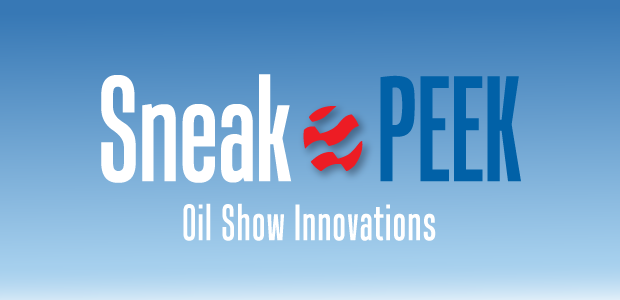
Industry Perspectives: PBIOS Oil Show Innovations To Please
By Larry Richards
Early in my 35-year career, most of the leading innovations in our industry occurred in the offshore or international arena. I spent my first decade chasing large equipment contracts in the United Kingdom and Norwegian sectors of the North Sea, deepwater projects in the Gulf of Mexico and Brazil, and various national oil companies with large budgets and even larger engineering teams.
The good Lord chose to put oil under some of the ugliest, most inhospitable places around the globe, and I have been in the field in almost every oil producing nation it is legal for a U.S. citizen to travel, and every producing state except Alaska. I am a student of history, and I love to see how different teams and cultures approach the intense problem solving and technical challenges so critical to our industry.
That is one of the key reasons I love West Texas. In the past two decades, the tides have shifted, and we have seen most of the leading innovations that have changed our industry originate in the onshore oil fields of the Permian Basin. My 25 years in this region suggest that has not happened by accident.
My friends and family were not surprised when I moved my family from Houston to Midland in 1997. After all, most oil company personnel have to “do their stint” in West Texas, and I was making the move to run a small company that Continental Emsco had acquired at my recommendation. But most are surprised I chose to spend the next 25 years in Midland.
For people who love innovation, technology and competition, the reason is clear. In most parts of the U.S. oil industry, and even more so internationally, change happens slowly. Oil company personnel are extremely reluctant to try new things, much less new techniques or equipment. In many larger companies, one major failure can be a career-ending decision.
I have found the exact opposite to be true in the Permian Basin. Careers and companies are made by taking chances, trying new ideas, failing and continuing to try again until you hit pay dirt. Over the past 20 years, most of the top selling products at my Permian-based businesses literally did not exist as an option for that application two years before. We would launch three or four research and development projects each year. The majority failed, but the ones that succeeded often became our top-selling technologies the following year.
What was amazing was the willingness of oil and gas companies to allow us to work with them to try new technologies at their locations. While part of that trust was earned, another part was rooted in the region’s culture. The constant level of customer communication and collaboration, risk taking and innovation made our company and products better, and helped the industry with better solutions. Similar cultures may exist in other parts of the world, but that has not always been my experience.
The Permian’s Power
The Permian region couples a raw entrepreneurial spirit with a uniquely intense work ethic, focusing companies on results rather than the process of achieving them. While safety is paramount, everything else is subject to experimentation. Real, hands-on problem solving is required every morning and afternoon. The field conditions are brutal, with temperatures ranging from -16 degrees F in winter to 116 degrees F in the summer. The distances are long; reaching many locations takes two or three hours of windshield time, half of which may be on a caliche ranch road.
Add in sandstorms, hailstorms, truck traffic, rattlesnakes and both customers and competitors trying to hire your field team every time they show up on location, and you have a taste of a hyper-competitive and tough business environment. While not for the timid, there is no better environment to constantly learn, create, evolve and improve.
This innovation is seen in the region’s producers, service companies, engineering firms and manufacturers. A perfect example is Midland-based Henry Petroleum trying its first slickwater fracturing treatment in 2003, pioneering a combination of new horizontal drilling and fracturing techniques at the same time. The small independent transformed our industry and our nation’s reserves profile. Using its new technique, Henry managed to bring in huge wells from worn-out old fields that my father considered depleted during his stint in the Permian for Getty Oil in the 1960s.
