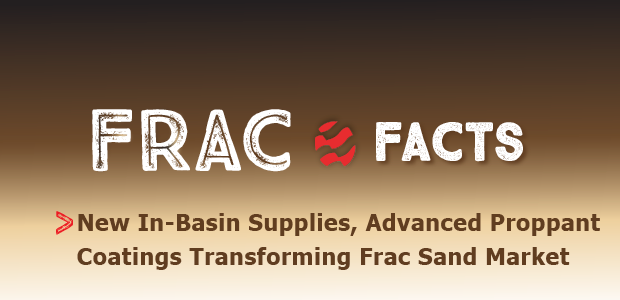
New In-Basin Supplies, Advanced Proppant Coatings Transforming Frac Sand Market
By Kari Johnson and Tim Beims
No one embodies the full-circle success of the Permian Basin, nor the spirit of the American wildcatter, more than Ben M. “Bud” Brigham. From humble beginnings exploring conventional targets in the Permian Basin with 3-D seismic and $25,000 in initial investment capital, Brigham subsequently built world-class positions in unconventional plays–first in the Williston, and then the Permian–and closed separate billion-dollar transactions in both basins.
After reaching the pinnacle of success playing the role of the independent oilman, Brigham now is recasting himself as the “independent sandman,” helping the companies that not long ago were his peers satisfy their insatiable appetites for quality frac sands in Brigham’s familiar old stomping grounds in West Texas.
According to IHS Markit, Delaware and Midland basin operators put away 50 billion pounds of proppant in 2017, quadrupling 2014’s total. By 2022, forecasts call for annual Permian proppant consumption to quadruple again to 120 billion pounds–enough sand to fill 2.5 million hopper trailers to the brim.
That is where Brigham and his newest company, Atlas Sand, come in. Born in the Permian, trained as an exploration geophysicist to always look for the next big thing, and conditioned as an independent operator to move decisively when opportunity presents itself, he says, he did not hesitate when childhood friends told him about the quality and availability of West Texas “dune sands.”
So within months of selling Brigham Resources and its Delaware Basin leasehold in December 2016 for an aggregate $2.43 billion, the consummate oilman re-entered the Permian scene, but this time eyeing vast reserves of another kind: natural sand deposits. “The play made perfect sense to us from both a geological and an entrepreneurial perspective, which gave us the confidence to move quickly,” he states.
Atlas Sand now controls about nine sections (60 percent) of the Kermit dune to the north and 100 percent of the 14 sections over the Monahans dune to the south, excluding a local state park. In addition to this approximately 14,500 acres, Atlas holds another 23,500 acres of off-dune buried sand in the region, the largest sand reserves in the Permian.
The company is on track to open two in-basin mines in 2018, bringing on an estimated 7.8 million tons annually of its Atlas Pure Permian™ sand. The company plans to increase capacity to at least 14 million tons by the end of 2019 and could double that by 2020-21. Brigham says they control an estimated 100 years’ worth of what Atlas terms “tier-one” sand reserves.
Hunter Wallace, former vice president of operations for ATX Energy Partners (the private equity-backed successor company to Brigham Resources), joined Atlas as chief operating officer early on. “Seeing Brigham’s vision and knowing that he was going to capitalize it the right way and run it the right way made the potential too much to pass up,” he concludes.
Perfectly Sized For Fracturing
Over the first six months of the project, Brigham says they learned that the deposit is quite consistent both spatially and in-depth in the open dunes. He attributes that to the topography and prevailing wind direction. The sand in the fairway is sourced from the north and northwest. An escarpment to the east slows wind velocity, causing sand particles to fall out that are perfectly sized for fracturing, Brigham details.
With proppant consumption increasing dramatically across West Texas, Atlas Sand is opening two new mines this year to provide an initial 7.8 million tons of tier-one “dune” sand production annually, with plans in place to expand capacity to at least 14 million tons a year by the end of 2019. As shown here, the mines are located near Kermit and Monahans on the Central Platform, with ready access to high-proppant-intensity wells in both the Midland and Delaware sub-basins.
“It is ironic, and quite a blessing, that this has happened to occur right here in the Permian Basin as local demand for frac sand hits record highs,” he notes.
