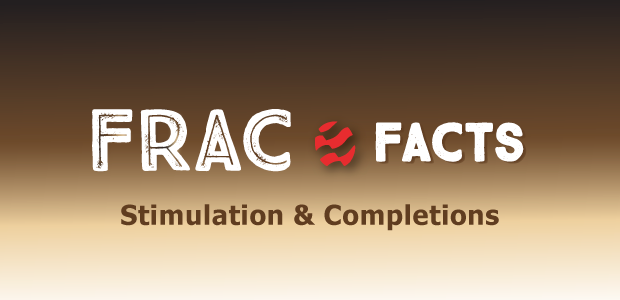
Practical Innovations Ease Fracturing
By Colter Cookson
In the fourth week of November, Primary Vision’s national tally of active hydraulic fracturing spreads had reached 274, 139 higher than the same week last year. While that ascent primarily reflects higher oil and gas prices and a stronger economy, it also is a product of the industry’s success at streamlining completions and improving well economics.
Service companies, equipment manufacturers and software providers involved in hydraulic fracturing say the march toward greater efficiency supports an industrywide effort to reduce emissions and other environmental impacts. The latest advances in efficiency and environmental protection draw on shrewd engineering, robust automation and modern materials science, but ultimately come from a drive to look at standard procedures with fresh eyes.
“To minimize safety risks, costs and emissions, pressure pumping companies need to rethink how they perform jobs,” argues Akshay Sagar, the president of Universal Pressure Pumping. “We need to develop workflows that leverage automation and centralized facilities to redefine peoples’ roles.”
With automation and the right infrastructure, Sagar says a single person should be able to manage work previously handled by three. “That can mean one person manages three spreads or cross-trains to perform different functions as needed,” he clarifies. “The goal is to give people more impactful roles.”
Sagar predicts that by 2022 or 2023, Universal will handle remotely half the tasks performed on site. “Depending on the area, we already are 30%-50% of the way there,” he says. “While this has reduced costs, the real benefit is allowing us to systematize processes. We already are seeing significant improvements in consistency and reliability.”
Recruiting people with the broad skill set, positive attitude and drive to excel in the new roles can be challenging, Sagar acknowledges. “As an industry, we need to show the next generation of workers how ambitious we are about environment, sustainability and governance and how much we use modern technologies,” he reflects. “We also need to show them that we offer appropriate compensation and career paths that will allow them to develop their skills.”
Emissions
Powering frac spreads with engines that run on a mix of natural gas and diesel can reduce emissions significantly, Sagar says. “Dual-fuel engines continue to improve,” he reports. “When we started pioneering dual-fuel frac spreads more than a decade ago, the engines could replace only 40%-60% of the diesel with natural gas. Today, the best engines can achieve substitution rates as high as 85%.”
Universal can deploy a battery system alongside its dual fuel engines. “This energy storage system runs backside equipment and helps support peak demand without additional engines, optimizing overall engine utilization and efficiency,” Sagar explains.
By deploying automation and remote monitoring, Universal Pressure Pumping says it is moving many tasks associated with hydraulic fracturing off site. In addition to reducing costs, safety risks and emissions, the company reports that this initiative helps it deliver consistent performance with a smaller footprint.
He adds that Universal has developed a system to shorten engine idle times. “The system detects when the engine is idling, usually between stages, and automatically shuts off the pumps. When they are needed, it automatically restarts them. Like the start and stop systems many cars use at stop lights, this reduces fuel consumption and emissions.”
The company also seeks to minimize water and chemical consumption. “We have subject matter experts in our labs constantly evaluating chemistries that are more biodegradable and sustainable,” Sagar relates. “We also have a program that focuses on identifying nonchemical ways to control bacteria and perform other functions.”
Usually, the greener chemistries perform at levels that equal or exceed standard ones, Sagar assures. “I have to give a shout out to operators,” he says. “They have been extremely open to trying new chemistries that can reduce their environmental impacts.”
Site Footprint
To reduce the amount of equipment and people that must travel to and from the well pad, Universal is experimenting with pumps that offer higher horsepower density, Sagar reports. “All our math says it is feasible to get twice as much horsepower in a pump as is standard, and we are about to trial a system that already achieves that,” he reports.
“We also have pivoted to a more intelligent ground iron network,” Sagar adds. “We have partnered with Scout Surface Solutions to deploy more efficient hose layouts that shorten setup times and require less iron on site. We instrument these ground iron networks so we can detect leaks and make adjustments without putting people in the red zone, which we are 100% against.”
