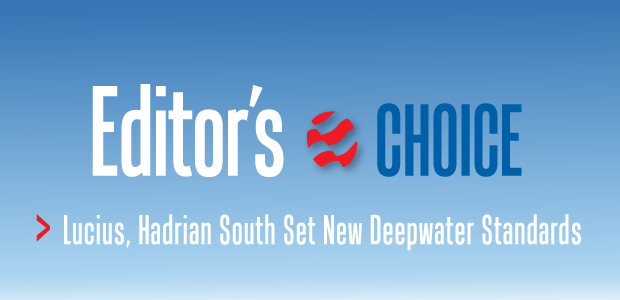
Fast-Tracking Offshore Projects
Lucius Truss Spar Project Sets Standard For Heidelberg, Future Anadarko Developments
By Matt Lamey, Joe Gayneaux, Danny Hart and Tim Arthur
HOUSTON–Utilizing a “design one, build two (or more)” production facilities approach, Anadarko Petroleum Corp. and its partners achieved first oil on a newly installed truss spar at the deepwater Gulf of Mexico Lucius Field on Jan. 16, 2015. One year later and some 100 miles to the northeast, production commenced significantly ahead of schedule on a “sister” truss spar at the Heidelberg Field.
The look-alike spars are both 110 feet in diameter and 605 feet long, with hulls weighing 23,000 tons. Stationed in 7,000 feet of water at Keathley Canyon 875, the Lucius spar has a daily capacity of 80,000 barrels of oil and 450 million cubic feet of gas. The Heidelberg spar is in 5,300 feet of water at Green Canyon 859 and has a capacity of 80,000 bbl/d and 80 MMcf/d. Lucius was brought online just over three years after project sanctioning, and Heidelberg achieved first oil only 32 months after sanctioning.
The Lucius spar design was meant to be flexible. The benefits of using the same standard design for multiple projects include less time to sanctioning, reduced engineering charges, expedited order placement, ease of contracting, certainty of design and scheduling, and enabling the exchange of parts, personnel, equipment, etc. The synergies and efficiencies created by this strategy helped Anadarko produce first oil at Heidelberg–the first field development to replicate the Lucius spar design–ahead of schedule and under budget.
In fact, Anadarko was able to move from concept selection to cutting first steel for Heidelberg spar’s hull within six months, and from concept selection to cutting first steel on the topsides in only 12 months. In addition, Anadarko reduced the number of engineering man-hours for Heidelberg’s hull and topsides by 17 and 24 percent, respectively, and the fabrication man-hours by 16 and 17 percent, compared with its Lucius twin.
Lucius (Keathley Canyon 874, 875, 918 and 919) is estimated to contain more than 300 million barrels of recoverable oil-equivalent reserves, while Heidelberg (Green Canyon 859, 860, 903, 904 and 948) holds an estimated 200 million-400 million boe of recoverable resources. Anadarko is operator of both projects (Figure 1). ExxonMobil, Plains Offshore Operators/PXP Offshore, Petrobras, Eni and Teikoku (Inpex) are partners on Lucius; and Eni, ExxonMobil, Marubeni Oil & Gas, Freeport-McMoRan, Statoil and Cobalt International Energy are partners on Heidelberg.
An additional strategic consideration at Lucius was implementing a hub-and-spoke development philosophy–the first spar host facility built by Anadarko since 2006. It was designed not only to accommodate the initial six wet-tree Lucius oil wells in the southeast corner of Keathley Canyon, but also to host two subsea well tiebacks from ExxonMobil Development Co.’s Hadrian South natural gas field, located eight miles to the southeast in 7,500 feet of water at Keathley Canyon 964 (ExxonMobil’s deepest subsea tieback). The 300 MMcf/d tieback was executed in parallel with the Lucius development, and achieved first production in March 2015.
The ability to successfully execute a project as large and complex as Lucius on a fast-track timeline can be credited largely to Anadarko’s development strategy of utilizing a core group of proven, trusted suppliers, and to close cooperation between the Lucius and Hadrian South project teams. Based on Anadarko’s experience on Lucius, several staffing and organizational changes were recommended for future major projects, including Heidelberg. The recommendations primarily enhance compliance efforts with Safety and Environmental Management Systems (SEMS) regulations, the predictability of equipment delivery for fabricating topsides, and managing offshore hookup and commissioning efforts.