Brigham says Atlas Sand’s two sand plants are optimally designed to serve the basin. Both are built for Texas weather, with built-in redundancies and backup systems. Both are expected to initially produce 3.9 million tons annually, and have a combined 70,000 tons of silo storage. Each silo has its own loading lane for streamlined load-out. “We doubled down, because we know firsthand the value of reliability and flexibility,” says Brigham.
By controlling both of the large open dunes to the north and south, Atlas is logistically advantaged to deliver tier-one sand to wells in the southern and northern parts of both the Midland and Delaware basins. The mine sites are close to Interstate 20 as well as state highways 302, 115 and 18, putting them within 50-75 miles of Permian well sites. “When we talk to operators with scattered acreage positions in both Midland and Delaware plays, we can show them relative to their acreage where our two sites are and how we can reliably and cost-effectively serve them.”
Access to both basins also is of high value to pressure pumpers, who do not know exactly where in the vast Permian Basin their fleets may be a few months into the future. “Having a good northern access point and a good southern access point makes us very attractive,” Wallace remarks.
“The fact that this sand is right next door to the wellheads really de-risks the supply chain for operators by a vast margin,” continues Wallace. In addition, the simplified logistics of in-basin supplies provide immediate cost savings. As Wallace points out, transporting sands from sources over longer distances involves more infrastructure, more logistics and more cost per delivered ton. He predicts that cheaper and more reliably delivered sand will drive up well performance by enabling operators to further ratchet up sand concentrations placed per lateral foot.
Quality And Proximity
Brigham notes that Atlas Pure Permian sand is closer in color and quality to northern white mined in the Upper Midwest than the traditional Brady brown sand sourced in Texas. By nature, Pure Permian sands have good sphericity and low impurities, providing higher yield and lower cost, he adds, noting that the combination of quality and proximity can shave 5 percent or more off total well costs.
Overall, Brigham says the sand’s quality matches what operators are accustomed to using in the basin. Roughly 80 percent of the deposit is 100-mesh, and considered by the Atlas team to be comparable to northern white. The rest is 40/70-mesh and graded above Brady-quality brown. The 40/70-mesh is 1-2 K values lower in crush resistance than northern white, according to Brigham, which he says is a level sufficient for virtually 100 percent of West Texas wells.
Testing on sands sourced from the Kermit area is yielding positive reports on well performance from operators. Wallace also notes that production can be switched to 100 percent 100-mesh, depending on market demand.
The company plans to provide transportation to well sites for any operators requesting it. “We find that many operators want to buy directly, but may not have the logistics team to move the sand from the mine to well sites,” Wallace relates. “Operators or service companies also can pick up sand at the mine sites.”
Either way, the cost advantage over out-of-basin sands is substantial, Wallace continues. “It can cost $50-$60 more per ton just to get the sand into the basin.”
“We see a lot of growth potential for in-basin sand,” adds Brigham. “And because we are a Permian pure play with 100 percent of our sand sold into West Texas, every dollar we spend benefits Permian operators.”
First In-Basin Mine
Hi-Crush has opened the industry’s first in-basin mine in the Permian, producing 100-mesh sand at its new facility near Kermit. Laura Fulton, the company’s chief financial officer, says the mine has an annual production capacity of 3 million tons with 15,000 tons of silo storage. The sand is coarser than Hi-Crush’s northern white sands, but meets all API specifications, she says.
“Customers tells us they like the Kermit sand and that it is performing really well,” Fulton comments. “Most operators also want high volumes of 40/70, some 30/50 and even some 20/40-mesh sand for their completions, which means sand will be sourced from different locations.”
The company operates multiple transload terminals for northern white sand from its Upper Midwest mines, with a site near Pecos in the southern Delaware Basin and terminals at Odessa and Big Spring in the Midland Basin. Generally, Fulton says, Hi-Crush can supply 80 percent of the wells within a 50-mile radius from the three terminals and the new Kermit plant.
Given soaring proppant demand across the Permian with no letup in sight, Fulton says Hi-Crush sees plenty of room for both in-basin and northern white sand. “We expect that demand will continue to grow and that the new West Texas sands will add to, rather than displace, current supplies,” she states. “Operators will be able to complete their wells using even more sand per lateral foot, and do so at a potentially lower cost with more supply options.”
