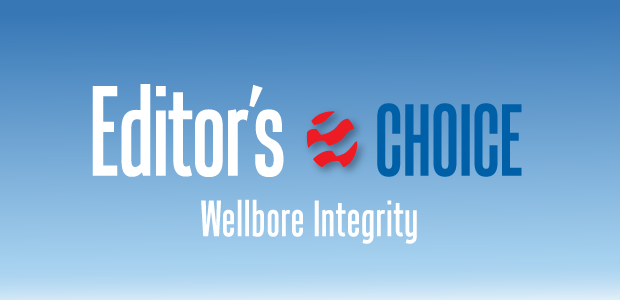
Better Cement And Reliable Repairs Advance Wellbore Integrity
By Colter Cookson
In worst case scenarios, wellbore integrity failures can be catastrophic for a company’s reputation and the industry’s license to operate. Rare as those scenarios are, the repair costs and inefficiency associated with more routine integrity issues, such as breaching casing collars during perforating, can erode a well’s profitability.
Despite wellbore integrity’s importance, engineers and service companies must find ways to balance risk with cost. Today, they also are grappling with more challenging downhole environments as operators drill longer laterals and target deeper benches.
Fortunately, service companies say the industry is getting better at achieving wellbore integrity, diagnosing issues that occur, and making the necessary repairs. The companies note that a proper cement job is essential to integrity.
According to Joseph Huwel, president of U.S. cementing and coiled tubing at Nine Energy Service, cement is getting both harder to find and more expensive. While he predicts availability will improve quickly, he cautions that costs will continue to climb.
The rising costs come in part from a boom in road, bridge and foundation construction, but Huwel cites at least two other factors. “Manufacturing cement is energy intensive, so as energy costs go up, so do cement costs,” he observes. “Also, the regulatory climate is becoming less conducive to cement manufacturing. I do not think there will be many cement plants built in the United States, which means we will need to import more.”
As cement costs rise, Huwel suggests that alternative isolation materials may become more attractive.
Short-Term Solutions
“In the short term, I envision companies reducing the amount of cement in their slurries, which is generally between 80%-100% today,” Huwel predicts. “Some of the cement will be replaced by cement kiln dust, a byproduct of the manufacturing process, or gilsonite.
“Resin is likely the most effective alternative to cement, but it also is the most expensive,” Huwel comments. “Right now, it is cost-prohibitive, but that may change if resin costs fall and cement costs continue to grow.”
Cement slurries are becoming more reliable as additive manufacturers refine manufacturing processes to deliver more consistent products, Nine Energy Service reports. Other keys to proper cementing include careful slurry design, which requires communicating with drillers to understand the downhole environment; redundancy and thorough equipment maintenance; and robust training programs.
Interest in cement alternatives is driven not only by costs but by cement’s limitations, Huwel relates. “Conventional cement is extremely strong in compression but extremely weak in tension and shear,” he details. “Over time, pressure cycles, which compress and then shear the cement, can break up cement. This is why we often see sustained casing pressure in wells that had no issues during the first part of their lives.”
Pressure cycles occur during each frac stage, so as stage counts grow, so do the demands placed on cement, Huwel notes. He says the ideal material will combine compressive strength with the ductility needed to flex with the pipe.
“By default, cement’s ductility is almost zero,” Huwel points out. “However, many recent additives can give cement some ductility. A small amount can go a long way toward improving cement’s long-term reliability, so those additives should continue to advance.”
Consistency
Huwel says suppliers also are refining additives for maintaining slurry suspension and preventing fluid loss. He says most of these improvements come from more consistent coating processes.
“When we evaluate additives, we are looking for consistency,” he stresses. “We want the materials to behave the same in the lab and on location from job to job, which generally means they need to have predictable manufacturing processes. The goal is to minimize variability as much as possible.”
When cement performs poorly, Huwel says the root cause generally falls into one of four categories: improper cement design, improper blending, mechanical error or human error. “The key to preventing design mistakes is strong communication,” he remarks. “If we know what is going on in the well, our engineering team can come up with an effective slurry and test it in the lab to verify it will perform.”
