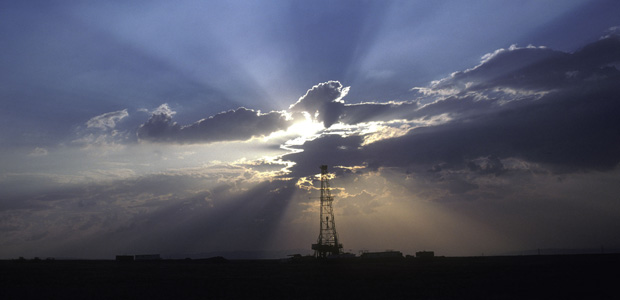
Next-Generation Systems Optimize WBM Performance In Horizontal Shale Plays
By Tim Beims
A decade ago, shales still were viewed as little more than nuisance formations that presented a litany of problems as operators drilled through them to reach underlying reservoir targets. Today, shales are target number one.
The U.S. Energy Information Administration notes in its Annual Energy Outlook 2010, “The growth in shale gas production is one of the most dynamic stories in U.S. energy markets.”
It is hard to argue that. Shales already are transforming lower-48 oil and gas supply trend lines. To get an idea what the future holds for emerging plays such as the Marcellus in the Appalachian Basin, the Haynesville in Louisiana and Texas, and the Eagle Ford in South Texas, one only needs to look at the play that started it all: the Barnett Shale.
Annual Barnett production exploded from 41 billion cubic feet in 1999 to 1.76 trillion cubic feet in 2009, according to the Texas Railroad Commission, with the Barnett well count jumping from 500 to 14,000 over that period–the vast majority of them horizontals since 2006. “Shale plays are changing everything,” affirms Roi Lam, group lead for Encana Oil & Gas (USA) Inc.’s Mid-Continent business unit. “It is amazing to be at the forefront of this technological evolution.”
Change has come to every facet of the reservoir development process–from high-resolution seismic imaging, to long-lateral horizontal drilling on multiwell pads and simultaneous multistage fracturing operations. Drilling fluids are no exception. The latest developments in mud systems are geared toward engineering a new generation of nontoxic, environmentally friendly water-based systems that have performance features that rival those of oil-based products.
Shale Drilling Issues
Geological, mechanical and hydraulic issues all come into play when drilling horizontal wells in shale formations, according to Lam. “As we identify where the fairways are located in shale reservoirs, we are finding that a lot of them go to deeper horizons,” he relates. “The fairways are the sweetest spots to drill, but in the Haynesville and Eagle Ford shales, for example, the fairways are also deeper and hotter. Because of that, the first fluid system challenge is temperature.”
In addition to economic and environmental considerations, geological, mechanical and hydraulic issues all come into play when drilling horizontal wells in shale formations. In the Haynesville–arguably the most demanding of the shale plays because of depths, high temperatures and the presence of acid gases–Encana is using oil-based muds as well as experimenting with high-performance water-based systems in long-lateral wells.
The second challenge, he adds, is being able to maintain the rheological properties of the mud in the lateral section to maintain lubricity and reduce torque and drag, especially with lateral lengths extending ever-farther into the target zone. “Proper mud properties are critical in the lateral to maintain the carrying capacity to lift cuttings to surface and prevent cave-ins during drilling to avoid stuck pipe,” Lam states.
From Encana’s perspective, Lam says the key is a fluid system with high native mud weights but low solids content–particularly low-gravity solids. “It is a trade-off between higher mud weights to control well bore pressures and lower solids concentrations to achieve faster penetration rates while minimizing waste and the need to use surface equipment such as centrifuges and dryers to reduce solids content,” he details.
The most fundamental fluids question is whether to drill with a water-based mud (WBM), oil-based mud (OBM) or a synthetic system, or a combination where one system is perhaps used to drill the vertical section and another to build the angle and drill the lateral. The answer is primarily a function of mitigating risk, according to Lam.
