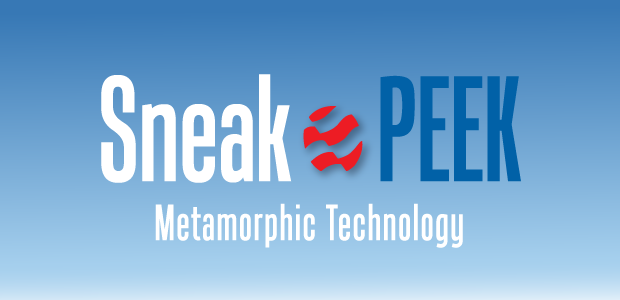
Disposal Constraints Drive Creative Research Into Water Treatment, Reuse
By Colter Cookson
On average, Permian Basin wells lift three or four barrels of water for every barrel of oil. For some wells, the ratio of water to oil is 12 to 1. Although produced water can be treated and used in hydraulic fracturing operations, the vast majority of it goes into saltwater disposal wells.
To decrease reliance on SWDs and provide much-needed water to arid regions, private companies, academic institutions and government organizations are investigating ways to treat and reuse produced water in applications outside the oil and gas industry, notes Mark Patton, president of Hydrozonix. He says it is vital to expand destinations for recycled water.
“Estimates for how much water we can reuse within oil and gas put it somewhere between a third and a half,” he says. “That percentage should go up as produced water pipeline networks grow and technology improves, but the industry still needs outlets for produced water that do not depend on completion activity.”
From 2010 to 2022, B3 Insight estimates that the amount of water injected into Permian Basin SWDs increased sixfold, from 900 million barrels in 2010 to more than 5 billion barrels in 2022. Amid concerns that such injection may induce seismic activity under specific conditions, regulators and operators are restricting injection in a few areas. This has reduced the amount of disposal capacity available and increased transportation costs to reach the remaining capacity.
In the short term, Patton predicts the most economic option will be drilling disposal wells outside seismic response areas and transporting water to them. “If disposal capacity falls in one area, pipelines can divert water to wells with spare capacity,” he describes. “I have even seen people talk about drilling disposal wells in the Central Basin as overflow capacity. There is less activity there than in the Midland and Delaware, so induced seismicity is unlikely to become a concern.”
Because evaporation shrinks the amount of water that needs to be injected, Patton says he detects strong interest in technologies that increase evaporation rates. One of the most intuitive and time-tested approaches involves spraying water from produced water ponds into the air as droplets to increase the surface area exposed to the sun’s heat. He cautions that this technique needs to be deployed carefully because wind can carry any salt the droplets contain onto nearby fields, where it can accumulate and eventually harm crops or vegetation.
Spraying produced water into the air speeds evaporation, but it can allow wind to carry salt outside the pond. To prevent that, Hydrozonix says it has developed smart sprayers that constantly calculate how far salt can go and only turn on when conditions are safe.
“Hydrozonix has modeled how much spray drifts and come up with a smart system that only turns the sprayer on when it can do so without spreading salt,” Patton says. “That only happens when the area has low wind speeds, and natural evaporation still needs high temperatures and relatively low humidity to occur quickly, so it only has a significant effect on water volumes for a few months a year.”
Thermal evaporators that generate internal heat can turn water into vapor throughout the year, but Patton says they generally require too much power to be economic. “We are working with a few operators to extend the period when natural evaporation makes sense,” he shares. “We also are looking at a new technology that may make evaporation much cheaper and act as the first stage in a process for desalinating the water.”
Desalination is exciting because it may allow produced water reuse outside the oil and gas industry, he considers. In industrial applications, the water can assist cooling towers, heat exchangers and scrubbers. Eventually, Patton says treated water may irrigate crops and recharge aquifers.
Enabling Reuse
Patton points out that several companies are seeking or developing low-cost technologies to desalinate produced water. “There is a big joint project between ExxonMobil, Chevron, ConocoPhillips and ARIS Water Solutions where they are evaluating three desalination systems, and almost every major oil company already has done at least one desalination trial,” Patton relates. “We still have a lot to learn, but I do not think developing technology will be the hard part.”
Instead, he suggests, the key will be developing regulatory and legislative frameworks that allow treated produced water to be repurposed, as well as markets that incentivize reuse. He says Australia shows how effective such markets can be. “Like Texas, Australia has areas that are arid and dry, as well as ones with plentiful water,” Patton says. “To help water move where it’s needed, Australia allows the markets to buy and sell water usage rights. In many areas, the value of water is high enough that developers can justify building pipelines to import it.
“In the Permian Basin, a similar market may justify not only moving water, but also desalinating produced water to a point that it can be used for groundwater recharge,” he envisions.