Hi-Crush has opened the industry’s first in-basin mine in the Permian with its new facility near Kermit, which has annual production capacity of 3 million tons and 15,000 tons of on-site storage. The company also operates multiple transload terminals in both the Delaware and Midland basins. Hi-Crush’s PropStream™ integrated supply chain solution uses proprietary containers and an on-site conveyor system called PropBeast™ to optimize logistics from the mine site or transload terminal to the blender hopper.
Meanwhile, demand for northern white remains very strong outside the Permian. “We have a very strong footprint in the Marcellus and Utica,” notes Fulton. “Now that we are able to source 100-mesh in the Permian, we can free up some of our northern white sands to Appalachia and other areas.”
Fulton says Hi-Crush is taking the concept of “last-mile logistics” one step farther to alleviate costs, personnel workloads and logistical headaches for operators. “We are focused on logistics to the last foot,” she explains. “We sell directly to operators and deliver the sand all the way to the blender at the well site, handling all the logistics along the way,” she states.
The company’s PropStream™ integrated supply chain solution uses a containerized system to transfer proppant to well locations. “In the Permian, for example, sand is transferred from the transload terminals or the Kermit mine into two containers on a truck chassis. At the well site, the containers are off-loaded, and an internal conveyor system called PropBeast™ moves the sand directly into the blender hopper,” she explains. “Meanwhile, empty containers are loaded back onto the truck to minimize idle time. The container and conveyor system speeds loading/unloading and dramatically reduces dust exposure.”
The goal is to provide end-to-end supply to give operators surety of quality and availability as they pump ever-larger volumes of sand in their wells while significantly simplifying logistics. However, added benefits include the fact that the system meets the new U.S. Occupational Safety & Health Administration respirable silica dust exposure requirements, and also significantly reduces well site noise levels, according to Fulton. “Dust exposures tested below the new OSHA permissible exposure levels, and below the lower action level for PropBeast operators,” she notes.
Trucking capacity has been tight in the Permian for some time, and trucking costs have been on the rise as expanding proppant demand has created shortages of both trucks and drivers, Fulton states. Putting sand as close to the well as possible helps reduce trucking miles and costs, she notes.
“That is why we built out the strategic footprint at the Pecos terminal,” she says. “We wanted to be able to service Delaware Basin demand more locally, without sending trucks from the two terminals on the Midland Basin side.”
Increasing truck volumes and turnarounds is another way to offset higher hauling costs. Fulton estimates that the containerized system is generating a 10 percent increase in allowable sand volumes per truck, reducing total truck trips. “We also have seen as much as an additional truck turn a day, depending on where the facility is located relative to the well site,” she adds. “Logistics is the name of the game. Being as efficient as possible is critically important to success in any shale play, but especially the Permian.”
All About Contact
The end game for operators in horizontal resource plays is simple: Maximize the stimulated reservoir volume and keep induced fractures propped open so hydrocarbons keep flowing. Accomplishing those objectives, says Don Conkle, vice president of marketing and sales at CARBO, is leading the industry to pump more proppant per well.
“There is an inclination to pump more proppant with closer fracture stages, increasing the number of clusters and reducing stage spacing,” he notes. “Some operators are using new diverter materials, biodegradable balls and other techniques to achieve a higher assurance of frac initiation, but the bottom line is a lot more proppant demand.”
According to Conkle, CARBO sold nearly 400 million pounds of premium ceramics/technology proppants and 2.2 billion pounds of natural and resin-coated sand products in 2017. He says demand for northern white sand is expected to remain strong in shale plays, particularly for 40/70- and 100-mesh.
While advancements have been made in reducing logistical costs and increasing supply flexibility, Conkle says most operators recognize that there is still more efficiency and productivity to be gained to maximize operator and shareholder returns. “I ask operators what inning they think they are in and they agree that the game is far from decided,” he relates.
Layering in high-strength, lightweight ceramic proppants with natural sand has improved well performance in the Eagle Ford Shale. As illustrated here, 12 wells in which CARBO’s CARBOAIR™ ceramic proppant was tailed in with sand outperformed 12 offset wells completed with only sand. The lighter weight of the ceramic proppant allows it to carry deeper into the fractures, and its superior strength and crush resistance prevent fractures from closing over time as wells produce.
