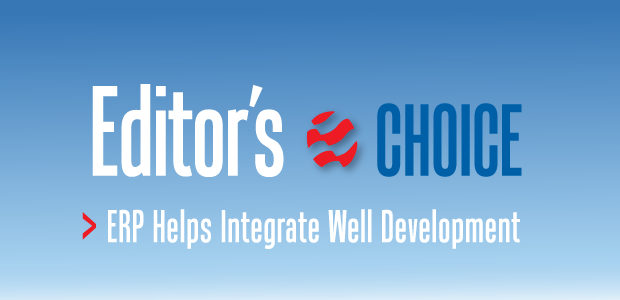
ERP Helps Integrate Well Development
By Kari Johnson
A pumper on his regular rounds enters production data into an electronic form on his tablet. With the press of a button, the data are transmitted to a service that inserts them into the corporate system.
An executive at the airport awaiting her flight uses her smartphone to check on the latest production performance data. She notices a trend in the day’s production that requires follow-up.
At company headquarters, a committee meets to review the latest authorization for expenditure. After discussion and a few budget adjustments, agreement is reached. Each team member signs off on the AFE using whatever device–tablet or phone–he brought to the room.
A planning group gathers to review current and potential drilling activity. Its members access maps, historical financial records, production data and land records simultaneously. The group does not know or care that the data are managed in several applications.
These scenarios are just part of the vision shared by Reggie Cook and Jeff Hartwig, who are working hard to make them reality at Chaparral Energy Inc. The desire for improved efficiency and incremental value is driving key changes to the company’s information technology architecture. Central to implementing that desire is using enterprise resource planning (ERP) software to integrate all digital operating solutions (Figure 1). For Chaparral, its enterprise decision relies on Enertia, a key well life-cycle platform that provides a common software application solution for business management.
Information
Just about everybody at Chaparral uses Enertia Software’s namesake product, says Cook, the company’s vice president and controller. He indicates land people use it for land administration and balloting; accounting staff for financial recording, reporting and planning; production department personnel for production gathering and reporting; reservoir engineers to update their reserve reports; and drilling crews to monitor costs.
Personnel throughout the company are involved in workflows and incident tracking, and Cook asserts that every single department needs such a solution for information retrieval or action. Chaparral installed the ERP as its platform several years ago, he recalls, adding that he was quick to appreciate how integrated the modules were within the ERP, and wanted the same user experience when accessing data outside the solution. That was achieved at the time through custom integration.
Chaparral uses WellView®, a well management system from Peloton Computer Enterprises Inc., for moment-by-moment tracking of the drilling scenario. WellView feeds data to the ERP, which validates the estimated costs versus actual, Cook says, adding that identifying any variance is critically important. “With horizontal wells running $12 million-$13 million, you need to pay attention to exactly what is happening and what the actual costs are. With vertical wells, it doesn’t take much variance from AFE to become uneconomic.”
Chaparral also moves a lot of data between its GIS and reserves systems, and information and analytics from IHS Inc. to get a more comprehensive map of operations, competitive drilling, and possible and probable drilling sites. The company is planning to use a new production data gathering system for what Cook calls “out of the box mapping” for specific dashboard-style reports.
The company also emphasizes enhanced report generation, ensuring that everyone has consistent information, he says. “Once we were able to produce meaningful and reliable reports, even the operations guys became confident in the system.”
Gaining Efficiency
A joint effort now under way with Enertia Software will make application integration faster and more standardized, predicts Hartwig, vice president of information technology at Chaparral. This, combined with mobile app support, will improve workflows and access to key performance data. He points out the project began in early 2013 as part of a larger IT architectural assessment.
“We laid out where we thought we should go, identified gaps and made recommendations,” he reports. “A key architectural principle for us is to give people the information they need to do their jobs without constraints and restrictions. Mobility and the Web are going to be a big part of making that concept reality.”
Chaparral used Microsoft’s upstream reference architecture as its model. “We started by defining what the value chain looked like in a midstream oil and gas company,” he says.
Capabilities were split into three categories: leading, operational and enabling. Four enterprise architecture layers were mapped on top of that.
Because the ERP software is mission critical to operations, Chaparral needed to map it into the company’s architecture, says Hartwig. Following an all-day session with Enertia Software, a joint vision was agreed, with the company committing to support a service-oriented architecture. That architecture makes it easier and faster for users to add custom functionality and integrate with other applications, Hartwig says. Customers will have a standard way to access functions such as inserting records and retrieving data without having to know all the underlying details of the application, he adds.