“I have to identify our goals for a particular well so I can assign risk to it. If a well is in an area without much well control or a lot geological uncertainty, we have to be more risk averse,” he explains. “However, if the well in a geologically quiet area with no faulting issues and some well control, I can be more aggressive because there is less chance of having target changes during drilling that would create a tortuous well path.”
Tortuosity, Lam notes, equates to torque and drag, which reduce the chance of getting casing to bottom. “The worst-case scenario would be a wildcat in an area with no good 3-D seismic or well control, because I would have no indication of how much faulting to expect,” he goes on. “The possibility of having to move the lateral up or down and left or right to hit the sweet spot would force me to use an OBM because of the risk of increased tortuosity. OBMs give the most repeatable performance across a wider set of parameters, and at this point, provide the best chance of getting casing and cement down in deep, hot and tortuous holes.”
Once enough penetrations have been made in an area to provide sufficient well control, however, Lam says WBMs can become the preferred alternative. “The more information I have, the more aggressive I can be. The more aggressive I can be, the more inclined I would be to use a WBM,” he avers. “Even though there may geologic complexity and the formation may be deep and hot, we can drill with a WBM as long as we understand the subsurface environment.”
Advantageous Qualities
Encana is experimenting with high-performance water-based systems in some of its operating areas, including the Haynesville–arguably the most demanding of the shale plays because of its depth and higher temperature profile, as well as the presence of acid gases.
“We are working to resolve some of the challenges of using water-based systems in more demanding horizontal shale drilling,” Lam reports. “You can run into problems if you push the application limits or use WBMs in younger shales that are highly water reactive, but WBMs exhibit qualities under certain conditions that are very advantageous for our drilling programs.”
He adds that Encana’s experience to date bodes well for high-performance WBM economics, considering the cost and logistical complexities of treating and disposing of cuttings from oil-based muds. “Factoring in all the cost and environmental considerations, WBM comes out ahead of OBM,” he confirms. “However, the caveat is the WBMs are advantageous only if you can achieve good penetration rates and get casing to bottom in a reasonable time. If those two things are accomplished, you can see definite advantages with a high-performance WBM.”
As with other operators, Encana is employing a “gas factory” approach with its shale play drilling and completion operations. In the Haynesville, Lam says the company is simultaneously drilling and fracturing six wells on each pad, but is considering increasing that to as many as 12 per pad. To optimize efficiencies, Lam says all the same intervals are drilled on each pad before switching out the mud system.
For example, he explains that a lignite WBM typically is used to drill Haynesville surface and intermediate intervals. The WBM is then recovered before displacing the active system with OBM to drill all six production laterals. “By drilling all the surface and intermediate intervals before we get to the production section, we avoid having to move fluids back and forth or clean tanks after every interval,” he reasons. “We also use the reserve pit as much as we can for WBM operations to recycle reserve pit water throughout the surface and intermediate hole sections.”
Whether using an OBM or a high-performance WBM, Encana’s objective is to recycle the same batch of fluid to drill multiple pads. “We may have to recondition the mud, but we try to use it on as many wells and pads as possible before building new mud,” he concludes.
Compounding The Challenges
Chesapeake Energy Corp. also knows a thing or two about getting shale wells to total depth, ranking among the most active drillers in the Barnett, Fayetteville, Haynesville, Marcellus, Bossier and Eagle Ford plays. “Shale drilling, in general, is difficult. And now we are drilling longer-lateral horizontals where hole cleaning, bore hole quality and stability, and friction compound the challenges,” says Darrel Overgaard, manager of drilling engineering for Chesapeake’s northern and eastern divisions, which include the Fayetteville and Marcellus plays.
The typical lateral length in Chesapeake’s Fayetteville wells is 4,500-5,000 feet, but Overgaard says the company is now pushing the lateral section in some cases to 7,500 feet. In such long-lateral wells, the fluid system challenges boil down to hole cleaning and lubricity/friction, he holds, noting, “If we get a lateral 5,000-6,000 feet and it becomes too difficult to steer or slide to make corrections, the drilling operation is done. That makes lubricity and hole cleaning critical to a well’s success.”
