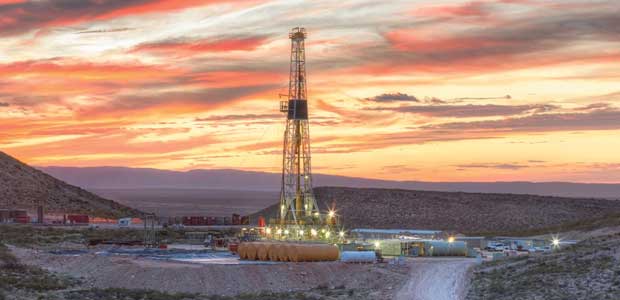
Top Permian Operators Leveraging Technology To Drive Bottom-Line Success
By Danny Boyd, Special Correspondent
The development of tight oil plays in the Permian Basin during the past decade has elevated the century-old workhorse of U.S. hydrocarbon supply into a global stallion at the center of technological innovation and operational excellence. And while a global economic shutdown knocked the Permian off course for a bit, activity has bounced back as operators launch into 2022 with restored confidence and renewed energy.
By every conceivable metric, business conditions across the basin have improved consistently month over month for the past several quarters. The most tangible reflection of that gradual, but marked, improvement is Permian oil production. According to the U.S. Energy Information Administration, oil production in January was up by 39% compared with the start of 2021, demonstrating the Permian is firmly back on the growth track.
What’s more, EIA says output is on course to eclipse pre-pandemic levels in February, topping 5 million barrels a day and representing a fivefold increase since 2012. Natural gas production is also back on the rise, now exceeding 15 million cubic feet day, or nearly double the basin’s gas volumes 48 months ago. This is shaping up to be another banner year in the Permian, and technology is at the center of it all.
Continual innovations in horizontal drilling, stimulation and completion, artificial lift, well site automation, water management, machine learning and emissions monitoring are among the advancements helping operators of all shapes and sizes capture a treasure trove of opportunities in the stacked tight oil benches of the Midland and Delaware basins. No matter the play or the player, high tech is standard practice in West Texas and Southeast New Mexico.
Drilling Solutions
As one of the Permian Basin’s largest and most established producers, Pioneer Natural Resources Company has drilled thousands of wells in its core Midland Basin operating area. But the company now is applying state-of-the-art technology to build on its deep operational expertise and elevate drilling productivity, efficiency and safety to new levels, says Larry Fizer, vice president of Permian drilling.
Specifically, Pioneer is using rig automation, real-time remote data communications for rotary steerable systems, ahead-of-the-bit stuck pipe alerts, real-time dynamic downhole modeling and other solutions to safely drill better wells in less time and at lower cost. “From a drilling perspective, continuous improvement and delivery of faster, less expensive wells is paramount,” Fizer says. “We see technology as an avenue to improve the economic returns of our Midland Basin wells.”
Last year, the company performed its first pilot of an electric rig, high-line powered to the lease and with all the capabilities of a diesel-powered rig, he reports. The six-well pad went smoothly with no downtime, and the company’s capital projects team has been installing high-line infrastructure to help meet a future goal of drilling all wells with electric rigs, according to Fizer.
Pioneer Natural Resources is using rig automation, real-time remote data communications for rotary steerable systems, ahead-of-the-bit stuck pipe alerts, real-time dynamic downhole modeling and other solutions to safely drill better wells in less time and at lower cost across its Midland Basin leasehold.
Deploying electric rigs and adopting other technologies to boost efficiency stem from a systematic method of evaluating high-grade potential technological solutions, he explains. Project leads calculate near-term and long-term economics and leadership then assesses the benefits of deployment and provides feedback.
On a weekly basis, Fizer says his team reviews all ongoing technology appraisal projects. Once approved, projects move into a trial phase before being rolled out strategically and continuously monitored, with weekly updates and progress reports providing the latest performance results, Fizer elaborates.
“We are very analytically driven and study the economics and the benefits associated with any changes we make to our program,” he remarks.
Rotary steerable systems help greatly in geosteering to the formation target and deliver longer laterals as Pioneer continues to push the bit farther through a wider implementation of 15,000-foot laterals this year and an average greater than 10,000 feet during the past few years, Fizer points out.
That drilling is monitored and supervised by Pioneer’s performance drilling center (PDC) at its headquarters in suburban Dallas. At the PDC, all rigs active on Pioneer well sites located some 300 miles to the west are monitored around the clock, with drilling engineers and geologists working 12-hour shifts to guide drilling decisions and rig activities for optimized performance. Using live wellbore and rig data, Fizer says, bottomhole assemblies are geosteered precisely to make sure laterals are spotted where they need to be within targeted benches.
