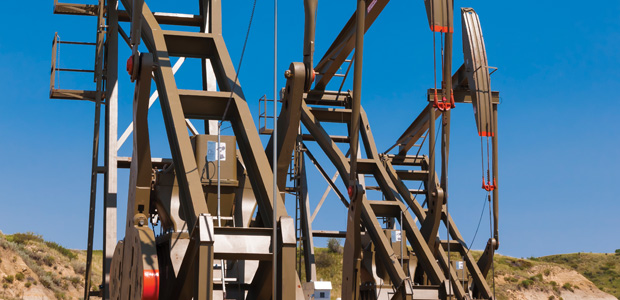
Wireless Networking Optimizes Artificial Lift, Production Performance
By Tom Bass and Al Majek
AUSTIN, TX.–Oil and gas companies have made major strides in optimizing well productivities and operating efficiencies in onshore U.S. unconventional plays during the past few years. As a result, shale gas and tight oil reservoirs that not long ago were regarded as high-cost alternatives have been transformed into a new class of low-cost, high-yield resources capable of changing the global energy landscape.
To date, the impressive gains in shale gas and tight oil productivities and economics largely have been driven by advancements in well construction, as operators leverage technology to continually improve horizontal drilling and hydraulic fracturing in ultralow-permeability rock. Drilling and completion times have been slashed even as laterals have grown longer and stimulation designs have incorporated higher stage counts with more fluid and proppant.
Innovations in wireless networking technology are enabling a similar transformative shift in the production phase, creating new efficiencies and optimizing asset performance on the scale of dozens, hundreds or even thousands of producing wells across a lease position.
As the industry broadens the scope of production operations to full-field development targeting multiple stacked horizons, the ability to improve well economics over time while efficiently producing the full reservoir volume–and recovering the maximum reserves in place–will differentiate the top-quartile operators in a given play, be it the Marcellus, SCOOP, Wolfcamp or Niobrara.
Increasing well productivity is undoubtedly the largest lever for improving well economics, and wireless technologies can provide the operational backbone to achieve efficiency and sustainable cost savings. Wireless technologies help operators reduce costs through efficient facility construction and scalable architectures, delivering future flexibility for field developments and production optimization. Operators that standardize on wireless capabilities can improve production, reliability, emissions and safety, and react quickly and decisively to mitigate production issues or capitalize on field development opportunities.
Moreover, when applied as part of a broader strategy with complementary technologies such as advanced artificial lift optimization and produced fluids management software, wireless capabilities give producers the means to dynamically respond to changing well production compositions and flow patterns to maximize production and enhance profitability. That is critical given many resource plays’ operational constraints, including lift gas availability, limited compression horsepower, separator capacity, water handling capacity, sales line capacity and more.
A lack of information about well operations constitutes the most common cause of unmet production goals. Some critical wellheads on a pad may have automated monitoring, but the cost barriers to implementing traditional automation and control solutions mean many wells do not. Cost-effective wireless solutions make it possible to remotely monitor and control production, helping operators to meet their production goals while continuously optimizing well operations, reducing environmental and safety incidents, and streamlining operations and resource allocation in the field.
Realizing these benefits is not simply a matter of access to well data; it is about having the right data at the right time to make quick and informed decisions. Some of the most fundamental measurements for onshore tight oil and shale gas wells are tubing, casing and bradenhead pressures. Like blood pressure in the human body, these data provide a reading of a producing well’s health at any point in time and indicate potential problems that can lead to downtime. Adding measurements of injected gas, chemical injection, electric submersible pump, rod pump and plunger lift well dynamics greatly improves well performance visibility.
Wireless pressure transmitters provide accurate, around-the-clock monitoring of casing/tubing pressures and chemical tank levels. Flowing tubing pressure is a measurement that production engineers typically check on a daily basis along with production volumes to analyze well performance. A sudden or dramatic drop in tubing pressure signals that a well has encountered a problem. Casing pressure measurement monitors the annular space between the tubing and casing, and a pressure build in the annular space indicates a potential tubing leak. Bradenhead pressure is another vital measurement that can identify a well integrity issue.
Artificial Lift
At the heart of any production operation is the artificial lift system. In shale gas and tight oil plays, artificial lift performance is challenged by highly variable production rates and multiphase production flows consisting of varying percentages of liquids and gas. Depending on well conditions and flow profiles, operators are using rod pumps, electric submersible pumps, jet pumps, multiphase pumps, plunger lift, gas lift and other forms of artificial lift. The most important measurements vary by lift system, but the main goal for any artificial lift solution is to maximize production while minimizing capital expenditures, maintenance and energy use.
For example, the key measurements for rod pumping are motor temperature, motor vibration, hydrocarbon leak detection and backpressure control. On the other hand, the key measurements for plunger lift are wellhead pressure; bradenhead pressure; gas line pressure, temperature, differential pressure and flow; liquids line pressure, temperature and flow; vibration monitoring; and plunger detection.
