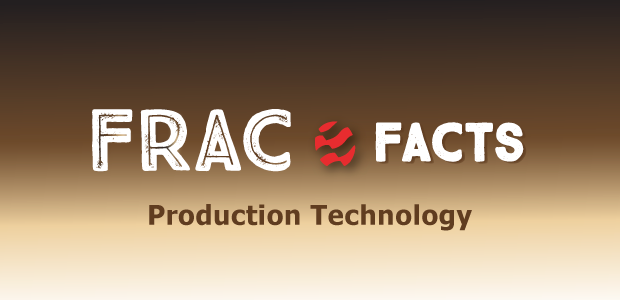
Low-Pressure Solution Gives Operators New Option For EOR In Tight Oil Plays
By David S. Schechter and Brian Schwanitz
HOUSTON–From the earliest days of tight oil development, operators recognized that horizontal wells with multiple transverse fractures generated high initial production rates but also had characteristic steep decline curves. The result is that long-lived shale assets typically yield a large percentage of their total production in the earliest stage of well life. Daily rates rapidly decline over the first year of primary production, and then typically plateau at a fraction of the IP rate.
The industry continues to advance the science of tight oil reservoir development, but the reality is that horizontal well decline curves coupled with the low-permeability tight rock matrix continue to challenge ultimate recovery. Primary production is estimated on average to recover only 6%-10% of the estimated total original reserves in place, leaving a lot of oil to be claimed through secondary recovery methods in tight oil plays.
Keeping in mind that horizontal development of tight oil resources is relatively new (the Eagle Ford was not even “discovered” until 2008), there are nevertheless thousands of wells that are in the latter stages of primary production life, making tens of barrels a day instead of the hundreds or thousands of barrels a day they produced when they were flowed back and brought on line. This is especially true in the Bakken and Eagle Ford shales, where tight oil activity initially was concentrated and where large populations of mature wells now exist.
Over the past decade, the technical feasibility of enhanced oil recovery for unconventional shale oil has been demonstrated by means of a single-well, single-phase gas injection huff-and-puff process. As opposed to flooding a reservoir with injected water or gas, huff-and-puff uses alternating inject-soak-produce cycles, in this case, injecting gas into the formation. Figure 1 shows the rapid decline in oil rates on an Eagle Ford lease and the 35% improved recovery from five single-phase gas injection cycles obtained from public data provided by the Texas Railroad Commission.
However, despite demonstrated increases in recovery, this type of EOR project rarely has proven economic, and consequently adoption has floundered. Single-phase gas injection requires very high surface pressures (5,000-9,000 psig), which drives up complexity, project risk and cost. Implementing huff-and-puff required significant upfront capital investment, including installing large compressors to inject the gas. Public data indicates that delivery times for these projects have averaged two-plus years, utilized large teams, and because of the long lead times for project delivery, required operators to make final investment decisions years before first oil.
New Solution
A new technique that co-injects low-pressure gas and water offers a solution to the drawbacks associated with traditional huff-and-puff and puts EOR in unconventional reservoirs within reach of operators of all sizes. This process has the potential to significantly increase the recovery factor, as observed in the Eagle Ford RRC data, giving oil and gas companies the opportunity to capture an enormous prize in assets they already own and operate: the 90% or more of original oil left in place after primary production in tight oil wells.
The new patent-pending EOR process, termed “rapid-switched, stacked-slugs” (RSSS), has been fully developed and field tested. The combined water and gas injection system dramatically reduces surface injection pressures and the related compression costs and emissions for huff-and-puff EOR, as well as the risks. Low-pressure gas injection is made possible by way of a patent-pending process that drops surface injection pressure in the range of 300-1,300 psig, thereby eliminating the need for large surface compressors. While surface pressure is reduced, the hydrostatic weight of the liquid, which is injected as precisely manufactured liquid slugs, allows the process to create pressures well above the reservoir’s minimum miscibility pressure (MMP). Also, a surfactant designed to alter wettability is delivered in the slugs of water.
