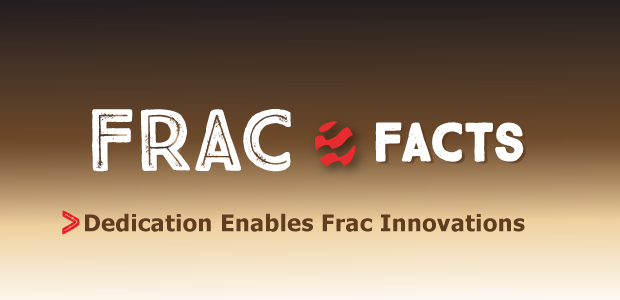
Dedication Enables Frac Innovations
By Colter Cookson
According to Rystad Energy, U.S. operators fractured 49 wells a day in June, five more than May and only one short of the 50-well record set in August 2018. The Permian Basin alone completed almost 550, easily eclipsing August 2018’s regional record of 520 wells.
Since completions account for half of most onshore wells’ costs and drive their economics, many operators devote as much energy to optimizing their completions as modern teenagers pour into Fortnite. Service companies say this has created a receptive market for innovations that can improve completions’ efficiency and effectiveness, including versatile friction reducers, damage-repairing polymer breakers, smart logistics models and more reliable degradable diverters.
Operators’ approach to completion chemistry is becoming increasingly sophisticated, says Jerry Noles, the owner, chief executive officer and technical director of CoilChem LLC. “Instead of depending on pressure pumping companies to select and provide completion chemicals, most operators are sourcing chemicals themselves,” he says. “They recognize how much the completion fluid affects each well’s cost and long-term production.
“When we visit operators’ procurement departments, instead of seeing accountants, we talk with Ph.D.-level chemists who have petroleum engineering experience,” Noles says. “These chemists need to manage costs, but they also know what more effective chemistry can mean for their wells and have the expertise to understand the technical justifications for new approaches. This has created tremendous opportunities for market innovation.”
Noles predicts that the rate at which completion designs improve will accelerate. “As we get better at gathering and interpreting data about completion performance, we are gaining a deeper understanding of the variables that influence where fractures go and how well they conduct fluids to the wellbore,” he explains. “At the same time, electric frac spreads and more sophisticated automation systems are giving us more precise control over those variables.”
Friction Reducers
The trend toward longer laterals has created a need for more effective friction reducers, Noles argues. “As lateral lengths increase, it becomes more difficult to transfer hydraulic force from the surface pumps to the reservoir,” he notes. “Frictional resistance is one of the biggest barriers to that energy transfer, so mitigating friction is essential to an effective completion.
High-viscosity friction reducers are gaining popularity because they enable operators to build completion fluids that combine great proppant transportation characteristics with easy pumpability, CoilChem LLC reports. The company says it is investigating how water quality affects HVFR behavior to develop pretreatment techniques that improve HVFRs’ performance and increase tolerance for high total dissolved solid concentrations.
“The standard FR has long been a polyacrylamide,” Noles mentions. “Polyacrylamides are affordable, but they vary widely in quality, with meaningful swings in molecular weight and activity from manufacturer to manufacturer.”
Noles adds that under specific circumstances, anionic polyacrylamides with extreme charges can attach (cross-link) to negatively charged suspended solids within the water, such as iron, creating blockages that impede flow. Certain polymers maintain charges that are more susceptible to charges within the water.
Because of how readily they can cross-link, certain FRs are a poor fit for water with high iron content, including produced water that has not been treated or diluted adequately. Cationic or positively-charged acrylamides work in low concentrations in produced water that contains a lot of total dissolved solids, but Noles cautions that they tend to be difficult to manufacture in high molecular weights and therefore expensive for meaningful levels of viscosity.
In addition to managing friction, the completion needs to be able to transport the proppant to the fracture, Noles notes. “In the past, we have relied on high viscosity to suspend the particles,” he describes. “However, because viscosity increases resistance to flow, it makes the fluid more difficult to pump.”
High-viscosity friction reducers (HVFRs) offer a way to transport the proppant without compromising pumpability, Noles says. “Instead of using viscosity to suspend the proppant, HVFRs utilize their high elastic modulus to essentially drag the proppant,” he describes. “Dragging requires less energy than suspending or carrying the proppant, so the HVFR can get the proppant to its destination even with lower viscosity levels.”
HVFRs transport proppant more effectively than slickwater completion fluids, which have such low viscosity that they rely on turbulence for proppant transport, while eliminating many of the concerns associated with cross-linked gels. “One of the biggest concerns is formation damage,” Noles says. “To generate enough viscosity to suspend the proppant, cross-linked gels need 18-20 pounds of solids for every thousand gallons of water. These solids get left behind in the fracture network and restrict flow.”