To be accepted by the public, recharging aquifers with produced water will require strict treatment standards that likely exceed the ones for drinking water. Once it’s treated, the water can be put in unlined ponds that allow it to percolate into subsurface reservoirs, much as rainwater does. Patton says this approach mirrors the one that many municipalities in the United States and abroad already use to recharge aquifers with wastewater from homes and businesses.
Given the extent of Texas’ and New Mexico’s arid areas, Patton says regulators and legislators in both states support broader recycling. In 2019, New Mexico State University partnered with the New Mexico Environmental Department to establish the New Mexico Produced Water Research Consortium, which describes its mission as “advancing scientific and technological solutions related to the treatment and reuse of produced water.” Texas has a similar organization in the Texas Produced Water Consortium administered by Texas Tech University. Both states continue to dedicate funds to research efforts.
Private firms from outside the industry also may help support broader reuse, Patton assesses. “Pepsi and Microsoft have committed to becoming net water positive, meaning they plan to replace any water they consume in their processes by developing new water sources,” he relates. “Cleaning up contaminated groundwater will be part of source development, but the biggest opportunity to make an impact on water supplies is in oil and gas. We generate so much water, and we have the technology to clean it.”
Data Collection
As produced water reuse expands and that water transforms from a waste stream into a product, Patton predicts the testing performed on produced water streams will become more robust. “Today, we worry about hydrogen sulfide for safety reasons and bacteria and iron because of the operational problems they can cause. Testing happens regularly, but it is rarely reported in real time,” he describes. “For reuse, we will need to look at a wider variety of characteristics, collect samples more frequently, and put the data into real-time dashboards that make it actionable.”
Regulatory changes also may expand the need for testing, Patton says. “Last year, New Mexico enacted a regulation requiring operators to monitor volatile organic compound emissions at many facilities, including ones that process produced water. These regulations require facilities to show a 25% reduction in those emissions next year,” he illustrates.
New Mexico’s VOC regulation is motivated partly by some counties’ status as nonattainment zones for ozone. Noting that the Texas side of the Permian Basin has been on the U.S. Environmental Protection Agency’s list of potential Clean Air Act nonattainment zones, Patton says similar regulations may appear elsewhere. He adds that EPA’s proposed methane tax includes emissions from methane dissolved in produced water.
To deal with VOCs and methane, Patton recommends treating produced water with ozone, an aggressive oxidant that many treatment facilities already employ to prepare produced water for reuse in completions. “Ozone is not selective, so it will try to oxidize anything it comes into contact with, including VOCs,” he explains. “To figure out how effective it is at addressing VOCs, we did testing at facilities in New Mexico and found that it reduces VOCs 26%-50%.”
For now, New Mexico’s rule only targets a 25% reduction. “Ozone can do the job as part of the normal recycling process,” Patton assures.
In situations where existing ozone generation cannot remove all the VOCs, the ozone can be mixed with hydrogen peroxide to increase its oxidation capacity. “When we do that, we have seen 90% removal,” Patton reports. “Adding hydrogen peroxide increases costs slightly, but the amount needed is so small that it is less expensive than putting in a bigger ozone system.”
Multistep Treatment
Recycling produced water will be critical to mitigating water scarcity in the Permian Basin, says George Nnanna, who heads the Texas Water and Energy Institute at the University of Texas Permian Basin and serves as technical committee co-chair for 2024 at the Produced Water Society. “Given our location, we are looking at produced water as a new source of water for both agriculture and industrial applications,” he relates. “This will free freshwater to be used in other sectors.”
Before reusing produced water in many applications, its salt content will need to be removed. “In the Permian, produced water often has 200,000 milligrams per liter of dissolved salt,” Nnanna notes.
Whether the goal is to remove total dissolved solids or address other contaminants, Nnanna says treatment often requires a range of technologies. “We may begin by using dissolved air flotation to remove some of the contaminants. That can be followed by screening, as well as coagulation and flocculation. Alternately, we may use thermal distillation to turn some of the water into a clean vapor that we can condense and collect.”
Membrane and thermal distillation require significant energy consumption, Nnanna warns. “Membrane distillation processes use energy to pump water through screens at high pressures, and thermal distillation processes need some form of heat,” he explains. “The energy consumption is high enough that energy costs are one of the major barriers to beneficial reuse.”
The heat that drives evaporation can come from the sun, but natural evaporation occurs too slowly to keep pace with produced water volumes, he observes. “To increase the evaporation rate, TWEI is testing a photothermal membrane that floats on a top of produced water ponds, concentrates solar energy, and brings water into contact with that solar energy,” Nnanna reports. “Based on lab tests, we think the membrane will accelerate evaporation by 23%.”
Membrane Marvel
According to Nnanna, the photothermal membrane works by collecting sunlight rather than allowing it to disperse in the pond. Through capillary force, water migrates from the pond’s surface to the top of the membrane, where it wets the heated surface and evaporates. This process repeats continuously, he describes.