Thorough training, automation, equipment with built-in redundancies and robust maintenance programs can address the other root causes, Huwel assures. “With maintenance, too much is better than too little, given how much on-site equipment failure costs us and our clients,” he comments.
Cement pumps and other well site equipment are becoming more reliable and fuel efficient, Huwel reports. “Looking ahead, cementing equipment will move from diesel motors to electric ones that run on the same power source as the rig,” he suggests. “Electric motors cost more up front, but because they eliminate many of the tasks and failure points associated with lubricants, belts and hoses, they require less maintenance and have greater reliability.”
Cement Extenders
The goal when designing cement slurries is to provide effective zonal isolation at the lowest cost possible, says Tyler Nelson, the chief operating officer of Obsidian Chemical Solutions. That often means finding ways to reduce the cement slurry’s weight without sacrificing strength.
“Lighter slurries exert less hydrostatic pressure, so they are less likely to break down the formation,” he adds, noting that this is especially important in the Permian Basin and other areas where decades of development have depleted reservoir pressures.
“For many years, the industry would lighten slurries using hollow glass beads, which cut densities to nine or 10 pounds, but are extremely expensive and come with operational issues,” he recalls. “With modern additives, we can build bead-free slurries that have high compressive strengths but weights between 10.0 and 10.5 pounds.”
To shrink cementing costs, Obsidian Chemical Solutions relates it is testing cement additives that deliver strong performance at low concentrations. This work already has yielded more affordable extenders and expanders.
Nelson points out that these additives often act as extenders. They increase the amount of slurry that can be mixed with each sack of cement, which can reduce overall costs.
“One of the biggest changes we see in slurry design is a dwindling supply of pozzolanic fly ash, an extender that comes from burning coal,” Nelson mentions. “As coal-fired plants retire, cement engineers are looking for substitutes such as perlite, a relatively cheap mined ore.
“Because there are perlite mines in New Mexico, perlite is available for a low cost in the Permian Basin,” he says. “However, in areas where mines are farther away, such as the Northeast, the industry still relies on fly ash.”
Nelson says there are other options. “For example, we have a unique strength enhancer that should deliver the compressive strength normally associated with 5% concentrations at a concentration of only 1%,” he reports. “In some applications, it can cut the extender portion of the cement bill in half.”
Best Practices
When belts need to tighten, companies often pump less spacer fluid or cut chemistry concentrations in the spacer, Nelson observes. “Be careful doing that,” he says. “The spacer needs to be able to flush out and clean the pipe and the wellbore. If there is oil-based drilling mud left on either, the cement will never get the bond needed for zonal isolation.”
Lost circulation materials can be vital to the cement job’s effectiveness, Nelson adds. “Cement slurries can be two times denser than drilling mud, so if a well has lost circulation issues during drilling, they only will be exaggerated during cementing,” he says. “Including LCMs in the spacer and the cement slurry can make a huge difference.”
In many areas, it can be worthwhile to monitor LCM performance and experiment with different types to find one that works well, Nelson reports. “The best LCMs either are fibers, which create a matrix across each other when they lengthen down hole, or materials with widely varied particle sizes and potentially fibers mixed in,” he says.
In most slurries, Nelson recommends using a pre- or post-set expander. “As cement cures, it tends to shrink. While the shrinking is minute, it can prevent a strong bond from forming by creating a microannulus between the cement and the casing or wellbore,” he explains. “Preset expanders keep pressure on the pipe while the cement is liquid to ensure it forms a good bond as it sets, while post-set expanders cause the cement to expand after setting.”
To save money, many operators will run slurries without expanders unless bond logs indicate they are necessary, Nelson notes. “We are developing expanders that work at much lower dosages,” he shares. “We want to get the cost low enough that even the most cost-conscious companies can include expanders in all their slurries, rather than starting without them and risking a poor bond on their early wells.”
Plug-Induced Casing Damage
While using its high-resolution acoustic imaging system to evaluate completion designs, DarkVision Technologies Inc. has discovered that casing often exhibits breaches or other damage where plugs have been set, relates Tom Littleford, the company’s vice president of product and marketing.
