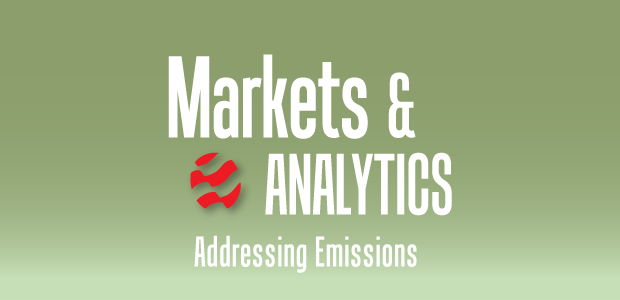
Scanner Allows Techs To Find Methane Leaks During Routine Maintenance
By Tim Novick
Methane leaks can be expensive. If a spark ignites gas leaking from a compressor and the engine catches fire, the cost to repair or replace equipment easily can reach $1 million or more, even after accounting for insurance.
Although maintenance can minimize such events, they remain common enough that many upstream and midstream companies are looking for better ways to find leaks. This quest is driven in part by a desire to preserve the environment and stay ahead of ever-tighter regulations. Because methane is 84 times more potent as a greenhouse gas than carbon dioxide, minimizing methane emissions is a priority for regulators and environmentally-minded investors.
But for many oil and gas companies, the biggest driver of leak prevention efforts is safety. Personal monitors and sniffers can detect hazardous concentrations of methane, but they generally do so only after someone already is standing in a dangerous cloud of the odorless gas.
Long-Range Detection
With this reality in mind, many maintenance teams have begun using portable scanners that pick up methane from as far as 330 feet away. These scanners work by shooting a conical beam of near-infrared light onto any surface and measuring the reflected beam to see if the light has passed through methane. If so, the device beeps to alert the operator. An LCD provides details on the alert, including an estimate of the methane concentration.
The beauty of this technology is how easy it is to use. It is comparable to shining a flashlight in a dark room. As long as the light has a surface to bounce off (such as piping, an engine or a tank), the scanner will pick up methane concentrations as low as five parts per million per meter. A technician can learn how to use it in a few minutes, then check assets in a fraction of the time required with traditional tools.
Because the scanner works at a distance and only picks up methane, technicians can look for leaks without turning off engines or otherwise disrupting operations. Nor do they need to wait for the tool to warm up before using it.
Technicians quickly realize how much they can do with the scanner. During demonstrations, they often take it out of the provider’s hands so they can start checking areas where they suspect a leak is occurring. It is not uncommon to locate unknown leaks that are severe enough for the technician to shut the equipment down and call for repairs.
Speed and Convenience
Technicians get excited about the open path laser because it offers a quick way to find leaks that represent a safety risk and lost revenue. Instead of waiting for quarterly, semiannual or yearly leak detection and repair (LDAR) surveys to learn of any needed repairs, they can turn the device on from a safe distance and sweep it across the points of interest. In addition, after any necessary repairs, they can use the device again to verify leaks have been mitigated and the asset is in proper working order.
This process works so well that many companies now use the scanners as part of routine compressor maintenance. At sites with several compressors, the periodic scans can help technicians identify those that need attention by picking up excess methane slip, leaks from crankcase vents or other indicators that something is off. These early warnings enable them to diagnose and fix the leak’s root cause before it leads to unplanned downtime and more expensive repairs.
The repairs themselves also go faster. Panning the scanner over all of a compressor’s valves, flanges and fittings can reveal which ones need to be repaired or replaced more quickly than traditional leak detection techniques.
The scanner’s affordability enables it to be included in everyday routines. The initial cost is a fifth or a sixth as much as that for an optical gas imaging (OGI) camera. The price is higher than some gas detection technologies, but the scanner requires so little maintenance that the total cost of ownership proves much lower over a lifetime.