Continuing the baseball analogy, Conkle says diagnostics and analytics technologies will be the next game changers to help operators better understand where proppant is going and how effectively reservoirs are being fractured to enhance productivity and efficiency. “For a hitter, how he contacts the ball can be the difference between a foul ball and a homerun,” he says. “The same is true for reservoirs. It is all about contact and the permeability of the proppant pack.
“We know the closer the perforations and stages, the more contact there is between the lateral and the reservoir, and the better the production should be in the short term,” notes Conkle. “However, we do not know what effect that has over the long term, but are now learning.”
Shale wells characteristically decline rapidly, and as production falls off and flowing pressure declines, the frac begins closing on the proppant with increasing pressure. A study in the Eagle Ford compared productivity curves in 24 wells, half of them propped with sand and the other with sand and higher-strength ceramics tailed in, Conkle details.
“As stress on proppant reached approximately 7,500 psi, the purpose and advantage of ceramic proppant became clear. A significantly steeper decline occurred in the productivity index of the dry gas wells propped with sand after 180 days of production than the ceramic tail-in wells,” he reports. “This is known as the ‘PI rollover,’ which could result in a decrease in forecasted reserves.”
In Utica dry gas wells, companies are starting to blend sand and CARBO’s KRYPTOSPHERE® ceramic, starting with 100-mesh sand and progressing to 40/70-mesh ceramic, 30/50-mesh ceramic, and finally tailing in 35-mesh KRYPTOSPHERE. “CNX Resources Corp. and several other operators have reported completing several wells in this manner with very strong results," Conkle remarks.
New Solutions
Conkle points to a well-documented challenge in proppant placement, noting that analysis shows that sand often ends up falling out of the fluid stream a short distance into the created fracture. “Beyond that point, the fracture is left unpropped, and eventually closes. Layering sand and an ultralow-density ceramic proppant such as CARBOAIR® is an effective way to address this ‘duning’ problem and obtain longer/higher propped fractures (especially farther from the wellbore).
“CARBOAIR is 28 percent lighter than sand, has a 12 percent higher packing advantage and requires 30 percent less water to place,” he continues, “resulting in 40 percent more volume being filled when pumping the same amount of mass.”
Pumping a mixture of sand and ceramic proppant can measurably improve reservoir contact, Conkle comments, referencing an operator in the Eagle Ford that performed a side-by-side comparison in virgin rock. “The only difference between the completions was that one well included a CARBOAIR tail-in,” he explains. “After six months, there was a 20 percent increase in production. Additional fine tuning with hybrid designs could yield even more improvement.”
Among the newest solutions in CARBO’s product line is an engineered proppant that protects against scale and salt, and an ultrafine 200-mesh proppant the company has dubbed NANOMITE™. The engineered proppants are filled with inhibitors and coated with a semi-permeable surface. “SCALEGUARD® is mixed with sand and/or base ceramic and pumped into fracs, where it treats the water that flows through it to mitigate scaling issues during production. It is particularly suited to the Permian, where scale can be a problem,” Conkle says. “NANOMITE can achieve better diversion and prop open small natural fractures in complex fracture networks.”
For diagnostics, CARBONRT® nonradioactive tracer helps operators pinpoint where proppant is located, assessing proppant entry points along a lateral in a horizontal well and propped fracture height in vertical wells. Conkle says the tracer is distributed throughout each proppant grain, allowing for the most accurate method to identify proppant location.
By year’s end, Conkle announces, CARBO plans to launch a new type of diagnostic service that uses a proprietary detectable proppant and electromagnetic detection technique to shed new light on proppant location within the reservoir–including in the far-field area away from the wellbore.
“Field trials demonstrate that the technology can detect the entire dimension of the frac,” Conkle enthuses. “The proppant is coated with a metallic substance and an electromagnetic signal from the surface induces a response that shows the proppant’s geolocation. This represents a major step in giving operators insights they can use to optimize field development and completion designs. They will know how much of the reservoir they contact, how far fractures extend and whether to change well spacing or zone perforation targets. It potentially could be key in evaluating their proppant and fluid selections.”
