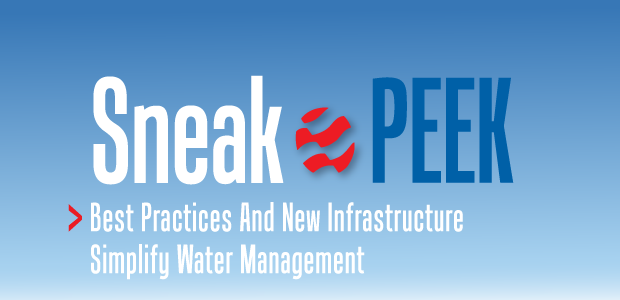
Water Management
Best Practices And New Infrastructure Simplify Water Management
By Colter Cookson
In the Permian Basin, Platts estimates, three barrels of water come up for every barrel of oil. The water-to-oil ratio is particularly high in the Delaware Basin, with a joint report by the Texas Alliance of Energy Producers and the Independent Petroleum Association of America observing that some wells there lift 10 barrels of water for every barrel of oil.
Even in the Midland Basin, where the ratio is closer to two to one, producers say managing water efficiently is critical.
“Water is the primary fluid we produce, so how we manage it has a tremendous effect on our operating expenses and ultimately our bottom line,” says Jay P. Still, president, chief executive officer and chairman of Guidon Energy, a portfolio company of Blackstone Energy Partners with 38,400 gross acres in the Midland Basin.
Guidon Energy’s recycling facilities use a four-pit process to prepare produced water for reuse. The initial pit allows oil to collect on the surface so it can be skimmed off. In the next pit, the water is treated with ozone to control contaminants such as bacteria and iron. Finally, the water moves to a large storage pit, where aeration preserves its quality. The remaining pit holds freshwater. Guidon says it adopted this approach because it is cost-effective and suitable for high produced water volumes.
Guidon reuses 60%-70% of its produced water in completions, Still reports. “Recycling is cost-effective and reduces our demand for freshwater, leaving more available for agriculture and other uses,” he says. “It is a win-win for the environment and the communities where we operate.”
For produced water to be reused, he describes, it must be treated and stored until a hydraulic fracturing treatment is under way, at which point it is transported to the job site, and re-treated to remove any problems that appeared during storage. It’s sometimes necessary to move water by truck, but Still points out that pipelines reduce costs and pose fewer safety and environmental risks.
“Until recently, Permian Basin operators could take care of their water by drilling a shallow disposal well near the tank battery. There was no need for integrated pipeline networks, so in many areas, it is not yet economic to move water long distances,” Still mentions.
But pipeline networks are expanding. “Most pipelines are owned and operated by producers, but during the past five years, the number of midstream service companies that focus specifically on water has boomed,” Still relates. “This is particularly true in the Delaware Basin, where wells tend to have higher water cuts and there are fewer shallow disposal wells.”
While he expresses appreciation for midstream companies’ economies of scale, Still says Guidon prefers to build its own infrastructure. “Water is central enough to our business that we want to control our own destiny,” he explains. “If we had to put a frac spread on standby because we were waiting on water or shut in a well because we could not find enough disposal capacity, the costs and lost revenue would add up quickly.”
Recycling Process
Drawing on 10 years of experience with water recycling, including time at Laredo and Pioneer, Guidon’s team has adopted an approach to recycling it describes as simple.
“At our recycling facilities, we have two 80,000 barrel pits that hold raw produced water,” says Chuck Pounds, the company’s manager for surface land and water. “While the water is in the first pit, we use a vacuum truck to skim the oil off the top. We leave the water there until the solids settle out.”
After that, Guidon uses a submersible pump to move the water to the second pit, where it is treated with ozone to control bacteria, iron and other constituents. “Ozone is one of the best bacteria killers and oxidizers available,” Pounds says. “We create it naturally using the corona method, which involves pulling ambient air across electricity, so we do not need to transport chemicals to the site.”