As shown in Table 1, the RSSS process compares favorably in head-to-head comparisons with single-phase gas injection for huff-and-puff EOR. For an equivalent application, the RSSS process has a much lower cost and provides faster delivery versus the large-horsepower compressors used in conventional gas injection projects. Importantly, gas compression and emissions are reduced by a factor of 10, and operational risks also are mitigated by dropping surface injection pressure from 6,000-9,000 psig to under 1,300 psig, which is within the range of normal gas lift injection pressures.
Critical EOR mechanisms have been added, beyond gas miscibility and re-pressurization. Surfactant blended in the co-injected water provides the EOR mechanism of surfactant-assisted spontaneous imbibition (SASI) as a result of altering the wettability factor. Also, mobility control is another key feature of the RSSS process, with the co-injected water limiting gas movement to adjacent wells. This was demonstrated in a recent field pilot.
RSSS Method
The RSSS method solves the problem of gas-liquid co-injection at high gas fractions. For downward vertical flow, gas and liquid separate in the wellbore, with liquid falling along the pipe wall, and in some cases, as droplets. This leaves a gas gradient acting on the reservoir, and prevents the hydrostatic benefits of the added water to be delivered to the formation. Only at very high liquid fractions does a homogenous bubble flow regime occur where a liquid gradient is transmitted to the reservoir. For EOR, it is desirable to deliver large quantities of miscible gas to improve oil recovery, so this is a genuine problem.
The answer to this problem is developing a way to manufacture the slug flow regime and transfer the hydrostatic weight of the co-injected water to the reservoir even at very high gas fractions. The RSSS process creates a multiphase gradient to the reservoir and delivers large volumes of gas for EOR benefits. The manufactured slugs remain stable when moving downward with increasing pressure. This is the opposite of upward flow, where flow structures become unstable as pressure is reduced and gas expands on the trip to the surface.
As shown in Figure 2, the vertical wellbore will have several liquid slugs and gas bubbles present at any given time; typically more than 20 slugs. The RSSS process varies the slug and bubble lengths at the surface to deliver a predetermined bottom-hole pressure and keep the slug flow structure stable. This multiphase gradient lies between a pure liquid and pure gas gradient, allowing injection using normal gas lift systems or small gas lift compressors that are readily available.
The multiple contact miscibility process has proven effective in Eagle Ford unconventional reservoirs. It is essential that reservoir pressure be raised above MMP–a pressure that varies with injection gas and reservoir oil composition. Analysis shows that RSSS can exceed the MMP in the Bakken, Eagle Ford and Wolfcamp reservoirs with rich gas, lean gas and carbon dioxide.
As noted, the RSSS process also results in SASI because it alters wettability with the proper choice of surfactant. The impact of wettability alteration with surfactant is well established by laboratory work, field tests and technical papers. Interestingly, the surfactant penetrates deep into cores to alter wettability and is not just a fracture surface mechanism, as illustrated in the computerized tomography scan of Wolfcamp core samples shown in Figure 3. The color changes to blue and green from the initial red color, indicating that a denser phase (surfactant solution) was displacing the less dense phase (oil). There also is supporting indication of this mechanism from field tests using surfactant in frac water, where surfactants accelerated and improved recovery over a 36-month field trial.
Uniquely, the RSSS process can be delivered as a leased service using a modular, self-contained surface system that can be installed quickly. The automated surface system is a small footprint skid-based unit that can be shipped and set on the well site in one piece. This product eliminates facilities requirements and reduces compression requirements by a factor up to 10.
The automated control system eliminates the need for close monitoring of EOR implementation. The reduced compression requirements slash energy consumption and greenhouse gas impacts, thereby resulting in more efficient and environmentally friendly EOR project operations. In addition to the hardware, the system includes software-as-a-service for the EOR process to reduce the requirement for large EOR project teams and expertise, putting EOR in reach for a wide array of producers.
