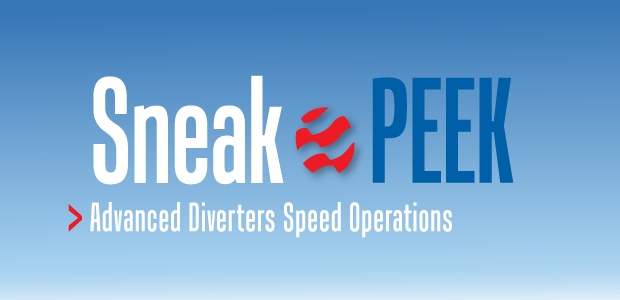
Advanced Diverters Speed Operations
By Colter Cookson
When proppants go down hole, they behave much like many high school students do three days away from spring break: given a choice between an easy and hard path, they almost always take the easy option.
The nonvacationing proppant typically flows to perforations with the lowest entry pressures while leaving high-pressure perforations poorly stimulated and unproductive. To promote more even proppant distribution, operators frequently deploy diverters to temporarily block the low-pressure perforations. These diverters range from particulate materials that bridge fractures by agglomerating down hole to preformed plugs that stop flow by seating inside the perforation.
Today, many diverters are made from materials that seal perforations during fracturing, then degrade or dissolve to remove themselves from the wellbore. This can lower well costs by reducing or even eliminating downtime associated with milling mechanical plugs and allowing diverters to be deployed in areas milling assemblies struggle to reach.
To bring degradable diverters’ savings to more wells, suppliers report they are developing versions that work in more extreme temperatures and remain intact for shorter or longer periods. At the same time, the suppliers are applying the diverters to control fluid loss or enhance oil recovery. They also are figuring out how to place diverters farther away from the wellbore to mitigate frac hits and promote fracture network complexity.
“Because far-field diversion requires more material than near-field diversion, we are seeing phenomenal demand growth,” says Frank Diodato, business development leader for NatureWorks, which manufactures polylactic acid (PLA), the base material for many degradable diverters. “We doubled sales to the oil and gas market in 2019, and 2020 is looking like it will have similar growth.”
NatureWorks Application Engineer Chad Kamann describes PLA as a fantastic diverter material. “PLA’s thermoplastic characteristics allow the diverter manufacturer to turn the material into precisely shaped powders and flakes, meaning it can develop a blend that will consistently plug fractures,” he says.
“But PLA’s biggest appeal is its tunable performance,” Kamann argues. “As it is exposed to water and heat, PLA turns into lactic acid through hydrolysis. By manipulating the chemistry, we can fine-tune how long this takes to ensure the diverter lasts long enough to do its job and then gets out of the way.
“PLA leaves no residue after hydrolysis, so it is unlikely to damage the formation,” Kamann says. He points out the lactic acid is so benign the U.S. Food and Drug Administration recognizes it as generally safe for use in food, one reason PLA often is the key component in compostable cups, plates and eating utensils.
Selecting the Right PLA
For any degradable diverter to be effective, Diodato stresses, operators must use the correct one for the specific application. “Since we began supplying materials for oil field diverters 10 years ago, we have heard stories from people who had poor experiences with diverters. Sometimes the diverter would last much longer than intended or leave residue behind,” he says. “When we investigate, we often discover the operator used the wrong grade given the well’s temperature and the desired degradation time.
“In some cases, the diverter likely was made from something other than PLA or was based on contaminated scrap,” he adds.
Polylactic acid (PLA) is one of the most popular base materials for degradable diverters. Manufacturer NatureWorks attributes PLA’s success to how well its degradation rate can be tuned for different temperatures and applications (top), as well as the variety of forms it can take (bottom).
Kamann says NatureWorks provides polymers that work in temperatures as low as 120 degrees F and as high as 300 degrees and last anywhere from a few hours to several weeks. He adds that the low-temperature versions do not require special handling or equipment.
Diverter suppliers create highly engineered combinations of particulates, flakes or powders from the PLA pellets NatureWorks manufactures, Diodato notes. “There is a surprising amount of science that goes into ensuring the particle sizes are consistent and have the right distribution,” he reflects. “As the raw material supplier, our job is to make sure the diverter design starts off with the right polymer choice.”