Because of their performance properties, OBM historically have been the preferred solution for long horizontal wells. “But the industry now is looking hard at water-based systems to achieve the goals of lateral drilling in shales,” Overgaard relates. “We rely on OBMs in more troublesome areas to inhibit sensitive shales that may become unstable with water-based systems.”
Synthetic systems provide another option. “Compared with OBMs and WBMs, synthetics have a higher cost per foot and require more maintenance,” Overgaard goes on. “However, synthetics and OBMs generally give us more reliable performance in the lateral sections than a WBM.”
Chesapeake is using both oil-based and high-performance water-based fluids in its Fayetteville horizontals. “We are using OBM in deeper areas of the Fayetteville, but we also have WBM field trials ongoing,” Overgaard relates. “In fact, we just finished a well in which both the vertical and lateral sections were drilled with a WBM. We believe we will be able to use WBM in many cases.”
When trouble is encountered in shale wells drilled with WBM, Overgaard says Chesapeake’s experience indicates the problems usually are related to hole stability. “We encounter lots of shale layers in long laterals, and some of them become unstable when reacting to water,” he reports. “If you cannot keep the hole clean and the friction coefficient factor low to keep pipe turning, wells will end short.”
The first consideration in mud selection for Chesapeake is matching a fluid to the drilling engineering plan to get the well to total depth. The second consideration, Overgaard says, is the environment and the associated cost and risk exposure. “The cost of OBM is increased by having to add closed-loop equipment and treat cuttings and transport them to the proper disposal site,” he says.
Cost Comparison
Although the upfront cost of high-performance WBMs tends to be higher than OBMs on a per-barrel basis, the reduced expenses associated with not having to dry and dispose of cuttings can have a significant impact on total expense, according to Overgaard. “Costs come out a wash between WBM and OBM,” he contends. “With the cost being more or less equal, the issue becomes balancing all considerations against the performance characteristics required to get to bottom.”
However, Overgaard says cuttings disposal can weigh heavily on the economics in some plays, where options may be limited by a lack of disposal facilities and cuttings may have to be transported long distances. “With cuttings drying and disposal costs, OBM can end up being less economical than WBM, which can require minimal cuttings treatment, and in some cases, can often be disposed of on site,” he points out.
Given the pluses and minuses associated with both systems, Overgaard says the optimal solution for long-lateral shale drilling would be a WBM with the performance properties of an OBM. “I think the industry is getting very close to having that capability with some of the new enhanced water-based fluids and lubricant additives,” he remarks. “We need the technology.”
He points to the MASTER CLEAR FLUID™ system from The Mud Masters Group as an example of a next-generation WBM. Chesapeake has used the MASTER CLEAR FLUID and the MASTER CLEAR MISTING SYSTEM™ in the Fayetteville play in both a liquid phase and in air drilling operations in a mist phase. “We have drilled two wells successfully with the liquid phase–including the lateral sections–and are currently using this product as a misting fluid to air drill the vertical sections,” Overgaard details.
Overgaard says the misting system is achieving improved penetration rates to the top of the Fayetteville, where drilling switches to an OBM for the horizontal turn and lateral. “We have considered the possibility of air drilling to total depth with the misted system, but the properties of the shale probably prevent that, especially in the curve, where faulting and tectonics cause stability problems,” he comments.
A mantra in Chesapeake’s shale drilling programs is “reclaim, recycle and reuse,” according to Overgaard. “That is a big component in our operational strategy. As part of a broader manufacturing process, efficiently recovering mud and carrying it over to the next well to reduce waste is a very important part of continuous operations in pad drilling,” he maintains.
Chesapeake’s average recovery factor for both OBM and WBM in a typical six-well pad in the Fayetteville Shale is 80-90 percent, Overgaard adds. “We get the same amount of use out of both types of systems, but one of the benefits of WBM is dilution,” he notes. “When solids build up in the mud, it is easier and more cost effective to dilute WBM because you simply add more water as opposed to adding mineral oil or diesel.”
