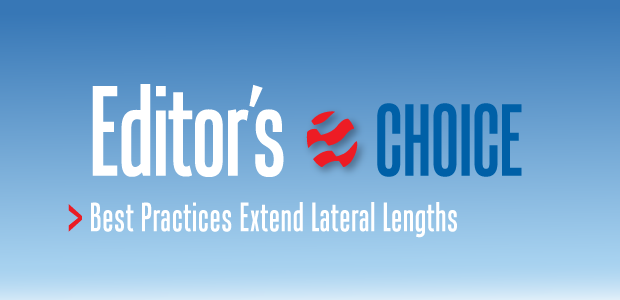
Best Practices Extend Lateral Lengths
By Joshua Doak, Matthew Kravits, Michael Spartz and Pat Quinn
CANONSBURG, PA.–Range Resources drilled the Renz No. 1 Marcellus discovery well in Washington County, Pa., in 2004 and commenced horizontal drilling in the play in 2006. Through mid-2018, Range had drilled more than 1,050 wells in Pennsylvania. The lateral lengths of the 850 Marcellus horizontals drilled between 2006 and 2016 averaged 3,950 feet, varying between 1,500 and 11,000 feet.
In 2018, the average lateral lengths of the 100 wells on Range’s drilling schedule in Southwest Pennsylvania were estimated at 9,830 feet for the dry gas area, 9,550 feet for the wet gas area and 11,550 feet for the “super rich” gas area. In the first quarter, Range drilled the two longest laterals to date in the Marcellus: one measuring 17,875 feet, and the other 18,129 feet. Both were drilled in Washington County, where the vertical Renz No. 1 had been drilled 14 years earlier.
The success of the extended-lateral program is rooted in Range’s extensive experience in the play, but specifically dates to late 2016, when the Marcellus drilling program began focusing on developing core acreage with longer laterals. As a result, the average lateral length for the 200 wells drilled in 2017 and the first half of 2018 increased to 9,450 feet, and laterals now routinely extend beyond 12,000 feet.
To accomplish this step change in well design, Range Resources’ Appalachian drilling team evaluated the processes that had been in place for 7,000-9,000 foot laterals to determine what operational practices would need to be revised to drill and case 12,000 to 18,000-plus foot laterals (Figure 1). The team focused on rig upgrades, directional tools, drilling fluids, casing flotation and other best practices, and then implemented field trials to evaluate extended lateral practices. Over the 12-month period of revising processes and making upgrades, Range drilled 34 horizontal wells with laterals longer than 12,000 feet (Figure 2).
Consistent use of best practices and systematic equipment upgrades has led to improved performance year after year in Range’s Marcellus operations, with wells progressively drilled in less time and at a lower cost. The focus has been on the key performance indicator of cost per lateral foot. One of the keys to successfully implementing extended-lateral drilling was drilling longer horizontals while continuing to achieve the goals of safe, environmentally compliant, sustainable and cost-efficient Marcellus development over time, including maintaining the KPI trend shown in Figure 3.
From 2006 to 2015, Range had drilled only five wells with lateral lengths exceeding 10,000 feet. The challenges faced on those wells and the time required to reach total depth raised concerns that multiple changes would be needed to successfully drill extended laterals in a continuous program. Consequently, in early 2016, the drilling team began planning a well pad with laterals exceeding 12,000 feet (including one longer than 14,000 feet) with drilling scheduled for the fourth quarter of that year. Comprehensive studies, followed by field tests, were implemented in preparation for the extended-length lateral drilling. The focus was on:
· Rig selection;
· Directional tools;
· Drilling fluids;
· Casing flotation; and
· Best practices.
Rig Selection
Range has utilized various types of rigs with different capabilities throughout the evolution of its Marcellus development program, including super singles with the capacity to drill laterals to ~6,000 feet, high-performance walking rigs capable of drilling laterals to ~10,000 feet, and walking triples rigs with a maximum lateral length capability of ~20,000 feet. The progression of rig capability has been instrumental in achieving longer laterals.
