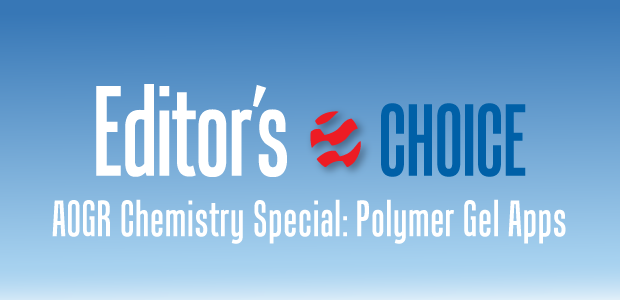
Today’s Treatments Enhance Well Economics, Optimize IOR/EOR Projects
By Randy Prater, Daniel French and Mehdi Salehi
PLAINVILLE, KS.–The use of polymer gel technology, while sometimes overlooked, is an effective means to improve economics and help overcome various challenges that can pop up in new and mature producing wells. Polymer gel aids in waterflood applications, but has also been used to aid in water shutoff with its ability to reduce reservoir permeability and eliminate casing leaks without the expense of a packer, patch or squeeze job. However, polymer gel’s ability to improve conformance makes this technology an integral part of a long-term production strategy.
The success of a secondary recovery or waterflood project depends on the method by which the injected fluid displaces the oil (displacement efficiency) and the volume of the reservoir that is contacted by the injected fluid (sweep efficiency). In the early 1960s, it was realized that blocking or plugging materials could be used to divert water from high-permeability flow channels into lower-permeability rock.
Hence, cross-linked bulk gel systems were developed and designed for near-wellbore problems related to water encroachment in producing wells and channeling of water out-of-zone in injectors. The former application of polymer gel systems is called a water shutoff application designed to address excess water production, and the latter typically is referred to as conformance and profile modification application designed to address reservoir heterogeneity. Bulk gel chemistry is robust and can be used in most waters and relatively high temperatures (<300 degrees Fahrenheit).
Water shutoff operations are designed to target the influx of water production through coning or channeling due to geological anomalies such as vugs, natural fractures or permeability contrast. During the process, gelant is injected into the reservoir at a rate under frac gradient targeting zones that contribute to significant water volumes. The gel forms under temperature, blocking water and modifying the drainage pattern to the wellbore in favor of increased oil production. Typical treatments result in as much as a 90% reduction in water and a 20%-30% increase in daily oil rates, to as much as a 1,000% increase in oil production after treatment. Additional benefits include reduced expenses for high water production volumes, such as electricity and chemical costs.
Conformance Treatments
Conformance/profile modification targets inefficient flood patterns to improve oil production by redirecting injection fluid to lower-permeability or tighter unswept portions of the reservoir. Conformance treatments address high-permeability streaks known as thief zones by blocking these areas deep into the reservoir, forcing the injection fluid around the gel block into tighter, oil-saturated rock. This results in the mobilization of bypassed oil to offset production wells, often resulting in significantly increased reserve recovery. Profile modification treatments address injection profile inefficiencies by directing injection fluids more proportionally when multiple zones are open. In many cases, the majority of fluid favors one or two intervals. As a result, injection fluid is forced into neglected intervals to increase oil production.
When managing a casing leak, ultralow-molecular-weight polymers, plus cross-linkers are advantageous in treating tight or pinhole casing leaks where cement cannot penetrate or hold. After successfully penetrating the offending area, the polymer can be set up as a rigid ringing gel. This process can eliminate the need for permanent mechanical solutions (i.e., liners) that can restrict production. In addition, this process does not require drilling out, making it considerably more cost-effective for the operator.
When strong channeling communication exists from injection wells to producing wells, waterflood performance can be compromised—sometimes severely. Large quantities of water may be cycled through the formation, resulting in limited development of an oil bank, limited contact with oil-saturated rock, and high water handling costs to produce a limited volume of oil. The bulk gel is injected into the formation, which blocks the strong channels, forcing subsequent water injection to move into tighter, oil-saturated rock.
Bulk gels are injected into the formations as a gelant solution, a pre-gel containing both polymer and cross-linker. The gelant moves into the predominant water flow path, which is the most permeable zone (fractures or permeable matrix rock). The gel forms after it is in the formation. For practical purposes, bulk gels provide a complete shutoff of water flow in the zones in which they are placed.
