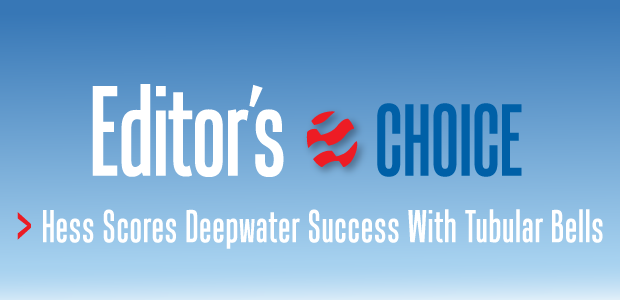
The Tubular Bells Tale
Hess Scores Major Success With Tubular Bells Project In Deepwater Miocene Play
By Danny Boyd Special Correspondent
HOUSTON–Successfully developing a high-pressure, high-temperature reservoir with multiple subsea wells connected to a new floating platform in 4,300 feet of water is an impressive engineering achievement under any scenario. Accomplishing that feat on budget in a little more than three years between sanctioning the project and commencing production is a marvel in its own right.
But on Nov. 13, 2014, when first oil began to flow from Miocene-aged sands 4.5 miles below the seafloor through subsea wellheads to processing facilities aboard a new floating production system (FPS), the Tubular Bells project expanded the industry’s working definition of “fast track” scheduling while staying within a budget of less than $3 billion.
“This is the most rewarding deepwater project I have been associated with,” says Mike McEvilly, an industry veteran of 34 years who served as project director of the Hess Corporation-operated Tubular Bells. “The success of the project on such a short development timeline is the result of a balanced combination of teamwork, execution efficiencies, technical expertise, budget discipline, and adherence to safety.”
The field is estimated to hold more than 120 million barrels of oil equivalent and have a productive life of at least 25 years, giving Hess (57.14 percent working interest, with co-owner Chevron holding the remaining interest) a significant and long-lived producing asset positioned in the heart of the subsalt Miocene trend.
The Tubular Bells success story began in October 2003, when BP announced the discovery well in Mississippi Canyon Block 725, 135 miles southeast of New Orleans. The discovery was drilled to a depth of 31,131 feet and encountered 190 feet of net oil pay. A successful appraisal well was drilled in 2006, five miles from the discovery location, followed by two successful sidetracks in 2007 to further delineate the field. In late 2010, Hess (already a co-owner in the project) agreed to pay $40 million to acquire BP’s interest and assume operatorship.
“Within a year of becoming operator, Hess sanctioned Tubular Bells for development,” McEvilly recounts, noting that one of the key milestones occurred shortly after project sanctioning, in October 2011, when Hess signed a facilities agreement with Williams Partners to construct and operate the Gulfstar One spar-based FPS and related export pipeline system.
The decision to contract with a third-party to build the production facilities helped to accelerate the time to sanction, according to McEvilly. “We delivered first oil safely and on budget in approximately three years, in spite of all the complexities of a deepwater subsalt field development (the salt canopy in geologic sections above the reservoir is more than 10,000 feet thick in some areas). Compared with standards benchmarking, we are very satisfied with the end result.”
Best-In-Class Performance
Hess’ best-in-class performance for a major project was made all the more challenging by middle Miocene reservoir pressures of about 17,000 psi at well depth and bottom-hole temperatures that approached 300 degrees Fahrenheit, according to McEvilly. Total vertical depth is 25,000 feet.
The topsides for the Gulfstar One FPS for the Tubular Bells Field were designed to process 60,000 barrels of oil and 135 MMcf of gas a day along with up to 60,000 bbl/d of water injection. Shown here is the main deck lift in May 2013 at Gulf Island Marine Fabricators’ construction yard in Houma, La.
“The pressures and temperature have to be accounted for in the engineering design, but the wells have high deliverability; some are capable of 25,000-30,000 barrels a day,” McEvilly states. “The reservoir is yielding 35-degree API gravity oil with a gas-to-oil ratio of approximately 2,000.”
By mid-March, Hess was producing from three wells at Tubular Bells, and a fourth was being completed and expected to go on line sometime this year. McEvilly adds that a fifth producing well may be added along with two water injection wells through 2016.
“There are additional exploitation opportunities and possibilities subsequent to where we are today with Tubular Bells,” McEvilly reveals. “We started with an underappraised field with wells on the west and east sides of it. We drilled in the middle of the field, which proved up and actually exceeded our prognosis to the point that we drilled an additional well to recover the reserves encountered so far.”
Net production to Hess is estimated at 30,000-35,000 barrels of oil equivalent a day over 2015, with gross production of approximately 59,000 boe/d, he says. Expected net production for 2015 could approach 10 percent of Hess’ estimated companywide output of 350,000-360,000 boe/d, representing an increase of 10-13 percent from pro forma production of 318,000 boe/d in 2014.
“Originally, we were looking at 25,000 boe/d net at Tubular Bells this year, but we have upped that by 5,000-10,000 boe/d,” McEvilly says. “Although gross total recoverable resources are estimated to exceed 120 million barrels, there are potential future exploitation wells that may improve that.”
