
Wet Sand Delivery Method Results In Significant Cost, Emissions Reductions
By Kevin Fisher and Brian Dorfman
DENVER—The U.S. shale industry consumed aan estimated 112 million tons of proppant in 2022. Transporting that volume required more than 4.5 million truckloads, and is equivalent to the gross weight of 472 of the largest cruise ships ever built. Assuming every one of those truck and trailer combinations spanned an average of 50 feet, lining them up from bumper to bumper would stretch that convoy some 42,600 miles, or from Midland to Anchorage, Ak., 11 times over.
That is a lot of trucks and an incredible amount of fracturing sand. In a business environment in which operators increasingly focus on environmental, social and governance initiatives, proppant and proppant transport probably are not the first issues that come to mind when producers think about managing their operations’ emission footprints. However, given the scope of frac sand consumption in shale plays, the potential benefits of technologies such as “wet sand” delivery can significantly reduce emissions related to producing and transporting frac sand.
Producing frac sand requires a washing process to remove impurities, and historically, it has required a drying process to allow for effective transportation and on-site metering. The ability to use wet sand eliminates the need for drying, and all the emissions associated with that process.
If all 112 million tons of sand the industry delivered to a frac blender last year had been dried using efficient natural-gas-powered drying systems, it would have consumed about 39 billion cubic feet of gas. Even with clean-burning gas, that translates to an estimated 1.43 million metric tons of carbon dioxide emissions. That is the equivalent of nearly 176,000 homes’ total annual energy demand, or 3.2 million barrels of oil, which equates to more than 300,000 cars on the road for a year. To what end? The dried sand simply was mixed with water again once it arrived on a frac location.
Multimodal Wet Sand Delivery
Multimodal wet frac sand delivery not only eliminates sand drying emissions, but coupling it with today’s “proximity” wet sand mines more than doubles the already substantial emissions savings associated with shorter trucking hauls. Together, these technologies reduce total last-mile operational emissions an average 90%.
This solution offers the ability to utilize all last-mile transportation techniques, including sand containers and belly dump trailers, to maximize supply. This flexibility ensures that sand supply remains uninterrupted during very high sand throughput on multiwell pads. Moreover, the novel multimodal wet sand equipment design creates additional economic value beyond overall emissions reductions for operators and frac service providers. The benefits include:
- Lower sand procurement and last-mile trucking costs;
- Fewer on-site personnel;
- Higher throughput capability;
- More secure sand supply;
- Less road congestion;
- Consuming less conventional water;
- Reducing trucking mileage, driver count, and the associated emissions; and
- Eliminating on-site exposure to respirable silica dust, which is subject to strict federal well site regulations.
Billions of Btus, millions of tons of CO2, and other emissions can be eliminated every year by skipping the drying process. It is safer, more efficient, and saves money.
FIGURE 1
Total CO2 Emissions for Dry Sand versus Proximity Wet Sand (Metric Tons/10,000 tons of sand)
Figure 1 illustrates the amount of CO2 emitted in the process of drying and moving 20 million pounds of sand 75 miles (illustrative of a typical Permian Basin well from a fixed mine producing dry sand) versus the same volume of wet sand hauled 10 miles from a proximity wet sand mine. The emissions savings are staggering: an estimated 338 tons of CO2 saved per well (38% of which relates to eliminating sand drying). This comes out to a 91% emission savings versus the dry sand, 75-mile base case.
Reduced Emissions
A well that requires 20 million pounds of dry sand using a natural gas-fired kiln creates an estimated 170-230 tons of CO2 emissions at the mine for drying alone (Table 1). To put the significance of these emissions into perspective, if the Permian Basin fully adopted this last-mile method and technique, an estimated equivalent of 170,000 cars would be removed from the road for a year. When combined with a proximity wet sand mine, those emission reduction figures improve two- or threefold.
Since this wet sand technology and method was introduced four years ago, approximately a dozen proximity wet sand mines have been commissioned in the United States, primarily in the Permian and Haynesville plays. These plants are smaller, less capital intensive and can be built with relatively short lead times of six-seven months. They provide an operator with a secure supply and allow customers to localize their supply chains, which simplifies a complex aspect of completion operations.
A modern fracturing crew needs a truckload of sand every 10 minutes on a 24/7 basis. If the origin of that product is closer to the core acreage, it shrinks the risk of delivery disruptions that create wellsite sand shortages. If operators can secure their supply, simplify the supply chain, and save on costs while also reducing emissions, why wouldn’t they?
Cost savings are significant when an operator combines a proximity mine with wet sand operations, including:
- Capital expenditures at the mine are reduced, since no drying infrastructure is installed.