New Permian Mines
Billy Ray Smith, US Silica’s senior vice president and president of oil and gas proppants, says the company is opening two new mines in the Permian during the first half of 2018. Its Crane County facility, which is expected to be on line by the end of March, has a capacity of 4 million tons a year. The Lamesa plant is scheduled to come on line in the second quarter with 2.6 million tons of annual production capacity. Both mines have production contracts in place.
The company also is expanding three other facilities in Texas and Oklahoma, which effectively will double overall regional capacity within eight months, Smith reports.
US Silica is among the nation’s largest sand producers with more than 20 mines nationwide, and Smith says the company recognizes better than most the significant cost savings that in-basin sand can provide. “Rail cost can contribute as much as 40-60 percent to the total cost of sand delivered into the Permian,” he observes. “By bringing on in-basin mines, we can provide significant cost reductions to local operators.”
Smith notes that both new plants have been built using a simplified plug-and-play design, enabling quick expansions or upgrades as needed. For example, he points out, a proppant coating facility could be easily added. “We took a SWAT approach to these projects, grabbing people from all over the organization to make these mines happen in record time,” he says.
The company also took a careful approach to logistics as it selected locations, Smith adds. “There is great concern about increased truck congestion in the Kermit area,” he says. “We know that demand comes in waves and surges, requiring a lot of storage and load-out capacity to prevent long lines of trucks on the roads.”
Accordingly, the Crane County location will have 12 load-outs plus an express lane for the Sandbox™ containerized delivery system. Each plant will have 72,000 tons of on-site storage. “We have had as much or more interest in the Lamesa plant as the Crane County facility,” Smith remarks. “Its product provides the best access to well sites in the Midland and southern Delaware basins.”
The two new mines will produce 100-mesh and 40/70-mesh sands. Pre-purchase testing showed the crush resistance is comparable to northern white. The 40/70-mesh has a crush resistance of 7-8 K values, while the 100-mesh has a crush resistance of 10 K values. “These and other properties of the sands fall within API specifications, and the 40/70-mesh meets or exceeds our ‘southern premium’ sand specification.”
Flexibility Is Key
Smith says he expects operators will continue to use a mix of sands sourced from different areas, including both regional sands and northern white. “Nobody knows yet how the new in-basin sands ultimately will impact production, but we are confident in the quality of our in-basin supplies,” he relates. To fully serve Permian operators and augment supplies of in-basin and northern white, Smith adds that US Silica has the capability to provide brown sands from expanded facilities at its Texas mines at Kosse and Tyler, as well as Mill Creek in Oklahoma.
Flexibility is the key. With today’s oil prices, plays are economic in every U.S. oil shale basin and sand demand is high. “With the scale of our nationwide footprint and the diversity of our supplies, we are positioned to react to operator demand for multiple sands from multiple locations in multiple regions,” he assures.
Fast responsiveness is central to the concept of the Sandbox system, which US Silica introduced to improve last-mile logistics efficiency and safety. The gravity-fed system also significantly reduces cost, noise and dust, according to Smith. “Sandbox is loaded onto a special trailer with a low center of gravity, making it safer for road travel,” he details. “Quick connects allow it to be offloaded in a matter of minutes. Drivers typically do not even leave the truck cab, and can do a quick turnaround with an empty Sandbox returning to the mine.”
Regardless of how many tons of proppant are sent down hole, a stimulation treatment will be effective only if the sand props open fractures throughout the reservoir, Smith points out. US Silica estimates that only 15-20 percent of fractures in a typical frac job are large enough to take 100-mesh sand, based on an analysis of fracture networks performed over the past 12-18 months. As a result, 75-80 percent of the fracture network is not stimulated.
To address this problem, US Silica has developed a new line of “microproppants” that are 200-mesh or smaller. Field tested by an operator in the Marcellus Shale, the microproppants can be carried farther into fracture networks and into previously unpropped fractures.
“MicroStim™ is 200-mesh while MicroStimPlus™ is a silica flour,” Smith elaborates. “As for their effectiveness, all I can say for the time being is that the Marcellus operator has ordered the microproppant for more of its wells.”