“We continue to find plug-related casing damage in about half of all wells we image, and it’s not uncommon to find damage throughout an entire well. This damage is not only an integrity concern, but can significantly impact proppant placement,” Littleford warns. “On average, stages with casing damage at the plug location have 12% less perforation growth, signifying there are large productivity losses associated with this phenomenon.”
If a plug develops a leak during hydraulic fracturing, water and proppant can erode and eventually breach the casing, warns downhole imaging company DarkVision Technologies Inc. The company says it is working with operators and plug manufacturers to understand when leaks occur and reduce their frequency.
Initially, some engineers suspected that milling caused the casing damage. However, the primary mechanism appears to be erosion created when plugs develop leak paths that allow fluid and proppant to flow past the sealing element, Littleford reports. To figure out when the damage occurs, he says DarkVision analyzed 2,700 plug locations and published the results in SPE-204412-MS, which won the Curtis Blount Outstanding Paper Award at the 2021 Society of Petroleum Engineers/Intervention & Coiled Tubing Association Well Intervention Conference & Exhibition.
“The two strongest predictors of plug damage we found were plug type and casing ovality. There was a strong correlation between severe ovality–meaning anything over 2%–and plug failures that led to casing damage,” Littleford summarizes. “The type of plug also matters, as does the plug’s proximity to a perforation. For example, if an operator sets a plug over a perforation because of depth control issues, there is a high likelihood of a large breach developing.”
According to Chris McCann, DarkVision’s vice president of sales, the likelihood and severity of damage can be predicted by analyzing the type of plug deployed. “Dissolvable plugs are less robust than composites by design, so it is more common for them to develop a leak path and cause casing wall loss. But, that wall loss tends to be much less severe, as the plug is much weaker than the casing and will fail before a complete casing breach occurs.
“Composite plugs are less likely to fail, but they are strong enough relative to the casing that when a leak occurs, the fluid generally eats into the casing and causes a breach,” McCann relates. “Composites fail much less frequently, but when they do, the damage tends to be more severe.”
Beyond that trade-off, McCann says downhole environments and completion parameters vary enough to make it difficult to distill data into broadly applicable plug selection guidelines. “However, our analytics can help operators evaluate how specific plugs perform, given their completion designs, and figure out which ones will work best,” he says. He adds that many plug manufacturers are working with DarkVision to understand how their products perform and increase reliability.
Perforating Across Connections
The downhole imaging system also showed that 90% of wells activate at least one perforating gun at the same depth as a casing collar, McCann shares. “If the connection is a premium one with no gap between the two joints, these cross-collar perforations behave almost identically to ones in the rest of the casing,” he reports. “However, if it is a standard connection, the perforated connection becomes a weak point and significant metal loss occurs.”
Strong depth control can minimize the risk of perforating across collars, McCann says. “As part of our completion evaluation service, we mark every perforation and plug location and compare it with the planned location to help clients understand their depth control’s effectiveness and improve it,” he mentions.
Wireline depth control is challenging enough that 10%-15% of wells have plugs set above the top cluster of perforations from the previous stage, McCann reports. “This means the current stage will include part of an already-stimulated stage, which is far from optimal,” he notes.
The lessons about plug-induced casing deformation and cross-collar perforations often are a side benefit of running the imaging tools to quantify perforation erosion as a proxy for proppant distribution. According to McCann, the service is valuable enough that it can quickly generate returns. “If a client can increase stage efficiency by 5% using the information we provide, the service will pay for itself, even if that applies only to single well,” he says. “Usually, a company can apply lessons from one well across several.”
Wellbore Integrity Applications
In addition to evaluating completions, DarkVision’s acoustic imaging systems can be deployed to help operators diagnose wellbore integrity issues such as milling damage, severe deformations or collapsed casing. “When operators have crews and equipment on-site, they need tools that deliver definitive insights quickly,” Littleford says. “By providing 3-D images and measurements regardless of fluid clarity, we remove the guesswork from diagnosing issues and enable operators to identify the best path forward without trial and error.”