Floating Production System
At the heart of the production system is the Gulfstar One, stationed in Mississippi Canyon 724. The 584-foot long classic spar hull is mated to a 7,500-ton, three-level topsides structure. The facility’s process design accommodates 60,000 barrels of oil a day and 135 million cubic feet of gas a day, along with the capacity to handle up to 60,000 barrels of water injection a day.
The host facility–including the topsides, hull and export lines–are owned by Williams Partners (Williams Partners developed the Gulfstar One project and has a 51 percent ownership interest, with Marubeni Corporation holding a 49 percent interest). Hess has exclusive-use rights to the topsides for the first five years of service, according to McEvilly.
Heerema Marine Contractor’s Balder deepwater construction vessel installed the mooring system, and Harvey Gulf’s War Horse and War Horse II vessels towed the hull 515 nautical miles to location in February 2014, where it was upended, ballasted and anchored in position with nine mooring lines.
The topsides were installed the following month. Crowley’s Ocean Wind and Pilot tug boats, and its Marmack 303 barge, towed the production platform, which was installed by the Saipem 7000. Heerema’s Balder conducted the heavy lifts, including recovering and hanging off the risers for connection to the FPS.
“The hull and FPS installations were very efficient,” McEvilly reports. “Everything was performed as planned. That does not happen without a lot of hard work from a lot of very capable people.”
Two eight-inch subsea production flowlines and one eight-inch water injection line tie to the FPS. The export system from the FPS consists of two 12-inch oil and natural gas lines that span 16 miles before connecting to the 18-inch Williams Mountaineer (oil) and Canyon Chief (gas) pipeline systems for transport to a Chevron-operated shore terminal at Empire, La.
“Tubular Bells is our first FPS in the Gulf of Mexico, and the first FPS built entirely in the United States,” McEvilly relates. “In fact, all aspects of engineering and constructing the project were conducted almost entirely within the United States.”
The Gulfstar One hull was fabricated at Ingleside and Aransas Pass, Tx., and the topsides were constructed at Houma, La., by Gulf Island LLC (topsides, living quarters and hull section), Gulf Island Marine Fabricators (hull section and water-tight flats), Gulf Marine Fabricators (hull fabrication), Signal International (hull sections), Dolphin Services (hull spool piping, topsides alloy spool piping, pipeline end terminals, pipeline end manifolds, and in-line structures), Intermoor (suction piles), and NRG Manufacturing (subsea manifold and chemical tanks). Wood Group Mustang engineered and designed the topside facilities.
“Creating 7,000-plus direct and indirect jobs from the topsides and FPS hull fabrication work in the United States certainly was rewarding for Hess,” McEvilly says. “We may not be able to make that happen on every project, but we did on this one. It was satisfying to everybody in the group that we were able to help stimulate the area economies.”
The hull measures 85 feet in diameter and weighs 15,000 short tons, McEvilly says. The base operating crew, for both day and night shifts, consists of 32 employees. A 50-man quarters also has room for vendors and suppliers, McEvilly points out.
Subsea Architecture
Figure 1 shows a representation of the Tubular Bells subsea infrastructure. It includes two drill centers, a manifold to accommodate future production tie-ins, more than 28 miles of dual flowlines, water injection line, and the umbilical.
The 584-foot long hull is shown here in February 2014 as it was making its way through Aransas Pass along a 515-nautical-mile journey from Gulf Marine Fabricators’ facility in Ingleside, Tx., to Mississippi Canyon 724. Once on location, the hull was upended, ballasted and moored in position.
Major contractors of the subsea architecture were Technip (design, engineering, fabrication and installation of flowlines, steel catenary risers, pipeline end terminations, pipeline end manifolds, piles and structures), Weatherford (subsea control system), Oceaneering (umbilical system), FMC (subsea tree and equipment), Subsea 7 (installation of umbilicals, flying leads, production manifold and jumpers), and ClampOn (subsea acoustic sand and pig detection). Tenaris provided almost nine miles of eight-inch line pipe and the riser pipe.
The subsea tree is critical to successfully meeting the production challenges associated with the high pressures and temperatures, McEvilly says. The project uses an enhanced vertical deepwater tree (EVDT) from FMC that is similar in design to the tree that set a water depth record of 9,627 feet at Shell’s Tobago Field in the Gulf of Mexico Perdido Foldbelt.
“It is a monobore system that combines the safety and reliability features of a vertical tree with the operational benefits of a horizontal tree, so it gives us the best of both worlds, so to speak,” McEvilly remarks. “The tree is rated to 350 degrees and 15,000 psi. Working with FMC as one of the trusted partners in the Tubular Bells project team, we optimized the EVDT for this implementation.”
Trust and teamwork not only epitomize the engineering work on the subsea aspects of the project, but were the hallmarks of all phases of the Tubular Bells development, McEvilly holds. “Hess’ drilling and subsurface development teams worked hand in hand to ensure success without compromising safety to determine the bottom-hole locations and other key factors during drilling, and that kind of teamwork continued all the way through to commissioning the production system,” he says. “Hess had the insight to form lean and efficient teams of experienced people empowered to make decisions, and allowed them to leverage the skills of the suppliers and contractors to extract additional knowledge.”