Because of their versatility and efficient design, Range had vast success with super singles with 650-horsepower drawworks, 1,000-horsepower mud pumps, 150-ton top drives, 450-kilowatt generators, 4½-inch range III drill pipe, and 300,000 pound capacity masts. However, as drilling shifted toward laterals longer than 5,000 feet, it became evident that rig selection needed to be re-evaluated along with the number of wells drilled per pad, location size and wellhead spacing.
The second fleet iteration came in the form of a high-performance design with enhanced horizontal drilling capabilities. These rigs had 1,000-hp drawworks, 1,600-hp mud pumps, 500-ton top drives, 1,365-kW generators, 5.0-inch drill pipe, and 750,000-pound capacity masts. The rigs used range II drill pipe to build stands (triples) with a rack-back capacity of ~15,000 feet, and had the ability to walk ~20 feet an hour with a rack full of pipe.
These second-generation rigs have met the challenges associated with drilling 10,000-foot laterals with great success, drilling 805 Marcellus horizontals (one of the rigs drilled an 11,146-foot lateral). However, with the first 14,000-foot lateral planned, permitted and placed on the drilling schedule, the capabilities of the rig fleet once again came into focus in 2016 and the team determined another upgrade was necessary.
While larger hook load, power generation, flow rate, rotational speed, pipe handling and other capabilities were needed, the size of the rig was a critical consideration, especially with it becoming routine to return to sites with producing wells to conduct infill drilling. The upgraded rigs would have to be able to seamlessly fit within existing operations on pad locations and also be efficient to mobilize given the challenging Appalachian terrain.
Ultimately, Range decided to add a rig in late 2016 that features 1,500-hp drawworks, two 2,000-hp mud pumps (7,500 psi maximum rated working pressure with 4.5-inch liners), a 500-ton top drive (37,500 foot-pounds maximum continuous drilling torque capability), three 1,365-kW generators, 5.0-inch drill pipe, and a 750,000 pound capacity mast, capable of racking back 21,500 feet of drill pipe made up into stands. A second rig was added in March 2017.
Since upgrading the fleet with these rigs, Range has been able to meet the rigorous demands of continuous improvement by focusing on stability of personnel and monitoring KPIs to achieve program goals. Range successfully drilled 16 laterals longer than 10,000 feet in 2016, 47 wells in 2017, and 16 through the first seven months of 2018. In total, the rigs drilled 83 Marcellus laterals in excess of 10,000 feet through the first half of 2018, including the 18,129-foot well in Washington County. The team also has noted a 171 percent improvement in the amount of lateral footage drilled per rig in 2017 versus 2013.
Directional Tools And Fluids
With shorter laterals, the Marcellus horizontal program used a PDC bit, positive-displacement drilling motor, bent housing for directional control, and a mud pulse measurement-while-drilling tool. As average lateral lengths grew, it became increasingly challenging to slide drill effectively and hold consistent tool face. At that point, both rocking and agitator-type oscillating tools began to be deployed to assist in breaking static friction between the wellbore and drillstring, and help transfer energy to the bit. However, using rocking and agitator oscillating tools had practical limitations and heightened risk in laterals greater than 7,000 and 10,000 feet, respectively.
Eliminating the need to slide drill was mandatory to overcome frictional concerns in long laterals. Another driving force behind the move to rotary steerable tools was the decision to reduce geosteering target windows by 50-100 percent in an effort to improve well productivity. The team concluded that rotary steerable tools would be required to meet the new goals of the Marcellus program.
Rotary steerable tools provide precise directional steering for tight-target windows, and the ability to fully rotate the drill string throughout the drilling process reduces friction between the drill pipe and wellbore to minimize tortuosity, torque and drag in extended-lateral wells. Rotary steerables also enhance hole cleaning while drilling, improving ROP and stability. By combining rotary steerable tools with the right rig design and drilling fluid, Range has kept wellbores in the target zone for 99 percent of lateral footage drilled in 14,000-plus foot horizontals.