Concept Selection
Figure 2 shows a simplified geological interpretation of the Lucius Field. The discovery well was drilled to a total depth of 20,000 feet by the ENSCO 8500 drill ship in late 2009, penetrating a 200-foot subsalt Pliocene oil column. A successful appraisal well reached TD in early 2011, and a well test was performed on the discovery well in May 2011.
Delineation and testing showed the Lucius Field had thick pay zones consolidated in a relatively compact area. The relatively shallow Pliocene formation also made drilling and completion far less costly than in a deeper formation such as the Lower Tertiary.
Anadarko assembled a team consisting of exploration, development, drilling, completion, facility, marketing and operations to begin evaluating Lucius development options in mid-2010. The team considered stand-alone floating facilities based on both a truss spar and semisubmersible. Even though there is potentially more offshore installation work in integrating topsides to a spar hull than a semisubmersible, the company believed its long-standing experience in designing, building and operating spar hulls would work favorably for the project, despite the work.
Moreover, a truss spar could utilize three groups of mooring lines, while four groups of mooring lines associated with a semisubmersible would have been difficult to implement, given geotechnical challenges identified on site. The project also had to consider how to locate the facility to avoid landing umbilicals and steel catenary risers (SCRs) in less desirable areas with slopes and unstable surfaces.
A wet-tree truss spar ultimately was chosen as the development concept. This option yielded the best project economic metrics, considering full life-cycle economics. In general, Anadarko tended toward known technology, and proven methods and suppliers/fabricators with a history of delivering successfully for the company, not only for the hull and mooring, but also for other aspects of the facility.
Anadarko previously had utilized truss spar technology on its deepwater Boomvang, Nansen, Gunnison and Constitution fields. Although Lucius would be larger than any of its previous spar facilities, the experience on those projects gave the company confidence in designing, fabricating, and installing the hull and mooring facilities within the budget and schedule, which was accomplished.
Largest Possible Combination
Because of the remoteness of the location, and the exploration and discovery activity around Lucius, Anadarko elected the largest possible hull/topsides combination that could reasonably be built, given fabrication yard and installation vessel capabilities. The May 2011 production test of the discovery well reinforced the direction the development team had pursued initially. The facilities development team had begun engineering on the largest eight-section hull the spar supplier could fabricate in half sections in its “high hall.”
Meanwhile, the topsides engineering team was developing topsides that could not only support maximum production from four initial, 8.0-inch diameter SCRs for Lucius, but also accommodate a waterflood at an appropriate point in the future. The hull team worked cooperatively with the subsea engineering team to develop the concepts for pull tubes to support risers for future tiebacks. The topsides manifold and allocation metering also were set up for future tiebacks.
When ExxonMobil approached the Lucius partnership to inquire about adding risers and facilities to accommodate 300 MMcf/d of production from the Hadrian South gas/condensate development, the integrated team began incorporating facilities for Hadrian South in Lucius’ engineering work. By mid-2011, Lucius reservoir and facility engineering (including the Hadrian South tiebacks) had advanced enough to justify purchasing long-lead equipment and steel to begin fabricating the hull.
Simultaneously, the oil and gas export-line option evaluation had been done to select providers based on primary commercial terms. Detailed terms and conditions were negotiated while orders for the line pipe were made, along with advancing negotiations with installation companies. Additional development drilling commenced at Lucius in late 2012, and all six initial production wells were completed by the end of 2014.
Hadrian South is a reasonably straightforward gas/condensate development that utilizes methanol injection at the wellhead as the primary means of flow assurance. The subsea system consists of looped flowlines to enable pigging. The loop is completed with a spool on the manifold. The system is designed so that each of the two wells can be routed up individual, nominal 10-inch carbon steel flowlines connected to risers on the Lucius spar. The system includes a four-well manifold so additional wells can be added easily.
The subsea trees allow for rates up to 200 MMcf/d a well. The Aker Solutions’ tree control systems are hydroelectric multiplexed. The single umbilical for Hadrian South delivers chemicals, methanol, low-dosage hydrate inhibitors, controls, hydraulics and communications to the well sites. All subsea equipment was installed safely and successfully by ExxonMobil in the latter half of 2014.