Performance Attributes
Buddie Livingston, an independent drilling consultant, has worked with Chesapeake to apply the MASTER CLEAR FLUID in the Fayetteville Shale. He says several key performance attributes drove the development of the environmentally friendly, water-based system.
“It had to inhibit the well bore like an OBM, but be environmentally safe and nondamaging to the reservoir,” he expounds. “The formulation is highly inhibitive, and keeps sensitive shales dry by suppressing water hydration. Plus it has a high lubricity coefficient and low HP/HT fluid loss. It is phenomenal how well it works in shale wells.
Even though it is a water-based system, one of the key benefits of the new MASTER CLEAR FLUID™ from The Mud Masters Group is the ability to suppress shale hydration. This image shows Fayetteville Shale samples in a mixture of 50 percent MASTER CLEAR FLUID and 50 percent water (left) and in 100 percent water (right) after eight days of exposure, with the shale in 100 percent water completely collapsed.
The system was first applied in Buda/Georgetown horizontal drilling in East Texas by Houston-based Signa Engineering, Livingston reports. “There are a lot of nasty shales in the vertical sections of those wells. To come in at the top of the Buda, the curve has to drill through the water-sensitive Midway and Maness/Dexter shales (part of the Woodbine series), which can slough and come apart with WBMs,” he describes. “The system has successfully drilled Buda horizontals with MASTER CLEAR FLUID concentration of 20-35 percent of the total liquid volume.”
Livingston says 95-100 percent of the liquid phase fluid can be recovered from each well and recycled. “Gel water is pumped ahead of the final cement job to push the drilling fluid out of the well. It stores very easily, and does not sour or have bacteria problems,” he comments.
The next application was Chesapeake’s Fayetteville Shale operations, Livingston recalls. “The system worked well in the liquid phase, but the real story to me is the results with the misting system, which was a blessing that came while Chesapeake was looking for a way to improve drilling the Hale sands and shales above the Fayetteville,” he states. “The proactive approach was to use a diluted portion of the fluid system in storage from the last liquid phase mud job, and it was a misting success.”
The Hale interval is made up of very hard, high-compressive strength sands in the intermediate vertical section, as well as shales. Livingston says penetration rates on fluid can be as low as four-five feet an hour. While drilling below the surface casing shoe, these shales can soak up the water produced from the sand sections, causing the shales to deteriorate.
“Chesapeake was drilling vertical intermediate-hole intervals of 3,000-3,500 feet, then having to bring in a big rig to mud up with OBM, and drill slowly to the top of the Fayetteville at 5,000-7,000 feet to the kickoff point for the lateral section,” he remarks.
Since applying a 1-10 percent concentration of the new fluid system in the misting water recipe to air drill the vertical interval, Livingston reports 68 wells have been drilled to the top of the Fayetteville. “These vertical sections have drilled deeper and faster with fewer problems, saving an average of two-three days for every vertical section drilled,” he remarks. “The Mud Masters Group is improving the mist recipe with an additional product and mixing tank prior to the mist tank.”
A key benefit is that the drill cuttings require no treatment or special disposal, Livingston stresses. “The cuttings have no environmental aftereffects,” he affirms.
Livingston suggests the system’s inhibition characteristics also give it intriguing possibilities in fractured limestones and sandstones. “Natural fractures in limestones can be as small as a human hair, yet produce a lot of hydrocarbons. A single water drop can get into one of those fractures and have a tensile strength of 20,000 pounds, preventing it from producing,” he says. “Even though this technology is water based, it encapsulates a large percentage of the water to prevent it from entering microfractures.”
Meeting All Criteria
Charles R. “Rick” Stone, chairman and chief executive officer of Signa Engineering Corp., also has been working with operators to apply MASTER CLEAR FLUID. According to Stone, the “ideal” drilling mud should be nontoxic and environmentally friendly, have a native mud weight of 10 pounds per gallon or higher, contain no suspended solids, provide superior lubricity, and have a native viscosity at ambient temperature.