Adopting rotary steerable tools to drill extended laterals contributed to another critical design: switching from the high-chloride, water-based fluid that had been used with positive-displacement motors to a diesel-based mud. Modeling indicated a significant reduction in friction and torque by replacing the saltwater polymer-based mud with the OBM system with better shale inhibition and lubricity characteristics.
Both fluids were tested on a four-well pad in which the same rotary steerable tools were run, changing only the mud type. The wells in the study that were most comparable had 10,042 and 10,150-foot laterals and similar trajectories. The well that used the WBM recorded 9,000 foot-pounds more torque than the well drilled with the OBM. Over the past two years, the diesel-based fluid has proven crucial to successfully drilling laterals longer than 10,000 feet utilizing rigs with higher-horsepower and rotary steerable tools. Wellbore stability has improved drastically and the team has observed numerous performance improvements.
Those improvements include a dramatic increase in daily footage rates since switching to rotary steerables and OBM. On average, lateral footage averaged less than 2,000 a day prior to 2016. In fact, prior to 2016, the most lateral footage drilled in a 24-hour period was 4,344 feet. Since implementing the design changes, daily footage rates have averaged more than 3,400 feet. From 2017 through July 2018, Range recorded more than 30 days when lateral footage rates eclipsed 5,000 feet in 24 hours, including two days with more than 6,000 lateral feet drilled.
Casing Flotation
While drilling a record-setting lateral length is exciting, the process is all in vain if the production casing string cannot be run to bottom and cemented in place for the completions team to successfully stimulate the well. To ensure success, Range is utilizing casing flotation technology on a vast majority of its wells.
When running a long string of casing, increased drag considerations must be taken into account. If the drag associated with running casing is modeled to reach a critical limit in which the pipe will not be able to be slacked off to bottom, a casing flotation sub can be utilized to achieve a desired set depth with minimal operational changes.
A flotation sub can be placed strategically in the casing string to aid in running casing to bottom. With a single fluid system, a specified length of casing is left empty (air-filled) with the area above the flotation sub filled with fluid to aid in weight transfer. In the lateral, a buoyancy effect acts on the casing because of the difference between the drilling fluid and air filled portion of the casing, helping “float” the casing to bottom.
After the casing is landed at the desired depth, depending on the type of flotation sub used, the sub is opened or ruptured to allow the lower portion of the casing to fill with fluid. The air typically is allowed to swap with the fluid-filled portion of the casing string, and carefully circulated back to surface, where it is bled off in a controlled manner. After the void is fully filled to surface, circulation begins to condition the wellbore before cementing the production casing string.
Hole Cleaning And Tripping
A major obstacle faced in drilling extended laterals is ensuring the hole is cleaned appropriately before tripping and running casing. A study of wellbore cleaning was performed, focusing on the best parameters to aid in designing an optimal process to clean wellbores, including pump rates, rotating speeds, high-density mud sweeps and drill pipe reciprocation.
As lateral length grew in 2014-15, abnormal amounts of wellbore issues were encountered. After investigating problems such as stuck or lost BHAs, casing running issues, lost circulation during cementing, etc., it was found that the hole cleaning parameters had to be revised. An in-depth review determined that flow rates and RPM needed to be increased while drilling.
After drilling to total depth, circulation at TD and the landing point were increased and maintained within specific parameters. The increased parameters also included a weighted sweep (2.0 pounds/gallon over mud weight) at the start of the final bottoms-up circulation at TD and pipe reciprocation at a set speed.
