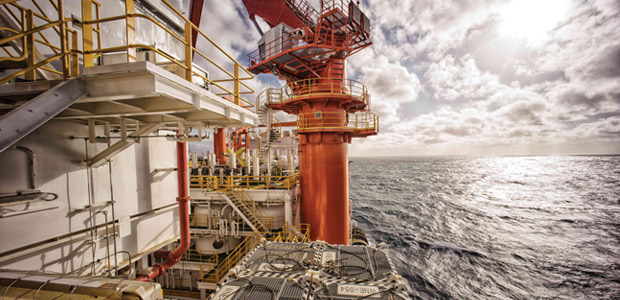
Completion Case Study
Modified LWC Proppant Improves Performance Of Deepwater Frac Pack
By Erik Hoffpauir, Naima Bestaoui-Spurr, David Stanley, Marty Usie, Hanh Nguyen, and Vanessa Williams
HOUSTON–Frac pack completions combine the stimulation advantages of hydraulic fracturing with sand control. Often used in the Gulf of Mexico, a successful frac pack completion maximizes conductivity from the formation to the wellbore by providing a short, wide fracture that bypasses near-wellbore skin damage. A highly conductive proppant pack placed from the tip of the fracture to the wellbore allows hydrocarbons to migrate from the formation while controlling sand production by maintaining formation stability and bridging sand directly in the reservoir, rather than allowing it to reach the wellbore.
Advanced fluid systems and breakers constantly are being developed to improve flowback recovery and make frac pack completions as efficient as possible, increasing ultimate hydrocarbon recovery. Methods to reduce capillary pressure forces also are being used to improve sand pack drainage.
Proppant pack permeability is the primary factor impacting frac pack well productivity. In frac pack operations, a viscous fluid is used to break the formation and transport the proppant. After treatment, the viscosity of the fluid must break completely and flow back to the surface. If the fluids do not break efficiently, they can leave gel residue in the propped fractures and proppant pack, impairing production. If left in the fracture, the fluids concentrate in the proppant pack and leak into the porous formation, decreasing permeability and conductivity.
Typical additives in a fracturing treatment include some type of surfactant to reduce surface tension and maximize load water recovery. However, surfactants have limitations. While they alter interfacial surface tension on both sand grains and the formation face, the effect is temporary and they can plate off quickly, treating only a portion of the sand pack. Surface wettability changes through time still may lead to water blocking within the proppant pack, hurting the overall conductivity.
Permanently modifying the proppant surface can improve proppant pack conductivity and speed well cleanup. The major causes identified with conductivity loss in the proppant pack include proppant flowback, fines and gel damage. Resin coating increases conductivity by decreasing proppant flowback and reducing polymer damage inside the pack. Other methods use superhydrophobic chemicals to directly treat proppant surfaces or as additives in the stimulation fluid treatment while proppant is pumped. These additives have shown the biggest benefit in immobilizing fines.
Coatings or surface modifiers of super-hydrophobic nature have decreased well cleanup time and improved conductivity, but they have not been proven to assist in overall fluid flow of both oil and water in the proppant pack leading to optimized dual-phase flow. This mechanism is necessary to optimally decrease capillary forces and ensure that neither oil nor water gets trapped in the pack and degrades overall permeability and conductivity.
If the stimulation fluid and produced water do not attach to the surface of the proppant, cleaning is easier, minimizing damage within the pack. Furthermore, if the surface is oleophobic, hydrocarbons will not attach to the surface and will move more easily. In such a case, the capillary pressure is null for both water- and hydrocarbon-based fluids, keeping the pores wide open for flow. Using a proppant that is simultaneously hydrophobic and oleophobic will assist not only in stimulation fluid load water recovery, but also potentially positively impact hydrocarbon flow.
Deepwater Application
A neutral wet lightweight ceramic (LWC) proppant with a 30/50-mesh particle size distribution was used in a frac pack completion in the Gulf of Mexico. This well had very low bottom-hole pressure, low reservoir energy, and was not using gas lift. The goal of treating with the neutral wettability proppant was to eliminate capillary pressure within the proppant pack and reduce the effective pressure necessary to flow the well.
The assumption was that since conventional proppant is water-wet, it would capture some amount of fracturing fluid on its surface. The corresponding pore spaces then would be occupied with the viscous fluid, thereby slowing fluid flow and affecting relative permeability. Because of the high affinity between the fluid and the proppant surfaces, more time is required to recover the majority of the stimulation fluids pumped into the well. Permanently surface-modifying the proppant to a neutral wettability state decreases the intermolecular forces between the surfaces and the fluid, leading to an easier flow.
The proppant used in the completion was evaluated in the laboratory for compatibility with the fracturing fluid and for its cleanup properties through the proppant pack. When applied in the frac pack operation, stimulation flowback data and first oil recovery data were recorded.
Early results indicate that the new proppant surfaces not only reduce water saturation, but also improve oil mobility. These observations show promise for permanently modifying surfaces as “next-generation” products for improving flow and decreasing the risk of formation damage caused by fracturing fluids left behind after treatment. When the proppant was applied in the Gulf frac pack completion, flowback was efficient, with rapid recovery of all pumped fluids.