The ERP will allow Chaparral to compose applications using business objects, data warehouses, business intelligence and institutional workflows, Hartwig says. As the common software application solution becomes available, it will be deployed in the cloud for Chaparral integration testing.
While the ERP builds the service layer on top of its business objects, Chaparral is working to create a lightweight communication capability to establish workflows in the service environment using Microsoft’s collaborative software program, SharePoint® 2013, and the underlying workflow communications foundation and workflow foundation. With another common technology, Hartwig reports, the company can expose data as service and workflow components to domain applications that don’t have a service layer.
The 500-pound gorilla is mobility, he says. As companies open their business objects through Web services, mobility becomes extremely intriguing. “We see mobility as being a very large channel for delivering situational knowledge to people in the field,” Hartwig advises.
He says he is hopeful that Microsoft will embrace the work that Chaparral has done, take leadership and give the marketplace an architecture guideline, extending the MURA prescribed for the midstream. Microsoft technologies are pivotal in any case, he points out, including SharePoint, and creative use of its Windows® Communication Foundation and Workflow Foundation technologies.
Chaparral will soon be able to leverage Microsoft technology such as Excel® and the PowerPivot add-on in SharePoint with the ERP, predicts Hartwig. “Everybody gains by this, and we don’t have to train users on new tools,” he asserts
ERPs represent a significant change in how the user interacts with multiple applications, he offers. Instead of suffering the inevitable friction caused by working with separate applications, the user can seamlessly navigate to the data he needs. Such services are the bridge between technology and business, Hartwig says, adding, “Services give you the ability to compose and orchestrate, and to form fit processes to strategies. This removes a lot of the friction.”
It comes down to pure economics, he says. “If you try to solve every problem by buying the best and the newest off-the-shelf software, you lose the ability to create value for your operational people,” Hartwig points out. “Services give you the ability to form fit technology to your processes to create the incremental value that everybody needs.”
Penn Virginia
Gary Bailey, vice president of IT at Penn Virginia Corp., an oil and gas exploration and production company, is excited about the potential for business intelligence. “That really is the next frontier for our business, from a technology perspective,” he says.
Companies are hungry for graphical reporting of real-time key performance metrics, Bailey says. “For example, cost tracking in the drilling process is paramount; you have to have up-to-the-minute information in order to control your costs.”
On the strategic side, when forecasting for business change such as property sales or acquisitions, key information at one’s fingertips helps in making solid high-value business decisions, he adds.
Similarly, Bailey insists access to production volumetric information is essential. “Businesses live and die by what they produce on a daily basis,” he says, pointing out that flexibility in delivery and access is key. “Our users should be able to use any device any time to get data, and, if desired, they should be able to request simple e-mail reports sent at the frequency they need,” he insists.
“We would like to have a dashboard view of our key performance data–whether in Enertia or ancillary systems such as gas marketing or reserve calculation software,” Bailey says. “For us, out-of-the-box reporting for the oil and gas industry needs to present very targeted results that executives can truly use (Figure 2).”
Make that information accessible on any mobile device and there is real leverage, he adds. For the moment though, all of this is gravy for Penn Virginia, Bailey says. First, the company needs to complete its migration from SAP to Enertia.
Penn Virginia has gone through a major transformation since 2010, selling off its midstream and natural resource land management business. “We have become a very focused exploration and production company,” describes Bailey.
Bailey predicts the result will be much greater efficiency in a much simpler computing environment. Penn Virginia selected Enertia in April 2013, and plans to complete the implementation by the end of the year. “Switching to a smaller footprint focused exclusively on oil and gas meant saving literally millions of dollars,” says Bailey.
For Penn Virginia, the focus is on getting the basics right so that people have the information they need to do their jobs. The company is implementing the full suite of capabilities from the ERP suite, and also is connecting to other systems as needed. For example, production accounting volumetrics are managed in another third-party application already in use, and the new ERP will facilitate integration with this application.
As at Chaparral, Bailey says most Penn Virginia employees will use the ERP system at some point. “We will be using the workflow approval process, which involves a lot of people,” he says.
Penn Virginia has most of its operations personnel in Houston and all its drilling in the Eagle Ford Shale play, he reports, with some production in Oklahoma and Mississippi.
Penn Virginia will use all best practices out of the ERP box, Bailey predicts. The company is in the midst of configuring the system for those processes and converting data as it exists in its current SAP and land systems. It is using a combination of Enertia implementation resources and consulting services from Houston-based Magnum Forge.