New technology has streamlined plunger lift monitoring and control. Technologies such as smart automation and online data management allow operators to monitor and control plunger lift systems remotely, without regular field visits. Wireless sensors can be used to notify plunger arrival at the wellhead, with a late plunger indicating problems such as a potential timing issue. Once the plunger arrives, a remote terminal unit can control a flowline choke valve to optimize well output.
Accurately measuring flow on a gas wellhead that utilizes a plunger lift system can be a formidable challenge, and one with significant financial consequences if not done properly. Although a plunger lift system solves the problem of resuming the flow of gas in mature wells, it creates its own set of challenges. With every plunger cycle, the system subjects flowmeters to large pressure spikes with wide flow rate variations. As the plunger cycle repeats, it makes it impossible for conventional transmitters to measure the flow of gas accurately. Utilizing a highly accurate multivariable pressure transmitter with extended range capability allows operators to increase wellhead production, capture the gas flow cycle in its entirety, and avoid lost profits.
Smart automation can go a step further by providing real-time adjustments of various control parameters to maximize production with virtually no operator intervention. One typical example is its ability to react to flow rates that drop below the rate needed to lift fluid from a plunger lift gas well. Critical velocity, as determined by the well-known Turner-Coleman equations, is correlated to the critical rate necessary to lift fluids from a wellbore. Flow rates below the critical rate cause liquids to accumulate in the well to the detriment of gas production. Local automation devices can perform the required calculations consistently and end a plunger lift cycle before the gas flow drops below this important value.
Gas lift is growing in popularity in both oil and liquids-rich gas plays. Figure 1 shows a schematic of gas lift using injection flow rate, casing pressure and production tubing pressure at the surface as parameters to monitor and optimize well operations. In oil wells, continuous gas lift injects a percentage of associated gas output through the production string and into the liquid column, thereby reducing the backpressure or hydrostatic pressure of the liquid column acting against the production zone pressure. In gas wells, intermittent gas lift periodically removes the entire liquid column.
Although several design parameters must be considered for efficient gas lift operations, the most relevant are ensuring that appropriate gas flow rates and pressures can be maintained during lift operations. For gas wells, a suitable gas slug and velocity must be reached in the tubing for liquid removal with minimal fallback. In oil wells, the key is maintaining optimal injection rates to accommodate changing production characteristics. In both scenarios, overinjection wastes sellable gas and can lead to operational problems. Key measurements for optimizing gas lifted well operations are wellhead pressure, bradenhead pressure, gas lift pressure, gas lift temperature, gas lift flow and vibration monitoring.
Handling these various parameters and making timely adjustments becomes an extremely demanding job for operators with an ever-growing inventory of wells. By monitoring a well’s actual production, automation packages using optimization algorithms can find the desired balance between the parameters and execute adjustments accordingly. The effect is equivalent to having someone at the wellhead 24 hours a day, seven days a week, thereby creating a virtual workforce to augment operator personnel.
Central Facilities
One of the paradigm shifts in resource play development is centralized production facilities shared by multiple pads and even leases. A central facility can be sized to process the initial production of a series of wells, and as those wells decline with time, new wells are tied in to keep the facility processing at full capacity.
The initial capital investment in a central facility plays a significant role in the return on investment in a field development program, and the sheer size of these facilities implies high maintenance and operating expenditure that also can chip away at profitability. Fortunately, wireless technologies are helping operators maximize central facility designs from both an initial CAPEX and a long-term OPEX perspective.
With service costs trending upward to meet growing demand as the pace of drilling and completion activity picks up in onshore resource plays, producers are facing the issue of how to mitigate cost increases for all types of well services. For central production facilities, the most effective answer is to design a facility that can be installed more efficiently.
As an example, consider the case of a simple central facility with 30 storage tanks, 14 three-phase separators, seven heater-treaters, one sales gas compressor, two gas lift compressors, a flare, a vapor recovery unit and a pipeline lease automatic custody transfer unit. A typical instrumentation and electrical crew of 30 will assemble and install the cable tray, cables and junction boxes, and terminate wires at the instrument and programmable logic controller.
A 30-person crew working for 20 days will cost $256,000, not including loop checks and commissioning time. Most of the labor is spent pulling cable, installing the cable tray, installing junction boxes and terminating wires. However, equipment with wireless instrumentation will make a crew more efficient, and some customers report it cut time requirements–from when a crew is mobilized to when facility commissioning activities start–by 75 percent. For the hypothetical 30-person crew example, a 75 percent time reduction would slash $192,000 in labor costs.
Another unique benefit that wireless technology brings to central facility operations is the binary troubleshooting technique. A device either is able or unable to communicate to the gateway. A communication problem is solved by fixing the transmitter or adjusting the line of sight. For a wired device, there are issues such voltage drop with distance, or incorrect or faulty instrument and junction box wiring. Although some operators may not view these examples as sources of major cost savings, it is worth remembering that wireless technology is designed to drive efficiency and leverage operator experience to more significant activities, as opposed to solving communication problems.
Separation, Custody Transfer
Separation is a fundamental link in the production process at centralized facilities. As illustrated in Figure 2, using wireless temperature transmitters, pressure transmitters and level switches gives operators the ability to measure and optimize separator equipment and ensure proper set points.