Candidates for injection well bulk gel treatments are patterns where rapid channels or thief zones exist. An important consideration is that a significant amount of bypassed oil may be left in place that can be easily recovered through a gel treatment.
The injection well must be able to accept the gel, which has a substantially higher viscosity than water. Another consideration is that the operator should be prepared to commit to a pattern for a minimum of several months without making changes after the gel treatment is placed. This is very important to determine incremental oil recovery through post-treatment evaluation.
In a conformance gel treatment, the goal is to fill the largest possible portion of the conductive channels from the injection well to one or more offset producers. Several strategies can be used to size gel treatments, and all of them fall under the general categories of volume or distance. A volume sizing strategy refers to filling a portion of the channel volume from the injector to the producer(s). A distance strategy refers to placing the gel at a specified distance from the injection well.
The best method is to size the treatment as a percent of the movable pore volume in the channel. Once the channel volume is determined, a decision must be made regarding how much of the channel’s volume to fill with gel. With a small volume, it may be economically feasible to fill the entire channel. If the channel volume is large, it may not be economically viable to fill the entire channel; typically, a percentage is considered. Experience suggests that “bigger is better.”
Bulk gels usually are processed and injected using mobile or portable process system plants, including all chemical process subsystems and the primary injection pumps combined into a single, integrated mobile facility.
Monitoring the treatment during application is at least as important as planning, sizing and designing the treatment. Each formation may respond differently than expected to the treatment, and decisions must be made in the field to alter the treatment as necessary in response to the reservoir. These changes may involve pumping a smaller or larger treatment, increasing or decreasing the chemical concentrations, changing the pump rate, or even shutting off producers.
North Slope Case Study
The Kuparuk River Field on the Alaska North Slope is a structural-stratigraphic trap consisting of two productive sands: Sand A with low permeability and the high-permeability C sand. The field has more than 1,100 wells under waterflood and miscible or immiscible water-alternating-gas. Extensive faulting and drastic permeability distribution in the C sand has resulted in severed communication between injectors and their offset producers, instigating high water production and low sweep efficiency.
Injector Well I-1 initially was drilled as a single wellbore, completed to inject into the Kuparuk C sand. To increase the injectivity and support the offset production, two sidetracks were completed later in the C4, C2 and C1 sands. After sidetracks, the average injectivity of this well was about six barrels a day per psi and at times showed as high as 11 bbl/d per psi while the field average for similar wells was one-five bbl/d per psi.
Quick communication between this injector and its offset producers was confirmed by immediate gas breakthrough to the offsets during miscible gas injection. An interwell tracer study also showed 30.2% of the injected tracer at injector I-1 recovered in three offset producers in 16-22 days, indicating quick communication through highly conductive features/faults.
A polymer gel conformance treatment was recommended to address the communication and improve the oil recovery in this pattern. Use of high-molecular weight cross-linked polymer was specifically suggested to avoid penetration into the matrix with lower permeability. Roughly 20,000 barrels of high-molecular-weight polymer was injected in stages from 3,000 to 10,000 ppm at a 40-to-1 polymer-to-cross-linker ratio. The injectivity was reduced from 7.0 bb/d to 1.3 bbl/d per psi during the treatment (Figure 1).
The polymer gel was placed in the high-permeability feature responsible for high water production, quick gas breakthrough and low sweep efficiency in this pattern without damaging the low-permeability rock. The conformance treatment had an immediate impact on the injectivity of injector I-1, indicating the injection fluid was being diverted onto unswept areas of the reservoir (Figure 2). Increased delay in gas breakthrough and increase in oil production (Figure 3) proves that the means of communication was addressed.
In summary, polymer gel conformance treatment resulted in total incremental oil of 460,000 barrels at an effective incremental rate of 630 bbl/d for the pattern. Incremental oil production had to be corrected for the time that injector I-1 was down until it returned to normal injection. A temporary decline in the trend of incremental oil production can be observed, which is due to a lack of miscible gas injection in the pad.
West Texas Case Study
A cross-linked polymer gel solution also was applied in one of the first waterfloods in a West Texas carbonate reservoir. The field was discovered in 1953, and because of low original pressure, was put on waterflood in 1956. The field produces from the naturally fractured Permian-age Grayburg carbonate, with a starting depth of 4,700 feet and a maximum pay of 150 feet. The average porosity is 12% and the permeability ranges from less than 1 milliDarcy to over 1 Darcy, resulting in a Dykstra Parsons factor of 0.82. This reservoir heterogeneity resulted in lower-than-expected waterflood recovery factors in some areas of the field.