Diodato points out that the company has been manufacturing polylactic acid for 30 years and operates the world’s largest factory in Blair, Ne. He says the company’s other fast-growing markets include 3-D printing, an application that requires repeatable performance in a variety of printers and environments, and compostable coffee pods and tea bags, which must have finely tuned heat and impact resistance.
PLA is made with renewable resources. “We use plants to capture and sequester carbon dioxide and transform it into long-chain sugar molecules. We ferment those sugars to make lactic acid, the building block of a wide range of advanced PLAs,” Diodato details.
When they are used to improve cluster efficiency, Kamann says PLA-based diverters can deliver measurable increases in production. “We are looking at developing even lower-temperature diverter materials and solutions for building filter cakes and controlling fluid loss during drilling,” he says.
Lost Circulation
Degradable diverters have the potential to be a fantastic way to stop lost circulation during drill-out or clean out operations, says Nick Koster, vice president of technology and applications for DiverterPlus LLC. However, the application requires shorter-lived products.
“The long-lasting diverters used in hydraulic fracturing work fine for drill-outs or clean outs when everything goes perfectly, but if something unexpected happens, the tool can get stuck until the diverters degrade,” Koster warns. “In low temperature wells or situations that limit the diverter blend’s exposure to fluid, waiting for that to happen will be extremely expensive.”
Rather than risking such costs, many operators stick with traditional diverters, such as rock salt, that require much greater volumes to be effective. To reduce the risks so degradable diverters can be used in more wells, Koster says DiverterPlus has developed ones that degrade rapidly even in low temperatures.
“By sacrificing the ability to withstand high pressures in order to accelerate degradation, we have created diverters that only last a few hours in downhole temperatures as low as 60 degrees F,” Koster details. “Because they go away quickly, operators can be more aggressive with these diverters.”
From January to March, Koster says, sales for fast-degrade diverters doubled. “Many of the buyers are operators and service companies that want to use the diverters with coiled tubing units to clean wells and distribute chemistry into each cluster,” he remarks.
“Disposal well operators are using them too,” he continues. “Disposal wells are so conductive that it is hard to bridge a section using rock salt, and if the operator succeeds, it requires a tremendous volume. The degradable diverters can deliver better results at 10% the volume.”
Permanent Diversion
Other well applications call for permanent or semipermanent diverters, Koster says. “These diverters do not have as much strength as cement or liners, but they are strong enough for many jobs while being more affordable and less risky to deploy,” he says.
Particulate diverters are becoming more versatile as suppliers introduce formulations that only last a few hours or provide permanent seals. According to DiverterPlus, the fast-degrade diverters excel at controlling lost circulation during well clean-out, while the permanent versions support enhanced oil recovery projects and streamline plugging and abandonment.
The permanent diverters are used in plugging and abandonment operations to stop gas migration and seal off formations in vertical wells that are no longer economic so others can be developed, Koster says.
“We also have deployed them to refracture high-temperature wells where it is difficult to create a temporary diverter that will last two-four weeks,” he relates. “After squeezing the diverter into the lateral, operators can complete the well as if it’s new at their convenience. Then, they use a wash to break the diverters.”
DiverterPlus is testing whether these permanent diverters deliver long-term benefits in enhanced oil recovery applications. “In most EOR applications, the operator injects fluids into one well to push hydrocarbons toward another well,” Koster notes. “The fluids are meant to go into the primary matrix, but they often end up flowing through highly conductive fracture networks that already have been produced.”
Koster suggests this wasteful flow will become more common as EOR moves into shales, which have limited conductivity outside induced fractures. “By blocking those fractures with diverters, we should be able to force the injected fluid into the primary matrix and significantly improve recoveries,” he predicts.
In case something goes wrong, Koster says the diverters include an “undo button.” “They are strong enough to withstand everything they are likely to encounter down hole, but if they don’t have the desired effect, the operator can pump a specialized breaker to remove them,” he describes.
Offshore Applications
To take degradable diverters offshore, DiverterPlus had to come up with a way to protect them from the alcohol-based fluid systems used there. “Almost every polymer will dissolve in xylene and toluene,” Koster explains. “To stop that, we coat the plastics to give them extra resistance.”
For now, the coated diverters are used almost exclusively in gravel packs. According to Koster, the goal is to block channels within the packs that keep asphaltene and scale treatments from performing. He points out that traditional diverters for this application must be deployed in a liquid form to penetrate the gravel pack, which limits their endurance under differential pressures.