The scanner works by applying tunable diode laser absorption spectroscopy (TDLAS). When the beam it produces comes back to the lens, the instrument measures the total absorption of the laser from beam transmission to reception. TDLAS instruments are tuned to a specific molecule, which in this case is methane. Such tuning means the device only picks up methane rather than other gases, rendering it immune to the cross-gas contamination seen in conventional detectors, including electrochemical cells, infrared, flame ionization devices and metal oxide sensors.
Detecting methane and methane alone is a huge benefit given how much new regulations and investor concerns focus on methane specifically.
TDLAS also eliminates the risk of drift. With most instruments, changes in temperature, pressure and humidity gradually cause readings to move off their calibration curve. To compensate for these changes, the instruments need to be recalibrated periodically to keep their measurements’ accuracy within an acceptable range. Eliminating the headache associated with calibration adds up to significant time and cost savings.
The TDLAS scanner’s simplicity can be a huge boon during any sudden surge in demand for leak detection. After an aggressive freeze, such as January 2024’s Winter Storm Heather or February 2021’s Winter Storm Uri, the potential for leaks in the oil and gas industry and other sectors increases because extreme cold causes elastomer seals to contract and potentially crack. When emergency crews are called into service to find leaks, pulling additional equipment off the shelf at the last minute, they often discover their equipment needs to be recalibrated before use. With a TDLAS device, they can get to work right away.
The scanner is built for the field. It can endure the vibrations associated with riding down a gravel road in a truck bed or the impacts that occur falling out of the car or being dropped in the field. Based on experience with other TDLAS devices, it would not surprise me to see a scanner manufactured in 2024 working 15 years later with little maintenance beyond occasionally wiping off the lens.
Safety First
For safety reasons, the methane-specific scanner includes an internal test cell containing a known quantity of methane. As the device turns on, it passes the laser through this bump test cell to verify proper operation. In the unlikely event it can’t detect the gas or measures the amount incorrectly, the instrument will shut off to eliminate any risk of telling a technician an area is safe when it contains potentially explosive levels of methane.
The scanner does not replace the OGI cameras generally used for mandatory LDAR surveys. However, it will allow certified OGI technicians to focus on regulatory compliance, while empowering other team members with a more affordable instrument to safely scan for leaks outside of prescheduled LDAR checks.
Almost all facility managers I have met love the idea of identifying leaks more frequently. They want to look for and fix leaks rather than reacting to surveys that only occur at prescribed intervals.
Of course, the end goal is to prevent leaks to begin with. To do that, many companies analyze the information the instrument collects to spot trends and figure out why they occur. For example, they may notice that a specific fitting tends to fail earlier than expected and replace it with an alternative more suited to the application. Such lessons can improve designs for future facilities.
To simplify data collection, the scanner can be paired via Bluetooth with a mobile app that automatically records where the scanner goes, when it detects methane and how much methane it detects, as well as the device’s serial number and the operator’s information. At the end of the day, the technician sends the recorded data to a cloud-based repository with the press of a button. There is no need for humans to interact with the data, which saves time and eliminates the risk of human error.
Digitizing and centralizing data collection also means that all the data arrives in the same format, regardless of who collected it, when collection took place or where it occurred. This lets companies focus on analyzing the data rather than combing through emails, spreadsheets, databases and handwritten notes to collate data and correct labeling and reporting eccentricities.
The software can handle basic analyses, such as tallying leaks and associated emissions in an area. It also can make trends more obvious by tracking repeat leaks. The first time a leak occurs, it will record it as a parent. If the leak reoccurs, the new event will be tied to the parent.
Pairing the scanner with a phone or tablet is optional. If a company wants to check sites without worrying about setting up software or collecting data—a common situation when companies first begin trying a new tool—it can.
As companies across the oil and gas value chain strengthen efforts to mitigate methane emissions, they are relying on a suite of devices to detect, pinpoint and quantify leaks. Many of these devices’ underlying technologies have multidecade track records in applications that demand precision, reliability and traceability.