Tripping procedures also were revised. The focus on shorter laterals had been on tripping fast to get the wellbore cased and cemented as quickly as possible. With extended laterals, there came a point at which pulling the drillstring off bottom without needing the drilling contractor’s overpull approval was unachievable. In those instances, back-reaming was the recommended method to get off of bottom. Range’s first two 15,000-foot laterals used back-reaming to trip out of the hole after reaching TD. In both wells, the drillstring encountered tight hole spots while tripping out that required back-reaming to continue out of the hole.
On the third 15,000-foot lateral, back-reaming operations resulted in the drillstring getting stuck and leaving the BHA down hole. A thorough investigation was completed to determine the cause of the stuck BHA. It found that the drillstring was back-reamed out of the hole at a higher speed than recommended. Even with back-reaming, at that speed, the BHA was pulled into a cuttings bed that ultimately packed it off. New back-reaming standards were implemented to limit tripping speeds and overpull in tight spots.
When overpull/tight spots are encountered, the new procedures include tripping back below the tight spot, pumping and rotating at set parameters, and circulating a minimum of one bottoms-up. If the shakers do not clean up, a bottoms-up continues pumping until the shakers are clear of cuttings. At that point, the BHA continues tripping out of the hole on elevators.
With lateral lengths extending to 18,000 feet, additional planning and engineering is necessary to minimize risk during drilling and tripping procedures. The first of Range’s 17,000-foot laterals included procedures such as increased circulating time at TD and preset back-reaming and circulation parameters based on insights gained from previously drilled 15,000-foot laterals. Once the drilling rig could pull on elevators, the rig circulated for an additional planned time before tripping out to run casing and successfully cement the wellbore.
A similar plan was put in place for the 18,000-foot lateral, which was drilled to TD without any issues. Circulating and tripping procedures from the previous 17,000-foot well were utilized to provide smooth tripping out of the wellbore. The production casing was run to TD using a flotation device, followed by cementing operations. These procedures, based on lessons learned from past experiences, allowed this record-setting well to be successfully drilled, cased and cemented.
The focus on drilling practices has enabled faster drilling rates and less days spent on each well, despite drilling much longer laterals. The increased performance results in rigs drilling more lateral feet a year, which means fewer rigs are required for improved capital efficiency in Range’s long-term development of the Marcellus. The new processes and procedures the drilling team put in place to drill record Marcellus lateral lengths in 2018 will continue to be utilized as Range drills more extended laterals in the Appalachian Basin in the future.
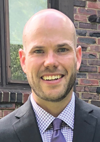
JOSHUA DOAK is director of drilling at Range Resources-Appalachia in Canonsburg, Pa. He joined Range in 2010, serving first as a drilling engineer and then as drilling engineering manager. Doak began his career in 2004 as a drilling and development engineer at EQT Production. He holds a B.S. in petroleum engineering from Marietta College.
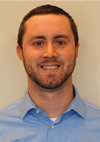
MATTHEW KRAVITS is a drilling engineer at Range Resources-Appalachia. He joined the company in 2011 as a production engineer prior to working as a drilling engineer in both the Marcellus and Utica shales. Kravits holds a B.S. in petroleum engineering from Texas A&M University.
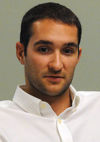
MICHAEL SPARTZ is a drilling engineer II at Range Resources-Appalachia. He joined Range in 2012 as a production engineer. Spartz subsequently has served the company in a variety of drilling, facilities and reservoir engineer roles. He holds a B.S. in petroleum and natural gas engineering from Pennsylvania State University.
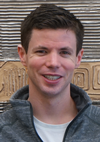
PAT QUINN is a drilling engineer II at Range Resources-Appalachia. He joined Range in 2014 working in the Mid-Continent division. Quinn was a drilling rig supervisor for CONSOL Energy before joining Range. He holds a B.S. in petroleum and natural gas engineering from West Virginia University.
For other great articles about exploration, drilling, completions and production, subscribe to The American Oil & Gas Reporter and bookmark www.aogr.com.