar on a speculative basis.
A foremost advantage of the OPTI-EX is a field installation-friendly design that requires no offshore derrick lifts for mating the deck to the hull. The light weight, yet strong deck allowed installing the majority of topsides equipment inclusive of installing interconnecting piping, instrumentation and control systems, and precommissioning in the fabrication yard. A subsequent shore-side, single lift-and-set operation installed the nearly completed deck onto the hull. Only a few remaining customer-specific equipment items were required to be installed and hooked up “in the air” at quay-side before going offshore.
Another significant advantage was that the unit’s pontoon displacement had sufficient reserve transit freeboard, which when coupled with its transition draft stability, allowed for a simple tow out and offshore hookup to mooring, risers and umbilicals. This advantage allowed loading equipment and rigging for mooring line hookup, riser and umbilical pull in at quay-side before towing out.
The approximate one-to-one hull weight-to-topsides deck weight ratio means the unit cost less to build than an equivalent capacity platform because significantly less material is needed. Naval architectural design considerations of hull/topsides environmental drag, deck load capacity, air gap, stability, motions in a seaway, mooring performance, global strength and fatigue strength were all designed in light of post-Katrina requirements. The inextricable linkage between these measures during design ensured they were on the high value part of curves of these measures versus light ship weight, and displacement versus light ship weight. They all contribute to the weight efficiency and sophistication of the unit’s design.
OPTI-EX designers also achieved high value in production performance, production equipment operational availability (up time), and cost to operate over the life of the unit. Using a modular design, spark-ignited reciprocating engines with self-contained and overhead-mounted air cooling as prime movers for pumps, compressors and production utility-support power generators conserved deck area, reduced weight, lowered investment in central support utilities, and made it possible to more easily expand productive capability.
A reserve capacity of 1,000 tons of deck load and 3,300 square feet of space was designed into the unit for future changes. The flexibility in accommodating future production/process needs is matched by flexibility in terms of accommodating present and future field architecture needs. OPTI-EX was designed to accept 20 production, import and export risers located along three of its four sides. Ultimately, the OPTI-EX was fitted with 14 riser slots for the Who Dat Field.
This future production capability expansion and field architecture flexibility is significant, simplifying the addition of more compression, pipeline pumping, power generation or water treatment facilities. Process debottlenecking or other modifications are simplified by designing process modules friendly to retrofits and upgrades. Adding future risers or umbilicals is possible, utilizing preplanned, simple and robust prefabricated mounts on lightweight preinstalled riser porches and hull pipe racks.
Fastest, Lowest-Risk Option
LLOG chose the OPTI-EX because of its design advantages and the fact that it would lead to first production at least one year faster than most other options. It was clearly the fastest, lowest-risk option.
LLOG began discussions with Exmar in April 2010. Exmar originally had envisioned a lease arrangement with a day rate, but that arrangement was not attractive for LLOG since it planned to keep the OPTI-EX at the Who Dat location for the design life of the FPS. An outright purchase would be difficult for LLOG because of the large investment required for the wells, pipelines and subsea system.
The companies eventually agreed on an installment purchase with a significant payment at delivery and 62 monthly payments. There was also a relatively small production-based payment in months where production exceeded 35,000 boe/d. The arrangement allowed LLOG to focus its capital resources on exploration and development, while proving Exmar an acceptable return on investment.
The OPTI-EX was designed to maximize flexibility so it would not be limited in its application. As a result, certain equipment was not installed. For example, riser porches were not installed since Exmar did not know how many risers or what sizes/pressures would be required. As another example, a gas sales skid and lease automatic custody transfer (LACT) unit were not installed, since pipeline pressures and sizes were not known. In general, only the basic production train was installed.
The topside facility was designed as an oil production facility with a daily capacity of 40,000 barrels and 50 MMcf of associated flash gas. At a minimum, the topsides would require pipeline pig launchers and receivers, LACT, sales gas metering, and chemical injection.
Compressor and oil pipeline pump sizing were adequate and did not require immediate rework. The specific requirements of the Who Dat Field included a high-pressure gas separator and dehydration system to accommodate the gas zones. The system allowed the gas capacity to increase to 150 MMcf/d. Without a high-pressure system, the gas would have to be throttled to low pressure and compressed back to pipeline pressure, greatly restricting capacity and wasting large amounts of fuel. The original gas dehydration system was left operable and will be used once there are no producing high-pressure gas wells.