Improper temperatures on heated separators can reduce separation efficiency by not allowing emulsions to break up, inhibit reaching correct Reid vapor pressure limits for transportation requirements, or boil off valuable natural gas liquids and reduce crude oil quality. Excessive separator pressure can increase well back pressure on artificially lifted wells, reducing production and leaving too much gas entrained in the oil. Insufficient separator pressure can cause excess NGLs to be lost to the gas and reduce crude quality.
Level switches ensure safety shutdown of a well in the event of a separator high- or low-level alarm. High levels can lead to spills or send liquids to the flare, while low level conditions can cause excessive gas venting to tanks. Sensors also monitor pressure relief valves for releases should the separator become overpressurized.
Managing oil inventories and custody transfer operations is critical to minimizing fiscal risk and lost and unaccounted-for production. Managing produced water disposal transfers to validate hauling volumes can reduce lease operating expenses by preventing errors and overcharges. The ability to detect oil in the water tank from a separator upset can prevent oil losses to the water hauler. With insight into tank levels, operators can improve the efficiency of oil and water hauling logistics, reducing operating expenses.
Applying wireless level monitoring lets producers gain continuous insight into tank levels, minimize high level alarms and prevent spills. The API MPMS Chapter 18.2 standard (Custody Transfer of Crude Oil from Lease Tanks using Alternative Measurement Methods) allows operators to use automatic tank gauging for custody transfer. This keeps workers off the tops of tanks to eliminate safety risks from manual tank gauging and reduce measurement uncertainty. Operators also can also detect oil/water interfaces to prevent oil losses and a high-level switch prevents spills and enhances safety at pad tank facilities.
Minimizing emissions and improving storage tank safety are critical for central production facilities, especially given the scope of operations and stricter tank emission regulations. Pressure vacuum relief valves and emergency vent/vacuum relief valves prevent tank damage caused by abnormal situations and pressure surges. By monitoring the activity (opening/closing) of relief valves, operators can ensure a quick response to upsets and so minimize emissions and fines.
Wireless emergency and pressure vacuum relief valve monitoring detects the open or closed position of the pressure and/or vacuum-side relief valve. Integrating a wireless transmitter enables quick identification and response to potential difficulties, reducing unintended emissions that may create environmental issues, while also preventing tank damage. Wireless gas detection and hydrogen sulfide monitoring detects the presence of dangerous levels of H2S and other hazardous vapors near the tank hatch to protect workers from exposure.
Network Controller
As producers optimize their full-field drilling and development programs, the latest in wireless technology is pushing the industry to adapt more unconventional approaches to automating production facilities. Utilizing cost-saving wireless instrumentation is one way to keep up with busy field work schedules and production volumes. An additional piece of the puzzle is integrating an advanced wireless remote terminal unit to run a central facility. A distributed RTU network integrates with radio technology to provide transparent data connectivity to enable shared, distributed control of multiple devices across a wide geographical area (Figure 3).
Integrating a WirelessHART® communication module with the RTU allows wireless instrumentation data to come in seamlessly, since all devices are part of the network. A wireless IEC 62591 standard interface speeds seamless integration and installation. With the interface installed, the RTU automatically detects WirelessHART devices as they are added to the network. No site survey is required, making it easy and fast to set up wireless field instrumentation. Additionally, the integrated interfaces have been optimized for a low-power environment, minimizing investments in power infrastructure.
This seamless integration means data do not need to be mapped out, saving time in the commissioning process before startup and during a retrofit or expansion of an existing facility. The typical daily rate for a commissioning technician is between $800 and $1,000 and a technician typically spends five days on location to commission a facility. This assumes a producer will spend an average of $15,000 to commission a facility.
Using an RTU with an installed IEC card has shortened commissioning times significantly, reducing commissioning budgets 60-70 percent in some cases. If the producer plans to build 20 facilities in one year, the cost savings to commission them may be $100,000 or more per facility.
Wireless technologies can have a demonstrable positive impact on lease operating expense line items such as repairs and maintenance, production chemicals, and labor. Together, these three cost components account for 45 percent of total LOE on a per-barrel-of-oil-equivalent basis. By applying wireless automated solutions, oil and gas companies are achieving significant productivity improvements on multiwell pads and central facilities while simultaneously optimizing production performance, improving equipment reliability, reducing safety risk exposure and enhancing capital efficiency over the full life cycle of a field development project.
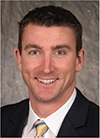
TOM BASS is the wireless business development director at Emerson Automation Solutions Rosemount, headquartered in Shakopee, Mn. Since joining Emerson in 2006, he has served in several industry focused business development roles. In his current capacity, Bass is responsible for leading business development for Rosemount Wireless and manages the Plantweb™ pervasive sensing application portfolio.
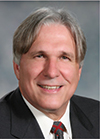
AL MAJEK is the oil and gas production area technical manager at Emerson Automation Solutions. He has more than 35 years of experience in designing, manufacturing and deploying automation technology in the oil and gas industry. Majek is a certified project management professional and a registered professional engineer.
For other great articles about exploration, drilling, completions and production, subscribe to The American Oil & Gas Reporter and bookmark www.aogr.com.