With an 18-20 pound cross-link, Noles says a typical fracture network’s retained conductivity will be approximately 30%. HVFRs’ retained conductivity values often exceed 100%, Noles reports, a benefit that can translate into higher production.
Growing Popularity
To illustrate how effective HVFRs can be, Noles recalls an in-field drilling program in the Eagle Ford Shale. “The reservoir had been partially depleted by earlier wells completed with cross-linked gels, so the operator only expected the new wells to match the original production rates,” he says. “Instead, production doubled. While higher sand concentrations and other variables contributed, one of the biggest contributing factors was how little HVFRs leave in the formation.”
The shear thinning nature of HVFRs may be easier on surface equipment than either cross-linked gels or slickwater, Noles adds. “When we switch from viscous fluids or slickwater to HVFRs, the pumps tend to produce less vibration and noise, and we have seen significant reduction in decibel levels on location. Both point to a decrease in pump cavitation, one of the primary sources of pump degradation.”
HVFRs simplify hybrid completions, which begin with slickwater, then transition to high-viscosity fluids to support higher proppant concentrations, Noles reports. “As the proppant concentrations increase, the operator gradually increases the amount of HVFR in the fluid to achieve the elastic modulus needed to drag the proppant,” he explains. “This lets the operator transition to cross-link-like transportation characteristics without changing the fluid system.”
Noles says HVFRs’ popularity will continue to grow, but cautions that HVFRs are a poor fit for reservoirs with high frac gradients and extreme temperatures.
“The Haynesville Shale is a great example,” he illustrates. “The wells there tend to be deep and hot. HVFRs are shear-sensitive, so by the time they reach the perforation, they have thinned too much to create fractures with enough separation. A cross-linked gel may be harder to pump, but the frictional resistance it creates is helpful for separating the rock and allowing fluid and sand to enter the fractures.
“Every year, HVFRs get better at tolerating variations in fluid chemistry,” Noles says. “For example, we are coming up with HVFRs that perform well in higher TDS fluids. Our goal is to extend TDS tolerances from 50,000-150,000 parts per million to 200,000 ppm to reduce operators’ need to dilute produced water with freshwater when they are building completion fluids.”
CoilChem is investigating how water quality affects HVFR performance and experimenting with pretreatment techniques, Noles mentions. “We have quite a bit of testing left, but the preliminary data suggests the right pretreatment will improve HVFR performance and the well’s production,” he reports.
Mitigating Damage
FRs are an essential component of the completion fluid, acknowledges Scott Bailey, senior scientist with Flex-Chem Corp, but he also warns of the downsides associated with a negative charge. “When they are down hole, this charge causes them to cross-link with minerals in the shale and create polymer derivatives that plug the formation,” he explains.
That plugging can greatly reduce the well’s production, Bailey says. “In the Mid-Continent area, we see wells’ production rates decline 85%-90% within the first year largely because of plugging,” says Bryce Conway, Flex-Chem’s president. “In some wells, even the initial production is much lower than it should be given their location and the offset performance.”
Even premium friction reducers can cross-link with the metal-bearing clays found in shale formations and leave behind polymer derivatives that restrict flow, Flex-Chem Corp.warns. Extensive testing in the Mid-Continent region shows that treating wells to remove these polymer derivatives can increase production significantly.
Samples from these wells generally have FR polymer derivatives containing metals from the formation, Conway says.
“Polyacrylamide-based FRs’ tendency to cross-link with the formation is sufficiently well-known that operators are experimenting with alternative FRs to reduce the damage. For example, they are trying anionic, nonionic and cationic polymers, as well as HVFRs,” Conway observes.
Conway says his company’s experience suggests that in many applications, it can be more economic and effective to prevent or repair the blockage with breakers that pull the metals out of the polymers. “This transforms them from a shoe-rubber-like material into a low-viscosity, water-like liquid that flows out of the well,” he says.
Flex-Chem has applied such breakers to 700 Mid-Continent wells, particularly in the Meramec and Woodford formations. According to Conway, nine out of 10 wells have seen production improvements after the treatment. “In 35% of the wells, we see production above the IP. This has happened even in wells that are four years old.
“The breakers should yield similar results in other shale plays, such as the Marcellus, Utica and Eagle Ford,” Conway predicts. “Like the Meramec and Woodford, these plays have metal-bearing clays such as illite, smectite, chlorite and pyrite that cross-link with slickwater completions’ friction reducers.”