Test separators were installed to allow testing of the flow through any of the four infield subsea lines. This arrangement provides the most accurate system of measurement, which is important at Who Dat because of differing royalty rates.
The FPS was designed with a significant amount of expandability/flexibility with spare deck space and weight-bearing capacity, and LLOG desired to keep as much flexibility as possible. All new equipment and skids were designed with options for expansion. Removable beam packages were installed in unused open spaces topside to allow for immediate utilization and future utility.
The FPS was built with no hull fixtures to support the incoming and export pipelines or control umbilicals. The team designed riser adapters for the pontoon, but the mounting brackets required installation using coffer dams. As a result of the complexity of the riser porch installation, the fabrication and installation of hull fixtures and piping were on the critical path and drove yard scheduling and equipment deliveries.
LLOG originally planned for 16 riser slots (one oil export, one gas export, four infield flowlines and 10 futures). The OPTI-EX can accommodate many risers since the weight of the additional risers is offset by reduced ballast water rather than reduced payload in the topsides. As the project progressed, it became apparent that installing all of the planned riser porches would delay sail away of the FPS. LLOG changed the plan to install 14 riser slots, leaving eight future slots that should be adequate for nearly all realistic scenarios. If additional porches are required, they can be added offshore.
Export Lines
LLOG reviewed landing point options for both exports for overall flow assurance, capacity assurance, connection cost, counterparty reliability of performance, agreement terms, and overall revenue/unit netback.
Since Who Dat’s oil is light-medium sour, Shell’s Mars pipeline system represented the best overall fit for oil export. Mars had a tie-in point at MC 718, located 19 miles west-southwest of Who Dat. A 14-inch pipeline ensured the oil pipeline capacity would be adequate to match the topsides capacity of 60,000 bbl/d under the worst expected blended viscosity. An 111⁄2-inch inside diameter, flexible riser was used, which was the smallest flexible riser that would allow pigging of the oil export. Steel catenary risers were not an option for any of the risers because of hull motions in the 3,100 feet of water.
For gas export, Enterprise’s Independence Trail is in close proximity to the OPTI-EX and had adequate firm capacity and revenue per unit. The pipeline had a connection point in MC 553, 17 miles east of Who Dat. A 10-inch pipeline with a 9 1⁄2-inch inside diameter flexible riser matched the topsides design capacity of 150 MMcf/d at the highest expected pipeline pressures.
Both export lines required installation through an area that was used previously as an ordinance dumping area. Fortunately, the pipeline survey indicated no obstacles that required remediation along either route.
The subsea system was designed to accommodate eight wells from the western (“E”) location and four wells from the eastern (“A”) location. LLOG considered three options for the flow path from the wells to the OPTI-EX: two separate looped systems, a single piggable loop, and individual flowlines. The individual flowlines were eliminated because they would necessitate using either subsea meters or significant shut-ins to test individual wells. While a single piggable loop was workable, ultimately, the two separate looped systems option was chosen to provide the most flexibility for testing and accommodating wells of different fluid types and pressures.
LLOG used an integrated production model to optimize flowline sizing, evaluating three sizes of infield loops. A 6- x 6-inch system was selected because it was optimal for nearly all scenarios, and a single size would increase ease and flexibility during installation.
The OPTI-EX was installed using 12, 80-foot suction piles with chain-poly-chain mooring in July 2011. The export and infield risers were installed shortly thereafter. First production began on Dec. 9, 2011. A project that had started as a three-well gas development with relatively small reserves using a long subsea tieback system eventually became a 12 well, 100 million-300 million boe gas and oil development using the latest semisubmersible FPS technology.
The reserve assessment for the field has increased over time as the operator came to better understand the seismic signatures, fluid properties and rock properties. The project overcame the uncertainty associated with the post-Macondo regulatory environment to become the fastest FPS development ever completed from concept selection to installation. Using a spec-built facility required careful scheduling management since items not typically on the critical path became critical, but ultimately led to a significantly improved schedule.