Today, the power of slickwater fracs is obvious. But in 2003, looking at impermeable rock and thinking, “This is no problem; we’ll turn it into a productive reservoir by drilling horizontally for a mile or two and injecting a football field worth of sand” took vision and guts. To see how an independent oil company thinks and acts, read The Wolfberry Chronicle by Henry Oil Geologist Gregory Berkhouse. It tells the story in wonderful detail, including in-depth explanations of the technologies, geology and terminology needed to understand modern Permian plays.
Every country around the globe is searching for similar tight shale formations to exploit using Henry’s novel approach, and the challenges that stem from these wells have spawned the next generation of equipment and services to complete and produce these beasts.
Takeaway Capacity
Highly-productive wells require takeaway capacity. The sooner that capacity can be built, the easier it is to meet demand.
That is where Odessa-based Saulsbury Industries comes in. In true Permian fashion, the firm specializes in completing projects quickly and safely. Started by entrepreneur Dick Saulsbury in the 1960s, the family-owned business has evolved into one of the largest, most respected engineering, procurement and construction firms in the country. Today, it boasts more than 5,000 employees, who are redefining state-of-the-art in facilities across the Permian and the United States.
Besides that, the members of the Saulsbury family are fine people. Their character and work ethic shows in the people they hire and the amazing company they have built.
As the industry focuses on minimizing emissions and flaring, Permian companies are helping lead the way. For example, Warren Cat is converting the industry’s ‘big iron’ from diesel to natural gas, which dramatically reduces emissions and utilizes natural gas produced in the basin.
This Caterpillar 3512E dynamic gas blending engine mixes natural gas with diesel, allowing hydraulic fracturing fleets to get the job done with lower fuel costs and emissions. It is one of many products distributed by Warren Cat to help companies in Texas and Oklahoma operate more efficiently.
Because natural gas has less energy density than diesel, it can be challenging to deliver the power frac pumps require using natural gas. But thanks to smart engineering, Caterpillar’s new 3512E DGB can achieve full power load with 80% natural gas and only 20% diesel. For a typical frac spread with 18-26 pumps, each with a whopping 2,500 horsepower, the reduction in fuel costs and emissions adds up quickly.
In areas where new, fully electric frac units are utilized, they often struggle with the lack of clean, reliable power from the grid. After all, a single job can draw 30 megawatts from the line. Even when electric power is available, remote locations often suffer from “dirty power” or power surges that can damage sophisticated electronic equipment. The Caterpillar G3520 generator produces 2,500 horsepower fueled by natural gas. In the Permian, where stranded gas can be a real issue, these technologies are a true win-win for both industry and the environment.
Limiting Flash Gas
Another great example is the new technology introduced by Bold Production Services with its large fleet of trailer-mounted production coolers, OneSkid dehydration packages and OneSkid hydrogen sulfide removal technologies. While I built a nice business capturing tank batteries’ methane emissions, my favorite technologies are ones that keep emissions from being produced in the first place. Permian operators use Bold’s large electric drive cooler fleet to reduce the temperature of their oil well effluent, resulting in less flash gas from their oil production before it goes into storage tanks.
Gas lift engineers are using OneSkid dehydration packages from Bold Production Services to keep their gas dry. This extends pipe and valve life by slowing corrosion.
By keeping oil temperature below 120 degrees F, one of Bold’s larger Permian customers has significantly reduced the flash gas volume that needs to be managed and sustained yields as great as 3% of additional oil production a day.
The wells also have high volumes of produced water, so the operator uses Bold’s coolers to drop the water temperature below 130 degrees F, allowing the water to be transported with affordable poly-pipe. This approach keeps vacuum trucks off the road and enables cost-effective produced water recycling. The trailer-mounted electric coolers often replace engine drive units, dramatically reducing nitrous oxide emissions and the customer’s carbon footprint.
In the past, companies had to flare gas for days or weeks at a time when cleaning out or completing preventative maintenance programs on hydrogen sulfide treating equipment. Bold has eliminated flaring during these operations by designing a trailer-mounted “Flex Unit” that allows operators to continue selling gas throughout the cleanout process, general maintenance, mechanical upsets or times where new production has outpaced existing infrastructure.