Vendors such as Schlumberger, Baker Hughes and Phoenix also collaborate with Pioneer to monitor and continuously improve drilling efficiency, he adds.
Pioneer works closely with drilling business partners to consistently improve automation that increases performance on some tasks formerly done manually, Fizer goes on. Through a program called Back to Drilling, automation has proven more efficient when resuming drilling after a drill pipe connection has been made, outperforming a driller in increasing the rotary back-to-drilling speed, bringing up pumps and applying the bit to the formation, he explains.
“We have seen a real decrease in damaged tools and rotary steerable systems now that we are letting the automated system resume drilling after making a connection instead of humans trying to do it right every time,” Fizer says.
For about a year, the company has deployed three automated mud skids that continually monitor fluid properties and provide real-time data to help with calculations for well planning.
Efficiencies in recent years, including rig movement, have boosted average per-pad well counts, from three a couple years ago to better than four today, Fizer says. Pioneer was drilling actively on multiple six-well pads in early February.
The drilling team focuses on building predictive alerts to mitigate risk from downhole complications, Fizer continues. For instance, washout alerts or other details provided by machine learning analyses are driving progress with real-time data on everything from weight on bit to pump pressures and rates, he says.
Capturing Synergies
In keeping with its diversified roots, Coterra Energy Inc. is capturing technological synergies between its core operation areas, and freely adopting new technologies and sharing findings internally to identify the best drilling and completion approaches across a broad position that includes 234,000 acres in the Permian Basin, says Vice President of Business Units Michael DeShazer.
The Houston-based company emerged in 2021 from the combination of Cabot Oil & Gas Corp. and Cimarex Energy Co., bringing together operations in Permian oil, Appalachia gas and Oklahoma liquids-rich assets. At the outset, operations teams from both legacy companies immediately worked to understand how each approached assessments, drilling, completion and production operations and technologies without prejudging or insisting on mandates, says DeShazer, who oversees business units in the Permian and Anadarko basins.
Coterra Energy Inc. is leveraging a number of innovative strategies and solutions across its Permian asset base, including tankless production facilities equipped with vapor recovery units to reduce venting and flaring.
“It is amazing to see how fruitful it can be and how many ideas are shared when you open the doors and take down the barriers between teams,” he says.
Some practices and applications vary from the dry gas window of the Marcellus Shale to the multilayered intervals in the oil-rich Delaware Basin, but Coterra’s business units are drilling two miles down and two miles out and will continue to learn from one another, DeShazer confirms.
The combined company maintains a willingness, birthed in predecessor companies, to deploy the latest innovations in the Permian, he stresses. For instance, he says, Cimarex was among the first in the Delaware Basin to deploy off line cementing that allows rigs to be skidded over to begin drilling a new well without first cementing the casing, which is done later by a dedicated cement crew. “The technique allows for substantial savings over the course of a project,” DeShazer reports.
Technology Solutions
On the drilling front, the company routinely experiments with new bits and has been involved in several trials using one-run drilling systems to bore wells’ curve and lateral sections without tripping, he reveals. Geosteering is deployed routinely to complement extensive seismic and well log data.
Although completion designs are kept close to the vest, Coterra is flexible, leveraging machine learning algorithms to help its experts assess variations within structures to help determine lateral landings, well spacing and stimulation plans for the Delaware Basin’s Bone Spring and Wolfcamp benches, DeShazer says.
A premium is placed on having as much discriminant data as possible to explore changes in outcomes determined by even the slightest variations in proppant or water, instead of automatic adjustments to both simultaneously, he says.
DeShazer adds that extensive in-house data on legacy completions helps fill gaps in public information that lacks details on cluster spacings and shots per foot while including lateral lengths and proppant and fluid aggregates.
Fiber optic and downhole cameras gauge outcomes during fracs, including perforation erosion, with a confluence of technologies allowing the company to tailor each frac design (cluster spacing and count can vary by stage) to most effectively divert fluid evenly across a stimulation stage, he says.
Throughout the process, the company focuses on incremental returns. “For example, an eight-well pad and 10-well pad may have similar net present values for potential oil and gas production, but drilling those two extra wells can mean spending more money without any additional gain,” DeShazer notes.
Pump selection after initial flow ebbs includes electric submersible pumps deployed in more oily areas in the northern Delaware Basin and gas lift in gassier properties in the southern Delaware, with gas lift supply supported by Coterra’s own midstream operation, he says.
