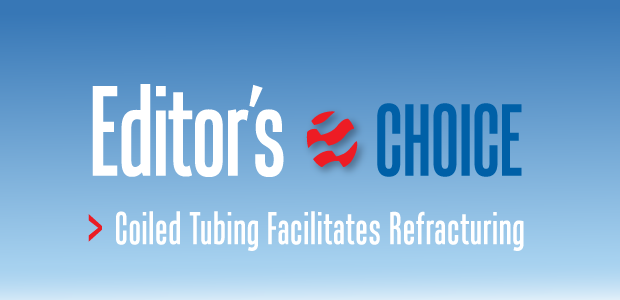
Refracturing
Coiled Tubing Enables Effetive Horizontal Recompletions
By Brett Fears
OKLAHOMA CITY–Low crude oil prices are making the concept of recompleting horizontal wells effectively and economically an intriguing topic for companies looking to increase revenue while limiting expense. Many mature shale wells suffering from low production still contain large volumes of oil and gas that can be produced through refracturing.
However, despite the considerably lower costs required to recomplete a well versus drilling a new one, further technological advancement in refracturing operations is needed to allow this technique to be an effective solution in today’s industry climate.
As with hydraulic fracturing for new wellbores, there are numerous refracturing methods that need to be explored and investigated to make recompleting a well a more cost-efficient and reliable strategy. To perform a recompletion operation effectively requires isolating the initial fracture locations along the lateral, creating additional perforations, and being able to pump frac slurries at sufficient rates and pressures to stimulate and prop open new rock to produce from the new stages.
Proven fracturing processes, combined with new technology, can be used to achieve successful results. One approach being investigated uses coiled tubing technologies in conjunction with high-velocity jet perforating techniques and chemical diverting agents to facilitate effective horizontal well recompletions.
Coiled tubing always has been a very efficient method for conducting drilling and workover operations, including both perforating and hydraulic fracturing applications. CT provides an excellent balance between the speed and low cost of wireline, and the strength and ability to pump fluids down hole that is provided by jointed pipe. Additionally, being able to pump continuously without having to break connections, and to work under high pressure without needing a snubbing unit, make CT a preferred method for performing downhole operations through highly deviated and extended-reach horizontal wells.
Jet perforation techniques use abrasive-laden fluids pumped at high velocities to create a communication tunnel through the steel-cased hole in the wellbore and into the formation. The perforating tools are carried down hole either by coiled tubing or jointed pipe to a desired target location, and abrasive slurry is pumped from the surface, through the tubing and out a specifically sized nozzle to establish the high velocity required to penetrate through the casing and out into the wellbore.
The abrasive perforation tunnels tend to provide excellent flow areas with clean and wide permeable paths, as opposed to perforating with explosive charges, which sometimes can leave a low-permeable skin on the walls of the perforation tunnel (Figure 1). These two benefits can lead to lower pressure being required to break down a formation during the hydraulic fracturing process.
Additionally, with the abrasive perforating technique, perforations can be performed multiple times without having to pull out of the hole. This allows for continuous swapping between zonal isolation, perforating and fracturing.
FIGURE 1
This photo of a partial perforation tunnel shows the “ballooning effect” as the abrasives return through the tunnel, which creates large surface areas inside the perforation tunnels.
Diverting Agents
Previously perforated frac stage intervals along the wellbore must be isolated to allow new hydraulic fractures to be placed at new or existing locations during the recompletion process. This prevents certain perforations from continuously receiving all the proppant and fluid pumped down hole during fracture treatment. Horizontal wells typically are fractured initially using ball-activated “plug-and-perf” or sliding-sleeve techniques to establish zonal isolation. However, mechanical isolation tools potentially can be quite costly in refrac applications, making chemical diverting agents an attractive option.
Diverting agents are placed within perforation tunnels or the fracture itself to create physical barriers that create a lower permeability than the perforations that remain exposed. The frac treatment fluid will follow the path of least resistance into the desired perforation, if executed correctly.
Among the different categories of diverting agents:
- Granular, self-degrading materials can be pumped through perforations into the formation. These materials usually are comprised of plastics such as poly(glycolic acid) or poly(lactic acid). The material is pumped much like proppant to plug outside the casing inside the formation, and breaks down when exposed to wellbore fluids for a certain time and at a certain temperature.
- Self-degrading frac balls, of course, are a proven method of plugging perforations in plug-and-perf operations in shale plays.
- Fibrous perforation plugging devices are of fibrous construction and are deployed much like frac balls. They are effective at finding and plugging perforations, and have the advantage of sealing irregular openings in the casing, and stick to perforations more effectively than frac balls. These devices can be acid-degradable or self-degrading. This type of diverting agent also may be drilled out of the wellbore mechanically.
Diverting technologies have been developed continuously over time with varying levels of success, and can offer tremendous cost savings over zonal isolation methods using conventional downhole tool operations.
Abrasive Perforating
Using coiled tubing for initial hydraulic fracturing as well as refracturing has been somewhat limited because of the size and strength of the tubing strings, since high rates and pressures are needed to break down and prop a given rock volume. Even as coiled tubing sizes have increased over time, CT’s size and strength limitations have prevented it from becoming a preferred means of transporting fracture treatment slurries to the desired downhole locations.