“The membrane’s thickness affects how well it accelerates evaporation,” he mentions. “If the membrane is too thin, the solar energy will pass through it and heat the produced water in the pond instead of concentrating on the surface. But if the membrane is too thick, it will inhibit the capillary force and prevent water from reaching the evaporation surface.”
Salt also can restrict water’s access to the surface, Nnanna notes. “To address salt blockages, we have designed channels through the membrane that allow water to dissolve the salt back into the pond,” he says.
The photothermal membrane is made from a commercially available material. “We modify the surface using nanosized particles to allow it to float and to support evaporation,” Nnanna describes. “We also create the hydrodynamic channels that allow water to dissolve salts, but these changes are simple enough that the cost of producing and deploying the membranes should be low.”
As of early February, the membrane’s effectiveness has been validated in the lab. “We still need to do pilot scale testing to move to a stage where it can be commercialized,” Nnanna notes. “We are talking to a couple companies to set up those tests.”
As with any natural evaporation system, the photothermal membrane will work best during the summer. However, Nnanna says it can promote evaporation at lower ambient temperatures. “Even at 85 degrees Fahrenheit, the evaporation is much faster than it would be without the photothermal membrane,” he reports. “Once we deploy the membrane outside, it will be interesting to see how wind speed and dust influence the evaporation process.”
Although he expresses excitement about the solar concentrator, Nnanna stresses that the industry must embrace a variety of approaches to produced water management. He points out that UTPB is a member of the Permian Energy Development Lab, a two-state coalition launched by the Cynthia and George Mitchell Foundation to promote innovation in several areas, including water treatment, use and conservation.
“For thermal distillation, there may be an opportunity to utilize waste heat from power generation,” Nnanna says. “Many plants produce electricity by sending steam from a boiler to a turbine. At the turbine’s exhaust, the steam is still 97% vapor. Normally, that vapor goes into a condenser, and the heat is wasted to the surroundings or the environment.
“With the right piping infrastructure, we may be able to move produced water to power plants in order to take advantage of the enormous heat that goes into the condenser to distill the water,” he envisions. “That should significantly reduce costs.”
Leveraging Waste Heat
In areas with limited disposal capacity, evaporation can help operators manage costs by reducing the water volume that needs to be hauled off and injected down hole, notes Michael Grossman, senior director of business development engineering at Heartland Water Technology and 2024 technical committee co-chair for the Produced Water Society. Of course, he observes, evaporation requires heat.
Using the hot exhaust from compressors to evaporate produced water can cut the volume that needs to be managed and therefore the costs associated with transporting water to saltwater disposal wells. According to Heartland Water Technology, this technique can offer compelling economics in areas with limited disposal capacity and few water pipelines, such as the Marcellus.
“The need to generate or harness thermal energy is one of the biggest contributors to evaporation costs,” Grossman says. “In some applications, it’s worth the cost to get that heat by combusting gas or other fuels. However, it’s more affordable and environmentally friendly to use waste heat from combustion that needs to take place regardless.”
In the oil and gas industry, such waste heat usually comes from compressor banks or flared field gas. “At compressor stations, the compressors’ engines spit out exhaust that can reach 800 degrees F,” Grossman says. “By using ducts and a fan-induced vacuum to pull that exhaust into a direct contact evaporation system, we can repurpose its heat for evaporation.”
The system uses a proprietary contact chamber to mix the exhaust with produced water and transfer heat to it, Grossman describes. The chamber works so well that in the space of only a few feet, exhaust can go from 800 degrees F to 150. Meanwhile, much of the water evaporates and returns to the hydrologic cycle as clean water vapor, where it has the potential to water crops and recharge aquifers.
How much water evaporates will vary from application to application, Grossman notes. “The key is what the customer plans to do with the solids the water vapor leaves behind,” he says. “Some customers, especially in other industries, like to achieve zero liquid discharge, meaning they dry all the solids in the water into salt and haul it away.
“Most operators stop short of full evaporation because it’s much easier to transport and dispose of the solids if they remain in a liquid matrix,” Grossman continues. “In these cases, the goal is to concentrate the solids into a smaller volume of liquid.”
The volume reduction varies according to several factors, but Grossman says lighter waters with fewer solids generally shrink more. “In the Permian, we can evaporate about 50% of a typical produced water stream before solids start precipitating out,” Grossman illustrates. “In the Eagle Ford, we can eliminate 80%-90% of the water. In the Marcellus, where water density varies widely, we target anywhere from 30% to 60%.”
The Marcellus hosts most of Heartland’s commercial deployments within oil and gas. “In places with nearby disposal wells and ample capacity, such as the Permian, evaporation tends to be more expensive than disposal, even when the thermal energy comes from exhaust,” he explains. “However, in areas where disposal is costly, evaporation can be competitive or more affordable.”