Quality Control
Sand quality is a function of original sand properties and the processes it goes through from the mine to well site, points out Scotti Bayman, HS&E and quality director at Shale Support. He says strict quality control processes improve efficiency and reduce waste, while providing a strong audit trail and product reliability. “With our QC protocols, there is no question that our customers get exactly what they ordered every time,” he says.
By implementing state-of-the-art quality control processes, Shale Support is improving efficiency and safety, lowering costs, assuring reliability and providing a strong audit trail. Extensive testing protocols at the company’s Delta Pearl™ mine and process plants in Mississippi are augmented by detailed tracking and quality monitoring procedures that include scannable quick response codes and bar codes on every rail car or truck with identifying information such as car number, weight, sieve data and destination.
Shale Support’s Delta Pearl™ is a clean white sand mined in Mississippi. Cut to order, the sand is typically sold in meshes ranging from 20 to 100. With low turbidity, the sand generates less dust and is ideal for stress-pressure conditions, Bayman reports. Delta Pearl made its entry in the Permian Basin in July 2014, and he says Shale Support now has four Permian terminals as well as terminals in other basins in Texas and the Appalachian Basin.
The wet mine and wet plant are co-located on 1,300 acres near Picayune. “The sand is cut and tested multiple times before being transferred to the dry plant,” Bayman says. “Wet operations include three cleaning cycles where fines are floated out and sand is rounded.”
The raw materials are tested again as they enter the dry facility following a five-mile transit, he goes on. “As the sand is dried, it is tested every hour using a particle size analyzer as well as roll testers,” Bayman comments. “The sand is tested on every shift, as well as with traditional sieves. We track the distribution of particle sizes and recalibrate the analyzers as needed.”
Another test is run as sand is loaded from silos into rail cars or trucks for delivery.
“We are meticulous in tracking product as it travels to termination points,” Bayman states, noting that the company has developed a process that ties logistics and quality together. As rail cars and trucks enter the yard, they are inspected and entered into a tracking system. Each hopper car or truck is assigned a product grade/mesh size. As sand is loaded, a sample is pulled and tested (a composite sample is saved for each order). If there is a mismatch at any point between the sample and the assigned grade, the system automatically stops the load-out.
“We work hard to prevent common loading process errors by building in this kind of automated fail-safe feature,” explains Bayman.
Once a rail car or truck is loaded, it moves on to a “scale-in-motion” weighing station and the data are captured in the tracking system. Finally, Bayman says a destination is assigned. Rail seals and retainer labels–complete with quick response codes and bar codes–are printed and placed on every rail car or truck. “The QR and bar codes are quickly and easily scanned for identifying information, including car number, weight, sieve data and destination,” he explains.
Bayman says Shale Support expects to continue expanding its operational footprint. It recently added barging and is now constructing a 300-acre transload facility in the Permian Basin to provide additional flexibility for short-notice orders. “The quality process may seem burdensome, but it pays off in improved safety, lower process costs and customer satisfaction,” Bayman concludes.
New South Texas Mine
Superior Silica Sands LLC, a subsidiary of Emerge Energy Services, also is opening a new mine in Texas, but the company made the strategic decision to focus its attention on the Lone Star State’s other major shale basin: the Eagle Ford.
“In the movement toward in-basin supply, we are taking the path less traveled,” says Rick Shearer, president and chief executive officer. Last year, the company acquired Osburn Materials’ mine south of San Antonio, within an 80-mile radius of core Eagle Ford activity and a seven-hour ride by rails to Midland.
“The mine had been producing sand for the building and sports markets. We immediately converted it to frac sand and began building a new facility with a capacity of 4 million tons a year. It should be operating by May,” he updates. “The sand reserves consist of 40/70- and 100-mesh.”
Already one of the largest northern white sand producers with five mines offering a combined annual capacity of 7.2 million tons, the San Antonio site expands Superior’s Texas footprint, adding to an existing “native brown” sand mine near Kosse, as well as regional transload and distribution facilities throughout West and South Texas.
As with West Texas sand, the brown sand produced at San Antonio does not have the properties of high-purity quartz northern white, but it meets API specifications for all grades, according to Shearer. “Operator interest has been very strong. We expect to soon have all of the mine’s capacity contracted,” he reports.