Editor’s Note: The authors acknowledge the contributions of LLOG Exploration Company’s John Doughtie, Bruce Cooley, Craig Mullet, Steve Stegeman, Barney Paternostro and Jack Boelte to the preceding article, which was adapted from a technical paper presented at the 2012 Offshore Technology Conference in Houston. Future AOGR articles will discuss specific elements of the Who Dat project, including the field’s geology, the subsea system and the FPS.
RICK FOWLER has been the vice president of deepwater projects for LLOG Exploration Company LLC since 2007. During his career, he has been involved in six Gulf developments using new floating production systems and numerous subsea tieback projects. Prior to joining LLOG, Fowler was employed by Dominion E&P (formerly CNG Producing), where he was in charge of the $5 billion offshore business unit, including managing more than 300 employees. He previously worked for Exxon for 12 years in various operational and supervisory assignments. Fowler is chairman of the American Petroleum Institute’s Delta Section and serves on the board of the Gulf of Mexico Foundation. He holds a B.S. in mechanical engineering from Tulane University.
ERIC ZIMMERMAN is vice president of geology at LLOG Exploration. He joined the company in 2007 as a deepwater geologist. Zimmerman has focused his career on exploration and development projects in the deepwater Gulf of Mexico with previous experience at BP and Dominion. He is the past president of the Southeastern Geophysical Society, vice president of the New Orleans Geological Society, and a fellow of the Geological Society of London. He holds a B.S. and an M.S. in geology from Louisiana State University.
JAY COLE is vice president of deepwater exploration for LLOG. He joined the company in 2000 as an exploration geophysicist and has 24 years of industry experience. Prior to joining LLOG, Cole held a variety of senior geophysical positions in Shell Oil Company’s deepwater group. He received a B.S. in geology from Nicholls State University and an M.S. in geophysics from Texas A&M University.
ED NAGEL is vice president and co-founder of Exmar Offshore Co. in Houston. Previously, he was employed by Diamond Offshore, Arethusa Offshore and Zapata Offshore for a combined 16 years in various design engineering and construction project management roles for the fleet of jack-up and semisubmersible rigs owned by those companies. Before joining Zapata in 1983, Nagel worked as a design engineer at the Stran Steel division of National Steel, a design engineer for The Offshore Co. (now Transocean), manager of ETPM USA’s U.S. engineering group, a senior staff engineer for land and helicopter transportable drilling rigs for Bawden Drilling, and a senior project engineer for the Murphy-Surla Projects consulting group. He holds a B.S. in civil engineering from the University of Detroit and an M.B.A. in finance from the University of Houston.
HARRIS KNECHT is president of Exmar Offshore Company. He has 35 years of experience in the offshore industry, primarily in the areas of floating drilling and production technology. Knecht was previously vice president of engineering for Zapata/Arethusa Offshore Drilling and Diamond Offshore. Prior to joining Zapata, Knecht was in Exxon Production Research’s marine engineering department, involved in the areas of stability, station keeping, floating production and vessel evaluation/safety. He is a member of the ABS Special Committee on mobile drilling rigs and the DNV Rig Owners Committee. He was previously on the U.S. and International Association of Drilling Contractors’ delegations to the IMO during the revision of the mobile offshore drilling unit code. He holds a B.S. in engineering from Columbia University, and masters’ in both naval architecture and ocean engineering from the Massachusetts Institute of Technology.
ELDON ROBISON is manager of operations and regulatory compliance at Exmar Offshore Company. He has been involved in the offshore industry for 33 years, and has been with Exmar Offshore since 2006. Previously, he was manager of marine operations for TODCO, business development manager for Bureau Veritas, technical adviser for Delmar Systems, senior project engineer for Diamond Offshore, and marine superintendent for Zapata/Arethusa Offshore. Robison holds a degree in general engineering from the U.S. Coast Guard Academy. During his career with the Coast Guard, he was a plan reviewer for the merchant marine technical office in New Orleans and a deck watch officer on a USCG vessel in Alaska.
For other great articles about exploration, drilling, completions and production, subscribe to The American Oil & Gas Reporter and bookmark www.aogr.com.