In the Marcellus’ case, water often needs to be hauled long distances to reach a disposal well, Grossman notes. “The biggest factor is the local geology, which rarely supports SWDs,” he says. “Also, drilling activity takes place in more populated areas where building water pipelines is impractical. Both trucking and disposal costs tend to be high, and that makes it attractive to shrink the volumes that need to be transported.”
Heartland’s largest direct contact evaporators handle several thousand barrels a day using exhaust from compressors on users’ sites, Grossman reports. He says the company is talking with operators in the Northeast to secure commitments for a larger, centralized evaporation facility.
In addition to leveraging heat from compressors, the evaporators can tap engines or turbines. According to Grossman, that is less common in oil and gas than it is in Heartland’s other markets, which include power plants, mines’ evaporation ponds and landfill leachate.
Noting that one user called the evaporators “case studies in simplicity,” Grossman says they are reliable. “We generally maintain 95% uptime,” he details. “There are only two major moving pieces: a fan that pulls exhaust into the system and helps vapor get out, and a pump for moving liquid into and out of the system.”
The fan draws in exhaust by creating a mild vacuum. It does not put any backpressure on compressors or other equipment, Grossman assures.
“In most produced water applications, the evaporator performs well without any need for chemicals or pretreatment,” he says. “We use automation to manage the valves, so outside of periodically cleaning and occasionally checking on the evaporator, it runs unattended.”
Managing Energy Costs
Energy costs are rising thanks to growing demand, lingering supply chain disruptions and general inflation, assesses Kevin Overton, regional sales director for Ndustrial. “In the Permian Basin alone, S&P Global Platts estimates that by 2032, utilities will need to expand capacity from 4.2 gigawatts to 17.2,” Overton reports. “In other words, capacity has to increase 400% to meet demand.”
The projected demand comes in part from operators’ desire to reduce emissions by electrifying compressors and other equipment, Overton observes. He says operators can mitigate energy costs by shedding load during periods of high demand, when prices tend to be higher.
“To dance with the grid, companies need to know when the high-cost times occur,” Overton says. “For Texas, Ndustrial’s software can predict Four Coincident Peak (4CP) days up to a week in advance, and help companies avoid real-time price spikes. It can overlay this information with a company’s historic demand, cost structure and present demand to help users decide how much load to shed.”
Reducing electricity consumption when costs are high can help saltwater disposal well operators and oil and gas producers save money. Citing early work in oil and gas and its experience in other industries, including the one from which the graph to the left originates, Ndustrial says the savings can be significant.
While every utility uses a different pricing structure, time of use almost always influences costs. Overton says this is especially true in California, where he says he has seen costs go from $0.08 a kilowatt hour to $27 a kWh in a single day. He adds that many utilities have demand response programs through which they try to anticipate periods of high demand and pay users to reduce consumption.
“When our software notices a sharp increase in the price of energy, or when a demand response call comes in, we can send a text or email to a vice president of operations, production manager, or other person with the knowledge to decide how the company should respond,” Overton says. “For example, at an SWD site, the manager may look at the tank levels to see whether it makes sense to stop pumping. If the water tanks are low and only one or two pumps are active, there may be an opportunity to shift injection to a lower-cost time of day. But if the tanks are almost full and there is any risk of them overflowing, pumping will continue.”
In addition to reducing unnecessary energy use during high-cost times, Overton says Ndustrial’s platform can help companies optimize energy efficiency. “On an SWD site, we want to minimize the amount of energy for every barrel of water injected. We look at analytics from the pump and variable frequency drive to find the sweet spot where the pump’s head pressure is high enough to inject at an appropriate rate but the VFD is using energy efficiently,” he illustrates.
While the resulting efficiency gains may deliver only minor savings, Overton says they can add up quickly. “For most of our clients, the goal is to save 2%-3% a year on energy,” he says.
Ndustrial began in the cold food distribution business, where it has more than 400 client sites under monitoring. Other segments the company serves include oil and gas, manufacturing, forest products and cryptocurrency mining, Overton describes.
“We can help SWDs calculate the Scope II emissions associated with their power consumption,” he says. “To do that, we look at the types of power going into the grid at a given time, which is called the grid mix. The mix can shift substantially from hour to hour, especially in Texas or other states that have invested in wind and solar.”
To account for those shifts, Ndustrial updates the mix for each zip code every hour, Overton reports.
“Oil and gas producers are beginning to use our software as well,” Overton says. “Like SWDs, they should be able to save money through power optimization while demonstrating their commitment to environmental responsibility.”
For other great articles about exploration, drilling, completions and production, subscribe to The American Oil & Gas Reporter and bookmark www.aogr.com.