Contracting Philosophy
Most major contracts were signed either at project sanctioning or soon thereafter for the hull and mooring fabrication, topsides fabrication, topsides installation, flowline fabrication and installation, and subsea installation. The Hadrian South topsides design was completed in mid-2012, and all equipment was ordered at that time.
The key contracting entities from prior Anadarko spar projects were invited to submit proposals for the Lucius facility. A design basis was generated to identify known differences between the last spar development, Constitution, and Lucius. Multiple entities bid on the topsides fabrication. Heerema Marine Contractors estimated the cost of installing the facilities as well as the flowlines/risers, and Technip Offshore estimated hull/moorings fabrication and delivery costs.
Since prior spar projects had been bid competitively, the team had sufficient data to benchmark the competitiveness of the proposal for the hull/mooring and installation contracts, thereby satisfying internal accounting requirements. Contracts for subsea equipment and installation, topsides equipment, etc., were tendered competitively.
Wood Group Mustang provided front-end engineering design, detailed design, procurement support, and engineering support for the fabrication and offshore construction effort, including administering an effective project change management system. The topsides engineering contractor employed a combined strategy of competitive bidding and sole-source awarding, based on historical client project data, operational experience, and input solicited from equipment vendors to determine optimal pricing and delivery schedules for topsides equipment.
Wood Group Kenny provided detailed design, procurement support, and engineering support for fabricating the subsea facilities (Figure 3). The subsea engineering contractor solicited input from key equipment vendors to determine subsea equipment pricing levels and delivery schedules. Most subsea equipment was sole-sourced. Long-term relationships with key suppliers played a big part in delivering the subsea components in a timely fashion.
Hull And Risers
As shown in Figure 4, the Lucius hull’s hard tank extends below the mean waterline to provide buoyancy. The truss section is fitted with two heave plates and connects the hard tank–designed for full hydrostatic pressure–to the soft tank, which provides buoyancy only during the float-off, horizontal tow-out, and the initial upending phase. An important function of the soft tank was containing the solid ballast needed to stabilize the platform once the hull was up-righted on location.
The center well inside the hard tank is sized for 10 flowline risers, 10 umbilicals and two flexible flowlines, as well as import and export flowlines. The total hull weight is 22,300 short tons, excluding the solid ballast (12,400 tons). The hull also stores 2,900 barrels of methanol in a cofferdam area above the waterline.
The mooring system consists of nine legs, laid out in three groups of three. From bottom to top, each mooring line is composed of a 112-foot long suction anchor (18 feet in diameter) fitted with 92 feet of pile chain and 300-350 feet of ground chain, two 5,000-foot polyester rope sections (10 inches in diameter), two 45-foot long polyester rope test inserts, and a 1,000-foot long spar chain segment. Subsea connectors allowed the piles to be preinstalled.
Lucius uses four umbilical slots while Hadrian South uses one. All risers are 8.625-inch outside dimeter risers with a 9,300-psig design pressure. The Lucius risers are insulated with a glass flake syntactic polyurethane wet system for flow assurance. The Hadrian risers did not require insulation, but were built identically to make them suitable for oil service, with a view that they might one day be reused.
The production lines run through pull tubes and guides from the bottom and outside of the truss to the top of the hard tank inside the center well. The umbilical and future tieback lines run through the soft tank, and up the truss and hard tank through guides.
Each Lucius riser pair has one control/chemical umbilical and one gas lift umbilical running to the base of the riser for enhanced recovery and flow assurance. The chemical umbilical can deliver low-dosage hydrate inhibitors, methanol, corrosion inhibitor, asphaltene inhibitor, xylene, and paraffin inhibitor to each well. The pipeline end manifolds have spare connections for future wells, and removable pigging loops to allow additional tiebacks.
The spar is designed to support two additional subsea tiebacks, each consisting of two flowlines and two umbilicals. One umbilical is assumed for controls/chemical injection, and the other for artificial lift. The pull tube design for future risers was intended to accommodate an insulated 15,000-psig, 8.0-inch riser, but sensitivities also were done to check for a 10,000-psig, 6.0-inch gas riser to make the design flexible enough to accommodate a range of options. Guides above the keel were designed to accommodate SCRs or flexible pipe.
In addition, the spar accommodates two, 10-inch flexible flowlines for future waterflooding. The flexibles are intended to come in through the center section on the keel and go through guides to the spar deck, similar to the umbilicals. These slots can be used for additional umbilicals also.