Flex-Chem has been working with operators to identify variables in the completion fluid’s design and the formation’s geology that determine the severity and type of damage, Senior Scientist Bailey reports. In wells where damage is likely, he suggests including polymer breakers in the completion fluid rather than treating the well a few months after production begins.
“It is tempting to wait until damage occurs to invest in remediation, but once the formation is plugged, it’s hard to get the treatment where it is needed most. We are developing better placement techniques to help with that, but it will be much cheaper to address the unintended cross-linking during the initial completion,” Bailey argues.
Chemical Logistics
Lead times can be extremely short for the trucking companies that deliver frac chemicals to the well site, says Jeff Greenway, president of Smart Chemical Logistics. “While some of the chemical suppliers we work for have long-term contracts with operators, most only know whether their suite will be used on a well a few days before the job,” he observes. “In fact, we frequently estimate chemical transportation costs for two or three companies that all want to sell to the same frac site.”
Greenway urges chemical suppliers and operators to communicate with their logistics partners frequently. “The more we know about expected activity levels, the easier it is for us to plan ahead and minimize the risk of delays,” he explains.
Cloud-based software is making it easier for chemical suppliers, operators and trucking companies to communicate and keep hydraulic fracturing crews supplied with the chemicals the job requires, Smart Chemical Logistics reports. The company recommends giving trucking companies access to tank level monitors so they can dispatch delivery trucks as soon as the on-site storage has enough space for another load.
Finding the time to update logistics partners can be difficult when a company’s workload is growing faster than its staff, as often happens when industry activity increases, Greenway acknowledges. He says GPS systems, tank telemetry and online portals can help by automating data collection and dissemination.
Even with adequate lead times and careful planning, occasional transportation delays still occur. “We are able to deliver 90%-95% of loads on time, but no amount of planning can eliminate traffic jams caused by accidents, and even the best maintenance program cannot stop every tire blowout,” Greenway says. “Because delays are inevitable, we encourage completion companies to store at least 24 hours of chemical on site.”
To maintain that 24-hour cushion, Greenway says logistics providers generally monitor tank levels and chemical consumption trends so they can send trucks out as soon as the tanks have enough free space to accept a new delivery. “This is especially important for high-volume products that the engineer may adjust,” he comments. “For example, we have seen the amount of FR used in each stage jump 30%-40% based on pressure spikes or feedback from previous stages.”
In many areas, including the Permian Basin, finding truck drivers can be difficult, Greenway observes. “The driver shortage is tight enough that smaller trucking companies may be willing to overlook blemishes on a driver’s record to get someone behind the wheel,” he says. “Larger companies can be pickier. For example, they might reject drivers who have a history of broken taillights, missing mudflats and other minor mistakes that indicate carelessness.”
For a trucking company to meet that standard, it needs to excel at retaining employees, Greenway emphasizes. “High salaries, retention bonuses, fair treatment, steady business and newer trucks help, but at least for us, the silver bullet has been quality housing,” he reports. “Most of our drivers come from out of state and work three weeks at a time before going home for a few days. If we jammed four drivers into two-bedroom apartments or bunkrooms, they would quickly burn out.
“Instead, we give each driver a private room with a kitchenette and a TV,” he says. “That is expensive, but the drivers enjoy their workweeks more if they have their own place to rest. That is one reason 75% of our drivers have been with us for at least two years.”
Greenway encourages chemical suppliers with enough business to arrange dedicated equipment with their logistics partners. “When companies use the trailers we dedicate to each product line, they eliminate the costly washouts required when a trailer switches from one chemical to another. In addition, the drivers work with the client’s team enough to create relationships that solidify the last step of the supply chain.”
Ideally, Greenway says dedicated equipment should be provided at a flat rate to minimize cost variations and the time spent looking through trucking tickets to verify hours and mileage. He adds that flat rates tie logistics costs to gallons sold, making it easier to justify logistics spending and budget an appropriate amount.
Thermoplastic Diverters
Thermoplastic diverters can be an excellent tool for optimizing cluster efficiency in hydraulic fracturing applications, says Nick Koster, vice president of technology and applications for DiverterPlus Inc. “Because thermoplastic diverters convert to a liquid after use without requiring additional intervention, they are easy to remove and have minimal potential to damage the formation,” he explains. “They are tough enough to withstand the high pressures generated by hydraulic fracturing, but light enough to get where they need to go.”
Thermoplastic diverters have strong track records in the United States and Canada, as well as the Middle East and China, Koster assures. “We have run them in temperatures as low as 90 degrees F and as high as 375 degrees F, and in everything from conventional wells in the Middle East to unconventional shales in the United States,” he says.