However, coiled tubing still can be very useful during fracturing operations when it is used with abrasive perforating and diverting agents as a way to deliver pinpoint fracturing and stimulation treatments, as well as post-job clean-out operations.
There are two possible methods for recompleting wells using CT technologies. The first can be used for both stimulating new wells and recompleting existing wells, and it provides a way to pinpoint each multistage fracture.
Initially, diverting agents should be pumped as needed to plug all perforations in the wellbore. A bottom-hole assembly with an abrasive jet perforator is then run down hole to the lowest target interval. An abrasive slurry is pumped from the surface to begin the perforating process of either new zones or existing perforated locations.
After the perforation process is complete, the BHA is picked up above the perforations to prevent the string from becoming stuck during fracture treatment. Once the BHA has been relocated, the frac slurry can be pumped down the annulus to establish an injection rate and hydraulically break down the formation at the perforated interval.
After the targeted zone has been fractured, the diverting agents can be pumped down the annulus between the tubing and the casing to isolate the newly fractured zone. The process of perforating, fracturing and isolating can be repeated for each subsequent stage until all stages have been completed.
Completing a clean-out of the diverting agents will reopen the wellbore for production. The method of clean-out depends on the type of diverting agent utilized. It can require acid to deteriorate/dissolve, be self-degrading with extended exposure to fluid and temperature, or be removed mechanically with a downhole motor for clean-out. For effective removal with a downhole motor, the diverting agent must seal at the face of the perforations and not in the fracture itself.
The major benefit to this recompletion technique is that it allows each individual stage/zone to be properly treated and fractured, providing the operator with a true representation of the performance of each stage/zone. Additionally, the pump time for the diverting agents may be recorded and correlated with the pressure charts to possibly confirm the desired location was fractured appropriately.
Diversion Process
The second method utilizes a diversion-type fracturing process that treats the entire wellbore, as opposed to targeting individual stages. This greatly decreases the time required to execute the entire operation, and also creates less wastewater. As with the first method, this diversion technique can be used on both new wells and recompletions.
All perforations are completed in a single run using coiled tubing and an abrasive jet perforating tool, after which the BHA is pulled to surface, leaving an open wellbore to carry out the fracturing process. The initial frac treatment is pumped first, followed by diverting agents to isolate the stage. In many cases, the formation can be seen breaking down during fracturing through a fluctuation in the treatment pressure.
As diverting agents begin to isolate perforations, an increase in treatment pressure indicates the frac fluid has been diverted to other perforations. Because of varying formation gradients, the treatment pressure may increase until a breakdown is seen on the newly exposed perforations. Once this occurs, the next stage can be fractured and the process may be repeated as needed. As in the first method, cleaning out the diverting agents is completed once all frac treatment fluid has been pumped.
Case History
A fracturing process using a fibrous diverting agent was performed on a new well in Grayson County, Tx., which borders the Oklahoma state line and is where activity has focused on horizontal Woodford Shale development. A total of 144 abrasive perforations were made using coiled tubing, with seven frac stages making up the entire hydraulic fracturing volume. After the perforations were made, CT and the BHA were removed from the wellbore to prepare for the fracture treatment.
The diverting agent was pumped down hole after the initial frac stage. A spike in pressure was observed after the volume to displace the diverting agent was pumped, indicating a successful isolation of the fractured zone.
FIGURE 2
Job History Chart Showing Frac Stages 3-7 of Well
Using Fibrous Diverting Hydraulic Fracturing Method
Acid was pumped directly behind the diverting agent to assist in the subsequent breakdown for the next fracture treatment. After the final frac stage was completed, the diverting agents were removed from the wellbore using a downhole milling assembly. A section of the job history is shown in Figure 2.
Positive indications of the diverting agents were seen during the milling operation, thus confirming a successful diversion as well as providing the operator with data indicating where each frac stage had been pumped. This diversion method can be applied easily to a recompletion simply by isolating existing perforations prior to the initial frac stage.
Conclusion
While there are many benefits to fracturing/refracturing methods based on coiled tubing, abrasive perforating and diverting agent technologies, some of the main considerations are speed, cost effectiveness and reliability. Having to run downhole tools such as packers, plugs and sleeve systems can be quite expensive and complex, and may require large tool strings, extensive drill-outs, increased downtime, increased water requirements, and reduced inside diameter restrictions in the wellbore.
Being able to combine efficient and proven technologies to achieve successful fracturing and refracturing operations is a very effective strategy to compete with the economic challenges inherent in today’s oil and gas operating environment.
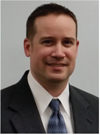
BRETT FEARS is team leader for Thru Tubing Solutions’ engineering department, where he has been working for six years. He has 15 years of experience as a design engineer for downhole tool applications. Prior to TTS, Fears spent time designing tools for Halliburton Energy Services’ casing equipment department. He graduated in 2001 with a B.S. in mechanical engineering from the University of Oklahoma, and received an M.S. in mechanical engineering from Oklahoma State University in 2008.
For other great articles about exploration, drilling, completions and production, subscribe to The American Oil & Gas Reporter and bookmark www.aogr.com.