- It slashes 30%-40% of the plant’s operating expenditures.
- There are fewer emissions permitting requirements.
- Reducing mileage also means spending less on hauling.
- It trims a location’s head count requirements by 25%.
Many new technologies fail because they are not cost-competitive. This technology combines massive emissions reduction with not only the operational benefit of a simplified supply chain, but also a significant cost reduction for each well. Operators that have adopted this method have publicly announced savings in the range of $100,000-$300,000 a well.
In the event that the United States adopts a carbon tax, gas usage will become even more pressing. Using frac sand demand figures from 2022, a tax of $20 a ton of CO2 emitted would have added up to almost $28 million in additional costs to dry frac sand. Combined with trucking from a conventional mine (75 miles away), a simple $20 carbon tax would have added an estimated $83 million in annual costs that, ultimately, would have to be passed on to the U.S. consumer.
Some 300,000-400,000 Btus are required to dry one ton of processed/washed frac sand. We estimate nearly 1 million tons of CO2 were emitted in 2022 in the Permian Basin alone merely to dry frac sand. Moreover, at an average 2022 Texas industrial natural gas price of $6.89 an Mcf, the Permian Basin would have spent over $138 million in fuel cost for the drying process last year. Consider all this economic and emissions impact in light of the fact that the dried sand is destined to be mixed with water to re-wet it before it is pumped down hole. How does that make sense?
New Wet Sand System
Wet sand is more difficult to move than dry sand because of its inherent grain-to-grain cohesion. Those who have built sandcastles can testify to the durability of those structures thanks to wet sand’s “stickiness.” That same stickiness makes it difficult to move wet sand without some added energy because it does not flow as easily as dry sand.
The industry’s initial last-mile system for delivering wet sand from truck to blender adds this energy by applying tuned vibration. This breaks the particle cohesion and sets the wet sand into motion out of the containers from which it has been delivered. An additional and unique patented feature entails a metering belt delivering wet sand directly into the blender tub, bypassing the surge hopper with augers, which always have been a consistent source of problems for frac service companies. This state-of-the-art wet sand system has pumped more than 3 billion pounds of wet sand successfully at daily volumes sometimes in excess of 12 million pounds for a single frac crew.
The combination of state-of-the-art multimodal wet sand delivery systems and “proximity” wet sand mines can reduce the total emissions associated with last-mile frac sand operations by 90%.
The next challenge was developing next-generation wet sand handling equipment with a design goal to make it multimodal so it could employ containers, belly dump trailers, side dump trailers, sand out of a pile, sand from a pipeline or almost any conceivable sand delivery mode. A new system eliminates vibration as the motive force and instead tilts the containers. This action dumps the wet sand out of the top of the container rather than draining it out of a gate at the bottom.
The new containers are placed on platforms by a forklift, where grapples secure the container to the platform. The platform then is raised and tilted into the large hopper, allowing the wet sand to dump from the top of the container. This allows the wet sand to discharge faster and more smoothly, while a high-capacity belt hopper holding nearly 100,000 pounds of sand delivers product consistently to the metering system. Much like the first-generation system, the patented metering belt functionality is utilized to deliver sand directly into a blender tub.
The static volume of the system’s large hopper belt allows for multimodal filling of the hopper through more than simply conventional sand containers. The system has discharged sand in containers, from a loading belt feeding the big hopper, and from piles of wet sand deposited on the ground via a front-end loader. In addition, multiple delivery methods have been combined to guarantee sand supply remains uninterrupted no matter the roads, traffic, weather or any other influences that can affect delivery efficiency.
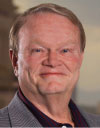
KEVIN FISHER is the founder, president and chief executive officer PropX. Prior to PropX, he was president of Liberty Oilfield Services. Before that, he served as executive vice president of business development at Flotek Industries and as CEO of Pinnacle Technologies. Fisher began his career with Halliburton in 1979, and holds numerous U.S. patents related to spectral gamma ray, gravel pack density logging, tiltmeter instrumentation, frac fluid and last-mile proppant handling equipment. He holds a B.S. in natural science/physics from Cameron University.
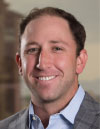
BRIAN DORFMAN is vice president of operations at PropX, a company dedicated to improving last-mile proppant logistics. He began his career at Halliburton in 2011, working various technical and sales roles in the Rockies business unit before leaving to be part of the startup team for PropX in 2016. Dorfman holds a B.S. in finance and a B.S. in accounting from Georgetown University.
For other great articles about exploration, drilling, completions and production, subscribe to The American Oil & Gas Reporter and bookmark www.aogr.com.