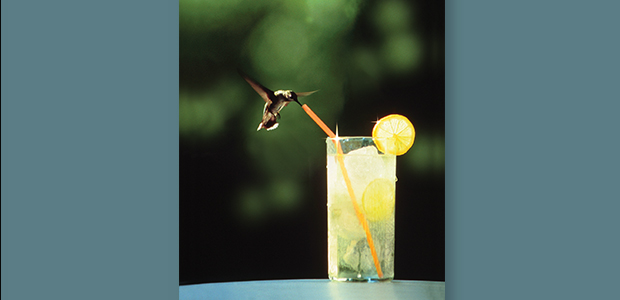
Surface Treatment Extends Plunger Life In Pinedale Anticline Test
By Jonathan Robins, Christopher Aguilar, Anthony Mason and Jason Freeman
A field study designed to evaluate the wear resistance, abrasion resistance and corrosion resistance of boron-carbide (B4C) treated steel plungers found that the B4C treatment more than tripled plunger run life.
PureWest Energy came to this conclusion after conducting an eight-well test in conjunction with Endurance Lift Solutions, a provider of technology-enabled artificial lift components. The study was designed to compare the longevity of B4C treated 4140 steel plungers (using data collected during the study) with the run life of plungers made of plain 4140 steel (using operating company historical data). The study was conducted over 14 months, from April 2020 through June 2021, on eight wells in the Pinedale Anticline field of Wyoming.
The B4C treated plungers ran an average of 414 days compared with 131 days for untreated plungers, resulting in a mean run time improvement of 283 days. The extended plunger life span reduced replacement cycles and equipment costs more than 67% during the study.
Before the study, PureWest relied on plain 4140 bar stock plungers in each of the eight wells. Historical data showed that plunger run times ranged between 76 and 163 days per well, at which time the plungers had to be replaced.
In practice, PureWest measures plungers every three-six months (earlier if well production declines) to determine if a plunger needs to be replaced, which occurs when the plungers have degraded so much that they can no longer provide an effective seal (Figure 1). The minimum acceptable outer diameter is 1.88 inches. New bar stock plungers have an outer diameter of 1.90 inches. Before the field study, PureWest had to change plungers two-five times a year on each of the eight wells.
Field Study Details
The field study deployed new B4C treated 4140 steel plungers, all of which had an initial outer diameter of 1.90 inches (Figure 2). The plungers were evaluated every three-six months and replaced if the outer diameter was less than 1.88 inches. PureWest recorded the number of run days achieved before plunger replacement and the production levels of each well across the 14-month period.
During eight months of production on eight separate wells, only five B4C treated 4140 plungers required replacement because they no longer met the minimum outer diameter of 1.880 inches. The plungers in these five wells still achieved an average run time improvement of 244 days when compared with the plain steel plungers placed down hole before the study.
The three remaining wells with B4C treated plungers were still running at the study’s conclusion. These wells recorded an average run time improvement of 348 days compared with the plain steel plungers (Table 1).
The B4C plungers had an average run time of 414 days compared with 131 days for plain steel plungers, representing a mean improvement of 283 days–an increase of 3.2 times. This increase in performance eliminated 18 tool replacement cycles across the eight wells studied.
Annual plunger replacements dropped 64% once the B4C treated ones were in the field. The run time improvements and less frequent replacements translated into significantly lower overall operating expenses, even after accounting for the additional cost associated with the treatment.
Why Replacements Occur
Plunger seal efficiency is critical in achieving optimal production. The plunger’s rise and fall during each production cycle causes plunger wear over time. The inevitable result of wear is poor seal performance, leading to diminished production. To sustain production, worn plungers must be replaced.
Sandy, corrosive and highly deviated wells are known to accelerate the mechanical wear, abrasion or corrosion of plunger lift system components. When a plunger wears, production suffers. Plunger failure also leads to higher operating expenses and lost production from equipment replacements and downtime.
Plunger replacement cycles vary from well to well. The goal of any operator is to achieve as much run time and production as possible from each plunger so operating expenses stay in line with production. To accomplish this, operators may optimize the well for the plunger application or change equipment designs and materials. Operators also may coat or plate the plunger itself to extend its run life. B4C treatment, which is neither coating nor plating, is a promising option.
Historically, using plain 4140 steel plungers on its wells in the Pinedale Anticline, PureWest was performing 3.5 plunger replacements per well per year on average. B4C-treated 4140 plungers cut annual plunger replacements to an average of 1.25 per well and increased average plunger run life from 113 days to 414 days.