Littleford says the tools can be deployed to meet regulatory standards mandating periodic wellbore integrity checks. “Our platform has a resolution of 0.01 inches, which is high enough it can profile corrosion, scale formation, and other issues early on, before they progress and become more costly.”
The tools work by emitting sound waves and measuring their time and amplitude as the reflections return. As the tools traverse the well, they create a detailed 3-D point cloud that machine learning algorithms scan for issues, which are verified by a team of analysts using proprietary visualization software, Littleford describes. He emphasizes that the high-resolution acoustic platform delivers direct measurements in fluid of any opacity, which means the imagers can be deployed even in wells with drilling mud, oil or other nonclear fluids.
Expandable Tubulars
With qualities comparable to P110 or L80 pipe and a minimal impact on the casing’s inner diameter, expandable tubulars offer a lasting and reliable way to restore wellbore integrity, says Mark Villarreal, director of sales for the Western Hemisphere at Enventure Global Technology. He says expandables’ pressure integrity makes them ideal for repairing wellbore integrity ahead of hydraulic fracturing.
“When a connection’s integrity is compromised before a completion, operators often call for an expandable immediately,” Villarreal reports. “For other wellbore integrity issues, expandables tend to be deployed only after less expensive options, such as cement squeezes, have failed.”
Because they offer excellent pressure integrity and preserve most of the well’s inner diameter, expandable liners or patches often are deployed when a connection’s integrity is compromised before a completion, Enventure Global Technology reports. According to the company, the same qualities allow expandable liners to excel in refracturing applications, where the extra inner diameter can enable more effective and efficient designs.
Parted or leaking connections are the most common reason operators request an expandable casing patch, he mentions. “That always has been true, but we are seeing more connection issues as laterals get longer. Length increases the chance casing will buckle as it is run into the hole, which strains the connections. Longer laterals also require more connections and increase the risk one will be made-up poorly.”
With natural gas prices increasing, some operators are restoring old wells to production or drilling sidetracks to access more pay, Villarreal observes. “The dormant wells can have casing issues from corrosion or scale that justify deploying an expandable patch or liner,” he comments.
To broaden expandables’ operating envelope, Enventure has redesigned its high-performance connections to increase tensile strength 16%, Villarreal relates. “This improvement gives our high-temperature connections the ability to be deployed in hot environments such as the Eagle Ford and Haynesville,” he says. “In fact, we have run a 2,600-foot liner in a well where temperatures approached 375 degrees F.”
In particularly hot or challenging environments, Enventure can enhance the connections’ mechanical properties by placing hanger joints around them. He says that’s rarely necessary but is effective when needed.
Modern expandable liners and patches have an excellent track record, Villarreal assures. “Because they have no connections, casing patches are particularly reliable as long as they are placed in the right spot,” he says. “Improper placement can occur if the casing tally is off or if we discover after deployment that leaks extend below the patch’s intended location.
“To minimize the risk of improper placement, we recommend setting a bridge plug 15 feet below the bottom of the patch. When the operator does that, we never have issues,” he says. “When it’s not possible, we usually suggest a larger patch.”
Refracturing
According to Villarreal, one of the most exciting applications for expandable liners is refracturing. “Expandables excel in refracturing applications because they have great pressure integrity and preserve much of the well’s inner diameter,” he explains. “Compared with a four-inch cemented scab liner, the traditional alternative, an expandable offers three-quarters of an inch more inner diameter, which equates to a 50% increase in flow area.
“That extra space allows operators to pump the hydraulic fracturing fluid at a higher rate and employ extreme limited entry perforating,” Villarreal says. “In addition to increasing the refrac’s effectiveness, this can save money by enabling longer stages. The savings easily exceed the extra cost associated with using an expandable liner rather than a conventional scab liner.”
When oil and gas prices are high, as they are now, Villarreal acknowledges that most operators prefer to drill new wells rather than refrac because new wells’ performance is easier to predict. “We are working with a hydraulic fracturing consultant to quantify how much oil is left behind in various fields using public data,” he reveals. “These analyses provide information operators find valuable, while taking some risk out of refracturing.”
For other great articles about exploration, drilling, completions and production, subscribe to The American Oil & Gas Reporter and bookmark www.aogr.com.