The pits are double-lined and equipped with leak detection, Pounds assures. He adds that the bottoms are sloped to force the precipitating solids to collect in the center, where a suction line keeps the solids from accumulating.
Once the water has been treated with ozone, it is pumped to a storage pit and held until it is needed for a completion. The 750,000 barrel storage pit has several aeration systems, venturi valves at the bottom that keep the water moving and suffuse it with oxygen microbubbles. “Oxygen is an oxidizer, so it helps control bacteria, and iron,” Pounds explains.
“We went with the ozone and aeration combo after looking at nine recycling technologies because it is simple and easy to scale,” he details.
In addition to maintaining the water’s quality, Pounds says aeration slows evaporation by replacing the warm water at the top of each pond with cold water. “The Midland Basin is hot enough in the summer that we can lose three inches of water to evaporation on a calm day and four or five inches on a windy day,” he reports.
Those fast evaporation rates can be a blessing when the water is too far from completion activity to be reused and Guidon wants an inexpensive way to reduce its disposal volumes, Still notes. He says that situation should become less common as pipeline networks interconnect.
“There are companies developing more efficient treatment technologies so we can afford to clean water enough it can be used on farms and in cities,” Still adds. “For example, a large manufacturer is working with Waterfield, another Blackstone company, to test a miniature desalination plant that should be far more economic than traditional designs if it is successful.”
Recycling’s Rise
Interest in recycling continues to grow, says Mark Patton, president of Hydrozonix. “Producers and midstream companies have gone from building facilities that can recycle 20,000 barrels a day to ones that can handle 40,000 or 60,000. We are even hearing talk of 100,000 bbl/d facilities,” he reports.
Patton says advances in automation and remote monitoring are improving plants’ efficiency. He cites the company’s experience operating plants for clients using a cloud-based dashboard that shows how much water is moving through the facility and tracks its location. The user can turn pumps on and off or open and close valves remotely, but Patton says the software automates routine tasks.
“With the dashboard, one of our operators went from needing a couple people at each recycling plant to running all four with one person,” Patton says. “We have gotten enough positive feedback on the software that we are beginning to market it independently of our other services.”
Disposal Constraints
In the short term, many recycling plants have shut down because of the slowdown in fracturing activity, a reality Patton says has strained disposal capacity in many areas.
To help producers minimize truck traffic and water disposal volumes in areas without recycling infrastructure, Hydrozonix reports it has developed an enclosed flare that uses produced water to scrub emissions. The heat generated by the gas combustion converts the water into steam and returns it to the hydrologic cycle.
“One of the operators we work with has 60,000 barrels of water coming out of the ground but only 40,000 bbl/d of disposal capacity. He could pay commercial disposal wells to take the water, but that would mean going over budget,” Patton relates. “Instead, the operator is storing the water to prepare for completions in August and September.”
Lengthy storage times may require more aggressive treatment regimens and extra aeration equipment, Patton cautions. When storage is not possible, he says operators are looking for ways to accelerate evaporation to lessen their disposal needs, a trend he predicts will continue even after hydraulic fracturing activity recovers.
“There always will be produced water in areas with limited disposal capacity or too few completions for recycling to make sense,” Patton suggests. “Evaporation lets operators reduce the amount of water they need to transport while improving their environmental profile by returning that water to the hydrologic cycle.”
To help address those situations, Hydrozonix has developed an evaporator designed to use gas that otherwise would be flared. “The gas is burned in an enclosed combustor. Because it maintains a consistent temperature, the combustor destroys 99.99% of the hydrocarbons that enter, far more than an open flare. In tests, this cuts particulate matter and sulfur oxide emissions in half.”
The combustor uses produced water to scrub the emissions, exposing it to heat and turning it into steam, Patton says. “That steam goes back into the water cycle today, but we are testing ways to use it for power generation or condense it into freshwater,” he reports.
The system is small enough it can be moved from site to site as produced water volumes change, Patton says. “We are targeting the Permian because that is where most of the industry’s produced water is, but the system also has drawn strong interest in the Marcellus, where volumes are much smaller, but disposal costs are high,” he comments.