Shearer says expectations for proppant demand in the Eagle Ford are growing almost by the day. “The picture looks very good for 2018. We have customers adding rigs and frac crews in the Eagle Ford that were not part of their plans only three months ago,” he relates. “Eagle Ford economics are strong in their own right, but with services getting so tight in the Permian, some operators with assets in both plays are taking the opportunity to shift activity to the Eagle Ford.”
Even with Eagle Ford demand on the rise, Shearer says sand from the San Antonio plant will find its way into the Permian thanks to on-site rail access to the Union Pacific mainline, providing low transportation costs for the short haul northwest. “It may sound surprising, but modeling shows that sand from San Antonio can be delivered by rail into the Delaware Basin at a lower cost than sand trucked from some West Texas mines,” he reveals.
Within the Permian, Superior Silica Sands has opened a new transload terminal near Big Lake–its sixth West Texas terminal. The 98-acre facility is on the Texas Pacifico Railroad with connections to major regional rail lines. The Big Lake terminal commenced operations last July, but Shearer says expansions are already under way.
“The in-basin mines are going to do very well, especially the early movers in opening West Texas mines. But we think northern white will hold serve in the Permian and demand will remain strong,” Shearer offers. “Not only are operators telling us they intend to continue using northern white, but multiple companies have signed long-term take-or-pay agreements for northern white deliveries at Big Lake. We expect to be bringing dual unit trains of northern white into Big Lake for a long time to come.”
Shearer says hybrid designs that combine finer-mesh West Texas brown with northern white eventually will become common. “A growing number of operators are using 100-mesh and feathering in coarser 40/70 or even 30/50-mesh sands. The market always is fluctuating, but combinations of sand types and mesh sizes should materialize more and more, assuming the trend toward coarser mixes continues,” he suggests.
The Permian represents 20 percent of Superior’s total frac sand deliveries, with 80 percent diversified among the Eagle Ford, SCOOP/STACK, Denver-Julesburg, Williston, Marcellus/Utica and Western Canadian basins, Shearer says. But demand is not all about horizontal wells. In South Texas, the company is completing a $3.2 million upgrade to double capacity at Kosse. “Drilling in the Eaglebine trend is picking up. But this is a backyard kind of play where we truck sand to local drilling rigs, including a number drilling more conventional vertical wells,” he remarks.
Advanced Coatings
With federal regulations taking effect to limit respirable silica dust exposure, Superior has what Shearer dubs the “ultimate answer” in the form of SandGuard™, a glycol-coated sand that reduces dust to below regulatory specifications. “We have sold unit trains to operators and they are delighted with how well it works. There literally is no dust from the time the coated sand leaves the plant in Wisconsin to the moment it is pumped down hole in a well halfway across the country,” he enthuses.
The glycol coating also can be applied to sands coated with other chemistries, such as Superior’s new SandMaxx™, a self-suspending proppant that uses a specialty polymer coating that is more easily carried deep into the fracture, where it expands to fill the fissures. “Field trials show the technology increases estimated ultimate recoveries by 20-40 percent. The coating minimizes the ‘duning’ effect, whereby the force of gravity leads to sand falling out and settling on bottom soon after entering a fracture,” he explains. “SandMaxx more completely and evenly fills the fissure to make sure proppant is placed efficiently to keep the fracture propped.”
In addition to improved productivity, Shearer says SandMaxx provides a number of other economic and operational advantages. For example, he points out that well applications to date have averaged 10 percent less water consumption and 15 percent less chemical usage. “The polymer coating acts as a lubricant, so it is not as abrasive as raw sand. That means it not only pumps very easily, but also reduces pump maintenance issues, which can save operators and frac fleet owners a lot of money,” he notes.
Field trials have been completed in the Bakken, Western Canada, and South and West Texas. In a two-year trial in the Permian, Shell documented that the self-suspending technology not only enhanced proppant placement, but allowed 15 frac stages a day to be pumped compared with the typical eight stages a day for treatments using untreated sand.
Shearer adds that another operator is now kicking off a new 10-well trial in the Permian. “With the industry recognizing the critical importance of proppant placement in optimizing frac treatments, we expect to see more demand for the technology in 2018 and beyond,” he concludes.
For other great articles about exploration, drilling, completions and production, subscribe to The American Oil & Gas Reporter and bookmark www.aogr.com.