The ERP will be installed at Penn Virginia’s co-located data center at CyrusOne LLC in Houston and virtualized except for the database. Penn Virginia has used CyrusOne for three years, Bailey reports. “The fact that we share all the costs with many other companies that are doing the same thing makes it really affordable for a midcap company,” he points out.
Bailey says he is looking forward to the cutover to the new application solution at the end of the year and then moving on to building business intelligence. “It’s a very competitive industry,” he observes. “Those of us who can provide information for tactical and strategic decision making will be ahead.”
Stepping Into Services
Technology companies are challenged continuously to innovate, reinvent and re-envision their products based on the evolving market. For Enertia Software, that means developing strategic partnerships with organizations such as Stonebridge, a business and technology consulting firm, to leap into services architecture. Stonebridge is focused on achieving better results and maximizing business performance in collaboration with organizations such as Enertia and its client, Chaparral Energy.
“Chaparral Energy approached us with its vision of the future,” says Kevin Schmidt, Enertia Software’s president and chief executive officer. “That strategy fit well with our strategy to scale up for larger enterprises.”
He adds Enertia now is shifting from a software application environment to a service-based framework.
“This isn’t the first time the technology has adjusted to suit users,” says Schmidt, noting that the ERP system was moved to Windows in the mid-1990s and has seen significant modernizations ever since by adopting .net and other leading frameworks to accommodate demands for integration, dashboards, and the bring-your-own-device culture.
Services are a convenient and efficient way to handle data and communication exchanges between devices and applications, Schmidt poses. Once a service is published, other applications can use it rather than reinvent it. A simple example is a service such as a time provider. There is only one service needed if everybody can talk to it and get to know what time it is. “The promise is that there are fewer services and they can be used together to do business processing in a very prescribed and standard manner,” Schmidt says.
Once a common software application solution is converted to a service-based environment, it could be tied into other systems that are service-enabled, he says. Economics, reserves, and mapping for geology all are services that now could be tied in, he points out.
At the same time, the solution software will be able to take advantage of Microsoft technologies–including SharePoint and PowerPivot–to replace their own custom user interfaces. Everything from the common software application solution is underneath the Microsoft tools, talking to the database. Schmidt says existing customers will see the interfaces and workflows go from proprietary screens to SharePoint and Excel.
Services will allow the users to configure their work environment more easily. It will be more about building a strategy for what is needed rather than building an interface for it, Schmidt predicts. “It will be much easier to change and evolve into the future,” he says. “Using the platform and services will allow Microsoft to tie all the other services together, including address service, map service, and so on. Our customers will ride the coattails of the service architecture.”
Single Integrated Solution
Today, if the customer adds integrations to his common software application solution, he must have a deep understanding of the data structures and tables before inserting data. With the services architecture, the interface is through the service. “So in the .net programming environment, a procedure is written that requests a service,” Schmidt says. “The service grants access and provides a standard interface for data exchange. The procedure can either push data or receive it.”
Behind the scenes, the ERP runs its logic to retrieve or insert data, including rules such as data validation. In the services model, there is no need to understand the solution software’s underpinnings to access its functionality. The services and integrations promise that data can be accessed near real time.
“An executive can see an engineer’s recommendation using the digital dashboard connected to operational data, ARIES data, maps and other records at the time the recommendation is made,” Schmidt says. “The potential value is enormous.”
The demand for efficiency and speed is growing along with the industry. “Companies are planning to spend trillions of dollars in shale plays,” Schmidt asserts. “With numbers like that, it is just an unending run forward. The oil and gas companies are running at such a fast pace and with such a capital-infused structure that they have to have data faster, more accurately, and livelier. How do oil and gas companies absorb the increased activity? They have to do it with technology, and with fewer and smarter people.”
The software provider must deliver quick insight to every corner of the building, Schmidt says.
“The challenge is to make access as easy for the occasional user as it is for the power user. Apple set the standard for technology that requires virtually no training to use,” Schmidt points out. “That is the standard to attain. You have to deliver value to people who are not technology savvy, who don’t like technology and don’t like change.”
One advantage for Enertia is that it began at the smaller end of the market, where jobs overlap, says Schmidt. “We learned the bigger picture from our smaller customers, where the users had multiple jobs and knew how everything tied together,” he offers. “The services work will pay them back with faster, easier integrations and true mobility.”
For other great articles about exploration, drilling, completions and production, subscribe to The American Oil & Gas Reporter and bookmark www.aogr.com.