“This system meets all five of those criteria, plus it has application as a drilling fluid, a spotting fluid, a packer fluid, and a hydraulic fracturing fluid,” he enthuses. “This is the water-based fluid I have been searching for my entire 30-year career as a drilling engineer. It is like the holy grail of fluid systems.”
Although it has no suspended solids, the system is 70-78 percent dissolved solids by volume, he claims. “It is clear; you cannot see any solids because they are dissolved completely,” Stone imparts. “You can read a newspaper through a vial of the fluid, yet it has a high native mud density.”
The high solids content acts like a sponge to pull water from the formation and dehydrate shales during drilling, Stone goes on. “Free water usually goes the other way, from the mud into the shale. That is the typical source of hydration problems with water-based muds that cause mechanical failures,” he asserts. “This new system provides the same positive effect of using a saturated saltwater phase in an OBM, but without the risk of mechanical failure caused by sodium chloride overly dehydrating the shale and creating brittleness.”
Stone says he has used The Mud Master Group’s fluid system on five wells, all of them Buda horizontals where the water-sensitive Midway, Dexter and Maness shales in the vertical intervals historically dictated using OBM. Next up, he says are horizontals in the Eagle Ford Shale and a deep, high-temperature Smackover exploratory well in Northeast Texas with a planned depth of ±20,000 feet.
“We are conducting hot rolling and high-temperature testing to determine the system’s stability point. The testing will give us an indication of what to expect, and we will push the limits. The temperature at total depth in the exploratory well is expected to be 380 degrees F. I do not think we will be able to go to 380 degrees, but I expect to get somewhere between 315 and 350 degrees F before we have to displace to OBM,” he reveals. “We have a casing seat appropriately located at that temperature/depth range.”
Although the patented MASTER CLEAR FLUID system has not yet been used as a frac fluid, Stone reports that he has plans to do so soon, blending it with saturated chloride brine to enhance the dehydration effects.
“The dehydration capabilities are pretty incredible as a completion fluid, another large facet of this product.” he remarks. “A frac job creates a macrofracture network. When you can create microfractures in the branches of the macrofractures by dehydrating the shale, you will have a better stimulation. And with no suspended solids other than proppant, there is no free water.”
Clay-Free System
Newpark Drilling Fluids is rolling out a clay-free, polymer water-based system engineered for shales. In fact, the research and development effort behind the high-performance WBM originated in response to operator requests from the Haynesville Shale, according to Del Leggett, Newpark’s director of client relations.
“The original base formulation was designed specifically for Haynesville geology, which means it has to have good thermal stability to tolerate the high temperatures, and be able to stand up to naturally occurring contaminants, particularly carbon dioxide and hydrogen sulfide. It also has to be recyclable and reusable,” he says, pointing out that the biggest design challenge was coming up with a polymer suitable for the extreme conditions. “The combination of high bottom-hole temperatures and CO2 tears up WBMs with conventional clays and bentonite.”
The system also was engineered to maintain hole cleaning and lubricity in the lateral sections of Haynesville horizontals. “The clay-free technology contains a powerful blend of lubricants that provides OBM-like lubricity,” Leggett reports. “The chemistry involved in this system is absolutely novel and the polymer is completely new to drilling fluids. Technology this dramatically unique comes around very rarely in the mud business. It ultimately saves operators money while optimizing drilling performance and protecting the environment.”
The development effort included using core analysis to characterize not only the low-permeability Haynesville, but also the overlying shales–including the Bossier–through downhole simulator cell testing, says Leggett, who notes that the fluid system is displaced at intermediate casing depth to drill several thousand feet of vertical hole before making the turn at the top of the Haynesville to drill laterally.