Bakken Field Pilot
The first RSSS pilot was executed in the Bakken formation (Table 2). The single injection cycle reached a bottom-hole pressure of 4,600 psig, which was significantly greater than the approximately 2,450 psig MMP and represented a first for an EOR process in the Bakken. More than 46 MMcf of rich gas was co-injected along with 40,000 barrels of freshwater with surfactant at two gallons per 1,000 gallons of water.
The pilot also demonstrated the ability of co-injection to reduce gas mobility in the reservoir and prevent gas breakthrough in adjacent wells. RSSS resulted in approximately 8,000 barrels of incremental EOR recovery in the first six months and more than 13,000 barrels of oil in a one-year period, which included offset well EOR contributions on the pad. This translates into an impressive gas utilization factor of less than 5 Mcf for each barrel of enhanced recovery, a significant improvement when compared with most gas injection projects.
While only one injection cycle was conducted in the Bakken pilot, this process is best applied in a round-robin fashion on a pad of four-six wells, with each well experiencing multiple injection cycles. This approach allows for effective repressurization of the overall pad and substantial voidage replacement (Figure 4). Given the positive response in oil production seen in offset wells in the pilot, it is suggested that the well injection sequence can be optimized much like a frac treatment sequence to achieve the best result.
[image 6]
While this article focuses on tight oil EOR, other potential RSSS application cases include carbon capture and storage (CCS), frac protection and expansions of conventional EOR projects.
Regarding CCS, the Bakken RSSS pilot demonstrated breakthrough low-pressure gas injection by injecting gas at 3 MMcf/d over a 15-day period in a depleted well. The CCS use case is of special interest to allow operators to eliminate flaring during battery and facility upsets, injecting the gas stream into a depleted well for multiple days or weeks. This allows production for the entire battery to continue while also meeting commitments to eliminate routine flaring. Batteries in the Midland Basin are a good match for the existing module when gas production volumes are considered.
Frac hit protection is another area where RSSS seems to be gaining interest. The process injects an energized fluid that improves recovery of water from the parent well on flowback. The energy is provided by the expandable co-injected gas, delivering an EOR pilot for essentially the same cost as a protection frac.
Finally, RSSS can reduce capital requirements and compression/emission for water alternating gas expansions and a wide array of conventional EOR projects.
Editor’s Note: EOR ETC LLC acknowledges the Energy & Environmental Research Center at the University of North Dakota and EERC members for funding the RSSS Bakken pilot project, and Liberty Resources for providing the wells and project execution support for the pilot.
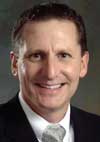
DAVID S. SCHECHTER is a technical adviser and member of the board of directors at EOR ETC LLC, which has developed the patent-pending RSSS technology. A distinguished member of the Society of Petroleum Engineers, Schechter retired this year as the George and Joan Voneiff Professor of Petroleum Engineering at Texas A&M University. He has been involved in laboratory and field applications of gas injection and surfactant EOR for more than three decades. Schechter holds a B.S. in chemical engineering from the University of Texas at Austin, and a Ph.D. in physical chemistry from Bristol University.
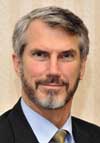
BRIAN SCHWANITZ is president of EOR ETC LLC. He has worked in the oil field services sector for 44 years, including 25 years with Schlumberger and 19 years with Welltec in various technical and management positions. Schwanitz has served for 13 years on the international board of the Intervention and Coiled Tubing Association and is a past SPE distinguished lecturer. He has served on two API committees and the SPE Energy Information Committee, and was awarded the 2016 SPE Production Operations Distinguished Service Award. Schwanitz holds a B.S. in geophysics from Michigan Technological University.
For other great articles about exploration, drilling, completions and production, subscribe to The American Oil & Gas Reporter and bookmark www.aogr.com.