By adjusting thermoplastic diverters’ mechanical properties, engineers can tailor them to provide reliable seals in a variety of applications, DiverterPlus Inc. reports. These applications include far-field diversion, an increasingly popular technique for mitigating hydraulic fracture hits and refracturing old wells. The image shows three far-field diverter offerings after compression in a test cell.
“When we compare the results from wells that are properly designed to use thermoplastic diverters to optimize cluster efficiency with wells that use no form of diversion, we frequently see 100% improvements in six month cumulative production,” Koster says. “Thermoplastic diverters also tend to outperform other degradable diverters because their mechanical properties are extremely flexible and can be tailored to fit the well.”
The production improvements vary widely, and in some cases, do not appear at all, Koster acknowledges. However, he says the technology is becoming more reliable as its proponents get better at engineering thermoplastics for specific downhole environments and well designs.
“If we take a one-size-fits-all approach and try to use the same diverter for every application, the effectiveness can swing back and forth even from stage to stage within the same well,” Koster says. “But if we tailor the geometry, mechanical properties and degradation behavior to the formation and fluid the diverters are in, they offer great reliability.”
To improve that reliability, Koster says DiverterPlus has partnered with an expert in computational fluid dynamics to more accurately predict the behavior of thermoplastics with different densities and shapes.
“Many traditional models of diverter behavior assume the diverter blend will arrive at the perforations as it was deployed ahead of the pump, then distribute itself evenly to every perforation,” Koster says. “That is not the case. In fact, the blend’s distribution and concentration often changes as it passes through the pump and travels through the well.
“As the blend moves through the lateral, the heaviest components can sink or settle. This can create a situation where a cluster’s downward-facing perforations are sealed but the upward-facing perforations remain open, meaning future stages will extend the existing fractures rather than initiating new ones,” Koster warns. “Fortunately, by understanding how changes in shape and density affect the diverter particles’ transport characteristics, we can create ones that stay in suspension and seal off the entire cluster as planned.”
Far-Field Diversion
With enough information and careful engineering, thermoplastic diverters can be a cost-effective way to achieve far-field diversion, Koster says. This technique encourages frac jobs that otherwise would produce a few lengthy, highly conductive fractures to instead create complex fracture networks. Specialized deployment designs can be used to minimize frac hits or refracture old wells, applications Koster reports are growing in popularity quickly.
“We are developing lab protocols to quantify far-field diversion’s effects, but getting far-field diversion right is an involved and iterative process,” Koster says. “When we have access to extensive data about past stages, especially those that have had rate changes or other treating anomalies, we can analyze the pressure responses to design a job that should be effective. Without that, we have to gradually identify the best approach based on feedback from each stage.”
Even when it is done well, Koster says far-field diversion can be expensive. “To accelerate our design process and improve far-field diversion’s economics, we have partnered with a company called Drill2Frac. By combining our strengths, we have figured out how to analyze multiple data sources to identify where far-field diversion is most necessary and how it should be utilized,” he shares. “This lets us deploy diverters more strategically and has the potential to cut the diverter costs of traditional far-field designs in half.”
With other partners and internally, Koster continues, DiverterPlus is developing new thermoplastics with different characteristics. “For example, we have come up with much lighter versions that can be run in the alcohol-based fluid systems used off shore. We also have created specialized coatings that allow the diverters to be used in previously incompatible fluids,” he details.
DiverterPlus is developing more efficient deployment methods, Koster adds. “In the past, companies would use a separate blending system to introduce the thermoplastics into the fluid, then send that fluid to isolated frac pumps designed to accommodate them,” he recalls. “The extra equipment, people and trailers added up.
“That was necessary because of clearance constraints inside the frac pump,” Koster says. “We have developed diverters that travel through frac pumps without causing damage to nonconsumable components. Through a partnership with NOV, we have been able to further protect clients’ pumps by installing special valves and seats that can pump the large diverter volumes needed for aggressive designs without frequent replacement.”
Koster attributes these valves and seats’ durability to an NOV-proprietary urethane compound that stops diverter particle embedment, a major source of damage and pump failure. “Independent mixing and pumping equipment still may be required if the stimulation fluid is viscous enough to need large diverter particles,” Koster says. “But in slickwater jobs, the diverters can go into the mainline blender tub, which greatly reduces their deployment costs.”
For other great articles about exploration, drilling, completions and production, subscribe to The American Oil & Gas Reporter and bookmark www.aogr.com.