“The Haynesville is one animal, and the shales above it are quite another,” he contends. “Therefore, we analyzed differences among the Haynesville, Bossier and other formations in the vertical section to determine what kinds of demands might be placed on the fluid system. Essentially, the system was designed to drill the Haynesville laterally and the Bossier vertically.”
Since the first of the year, the system has been used by six operators to drill nearly 40 Haynesville horizontals in eight Louisiana parishes and Texas counties with bottom-hole temperatures exceeding 360 degrees, Leggett updates. “It would not be getting that kind of operator acceptance if it did not work extremely well,” he insists. “And if it can work well in the Haynesville–the most challenging shale to drill–it can work just as well in other plays.”
In fact, Leggett says Newpark is working to qualify the system for the Marcellus, Fayetteville, Eagle Ford, Barnett and Bakken shales using the same preserved core analysis approach to characterize individual shales and downhole simulator cell testing. “We want to make sure the system is fully vetted for every application for which we recommend it. Before we will use the system in other shales, we will go through the same investigative process as in the Haynesville,” he holds. “The difference is that we are not starting from square one. We are starting pretty far down the road already with a very good system.”
Customized For Shales
Malcolm Ellice, Halliburton Baroid’s global drilling fluids technical services manager, says the company’s new SHALEDRIL™ family of water-based muds is customized for reduced dilution, enhanced bore hole stability, CO2 tolerance, fracture sealing, etc., to match the unique requirements of the particular shale being drilled.
Halliburton Baroid’s SHALEDRIL™ family of water-based fluids is customized to match the unique requirements of the particular shale being drilled. SHALEDRIL F, introduced in the Fayetteville Shale in 2009, is engineered partly to mitigate instability issues in the microfractured shale to prevent spalling, swelling, delamination and erosion. At left is a scanning electron microscope image of the Fayetteville/Morrow after soaking 24 hours in a typical inhibitive WBM, with only slight microfracture sealing compared to the image at right, which shows apparent microfracture sealing after soaking 24 hours in SHALEDRIL F™.
“The first formulation–SHALEDRIL F–was introduced in 2009 in the Fayetteville Shale, and the system now is being used in the Haynesville, Eagle Ford, Barnett and Marcellus,” he reports. “These fluids permit operators to drill horizontal shale wells with WBM to get away from the added environmental complications of OBMs.”
To custom engineer a fluid for each shale play, Ellice says Halliburton Baroid analyzed shale samples and tested various chemistries to obtain the best results. Because shales are variable within a given play, he adds that part of the system design process going forward is to obtain local samples to build a database and further customize the fluid using the specifics of the shale at the drilling location.
“We conduct rigorous studies on shale samples before the premixed fluid goes to the well to account for potential swelling, inhibition and microfracture plugging,” Ellice explains. “Polymers and inhibitive mechanisms are used to avoid lamination of the clays, and particulate materials plug microfractures so that the impact of the drilling fluid is maintained at the surface skin, and fluid and filtrate invasion are minimized.”
The goal is to keep the shale in a native state to maintain stability while drilling. “We want to keep the shale as undisturbed as possible, even though we know that after the well is drilled, the reservoir shale is often hydraulically fractured to create permeable flow paths for enhanced gas productivity,” says Ellice.
To illustrate the concept of customization, Ellice notes that SHALEDRIL F and SHALEDRIL H use the same WBM base, but that SHALEDRIL H has an alkaline chemistry to negate acid gas influxes and other mechanisms to enhance thermal stability in Haynesville wells. The chemistry of SHALEDRIL F, on the other hand, is designed to mitigate characteristic instability issues in the microfractured Fayetteville to prevent shale spalling, swelling, delamination and erosion, he adds.
The fluids are designed to drill the entire well bore, from the vertical section to the lateral. “We are achieving lubricant qualities that are moving these water-based systems toward the performance of OBMs, while keeping the shales stable through the vertical, curve and lateral sections,” Ellice claims. “Both performance and cost issues are crucial to the design features, as well as the environmental and recyclability benefits associated with WBMs. For example, the chemistries of the systems are designed so that the cuttings can be landfilled.”