The top of the soft tank is fitted with porches to receive the fitting on the titanium stress joint (TSJ) for each of the two 16-inch gas and oil export SCRs. Installing the SCRs after setting the topsides required using an installation beam, turning sheaves, and a chain jack on the main deck.
Topsides Design
The main deck of the facility is 158 feet above the water surface, and the production deck is 125 feet above water level. The elevation of the top of the spar is 55 feet. The maximum design weight of the topsides is 16,000 tons, with an initial weight of 14,000 tons. Considerable flexibility is built into the processing system, and the separation facilities include a high-pressure/intermediate-pressure/low-pressure primary oil train, an HP/IP/LP secondary oil train, an HP gas train, and an HP test separator.
Compression requirements are handled by two single-motor-driven vapor recovery units and two gas engine-driven, flash gas reciprocating compressors. Provisions also were made for two turbine-driven boost compressors. Power is provided by three primary generators, an auxiliary generator, and an emergency generator.
Accommodations are provided for a 44-man permanent crew and an additional 24 temporary personnel. Two 60-ton cranes provide the ability to load on both the east and west sides of facility using reeled loading hoses.
To coordinate changes during design, topsides fabrication and installation, a project change control system was used during various stages of the project, with captured changes related appropriately to key drawings and documents during the pre-startup review. Once the PSR was complete and the facility was started, the spar transitioned to the operations management of change procedures. Processes and procedures complied with both internal and external guidance on Gulf of Mexico SEMS rules, but allowed the flexibility to suit the particular phase of the project.
Topsides fabrication was undertaken at Kiewit Offshore Services’ yard at Ingleside, Tx. Large modules for the boost compressors, production system, fuel gas system, etc., were fabricated in Dolphin Services LLC’s facility in Houma, La. The living quarters were fabricated at Beacon Maritime in Orange, Tx.
The subcellar deck and temporary work deck were assembled at Kiewit’s yard and integrated with the hull on location after the hull had been upended and secured. A heavy lift vessel installed both the hull and mooring, as well as the subcellar and temporary work decks, which enabled the flowline risers and umbilicals to be installed prior to shipping the main deck to site.
All other topsides components were shipped on different barges. The temporary work deck was removed and the topsides components were installed successfully and safely. Figure 5 shows a diagram of the various lifts made on site.
Once on site, the accommodation vessel was used to quarter a construction workforce of up to 500 during integration and commissioning from April to December 2014. The vessel had an articulating gangway that allowed continued access to the topsides, and rest and meals away from the main spar while it was being commissioned.
Export Lines
Enterprise Products Partners designed, installed and operates the oil export pipelines, while Discovery Producer Services (Williams) designed, installed and operates the gas export pipeline. The oil export is an 18-inch line that takes processed oil from the Lucius platform north to the South Marsh Island 205 shallow-water platform, where it can be transported in the Auger or Poseidon systems. Allseas installed the oil export line on schedule and without incident.
The Keathley Canyon Connector export gas line transports gas from Lucius almost 209 miles through a 20-inch line to a new, shallow-water platform in South Timbalier 283. From there, it is transported through a 30-inch pipeline to a processing plant in Larose, La., which was upgraded to scrub vapor-phase methanol from the gas prior to entering the plant.
Because of difficulties in achieving rate with the air compressors used for dewatering, the gas export company engineered and successfully executed midline dewatering to reduce head pressure and allow better rate performance when it later continued air injection at the spar. Dewatering and nitrogen packing were completed in December 2014.
Both oil and gas export lines terminate at a pipeline end manifold (PLEM) 1.5 miles north of Lucius. From there, Anadarko was responsible for connecting the jumper and subsea connector, another riser base PLEM, the riser itself, and the TSJ that connects each riser to the soft tank on the hull. Both risers were installed after the topsides had been set. Both oil and gas export lines were ready to receive hydrocarbons ahead of the first production date.
Installation Program
The installation program was segmented in five phases. Heerema Marine Contractors was responsible for the first four installation phases: the mooring suction anchors; hull, mooring and subcellar/work decks; topsides; and flowlines/risers. Technip was responsible for the fifth phase, which involved installing the subsea system (umbilicals, flexible flowlines, and flowline jumpers).
The offshore campaign began by successfully installing all nine suction anchors in April 2013. The hull was wet-towed to site and installed in September 2013, along with the subcellar and work decks. Flowline, subsea and related facility installation began in late 2013 and continued through early 2014, along with various topsides integration efforts.
