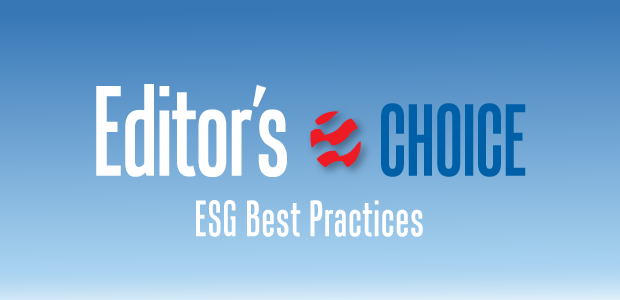
Closed-Loop Systems Provide Win-Win Benefits
By Garrow Wessendorff
HOUSTON–The oil and gas industry is focused like never before on maximizing returns on every dollar in the budget while simultaneously maximizing the value of field assets and elevating environmental, social and governance performance. That is a tall order, but what if there was a way for operating companies to economically address ESG concerns while also promoting long-term sustainability and operational profitability?
Closed-loop waste management is revolutionizing the oil and gas industry by offering a win-win ESG solution for the Eagle Ford and other shale plays. As the chief executive of The Panther Companies, I have seen firsthand the transformative power of closed-loop waste management systems. Indeed, these systems not only provide ESG and sustainability solutions, but they also benefit oil and gas operations’ bottom line.
By reducing waste and minimizing the risk of environmental damage, closed-loop systems can help companies increase profitability and investor interest. In addition, they can foster goodwill with local communities and regulators by demonstrating a commitment to responsible resource development.
Of course, implementing closed-loop systems can come with its own set of challenges and considerations. But with the right technology and expertise, these challenges can be overcome, and the benefits are too significant to ignore.
I am proud to see closed-loop systems becoming a more widely adopted solution, including for shale operators seeking to improve their ESG standing.
Closed-loop systems help minimize the amount of waste that must be disposed of by treating, recycling and reusing it, which in turn reduces oil and gas operations’ overall environmental impact. They also help prevent soil and water contamination by ensuring that drilling fluids and any associated waste are handled and disposed of in a responsible manner that minimizes environmental risks.
By helping mitigate the environmental impact of oil and gas operations, these systems also can improve profitability. A recent Eagle Ford project with a private operator provides a prime example of how closed-loop systems can benefit both the environment and profitability.
Since its 1985 founding, the operator has drilled more than 800 wells in the United States and abroad. The company currently focuses on acquiring and developing unconventional assets in the Eagle Ford trend, where it has implemented a closed-loop system for two horizontal wells in southern Fayette County, Tx.
The project’s first well targeted the Lower Eagle Ford Shale with a 9,600-foot lateral. The second was a Lower Austin Chalk well with a 10,500-foot lateral. Both would represent record lateral lengths for the play area. To facilitate the closed-loop operations, The Panther Companies provided the mud products, state-of-the-art solids control equipment, and managed the haul-off and disposal for both horizontal wells.
By implementing a closed-loop system, the company was able to successfully drill the longest laterals in this portion of Fayette County, while also minimizing waste and reducing the environmental impact. This project is a testament to the power of innovation and collaboration in driving sustainable practices in our industry.
As seen in our recent partnership, closed-loop systems can set new standards for drilling efficiency and sustainability. We are committed to continuing to lead the industry toward more sustainable practices and working with companies to achieve their ESG goals.
Application Envelope
As more oil and gas companies look to improve their ESG standing and lower costs, closed-loop systems are likely to become an increasingly important tool. However, it is important to consider when these systems are the best option versus when other processes may be more suitable.
Closed-loop waste management is revolutionizing the oil and gas industry by offering a win-win ESG solution, especially in unconventional resource plays such as the Eagle Ford Shale, where oil-based drilling fluids are required. In the right applications, closed-loop waste management systems not only provide ESG and sustainability benefits, but they also help optimize the bottom line of oil and gas operations.
One of the primary advantages of closed-loop systems is the ability to treat, recycle and reuse drilling fluids, which can mean significant cost savings. Therefore, closed-loop systems make the most sense when a lot of drilling fluid is being used and there are limited disposal options. It is much more economical to treat and reuse the fluid than to constantly dispose of it and bring in new fluids.
Additionally, closed-loop systems are ideal for areas where water resources are limited, since the systems significantly reduce the amount of freshwater that is needed for drilling operations. This is particularly important in regions prone to droughts or in which water is scarce.
On the other hand, closed-loop systems may not be the best option for every drilling operation. For smaller jobs that do not require much drilling fluid, traditional disposal methods may be more cost-effective. Moreover, if a site has limited space or infrastructure, it may not be feasible to set up a closed-loop system.
In these cases, it is important to evaluate other waste management options and consider each method’s environmental impact.
For a private producing company with Gulf Coast operations, the decision to use a closed-loop waste management system typically is determined by the well type and its geographical area. As a company that focuses on conventional onshore oil and gas exploration, the operator tends to opt for closed-loop systems when the well requires a weighted mud system with barite or an oil-based mud system. Other factors that come into play when choosing the disposal method include surface restrictions on land farming and environmental risks such as wetlands, waterways or densely populated areas.