Ellice estimates that 25-30 wells had been drilled with the system through July. “That number will multiple sequentially in the near future,” he avers. “We are seeing good performance everywhere. In each shale play, the performance indicates we are going in with the right solution the first time.”
Comparing the cost metrics of the new system with OBM, Ellice says, “We think it is on the right side of the line when you take into account all the environmental and waste management issues.”
All Options On The Table
M-I SWACO is concentrating its R&D efforts for horizontal shale drilling on water-based systems, but Darryl Cullum, director of technical services, says the company still is keeping all options on the table.
For instance, Cullum says M-I SWACO is using SILDRIL™ silicate systems in the Fayetteville; the chrome-free ENVIROTHERM™ high-temperature system in the Haynesville; and low-solids undispersed WBMs, invert emulsions and a paraffin-based synthetic in the Marcellus. “We understand there are different problems associated with each shale play, and different solutions for solving those problems,” he remarks. “We look at each application on a case-by-case basis to come up with the best solution, which is sometimes a conventional fluid.”
Catalin Aldea, the director of new technology at M-I SWACO, agrees. “We have seen a lot of success using high-performance WBMs, and while our priority is on advanced WBM technology, we still will see OBM and synthetic applications for the foreseeable future,” he states. “At the end of the day, our job is to find the best solution available to achieve the optimal technical performance and overall project results in demanding shale applications.”
M-I SWACO is concentrating its R&D efforts for horizontal shale drilling on high-performance water-based systems, but it is still keeping all options on the table for long-lateral horizontal wells, including using SILDRIL™ silicate systems in the Fayetteville, chrome-free ENVIROTHERM™ high-temperature fluids in the Haynesville, and conventional invert emulsions and paraffin-based synthetics in the Marcellus. An M-I SWACO laboratory technician is shown here performing a rheology check of a WBM system.
According to Cullum, one key is focusing on the big-picture challenges of shale plays to create all-encompassing systems rather than stand-alone fluid products. “An example is our environmental solutions group, which is looking at ways to recover and treat frac water so that it can be reused in WBMs,” he reports. “When you look at all the challenges together instead of individually, it only makes sense to reuse frac water as a WBM base fluid. That, of course, rules out an OBM, because an invert emulsion system is not going to use much recovered frac water.”
As part of that philosophy, the company also is working to reduce waste from drilling operations, whether using water- or oil-based muds. In the Marcellus Shale, Cullum reports that the company has demonstrated the capability to recover base oil from an invert emulsion fluid containing high solids content. “The RECLAIM™ process can recover virgin base oil from used OBM that otherwise would be waste,” he states. “Depending on fluid density, the base oil can range anywhere from 60 to 70 percent by volume, which reduces waste by 60-70 percent.”
Among the R&D projects at M-I SWACO is a cooperative program with nanotechnology researchers at the University of Texas at Austin and Rice University to infuse WBMs with nanoparticles that create a water-impermeable membrane on the face of shale formations to mechanically block water from entering microfractures, according to Quan Guo, manager of industry initiatives. “We want to tackle issues such as shale inhibition from both chemical and mechanical perspectives,” he says. “Chemical additives can minimize shale/water interaction, but we also want to develop technology to improve inhibition through mechanical means.”
Cullum concludes by noting that although OBMs offer the “easier path” to extending lateral reaches to 7,500 feet and longer because of their lubricities and no reaction with shales, WBMs are nevertheless the clear choice for the future.
“The obstacles are much greater for WBMs in long-lateral shale wells, but that is where the technology is going. That is why our R&D efforts put so much emphasis on WBMs. We are cognizant that while invert emulsions may be used now in the Marcellus and other shales, the long-term answer is WBMs,” he reiterates. “It is up to us as a service company to come up with the water-based technologies operators need in these plays.”
For other great articles about exploration, drilling, completions and production, subscribe to The American Oil & Gas Reporter and bookmark www.aogr.com.