“Through chemical deposition, we can make diverter particles with precise geometries and sizes as small as 25,000 mesh,” Koster says. “Think of them as engineered dust. They are small and buoyant enough to stay suspended even if flow stops, which is critical offshore, where remediation is costly.”
The particles travel through the gravel pack until they reach the formation face, then combine to form a seal. “This seal forces the treatment to stay in the gravel pack rather than entering the formation, making it more comprehensive and effective. Ultimately, this extends the time between treatments and allows more oil to flow through the pack,” Koster says.
Aid From Proppant
Pumping neutrally buoyant proppant (NBP) down hole alongside degradable diverters frequently improves well economics, says Harold Brannon, vice president of production enhancement at Sun Specialty Products. “At first, the proppant helps plug the fracture. Once the diverters degrade, it keeps the fractures from collapsing so more hydrocarbons can enter the wellbore,” he explains.
By blending neutrally-buoyant proppant with particulate diverters, operators can improve production, Sun Specialty Products reports. The proppant helps the diverters control flow during fracturing, then keeps fractures open once the diverters disappear.
NBP can deliver these benefits because it, like most particulate diverters, has an extremely light weight and low specific gravity. This allows the proppant to stay with the diverter particles as they travel to the fracture network, Brannon says.
NBP’s low specific gravity also means it stays suspended easily, adds Ron Coulter, Sun’s vice president of executive sales. He says this improves performance by enabling the proppant to travel farther into the fracture network and maintain a near-homogenous distribution in the fluid rather than collecting toward the fracture network’s floor.
“With sand, only 25%-35% of the induced fractures receive proppant,” Coulter estimates. “NBPs enter as much as 90% of the fracture network, and the more fracture propped, the higher the production.”
Wells that mix proppants with diverters frequently experience fewer frac hits, Brannon says. “We don’t know for sure why the blends protect wells, but it’s likely the diverters are plugging runaway fractures that otherwise would allow well-to-well communication,” he indicates.
Because NBP costs less than equivalent degradable materials, Brannon says pumping it with diverters can shave a few thousand dollars off each frac stage’s cost.
Low-Temperature Diverters
Since heat drives thermoplastics’ removal, designing thermoplastic diverters for low-temperature wells can be tricky. Get it wrong, and partially removed fragments can plug the formation or damage equipment by coming up the wellbore during flowback, warns Bessie Psihogios, market development manager for Soarus LLC, a group company of Mitsubishi Chemical.
By augmenting a polyvinyl alcohol to create a butanedial polyvinyl alcohol (BVOH) that dissolves in saltwater, Psihogios says Mitsubishi has developed a diverter that dissolves consistently in low-temperature wells. “We have formulations for temperatures as low as 40 degrees F or as high as 230 degrees F,” she says.
In diversion applications, the BVOH-based diverter is sent down hole as a mix of pellets and powder between 8 and 10 mesh in size. The pellets agglomerate to bridge the fracture but leave gaps, which the powders plug, Psihogios describes. Both the pellets and plugs swell by picking up water, creating a tight seal.
A shear-thickening diverter from Soarus creates strong barriers across fractures. The barriers generate spikes in surface pressure that are easy for crews to spot and give them the confidence to proceed quickly, Soarus says, adding that certain BVOH diverter formulations work in temperatures as low as 40 degrees F.
“The BVOH thickens in the presence of shear forces, so as it bridges the fracture, it forms a strong gel,” Psihogios says. “During the frac, when pressures are high, almost nothing can go through it. Once the frac ends, pressures decline and the barrier breaks.”
As temperatures rise after the frac, the bridge’s components dissolve. Psihogios emphasizes that this process only requires water and heat, and occurs even in salty, acidic or basic fluid conditions. It can take one-five days depending on the temperature, and once it’s done, there’s no risk the diverter will solidify as the well cools during clean-out.
To test the diverter’s strength, Soarus worked with Premier Oilfield Laboratories. “Premier told us that even after they bridge the slots on its test equipment, most diverters allow water to drip through. Ours was the first that let nothing pass,” Psihogios recalls.
In the field, the bridge’s strength has a side benefit. “As the barrier forms, surface pressure increases more sharply than it does with most diverters, so the crew members know the diverter is working. They don’t have to wonder or wait for a gradual signal before they go to the next step,” Psihogios details.