The customer identified a significant number of waterflood patterns that suffered from severe communication between injectors and their offset producers. High water production and poor sweep efficiency led to greater operating costs and lower oil production.
Based on the geological information and waterflood communication analysis using injection/production data, a cross-linked polymer gel solution was recommended to correct the rapid water channeling through fractures and high-permeability streaks. It was determined the MARCIT polymer gel system would be optimal based on reservoir temperature and the injection water total dissolved solids. The gel is made up of a medium molecular weight, partially hydrolyzed polyacrylamide and a cross-linker, which are mixed on the surface using specialty equipment and then injected down hole.
The reaction rate is delayed sufficiently to allow for placement of the gel in the reservoir. Between 2001 and 2006, 24 injectors were treated in four phases using an average gel volume of 16,550 barrels of gel polymer per well with concentrations ranging from 1,500 to 10,000 ppm. Each injection well had an individual gel volume design based off the estimated thief zone volume between the injector and offset producers. The pumped gel volume and concentrations were changed on the fly based on the injection pressure response, which is a good indicator of how effective the gel is filling up the offending reservoir features.
The polymer gel was placed in the high-permeability features and fractures responsible for high water production and low sweep efficiency without damaging the low-permeability rock matrix. Figure 4 shows a typical job log where the injection pressure was increasing continuously throughout the treatment (this pressure increase is promoted by increasing the polymer and cross-linker concentration/gel strength throughout the treatment).
Figure 5 shows the monthly oil rate trend for all 38 offset producers in phases 1 through 4. Note the increase in oil production three months after the first treatment followed by continual oil rate increases and a significant change in the oil production decline throughout the four phases.
Figure 6 shows the water-to-oil ratio versus cumulative oil plot for the area, which clearly shows a change in the WOR trend indicative of sweep improvement. Based on this analysis, the estimated incremental oil was 488,000 barrels. This resulted in an incremental cost per barrel of $4.68, an average payout per phase of 12 months, and a 31% internal rate of return for the field operator.
While the use of polymer gel has been well established throughout the oil and gas industry, emerging innovations have made this established technology gain the attention of operators looking to improve the economics of their wells with its ability to shut off water and enhance the efficiency of improved recovery operations, particularly in the areas of conformance and profile modification.
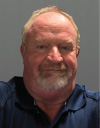
RANDY PRATER is chief executive officer of Polymer Technologies. He has designed and implemented more than 4,000 polymer treatments. Prater began his career in 1977 in well logging, perforating, cementing, stimulation and production chemistry roles. He founded Polymer Services in 1989, specializing in applying polymer gel systems for improved and enhanced oil recovery. Kemira Chemicals acquired Polymer Services in 2015, and Prater served as Kemira’s senior technical manager for IOR until May 2020. He founded Polymer Technologies in 2022. He is a member of the advisory board to the University of Kansas Tertiary Oil Recovery Program. Prater attended Fort Hays State University.
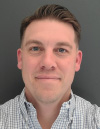
DANIEL FRENCH is vice president of IOR solutions with Polymer Technologies, where he focuses on identifying opportunities to improve asset performance and economics through polymer technologies. Prior to joining Polymer Technologies, French served at an independent Kansas operating company, where he assisted with growth and optimization of oil and gas properties and gained an understanding of the challenges producers face. He also has experience in stimulation and production chemicals. After graduating from Wichita State University with a bachelor’s in entrepreneurship, French joined Polymer Services as a project coordinator.
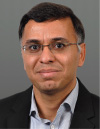
MEHDI SALEHI is a reservoir engineer with Polymer Technologies, responsible for the selection and engineering design of polymer gel, wettability alteration using nanosurfactants, clay stabilizers, injectivity improvement agents and casing leak technologies. Before joining Polymer Technologies, he was a project manager with Surtek, and was EOR group leader at Nalco Champion (ChampionX). Salehi has been conducting research on chemical EOR processes, field development, and deployment of these technologies for more than 15 years. He holds a B.S. in petroleum engineering from Petroleum University of Technology in Iran and an M.S. and Ph.D. in petroleum engineering from the University of Kansas.
For other great articles about exploration, drilling, completions and production, subscribe to The American Oil & Gas Reporter and bookmark www.aogr.com.