Increasing horsepower density may ease simulfracs, which Sagar says generally require 1.5 times the horsepower of a standard spread but make it possible to fracture two wells at the same time. Getting that much horsepower on location can be challenging in regions with hilly terrain and small pads.
Despite those challenges, Universal is performing simulfracs in both the Northeast and Texas. “Simulfracs generally improve the lateral feet treated each day by 50%, reduce the amount of horsepower required per wellbore by 22% and shorten the time on pad by 30%, so they offer tremendous value,” Sagar says.
For simulfracs to make sense, the wells’ geology needs to be homogenous enough that they will respond positively to the same chemistries and pressures, pad size and wellhead layout need to accommodate the equipment, and logistical networks must be in place to deliver water and proppant, Sagar outlines.
“We think 25%-30% of future activity will be a good candidate for simulfracs,” he says. “In many areas, operators who want to move to simulfracs need to redesign their drilling programs and pad layouts. Also, simulfracs require enough planning and equipment that they generally only add value with long development programs that enable continuous operations.”
Getting sand, chemicals and other products to site for simulfracs takes some finesse, Sagar adds. “The oil and gas industry is not immune to the supply chain issues that are affecting other industries,” he observes. “We think these issues will only last six months or so, but in the meantime, we are doing what we can to navigate them intelligently.”
That means maintaining long-term relationships with trucking companies, proppant suppliers and parts manufacturers, Sagar says. “The age-old tool of planning as much as possible and communicating with suppliers is critical, but we also are optimizing our product mix and supply chain timing using cutting-edge machine learning platforms,” he reports.
Machine Learning
Machine learning can help engineers work more efficiently and increase fracs’ effectiveness, says Jeremy Miller, the vice president of product for Well Data Labs. “We have had customers get 10x returns on investment by using ML to automate simple but common analyses,” he reports.
As an example, Miller cites the time it takes for each stage to reach the desired pump rate. “To calculate time-to-target rate manually, an engineer would go through data to pick out the start of each stage and when it hit the target rate, then subtract the end time from the start time. With ML, we can do that automatically as soon as data is loaded.
“The ML algorithms also compare each stage to historical data to highlight any that took longer than planned, as well as possible causes for the delay,” Miller continues. “The goal is speed routine data analysis so engineers can spend time on more valuable work.”
Because machine learning algorithms can detect and label subtle events quickly, they can enable or accelerate completion analysis, Well Data Labs observes. In this image from a sealed wellbore pressure monitoring project, an algorithm has labeled pressure waves arriving at either of two monitor wells from the two active treatment wells. Well Data Labs says SWPM helps completion engineers evaluate several metrics, including fluid distribution, far-field fracture counts and fracture height and half-length.
According to Miller, ML empowers increasingly busy engineers to optimize performance by assessing drilling and subsurface data alongside frac data. “Many operators would like to analyze drilling and geosteering data to see whether they are in zone and detect changes in rock characteristics that will influence how the frac behaves,” he says. “With ML, the foundation of our sealed wellbore pressure monitoring service, they can perform these analyses rapidly enough to apply them to more wells.”
As ML algorithms become more efficient and computing power grows, operators will increasingly analyze data in real time and tweak their completion parameters during or between stages, Miller says. “When we first started offering real-time services several years ago, operators did not know what they could change because they never had the capability to analyze data so quickly,” he recalls. “Today, they have a better sense of what adjustments are beneficial and possible to perform.”
Miller says many service companies are leveraging ML to improve their products. “For example, perf gun providers have asked us how they can use machine learning to understand failures and optimize design. These lessons will inform product development and potentially enable them to advise customers on how to increase the chances of a smooth frac treatment.
“Today, one of the most common conversations we have with customers is how ML can help them evaluate and improve their ESG metrics,” Miller remarks. “We are working with operators and service companies to automate ESG reports and identify situations where they can reduce waste and emissions without sacrificing performance.”
Deploying Machine Learning
Machine learning has a vast opportunity set in the oil field, Miller argues. “ML can be a poor fit when data is gathered manually and sporadically, but when the data is available and the primary challenge is aggregating and examining it, it’s worth exploring whether ML can partially or completely automate the process. This is true whether that process is simple and repeatable or involves deep analyses and multiple criteria.”
The amount of data needed to produce a useful machine learning model can be smaller than many assume, Miller assures. He says that in many applications, even a few wells’ worth of data can suffice to create a reasonably accurate model.
“Models need not be 100% accurate in every case to be useful,” he stresses. “If the model can accurately label when stages start and stop 95% of the time, but do it a thousand times faster than engineer, it’s still powerful because the engineer only has to look at the anomalies. Similarly, a model that predicts many instances of casing deformation that would be missed otherwise is still valuable even if it can’t predict all casing deformation.”