Midstream Momentum
While many producers operate their own water pipelines and recycling facilities, the percentage run by midstream firms is growing, assesses H2O Midstream CEO Jim Summers.
“The water midstream model’s growth resembles that of natural gas pipelines, with producers gradually becoming more willing to let third parties handle their water,” Summers says. “In shale plays’ early days, it made sense for producers to build their own systems because high oil prices put a premium on speed to market. Today, we are seeing many producers divest those assets and dedicate new acreage to midstream firms.
By spreading the cost of water pipelines, recycling facilities and disposal wells across several producers’ volumes, H2O Midstream says midstream firms can invest in redundancies, automation equipment and other features that improve water infrastructure’s safety, efficiency and reliability.
“Midstream companies benefit from economies of scale,” Summers notes. “We are putting multiple producers on a single system, so we can build 16- or 20-inch pipe in areas where individual producers may only be able to justify 10-inch pipe.”
Automation is helping midstream firms maximize scale’s benefits. “On our system, which serves seven producers in Howard County, Tx., we have 15 disposal wells with varying capacities and operating costs. Automation lets us divert water to different wells as their costs change from day to day,” Summers illustrates.
“Automation also makes it much easier to adjust to demand spikes,” he continues. “When a well pad begins producing at 20,000-30,000 bbl/d, we can spread the water across multiple disposal wells to handle it without exceeding maximum allowable pressures. This helps us keep trucks off the road.”
Summers stresses that the midstream model will only continue to grow if water management companies maintain a strong track record. “We have to provide flow assurance,” he says. “The capital efficiency midstream firms provide will mean little to producers if partnering with us endangers their ability to frac new wells or move the water associated with their existing production.”
H2O Midstream’s system has 99.98% uptime, Summers says. “Our customers have only experienced a few hours of downtime since our inception in 2016, and that was from unusual weather,” he says. “We make the upfront investment in redundancy to ensure our system will stay reliable over the long term.”
As the water midstream industry matures and best practices evolve, Summers says well-built systems are becoming even more reliable and efficient. “We also are finding ways to reduce the risk of spills and the amount of emissions associated with our operations,” he adds.
Minimizing Costs
Controlling costs has become the top priority for many producers, observes Trace Hight, chief commercial officer of water infrastructure at Gravity. “Water companies only grow if their customers can drill at prevailing prices, so we are doing everything we can to help our customers source fresh or produced water efficiently and drive their gathering and disposal costs down,” he reports.
Supporting multiple phases of the water supply chain helps Gravity control costs while limiting producers’ capital exposure, Hight adds.
Gravity’s newly drilled Hull saltwater disposal well in Howard County, Tx., benefits from an upgraded wellbore design that allows it to inject 45,000 barrels a day of piped-in produced water at low pressures. Gravity says the well is part of a broader effort to reduce customers’ gathering and disposal costs.
Investment banks’ estimates put the breakeven price for Wolfcamp A and Lower Spraberry wells in Howard County around $35 a barrel, Hight notes. “Our goal is to help our customers get that price even lower by streamlining our systems and operations,” he says. “Our biggest variable costs are electricity and chemicals, so that is where we are focusing.”
To reduce labor costs, Hight says Gravity is automating more tasks and working with equipment vendors to improve communication capabilities and uptime.
“To keep our utility costs down, we are using more efficient pumps,” Hight continues. “We also are making the investment to construct larger pipeline systems all interconnected with maximum redundancy to our new deep Ellenberger disposal wells. These wells are designed with larger casing and tubing, which reduces friction and allows us to inject an extra 5,000, 10,000 or 15,000 bbl/d of water deep without significantly increasing pump pressure and therefore electricity costs.
“These improvements in our gathering and disposal system’s efficiency will help ensure our customers can safely and reliably dispose of large produced water volumes at the lowest possible lease operating expense,” he says.
For other great articles about exploration, drilling, completions and production, subscribe to The American Oil & Gas Reporter and bookmark www.aogr.com.