This pressure spike is easy to spot even when the operator is sending the diverter down with proppant, Psihogios assures. “Our material is unique in that it binds to the sand and helps it move to the fracture. This means operators can pump at 90-100 barrels a minute, and still get diversion pressure,” she says.
Because BVOH softens in water, it is not as likely as hard diverters to damage equipment, Psihogios mentions, noting this eliminates the need to use dedicated diverter pumps.
Since its first field trial in June 2018, the BVOH-based diverter has been deployed in 40 Permian Basin wells, Psihogios reports. “We plan to try using the 80-degree version to control lost circulation during drill-outs and already have used the technology in three acid fracs,” she comments.
“We also are applying other specialty BVOHs to the oil field,” Psihogios says. “For example, to seal water-prone zones, we are experimenting with a grade that can absorb 200-300 grams of water for every gram sent down hole. Our current product is temporary, but we are developing a permanent version for plugging thief zones during drilling or watered-out formations during production.”
Eliminating Plugs
Operators can reduce or eliminate the need for bridge plugs significantly during completions by using pods to plug perforations, says Jenna Robertson, SlicFrac product line manager for Thru Tubing Solutions. She says the company has helped operators perform more than 50 plugless completions, with as many as 55 stages in a single wellbore.
“It takes time for operators to become comfortable with the pods and try a plugless completion,” Robertson acknowledges. “Most operators initially include the pods in their completion design by using them to replace bridge plugs at the toe of the well, or the portion milling assemblies can’t reach. Once they see the results, they often look at optimizing their full wellbore design by extending stage lengths, which reduces their total plug count.”
Results from two wells in the Austin Chalk show how much diversion pods can improve cluster efficiency and production. At the 90-day mark, Thru Tubing Solutions relates, the well with pods had produced 6,700 more barrels of oil than its peer.
As an example, operators may double their standard stage length by shooting more clusters across each wireline run. “Reducing the number of wireline runs and bridge plugs by half shortens frac pumps’ standby time,” Robertson says, “resulting in total savings that can add up to $500,000-$750,000 for each well.”
The pods are designed to seal the dominant perforation from inside the casing, Robertson says. They resemble a solid core made of dissolvable fibrous material with tassels on both sides. “As each pod flows down hole, the loose ends catch the turbulent flow and carry the pod to the dominant perforation, creating a strong intrawellbore seal,” Robertson outlines.
The pods are made of individual fibers that deform slightly to compensate for variations in the perforation’s size and shape. They are designed to reliably seal each perforation, with one pod for each perforation. According to Robertson, they have been used successfully across 2,000 wells.
To improve cluster efficiency, TTS suggests deploying pods during each stage. “In many applications, operators complete half the stage, then drop pods to seal the dominant perforations before pumping the remaining proppant. In extended stage applications, we typically see better results by splitting the stage more often to allow smaller segments to be stimulated with each proppant cycle,” she says.
It is common for each stage in these applications to have two-five diversion cycles, Robertson details, noting that more are possible if needed.
“When we compare wells that use the pods with ones that employ traditional diversion techniques or no diversion at all, we typically see a meaningful increase in production,” Robertson reports. “For example, one Austin Chalk horizontal on a two-well pad produced 6,700 barrels more than its partner after only 90 days on production.”
Pod-based diversion tends to increase production in part because the seal occurs inside the tubing, Robertson suggests. “This means the entire perforation is blocked, causing the fluid/proppant to divert to a new contact point within the reservoir. By sealing the perforation from the inside of the casing, there’s little risk of leaving any residual material in the reservoir,” she says.
To simplify removal, Thru Tubing Solutions makes the pods from materials that degrade when the well heats after the frac. “In wells where some or all the bridge plugs have been replaced, this lets operators complete the post-frac clean-out trip faster and turn the well over to production sooner,” Robertson says.
Restimulation
The pods can be deployed for restimulations ranging from full refractures to acid stimulations and/or scale squeezes. “With some of the acid treatments and scale squeezes, we have seen a significant production increase ranging from two to four times previous rates,” Robertson reports.
For a refracture, TTS typically recommends running a camera or caliper before the job to check for casing damage and quantify perforation sizes. “After a well has been producing for several years, many stages have a couple washed-out perforations, especially if the original completion used inadequate diversion,” Robertson observes. “To plug these large and sometimes oddly-shaped perforations reliably, we can customize pods with fit-for-purpose designs to ensure we achieve the best possible results for the wellbore.”