Data quality can influence a model’s accuracy, Miller notes. “It is notoriously difficult to stream high-quality data out of the field, so ML platforms have to be capable of working with low-quality data,” he says. “For many use cases, such as crew efficiency comparisons, the platform will clean up the data automatically. For more time-sensitive use cases, such as alerts during pumping, we may sacrifice some accuracy to provide faster results.”
Miller encourages companies who want to use machine learning to partner with experts. “It can take years and millions of dollars to hire data scientists, aggregate data from throughout an organization, build machine learning models and find a way to run them at production scale,” he warns. “By partnering with companies who already have made the necessary investments and have data scientists on staff, operators can get a much faster time to value.”
A Simple Idea
Seemingly simple improvements can have a huge impact on costs, reflects Joe DeGeare, chief executive officer of AWC Frac Technology. As a case in point, he offers AWC’s frac valve control system, which facilitates continuous multiwell fracturing operations by replacing multiple conventional hydraulic accumulators–one for each frac tree–with a single high-performance hydraulic power unit (HPU) that powers multiple freestanding control panels–one for each frac tree. As currently designed, each control panel can operate six frac valves.
“Not having to bring accumulators on site for every frac tree,” DeGeare says, “reduces the frac stack company’s capital expenditure or rental costs, simplifies maintenance, lowers emissions, shrinks the on-site footprint, and lowers risk of equipment failures.” According to DeGeare, these benefits add up to significant savings on pads with three or more wells. On a six-well pad, he estimates replacing six conventional accumulators with one AWC HPU can cut CAPEX by approximately $100,000.
AWC Frac Technology says its frac valve control system eliminates the need to bring a hydraulic accumulator on site for each hydraulic fracturing tree. Instead, a single HPU powers several freestanding control panels (one for each tree). According to the company, this approach reduces costs while simplifying maintenance and transportation.
The system’s environmental contributions are significant, DeGeare assesses. “Every conventional accumulator we eliminate reduces CO2 emissions by an estimated 235 kilograms a day,” he reports. “And that does not include the cost and emissions reductions from lower transportation requirements. For example, getting six conventional accumulators to a pad requires at least two trucks. To transport six freestanding control panels and one HPU, we only need a one-ton truck with a float trailer.”
Eliminating conventional accumulators and associated components also reduces risk of equipment-related downtime without sacrificing redundancy, DeGeare says. “Our HPU has two engines, two auto-start systems and 50% more accumulator bottle capacity than required, plus an air backup system,” he describes. “Frac companies can be confident operating without a second HPU for backup.”
Since AWC introduced the frac valve control system in February 2020, not a single control panel has failed, DeGeare reports. Failures are unlikely if the equipment is properly maintained, he says, adding that the HPUs and control panels are easy to work on. “Both motors on the HPU slide out so they are accessible from all sides, and all other key components are easy to service or replace quickly,” he assures.
Landing Casing
As laterals have gotten longer, mitigating friction between the casing string and wellbore has become an increasingly important element of getting casing to bottom, observes Justin Johnson, product line manager for well construction at NCS Multistage. He says flotation subs, which were first introduced by NCS in 2012, have proven to be one of the most reliable and affordable ways to achieve that goal. “In general, a flotation sub will cut friction in half and make running casing much easier,” he says. “In some applications, a flotation sub can save an operator days of costly drilling rig operations.”
While the original flotation sub has a ceramic barrier and has been widely adopted, Johnson reports that many operators have begun requesting a glass barrier, and there now are many such products on the market. “Glass generally has a lower pressure rating than ceramic, but shatters into smaller particles, which is perceived in the industry as an advantage,” he explains.
“To give glass the pressure rating needed to withstand the weight of the fluid in the vertical wellbore, while still ensuring it will burst on demand once the casing lands, many factors need to be controlled, such as the tempering, chemical makeup and geometry of the glass. Engineering glass products is never easy, but through a significant investment in research and development, NCS has designed a robust solution to this problem,” Johnson says.
While some operators prefer casing buoyancy systems with glass barriers, others continue to deploy ceramic flotation subs, NCS relates. Either material can offer reliable performance, the company assures, noting that glass breaks into smaller fragments and ceramic provides higher pressure ratings.
Since introducing its glass flotation sub, NCS Multistage has achieved a 100% success rate across more than 80 runs, he reports. “Success in this context means the glass seal stayed intact until the casing had reached total depth, at which point the operator successfully removed the seal by applying a predetermined shear pressure,” he says.