Generally, the operator tends to use closed-loop systems more than 90% of the time in Texas and 100% of the time in Louisiana because of state land farming regulations and litigation concerns.
Shale Oil Challenges
Oil-based mud is a common choice for drilling in the Eagle Ford because it promotes higher penetration rates and wellbore stability, especially in challenging geological formations. However, this preference adds another layer of complexity with regard to waste disposal.
In the Eagle Ford and other shale plays, operators are implementing closed-loop systems to successfully drill long laterals while simultaneously minimizing waste and reducing environmental impacts. Closed-loop solutions encompass drilling fluid products, state-of-the-art solids control equipment, and haul-off and disposal services.
Therefore, our upstream partner in the Eagle Ford prefers closed-loop systems for most projects because they ensure proper waste disposal and reduce the company’s long-term concerns. Even so, the benefits of closed-loop systems extend far beyond waste disposal.
By minimizing the volume of waste in need of disposal, operators can reduce their costs significantly. Additionally, reclaiming and reusing as much drilling fluid as possible improves drilling operations’ economic efficiency, especially in times of high diesel prices. In some areas of the Eagle Ford, for instance, the cost of a barrel of oil-based mud is around $175, which makes it a valuable resource that is worth conserving.
Panther uses state-of-the-art solids control equipment to dry cuttings and reclaim all possible fluids, minimizing the haul-off on both fluids and solids. Our equipment also can recycle much of the used oil-based mud.
This gets to the heart of what we consider the real reason behind closed-loop systems: Reclaim as much as possible; haul off as little as you can. Nevertheless, closed-loop systems also provide other benefits, and we believe that these systems are the future of the oil and gas industry, which makes us proud to be at the forefront of this technology.
Modern Closed-Loop
The upfront costs of implementing a closed-loop system typically are offset by reduced hauling and disposal costs. Additionally, the overall efficiency of drilling operations may improve with closed-loop systems and trim costs further.
State-of-the-art solids control equipment also makes closed-loop systems better for drilling operations. Not only does this equipment effectively separate drilling solids from drilling fluid, but it also ensures that the fluid can be reused in the drilling process, reducing the need for constant disposal and fresh makeup fluid.
By minimizing waste and limiting the discharge of drilling fluids and solids into the environment, closed-loop systems are a critical tool for shrinking drilling operations’ environmental impact. In addition to the environmental benefits, closed-loop systems also improve drilling projects’ efficiency and cost-effectiveness.
Furthermore, today’s solids control equipment is crucial to the effectiveness of closed-loop systems. With equipment such as shale shakers, hydrocyclones and centrifuges, solids control ensures that each stage removes progressively smaller particles from the drilling fluid. Removing solids and other materials can extend fluid life, improve drilling efficiency and reduce drilling operations’ environmental impact.
With a growing emphasis on environmental sustainability, many production companies are turning to closed-loop waste management systems to minimize drilling waste and, as a result, reduce their volumes of offsite waste disposal. This can lower the risk of accidents and spills during transportation. They also can help conserve water and other depletable resources that would be necessary for new treatment processes.
Other benefits of closed-loop systems include lessening the need for human resources dedicated to waste hauling and disposal, allowing personnel to focus on other areas of the operation. This can improve safety and worker satisfaction, as well as reduce waste disposal’s environmental impact. Additionally, closed-loop systems often have built-in safety mechanisms, such as automated monitoring and control, which further improve safety and environmental performance.
Overall, closed-loop systems offer a unique combination of environmental and financial benefits that make them a game-changer for the oil and gas industry.
Win-Win Solution
The oil and gas industry is evolving constantly, and as we navigate a changing landscape, closed-loop systems offer a compelling solution for producing companies looking to balance economic, social and environmental concerns.
By embracing these systems, companies not only can reduce their environmental footprints, but also improve their social and governance standing, demonstrating a responsible approach to conducting operations. Their adoption also may have a positive impact on investor attitudes toward the oil and gas industry.
As more investors prioritize ESG factors in their decision-making processes, companies that demonstrate a commitment to sustainability and responsible operations may be better positioned to attract investment. Moreover, the operational efficiency and financial benefits of closed-loop systems cannot be overlooked.
Closed-loop systems allow for the treatment, recycling and reuse of drilling fluid, thereby reducing offsite waste disposal. This, in turn, leads to significant cost savings for oil and gas companies, making their operations more profitable and efficient.
As the industry continues to evolve and face new challenges, adopting innovative technologies and practices that promote sustainability and responsible operations will be essential for success. Closed-loop systems are a win-win for the industry, the environment and local communities.
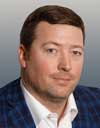
GARROW WESSENDORFF is president, chief executive officer and managing partner of the Panther Companies, which provides drilling and completion fluids, production chemicals, solids control services, closed-loop equipment, haul-off and disposal services, and wellsite fluid engineers. He has more than 17 years of operations management experience in the finance and oil and gas sectors. Before founding Panther, Wessendorff was a partner and vice president of operations at Stryker Fuels and a vice president of commercial lending at Frost National Bank.
For other great articles about exploration, drilling, completions and production, subscribe to The American Oil & Gas Reporter and bookmark www.aogr.com.