Robertson says the company has plugged holes as small as a fifth of an inch and as large as three inches long by an inch and a half wide with jagged edges.
“On vertical wells, we can go back and perforate sections of the well or intervals that were never stimulated in the original design,” Robertson continues. “The pods offer a less expensive alternative to straddle packers or squeeze-type systems while still allowing the hydraulic fracturing operation to stimulate one interval at a time.”
The pods’ reliability has allowed them to move into new applications, Robertson says. For example, they have been deployed to increase injection rates in saltwater disposal wells, including many where the operator tried rock salt but could not achieve adequate diversion.
“The results have been impressive,” Robertson enthuses. “The pods only plug a fraction of the wells’ flow paths, but that is enough to divert flow into new areas. In fact, the first trial opened so many new paths that the operator applied to increase the well’s maximum injection rate.”
Refrac Liners
Industry data shows that refracturing can provide a return on investment comparable to new wells by unlocking additional hydrocarbons and protecting parent wells from frac hits, says Mark Villarreal, Enventure Global Technology Inc.’s director of sales for the Western Hemisphere.
“Most people understand the value refracturing can provide and get excited when they look at or discuss it, but they often hesitate to pull the trigger,” he observes. “The issue is the perceived risk associated with preparing for the refrac using mechanical diversion, particulates or a combination of both.”
Expandable refracturing liners isolate existing perforations while providing the space needed for high pump rates. Enventure Global Technology says these pump rates unlock more effective and affordable refrac designs, including ones that employ extreme limited entry techniques to extend stage lengths and distribute flow more evenly across each cluster.
The actual risk has gone down significantly as service companies have gained experience with refrac proponents such as ConocoPhillips Co., Devon Energy Corp. and QEP Resources Inc., Villarreal points out. “Expandable refrac liners are a case in point,” he says. “To address the root causes of past issues, we have developed stronger connections and more reliable expansion assemblies.”
The company’s latest high-temperature refrac liner has 40 percent higher tensile strength than its predecessor and can endure temperatures exceeding 350 degrees. Even its standard model has 16 percent higher tensile strength and works in temperatures around 325 degrees, Villarreal mentions. He says these capabilities enable the liners to be deployed in every U.S. basin, including the Eagle Ford, where most refracturing occurs.
“As we designed the new connection, we subjected it to 120 heat, pressure and load cycles to simulate the stresses it would experience during a refrac,” Villarreal says. “Since we brought the connection and other changes to the field, the liners’ reliability has been well above 95 percent.”
Mechanical isolation systems can isolate old perforations completely to ensure the refrac stimulates new rock, says Tod Torgerson, Enventure Global Technology’s director of business development for refrac systems.
“In the world of mechanical isolation, expandable liners have the best economics,” he argues. “Cementing a scab liner in place costs less, but the expandable liner increases the space available inside the tubing. For a job with a base casing size of 5½ inches, the inner diameter is 40% higher.”
Preserving most of the original inner diameter allows the operator to perform a more effective refrac by using larger perforating guns and higher pump rates, Villarreal says. “In 5½-inch base casing, the extra space can boost the maximum pump rate from 65 bbl/m to 80 bbl/m. In some plays, such as the Eagle Ford, it is hard to generate enough hydraulic horsepower at 65 bbl/m to crack the rock, let alone perform an optimal frac.”
Across casing sizes and plays, expandable liners increase the pump rate by at least 10 bbl/m, Villarreal says.
To understand how much the higher rate can mean and help operators new to refracturing optimize their treatments, Enventure has partnered with an outside consultant that advocates extreme limited entry (XLE), a technique that reduces costs by allowing operators to increase the amount of clusters in each stage without sacrificing cluster efficiency. The technique works by using friction to compensate for variations in perforations’ entry pressure to distribute fluid more evenly across the cluster.
“Extreme limited entry perforating often is used in new well completions in part because it more efficiently distributes flow throughout each stage,” Villarreal says. “Combining XLE and expandables enables longer stages in refracs, through which we can deliver savings that exceed the extra cost of using expandable liners rather than cemented ones by at least three or four times.”
For other great articles about exploration, drilling, completions and production, subscribe to The American Oil & Gas Reporter and bookmark www.aogr.com.