The cooperative spirit extended to Hess’ co-owner, Chevron, as well as all the key service and technology providers. “At every point in the development timeline, there were numerous examples of teamwork between Hess, Chevron, and all the various contractors,” McEvilly relates. “It takes time to gain the trust factor, and we did that with Chevron. We kept (Chevron team members) engaged and utilized their experience throughout.
The 7,500-ton, three-level topsides departed Houma, La., in March 2014 in route to the Tubular Bells Field. The FPS was the first classic spar facility to be built entirely in the United States, with the topsides and hull fabrication work creating thousands of jobs in multiple states.
“We also have a great deal of confidence in our technology partners,” he adds. “Close collaboration among all parties involved is a major reason for Tubular Bells’ success.”
The teamwork also enabled Hess to bring in the project on budget, although final budget figures could change if the co-owners add more wells, McEvilly points out. “Considering that some offshore ‘megaprojects’ have been mega budget busters, our achievement of being on budget is commendable,” he insists.
Rewarding Achievement
The success of Tubular Bells is even more rewarding, given that it is Hess’ first operated deepwater development with an FPS in the Gulf of Mexico. “To put this project in perspective, Hess never had a deepwater floating facility in the Gulf prior to Tubular Bells, and it has been 10 years since our initial success offshore Equatorial Guinea on the Okume complex. It is very satisfying from our end,” McEvilly affirms.
In addition to holding down costs and working together, safety was a major priority as well during all phases of field development, including FPS construction and installation, he goes on. “Success on Tubular Bells did not come by compromising on safety,” McEvilly insists. “We had a very good safety record on this project, including a total recordable incident rate of 0.29 incidences per 200,000 man hours. There were no catastrophic incidents, no damage to the facility, and no lost-time incidents.
The Saipem 7000 heavy‐lift vessel installs the topsides on the classic spar hull stationed in more than 4,000 feet of water. Production operations commenced within eight months of the date of this photo, completing a fast-track schedule that brought Tubular Bells from project sanctioning to first oil in the span of three years.
“We talk about safety constantly,” he mentions. “We look at safety as a competitive differentiator for Hess. You can have the best reservoir and best facility in the world, but if you have major safety incidents, nothing else will matter.”
During drilling with the Stena Forth, a dynamically positioned Class 3 drill ship, safety factors were crucial when drilling through the massive salt sheets and optimizing the bottom-hole locations, he says.
“As you come out of the salt, there is a potential pressure differential that creates the risk for well control,” McEvilly observes. “We had to anticipate that and mitigate risk as we moved forward. Also, because of the exclusion zone at the salt face, there is potential for a sidetrack, so you want to set yourself up for success in the event you do not find your objective. You would have an open-hole sidetrack as opposed to a cased hole, which can cost $10 million versus $40 million.”
The first well drilled at Tubular Bells was well B, followed by well D and then well A, with the company effectively moving from a P50 drilling operation on well B to a P10 on well A, McEvilly says, because of vigilance in applying lessons learned and continually checking and adjusting operations to ensure a high level of drilling performance.
“At the end of the day, we worked to minimize nonproductive time without sacrificing quality and safety,” he insists. “That is where we want to be, not just from a drilling and completions standpoint, but from an overall project execution and development perspective. If you look at independent benchmarking of industry projects, we were within the top quartile in each of the key areas on Tubular Bells.”
For Hess, the lessons learned in the fast-track development of Tubular Bells will be leveraged to help ensure success on other projects, McEvilly notes. That includes international developments (Hess has offshore operations in the North Sea, West Africa and Asia) as well as in the Gulf of Mexico (Hess’ deepwater Gulf inventory includes about 200 blocks).
“We are in the post-appraisal stage in the deepwater Tano project offshore Ghana, and I and other members of the Tubular Bells project are transitioning to West Africa as well as other opportunities throughout the world,” he says. “The objective is to build off what we accomplished at Tubular Bells.”
Another project Hess hopes to build on is Stampede, located in more than 3,500 feet of water at Green Canyon Blocks 468, 511 and 512. One of the world’s deepest fields with reservoir depths up to 30,000 feet, Hess and its co-owners sanctioned Stampede (unitizing the former Knotty Head and Pony subsalt discoveries) last October. Hess is operator with a 25 percent working interest, with Chevron subsidiary Union Oil Company of California, Statoil, and Nexen Petroleum Offshore U.S.A. each holding 25 percent working interests.
Stampede is estimated to hold 300 million-350 million boe of estimated recoverable resources. Initial plans for the estimated $6 billion field development call for six subsea production wells and four water injection wells tied to a tension leg platform with gross topsides capacity to process 80,000 barrels of oil a day. The first rig in a planned two-rig drilling program is expected to begin drilling in the fourth quarter, with first production in 2018.
For other great articles about exploration, drilling, completions and production, subscribe to The American Oil & Gas Reporter and bookmark www.aogr.com.