The TDLAS scanner’s simplicity, reliability and low cost make it an ideal first step as companies begin their emissions management journey. However, most eventually will want more information than any single device alone can provide.
Next Steps
On some sites, it makes sense to install permanent monitors that watch for leaks and notify the operator when one occurs. These monitors frequently take the form of sensors at a facility’s fence line that can pick up unusual emissions and calculate the area from which they originate using Gaussian plume modeling. Even accounting for wind speed and direction, temperature and other factors, such modeling only approximates the emission source.
Similarly, satellites, planes and drones can alert users that emissions are occurring and point to a general location. Resembling smoke alarms, they issue warnings when something unusual is occurring in a general vicinity or asset but do not pinpoint the leak’s exact origin. Usually, someone must travel to the site to find the source.
The methane scanner can perform this function quickly and reliably. When technicians use it, they know exactly where they are looking. The optical beam used with TDLAS is invisible to the human eye, but a red dot sight and laser pointer show where it’s directed. When the scanner beeps, technicians can glance at the LCD to see the methane concentration and an estimate of the reading’s quality. These indicators can help the technician pinpoint the leak’s source.
As they weigh where to deploy permanent monitors and which investments to make in emissions management, companies often survey several sites for an emissions baseline. In the past, these surveys generally required methodical, close-up work with OGI cameras. Today, they can be performed more quickly by using the TDLAS scanner to find leaks, before turning to a more sensitive and precise tool to quantify them.
Ideally, surveys should use a leak quantifier that directly measures methane rather than relying on OGI cameras or other devices that extrapolate concentrations from models. Coupled with digital data collection, which can track when and where readings occur, direct measurements make surveys much easier to audit.
For now, many decisions related to preventing emissions do not require precise quantification or full traceability. But given the interest in methane from regulators, investors and the public, it’s likely the standards for emissions measurements will continue to tighten, with direct measurements gradually replacing estimates in many contexts.
One sign of that transition is the proposed Securities and Exchange Commission rules requiring public companies to report their Scope I emissions (direct greenhouse gas emissions from internal operations rather than service providers or end users). If the reported numbers come from extrapolations, auditors are in a tough spot. It’s hard to trust the reliability and accuracy of an emissions estimate based on an algorithm when other algorithms’ results will differ. Those differences may be minor for daily operations, but auditors need more certainty.
Recognizing that truth, carbon offset providers and companies seeking tax credits for emissions reductions have focused on direct measurement for the past 20 years. These industries started with models but quickly realized direct measurements would be required for the most profitable classifications. Their need to collect those measurements efficiently and build a comprehensive but understandable audit trail has driven decades of investment in instruments and software that will benefit the hydrocarbon industry as its needs evolve.
In the oil and gas industry, the markets occasionally may reward low-emissions production with a slight premium. However, it is likely emissions primarily will influence buyer preferences, with low-emission gas being purchased first while high-emission gas is pushed out of certain markets. Eventually, measuring and mitigating emissions may become part of the license to operate.
If this prediction comes to pass, I think the industry will embrace the challenge. Given methane’s status as a safety hazard, revenue source and greenhouse gas, people from the office to the field have strong incentives to keep it in the pipeline. The key is giving them fast, affordable and reliable ways to find leaks.

Tim Novick is the chief executive officer of Ecotec International Holdings LLC (“ECOTEC”), which provides tools and software for identifying, quantifying and measuring emissions, including the Gazoscan open path laser. In his current role, Novick manages the strategy, direction and implementation of ECOTEC across offices in the United States, France, Italy and the United Kingdom. He has worked with the company in various capacities since 2015, first on the advisory side and then later joining full time in 2017. Novick began his career as an investment banker at Barclays and later transitioned into an investing role in private equity at The Gores Group. He holds a B.A. from Princeton University and an M.B.A. from Northwestern University’s Kellogg School of Management.
For other great articles about exploration, drilling, completions and production, subscribe to The American Oil & Gas Reporter and bookmark www.aogr.com.