In addition to the focus down hole, technological innovations to reduce emissions above ground include an electric frac fleet, a move toward electric compressors, tankless facilities with vessels that allow vapor recovery units to pull off gas vapors, and a dedication to a steadfast goal of eliminating routine flaring, DeShazer concludes.
Pragmatic Approach
Any mention of the Henry name in the Permian Basin invokes one of the true pioneering giants of tight oil technology, and Midland-based private operator Henry Resources LLC is proud to continue that legacy by deploying new technology alongside a pragmatic approach to carefully assess what does and does not work, says Operations Manager Patrick Cohorn.
With Henry Resources deploying proven technology on a Permian position approaching 30,000 gross acres in the Midland and Delaware basins, a key is knowing the neighbors when reviewing datasets in new areas, he says.
Henry Resources LLC is deploying multivariate analytics driven by artificial intelligence and machine learning to optimize lateral spacing and completion designs in its Midland and Delaware basin operations.
“We try to keep an open line of communication and good relationships with everybody around us to learn what is working for them and determine if it can be a mover for us and improve one of our processes,” Cohorn explains.
When considering new innovations, the company has worked closely with a third-party research and development firm, Darcy Partners, to evaluate new technologies and systems, he says. Otherwise, well logs and data from its own extensive archive and information on offset wells from neighboring leases obtained through data trades, help the company site wells, determine lateral landings and design completion programs, Cohorn says.
To keep laterals on target, employees use StarSteer™ geosteering software that gathers real-time data from the rig from logging-while-drilling and gamma ray logs. Additional software called Mobilize™ provides more drilling analytics, Cohorn details.
Petro.ai analytics using machine learning and artificial intelligence architectures allow the company to plug in completion designs, price scenarios, well costs and other factors to obtain multivariate analysis on optimal well spacing. Through machine learning and internal evaluation of offset well results, the company chose same total vertical depth interwell spacing of approximately 1,000 feet. This translates into 11 wells a section targeting the two Wolfcamp B benches in Upton County, Tx., in the southern Midland Basin, he says.
On completions, geometric designs in Upton County typically include consistent stage spacing of 150-180 feet and 8-12 clusters per stage across laterals as long as 12,500 feet to allow for uniform yields from the geologically consistent bench underlying its acreage, Cohorn explains.
“Optimum frac designs in our Upton AOI include 2,500-3,000 pounds per foot of mostly 100-mesh sand, although some wells are stimulated with a combination of 70% 100-mesh and 30% 20-40 mesh sand,” he explains.
In southern Upton County, where wells have lower bottom-hole pressures, ESPs are installed after about a month, while wells located deeper in the basin can free flow for six-nine months before a pump is required, Cohorn says.
“Our preference is to flow them as long as we can,” he explains. “We are not fans of going in and killing a well when it still has good bottom-hole pressure and is able to flow just to install an ESP and get the rates up through the roof.”
To reduce emissions, vapor recovery units are installed on all facilities and the company is looking to install VRU towers, Cohorn says. To reduce emissions and increase safety by keeping trucks off the roads, the company pipes most of its oil and all its freshwater and produced water through its own system.
Data management and ease of access for the entire organization is crucial, and Henry has taken steps to optimize that, he reveals. Using a corporate SQL server relational database, Henry is able to push and pull data across the organization in a way never before possible. Layering software such as Spotfire, ArcGIS Online, Actenum DSO and other programs on top of SQL, the data can be brought together seamlessly and multiple design, performance and timing scenarios can be evaluated in short order, he says.
“Operational technology is really important and we are always keeping our head on a swivel for what may be available, but internal evaluation technology that has come to bear over the past couple of years has made a big difference in our ability to be nimble and take advantage of opportunities as a company,” Cohorn comments.
Off The Charts
Through the use of rich legacy data and deployment of the latest drilling, completion and production technologies, Houston-based Callon Petroleum Company continues to build on a Permian position that now exceeds 90,000 acres.
“When you look at the quality of our inventory, it is off the charts for a company of our size,” affirms Chief Operating Officer Jeff Balmer. “It includes good-quality, stacked inventory that has a high degree of confidence and a high degree of profitability.”
The confidence stems from a combination of extensive data and insights from acquired positions and its own proven history of project execution, bolstered by an in-depth understanding of parent-child well relationships in infill drilling projects, he says.
Callon’s 2019 acquisition of Carrizo Oil & Gas included detailed knowledge of the basin’s vertical stacks through microseismic and rigorous geologic understanding of what constituted barriers between benches such as the Wolfcamp B and C, he says. The addition also brought with it a strong set of data analysis and predictive performance.