Even with modern materials science, most glass flotation subs have a pressure rating around 10,000 psi, which drops as temperatures increase, Johnson notes. He says this has prevented glass subs from being used in particularly hot or deep wells, including ones in the Eagle Ford and Haynesville.
“For those wells, NCS continues to recommend its original ceramic product, which can achieve pressure ratings as high as 12,500 psi,” Johnson says. “Even in lower pressure applications, many operators continue to choose ceramic subs because they have proven successful in such applications for nearly a decade. In fact, NCS has completed more than 12,000 runs with ceramic flotation subs and can count on one hand the number of times a sub has failed to break as designed, or has broken early.”
Even so, the company is looking for ways to increase the temperature and pressure ratings of the glass barrier. “In the U.S. land market, most plays are shallow enough that we can use glass flotation subs,” Johnson acknowledges. “However, as these products gain popularity across the globe, we will encounter more situations that push NCS Multistage to continue innovating beyond the limits of today’s products.”
Simplifying Flowback
To improve safety, reduce costs and shrink their environmental footprints, operators want to manage the sand that returns during flowback with less equipment and fewer people, reports Mark Freeman, the president of EnerCorp. He recommends using an integrated system that automates sand management.
“The linchpin of our system is a cyclonic separator that can remove 97.0%-99.5% of the sand and other solids from the production stream,” he says. “The almost solids-free stream eliminates the need to periodically shutdown a well to clean sand from tanks and separators, as well as the risk of damage to production equipment and pipelines.”
Freeman attributes the separator’s high efficiency to research that involved more than a year of simulating fluid dynamics inside cyclones in extreme detail. “When we ran our simulations, we did not take any shortcuts,” he describes. “Instead of looking at single-phase flow to save time, we modeled oil, water, gas and solids to understand how different internal geometries affect the sand separator’s performance. By adjusting those internals for each application, we can achieve high separation rates.”
EnerCorp reports that its sand cyclones reliably remove more than 97% of sand and other solids from new wells’ production streams. The company says this consistency enables it to automate flowback management while reducing the risk of damage to downstream equipment.
Before developing the cyclonic separator, EnerCorp generally managed sand using two cyclones and a sand filter. “Now we can condense these three pieces of equipment, which are large enough that they need to be transported on semis, into a single cyclone. This consolidation cuts transportation costs and emissions, as well as the on-site footprint,” Freeman says.
The cyclone has a chamber at the top that spins the fluid to separate the solids, which drop into an accumulator. “When this accumulator is almost full, we open a valve and let the well’s pressure push the sand into an open-top tank,” Freeman describes. “Opening and closing a valve is a simple process to automate, especially when we only need to do it on one cyclone.”
To illustrate the benefits of automation, Freeman recalls a six-well pad that traditionally required 12 people (six during the day and six at night) to manage flowback. “By replacing legacy equipment with an advanced separator, we got the crew size down to eight,” he relates. “With automation, we would have needed only one or two people on site. Eventually, we may be able to manage flowback remotely.
“By removing people from the location, we are minimizing workers’ exposure on site and the need to drive to and from the site, which is one of the most dangerous tasks in the oil field,” Freeman says.
Freeman adds that efficient sand separation can reduce tank emissions. “Because we are able to remove so much sand, operators no longer need to divert production to frac tanks to let sand settle,” he explains. “Instead, they can flow directly to their production facilities, which are far more likely to have vapor recovery units.”
The Equipment
According to Freeman, EnerCorp’s integrated flowback system includes the sand cyclone, an automated blowdown unit, a sand quantification unit, a tank-level monitoring system, and a control unit that connects to the cloud. “These components work together to maximize the value of the service,” he says. “They let operators know what is happening on location whether they are at a desktop in the office or on a phone in the field.”
Looking at sand and fluid volumes alongside pressure data can help engineers determine whether to adjust the well’s choke, Freeman notes.
“We put pressure monitors and other instruments at various places so we can watch equipment performance and catch any anomalies before they become a problem,” he assures. “For example, we can detect potential leaks several hours before a person on site would know there is a chance of one developing.”
Since the automated flowback management system’s first deployment, it has handled 1.5 million pounds of sand without any leaks or environmental concerns, Freeman reports. “We are proud of that track record,” he says. “As we developed the e-flowback ecosystem, we worked with bpx energy to conduct risk assessments and ensure every piece of equipment would be ready for harsh environments.
“Today, we are testing other technologies to support the flowback process,” he says. “In the next 12-18 months, we plan to introduce several technologies that will reduce emissions, disposal costs and waste volumes.”
For other great articles about exploration, drilling, completions and production, subscribe to The American Oil & Gas Reporter and bookmark www.aogr.com.