By extending plunger run life in all eight wells, the B4C treatment helped PureWest reduce equipment and labor costs, and dramatically reduce overall downtime and lost production associated with maintenance and repair events.
Mechanisms For Longevity
The plungers treated with B4C lasted so long because the treatment alters the base 4140 barstock’s surface characteristics. The treatment creates a slick, hard, intermetallic boride layer that (unlike coatings or platings) does not alter the dimensions of the part. The treated surfaces’ slickness, hardness and corrosion resistance all contributed to the plungers’ longevity by protecting them from abrasion and corrosion.
The slick surface exhibits a lower coefficient of friction than the base metal or current industry coatings, which translates into permanent lubrication regardless of load. This low coefficient results in superior wear resistance, a key factor in the field study wells.
The surface hardness created by thermal boron-diffusion has been shown to outperform chrome, nickel carbides and standard hardness coatings, according to lab tests and field reports. The surface hardness of treated parts acts to reduce abrasion and mechanical wear.
With near-zero porosity, the treated surface exhibits excellent corrosion resistance. In lab tests, B4C treated couplings had no signs of surface loss after spending 48 hours submerged in acid. The field study confirmed that the treatment’s ability to elevate corrosion resistance can give parts longer run times.
Treatment Process
B4C treatment is a form of surface hardening in which boron is diffused into the steel substrate. The process results in a diffused layer of boron at the surface of the substrate (Figure 3). While the treatment is not appropriate for some materials, such as copper, aluminum and resulferized steel, it works on several ferrous and nonferrous materials used in the oil and gas industry.
Endurance Lift Solutions’ B4C treatment technology, which the company markets under the trade name BLAZE®, combines proprietary chemistry with heat to enhance the steel part’s surface. Boron atoms migrate into the treated material during the treatment process, converting the surface to a condition such as iron, nickel, cobalt or chrome boride, depending on the substrate alloy.
It’s worth stressing that B4C treatment is not a coating or plating that is applied to the surface. Instead, it is a thermal diffusion treatment that creates an intermetallic boride layer within the metal surface. This intermetallic layer cannot crack or peel.
Unlike coating or plating methods, the diffusion process does not change parts’ dimensions. This eliminates the cost, time and potential for mistakes associated with under-machining parts to accommodate a new coating or plating layer.
Plungers are not the only artificial lift equipment that could benefit from B4C treatments. The same technology can add longevity to trim kits, couplings, rod lift parts, pump components and related equipment.
JONATHAN ROBINS is lead production engineer at PureWest Energy. He has 19 years of operations experience throughout North America, including work in North Alberta, British Columbia, Alberta, Utah, Texas and Wyoming. Robins’ experience spans a range of production applications, including deep Devonian sour waterfloods, heavy oil, carbon dioxide floods and deep gas wells. He has applied several artificial lift techniques, including rod pumps, electric submersible pumps, jet pumps, plunger lift, gas lift and gas-assisted plunger lift. In his current role, he oversees production engineering for more than 3,400 wells and 650 million cubic feet of gross gas production for PureWest.
CHRISTOPHER AGUILAR is a senior production engineer at PureWest Energy with 13 years of multidisciplinary engineering experience. Aguilar’s background includes completion work in the Woodford and Barnett shales, as well as reservoir engineering in the Permian Basin and Pinedale Anticline, where he was responsible for forecasting, budgets and reserves project economics. Aguilar’s artificial lift experience spans rod lift, plunger lift and gas lift operations. As senior production engineer, he has served PureWest in the Uinta Basin as well as the Pinedale Anticline. He holds a B.S. in petroleum engineering from Montana Tech of the University of Montana.
ANTHONY MASON is senior vice president of specialty products for Endurance Lift Solutions, where he oversees the deployment of BLAZE® surface treatment technology across all forms of artificial lift. Mason’s prior industry experience includes various roles at Hanover Compressor Co., Exterran and Dover Energy. In addition to a BBA from Texas A&M University, Mason holds a master’s in technology commercialization from The University of Texas at Austin.
JASON FREEMAN’s responsibilities at Endurance Lift Solutions focus on corporate sales. He serves Houston-based company accounts, working on all forms of artificial lift. Freeman’s prior industry experience includes various roles within Baker Hughes and Dover Artificial Lift. He has worked in oil and gas fields in Alberta, Saskatchewan, California, Utah, Colorado, North Dakota, Oklahoma and Texas. Freeman holds a bachelor’s in international business from the University of Tulsa.
For other great articles about exploration, drilling, completions and production, subscribe to The American Oil & Gas Reporter and bookmark www.aogr.com.