The company’s technology also can improve the efficiency and reliability of gas lift. With Automated OneSkid dehydration packages, operators can preserve gas lift’s strong economics by preventing wet gas from corroding surface pipelines or downhole valves. The dehydrators also have proven to increase gas compressors’ run time and availability by drying the fuel gas.
Automated Chokes
A final example is one I believe will be the most significant a decade from now. Our industry historically has asked field personnel to maximize oil production from every well, every day, while working safely and controlling costs. Many oil formations were viewed almost like a river—if the operator did not pull the oil from a well today, the company on the next lease could produce it next month.
Today, the industry has an opportunity to take a longer view. Since the hydraulically-induced fracture networks in unconventional plays are surrounded by impermeable rock, the oil and gas in the reservoir is likely to stay in place until the operator is ready to retrieve it. Instead of producing as much as possible, the operator can limit production to account for bottlenecks at surface that limit takeaway capacity (such as the natural gas line or the produced water line).
Automated wellhead chokes from VanZandt Eagle can give operators more precise control over wells’ production rates. In addition to improving output during normal operations, the chokes help fields adapt to compressor outages or other unexpected capacity constraints, which minimizes lost production and frequently eliminates the need to flare.
VanZandt Controls in Odessa (now VanZandt Eagle) has led the industry with several novel innovations, from some of the industry’s first automated field air compressor packages to automated wellhead emergency shutdown devices. The founder, Lance VanZandt, was named West Texas entrepreneur of the year in 2017.
One of the company’s latest innovations is an automated wellhead choke that can be tied into an overall control philosophy and algorithms for a field, eliminating flaring completely if necessary. The concept is simple. If a gas plant or compressor boosting station downstream of the field loses 30% of its capacity, the system can sense the increased pressures in the gas line and begin slowly choking back all producing wells until production going into the separators matches the gas line’s takeaway capacity.
Rather than manually shutting down one or more wells, operators can use smart systems to slowly choke back all the wells simultaneously across the field. This restraint may cost production in the short term, but it maximizes total hydrocarbons production from the well over the long term while eliminating flaring and venting across the field.
VanZandt Eagle has helped many operators under flaring restrictions utilize this technology very effectively. During normal operations, the automated choke can keep the choke on the well’s natural production curve far more precisely than a manual choke, which can only be adjusted periodically in steps. The resulting increase in production appears to largely offset any quarterly production losses from choking back to eliminate flaring.
The few technologies I have outlined are but a tiny fraction of an industry in perpetual motion. Whether their goal is to streamline the logistics of site preparations, manage the rough and tough of drilling and completion operations, or make production and processing go as smoothly as possible, smart men and women throughout the industry carve out the time to learn about new technologies or processes. They are busy, but they know that adopting the right tools and techniques can lead to huge gains in safety, efficiency and reliability.
I am fortunate to have been blessed with some wonderful mentors and industry friends, and to have a family that has been behind me through the highs and lows that are part of life for anyone who has spent as much time as I have in the industry. I am proud of our industry, and the positive impact our hard work has on so many lives around the world. I am also honored to serve as president of the 2023 Permian Basin International Oil Show, which will take place Oct. 17-19 in Odessa, Tx.
I sincerely encourage everyone who wants to get ahead in the oil and gas industry to spend time with more than 700 exhibitors and thousands of attendees who work tirelessly to improve every aspect of industry operations. Plan to be at the oil show, where innovation and technology meet Permian grit!
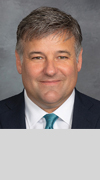
LARRY RICHARDS is the president of the 2023 Permian Basin International Oil Show. Before retiring in 2022, he served as chief executive officer of two successful Permian companies, Hy-Bon Engineering and VanZandt Controls, and held senior executive roles at Key Energy and Continental Emsco. Throughout his career, Richards has served as a contributing editor to The American Oil & Gas Reporter and mentored educators, students and field engineers. Richards was a lead technology presenter for the Natural Gas STAR Program, Methane to Markets and the Global Methane Initiative; served for more than a decade on the boards for the Permian Basin Petroleum Association and Casa de Amigos, a community center in Midland; and chaired the West Texas District Export Council.
For other great articles about exploration, drilling, completions and production, subscribe to The American Oil & Gas Reporter and bookmark www.aogr.com.