Meanwhile, various elements of Hadrian South’s facilities were installed by an independent vessel, and the heavy lift vessel was preparing for the arrival of the Lucius topsides in early 2014. The gas export line was being installed simultaneously off location by yet another independent contractor.
As many as five installation vessels were in the area at the same time. The simultaneous operations were managed without incident by having all involved parties supply their detailed scheduling information to one of the other installation contractors that had the best view of the overall plan, thereby managing integration into a detailed schedule. Weekly meetings among all involved contractors and both Lucius and Hadrian South operators kept the information coordinated and strengthened the simultaneous operations, despite day-to-day weather and logistical challenges.
Installing the subsea systems was integrated successfully among a number of other critical project activities. Several vessels were used for various phases of the installation, hookup and commissioning.
At nearly 10,000 tons, the main topsides module lift was a record for the installation vessel (Figure 6). Subsequent module lifts were completed by a separate installation vessel for the accommodation module (about 1,000 tons) and the two gas compression modules (650 tons each).
Installing the export riser after setting the topsides versus before (as originally planned) was the most significant impact to the overall offshore integration schedule. It required designing, procuring and installing the largest chain jack of its kind. The export chain jack work and export riser installation were completed successfully by July 2014, and the equipment was demobilized by August 2014.
Offshore construction on the topsides was completed in mid-November 2014, with the rest of November and most of December devoted to commissioning, including leak testing, initial liquid fills, logic testing, and validating safety devices. Lucius was commissioned and started first because the oil export system was needed for processing the condensate from Hadrian South.
Achieving first oil only five years after discovery is commendable for a project of this scale. Effectively managing the myriad interfaces in such a complex project was critical to overall success. Perhaps most importantly, the team’s safety performance was outstanding. Overall, a total recordable injury rate of less than 0.4 was achieved on a project that amassed more than 10.5 million man-hours of execution, including 1.5 million man-hours for offshore integration.
The cooperation among the operators of Lucius and Hadrian South and all contractors involved was exemplary, resulting in all operations being safely and successfully executed.
Editor’s Note: The authors acknowledge Anadarko Petroleum’s technical leads and in-house contractors, ExxonMobil Development Company’s Hadrian South team, Technip Offshore and its affiliates, Heerema Marine Contractors, Kiewit Offshore Services, Gulf Island Fabricators/Dolphin Services, W-Industries, CANUSA, the Edda Accommodation Company, GATE, Wood Group Kenny, and Wood Group Mustang for providing support to the project.
Matt Lamey is a deepwater facilities engineering manager at Anadarko Petroleum Corp., and served as project manager for Lucius facilities construction from 2010 through production ramp-up in 2015. He has nearly 35 years of industry experience, 20 of which have been spent in deepwater offshore production facilities surveillance, operations support, and facilities engineering and construction. Lamey has been with Anadarko for nearly 15 years, primarily managing major Gulf of Mexico and international offshore projects. He holds a bachelor’s in chemical engineering from Montana State University.
Joe Gayneaux is a staff facilities engineer at Anadarko Petroleum Corp., and served as topsides engineering lead, and hookup and commissioning manager on the Lucius facility. Before joining the company’s deepwater facilities project management team in 2010, he was a project engineer at Universal Pegasus International and a production/construction consultant at K&D Production Specialties Inc. He holds a B.S. in petroleum engineering and an M.B.A. from the University of Louisiana at Lafayette.
Danny Hart is a general manager at Anadarko Petroleum Corp. and served as general manager of the Lucius project starting in 2009. He has 21 years of experience with Anadarko, including eight years in deepwater development. Hart has served at Anadarko in multiple capacities, including general manager of the Delaware Basin, South American development, and investor relations manager. He holds a bachelor’s in petroleum engineering from Texas Tech University.
Tim Arthur is the Gulf of Mexico senior project manager, including Hadrian South, for ExxonMobil Development Company. He has spent more than 35 years working for ExxonMobil and more than 30 years working on major Gulf of Mexico and international offshore projects. Arthur holds a B.S. in ocean engineering from the United States Coast Guard Academy.
For other great articles about exploration, drilling, completions and production, subscribe to The American Oil & Gas Reporter and bookmark www.aogr.com.