The acquisition of Primexx Energy Partners last year included a trove of 3-D seismic data and an in-depth understanding of diverse components of the geologically complex Delaware Basin, Balmer continues. Callon’s combined team utilized AI for an extensive review of all the data, including scenarios for geological barriers, well spacing, completion designs and the timing of well development to gauge potential depletion, and set regional parameters from information obtained in data trades with nearby operators, he explains.
Tailored Development
The results from incorporating all the data into a machine-learning-driven predictive tool are enabling Callon to tailor full-scale development to maximize recovery and optimize capital efficiency, he says.
“Instead of seeing a lot of one-off, three-well pads throughout an area, you will see a lot of larger projects consisting of multiple three- or even four-well pads next to one another in the same area targeting multiple benches throughout the stack in order to maximize capital efficiency and recovery,” Balmer notes. “When we come in, we use a reasonable approach to set the stage for inventory. When you look at the analysis, it is a boutique, pad-by-pad development program for that specific area that has been extremely successful for us.”
Callon Petroleum Company is incorporating machine learning-driven predictive analytics to tailor full-scale development using a boutique, pad-by-pad approach that maximizes recovery and optimizes capital efficiency.
With the aid of predictive analysis and updated parameters, completion designs can vary throughout a multiwell project, he adds.
For example, engineers have the leeway to push more proppant and fluid through the initial toe phase on an 11,000-foot lateral to achieve a more radial frac development. “We can’t drill to the lease line, but can ensure that we are fully stimulating the rock volume out to the lease line,” Balmer comments.
The robust inventory assessment allowed Callon to continue developing lower zones during the 2020-21 downturn instead of focusing chiefly on shallower benches that are less expensive to drill and complete, he reveals.
Planning and operating groups are one in the same, meaning employees who input data and deploy the software to build an inventory assessment of the company’s 2,500 wells are the same employees who implement the drilling and completion program and who are responsible and accountable for its performance, he says.
Ongoing analysis also is a part of the company’s strategy to predict production outcomes with extreme precision, Balmer says. How precise? A predictive model performed in November varied from actual output by 5 barrels of oil equivalent a day out of more than 100,000 boe/d actually produced, he reports.
Twin Rig Approach
For privately held FireBird Energy LLC of Fort Worth, technology includes the latest in drilling and assessment systems to determine how best to develop an expanding footprint in the western Midland Basin, says Chief Executive Officer Travis Thompson.
With the addition of 21,000 leasehold acres from Chevron in December, the company is using petrophysical data from 400-500 vertical legacy wells and seismic across its now 72,000-acre position in Texas’ Ector, Midland, Crane and Upton counties to optimize well planning, he says.
Execution is enhanced by pairing two rigs on developments to strategically manage reservoir pressure and lower rig cycle times while targeting the Jo Mill, Lower Sprayberry and Wolfcamp A and B zones, Thompson reveals.
Twinning the rigs allows for simultaneous development of a large portion of a 1,280-acre unit from side-by-side pads, with each rig drilling three-four wells apiece before both move on in tandem, he elaborates. Laterals are typically about two miles long, or roughly the length of combined sections.
FireBird Energy LLC’s strategy in the western Midland Basin uses twinned drilling rigs for simultaneous development of 1,280 acres from side-by-side pads, with each rig drilling three-four wells at faster overall total cycle times.
The twinned rig practice reduces the time from a dollar spent to a dollar returned by 30%-40%, Thompson reports. “Those four zones vary across the position, but we know where each of them are and feel confident with two rigs and can add to that as we integrate throughout the year,” he offers.
Frac designs typically include 1,900 pounds of proppant per foot and pump rates of 80-100 barrels of fluid a minute, with stage spacing ranging from 150 to 180 feet, depending on the well, he says, although FireBird engineers vary designs as needed.
With horizontal development, the company is constructing centralized tank batteries, building out infrastructure and developing a five-megawatt solar field on its own surface acreage to provide the majority of field power, all in keeping with its quest to remain a low-cost and low-emission producer, Thompson goes on.
With a focus on practically and efficiently deploying technologies, the company continues to seek bolt-on opportunities that bring value both to FireBird and larger players around them, he adds.
“Building a sustainable business is a key tenet of what we are doing, and building the infrastructure that supports that is a key part of it,” Thompson concludes. “Having the redundancies and making sure we are being good stewards and good partners are all essential to what we do. I do not know that we are necessarily pushing the envelope on technology as much as we are using all of the proven technologies at our disposal.”
For other great articles about exploration, drilling, completions and production, subscribe to The American Oil & Gas Reporter and bookmark www.aogr.com.