In this case, the initial results indicate that the proppant surface reduced the intramolecular forces between the proppant and the fracturing fluid, eliminating capillary pressure within the frac pack and leading to more efficient and quicker fracturing fluid flowback compared with native state proppant. Moreover, first oil breakthrough occurred earlier than on other wells in the same area.
Neutral Wettability Proppant
Wettability describes a solid’s preference to be in contact with one fluid rather than another. A drop of a preferentially wetting fluid will displace another fluid, and at the extreme, will spread over an entire surface. Conversely, if a nonwetting fluid is deposited onto the surface, it will bead, minimizing its contact with the solid. In the case of a wetting state, the interactive forces between the surface and fluid are stronger than the cohesive forces within the fluid. In the case of nonwetting behavior, the cohesive forces within the fluid exceed the solid surface’s adhesive forces, prompting the fluid to bead.
In a porous media (such as a rock reservoir or a proppant pack) and in the presence of two immiscible fluids (e.g., oil and water), wettability plays a major role in fluid flow. When two immiscible fluids come in contact, they generate a clear interface between them that arises from interfacial tension. The interface is a curved surface and the pressure on the concave side exceeds that on the convex side, a difference defined as capillary pressure. In general, one of the phases is fully wetting to the capillary, while the other is a nonwetting phase. Capillary pressure then governs the distribution of the fluids.
Surface-modifying the capillaries to make them prefer neither of the two immiscible phases (meaning they are phobic to both phases) suppresses the capillary pressure. Under flow, the inner pore surfaces will not retain the fluids. Altering the proppant surfaces to a neutral wet state will decrease the intramolecular forces between fluid and proppant surfaces and potentially improve flow.
The LWC proppant was mixed thoroughly with the wettability surface modifier and then dried. During the drying step, the anchoring group from the modifier reacted with the proppant surfaces and became covalently bonded to the surface.
Figure 1 shows optical images of the neutral wettability 30/50-mesh LWC proppant obtained using a high-performance digital camera. Because it is a surface modification that requires very little chemical to treat the surface, the features of the proppant and particle size distribution do not change. The properties of the neutral wettability LWC were determined according to ISO 13503-2 for proppants used in hydraulic fracturing and gravel-packing operations. The sieve analysis showed that 92.7 percent of the particles were within the nominal sieves (-30/+50), while the apparent density was 2.69 grams per cubic centimeter (the same median diameter and particle size distribution as untreated 30/50-mesh LWC).
Figure 2 displays an example of the neutral wettability of the modified LWC proppant. A drop of tap water and a drop of paraffin oil were deposited on two areas of the proppant pack surface. Both water and paraffin oil beaded on the new surface, showing that it is neither water- nor oil-wet. The new surface demonstrated no affinity for these two fluids.
Fluid Compatibility, Conductivity
Figure 3 shows the viscosity data of the cross-linked fluid that used linear gel containing 4.0 pounds per gallon of neutral wettability proppant compared with a base line that used water that did not contact the proppant and a control that used the same procedure as the neutral wettability, but with an LWC proppant in its native surfaces. The three curves are very similar and the viscosity performance of treated and untreated proppant is similar to the base line. This indicates that the neutral wettability LWC is compatible with the fracturing fluid and the fluid was not affected by any coating chemical. The neutral wettability proppant mixed very well with the gel and showed no aggregation.
Conductivity measurements before and after cleanup were used to determine the regained conductivity of the proppant pack after fracturing fluid cleanup to simulate flowback recovery using the 30/50-mesh LWC neutral wettability proppant and standard 30/50-mesh LWC proppant for comparison.
The regained conductivity data were generated under 2,000 psi closure stress and a temperature of 200 degrees Fahrenheit. During fluid injection and leak off, a total of 91 milliliters of filtrate was recovered. After low-rate water cleanup, the initial regain conductivity was 60 percent, and after high-rate cleanup, it was 61 percent. After cleaning up with only water for an additional 50 hours, this test had a “water only” regain conductivity of 61 percent and showed little sign of improving.
Following gas cleanup and further water cleanup, the final regain conductivity was 94 percent, showing that the pack retained almost all conductivity after cleaning from the fracturing fluid. After completing the test, the cell was opened and observed for any remaining gel and damage. No obvious signs of any residual gel or filter cake damage were observed within the proppant pack.
Case Study Well
For the deepwater Gulf of Mexico well application, no modifications were made nor additional equipment added in the completion operation with the neutral wettability proppant versus traditional proppant. The completion was performed by installing a 9 7⁄8-inch, 62.8-pound liner cemented across the productive interval. Drilling fluid then was displaced to clear, solids-free brine using wellbore cleanout tools and filtering until establishing only clean, solids-free brine.
Positive and negative tests were performed to establish wellbore integrity. The cleaning assemblies were pulled out of the well and a sump packer was set on electric line to establish bottom and depth correlation references. Tubing-conveyed perforating then was run to depth, and the zone of interest was perforated in an overbalanced mode. Once losses were acceptable and the wellbore was stable, the assembly was removed from the well.
The frac pack assembly then was run to bottom and set in place. The assembly consisted of:
- An external sump seal assembly;
- A shrouded sintered mesh screen;
- Blank pipe;
- Frac pack extensions;
- A frac pack seal bore packer (external and permanent components);
- An internal sump seal assembly;
- A mechanical sliding sleeve;
- Internal isolation tubing;
- A hydraulic production sleeve and double pin sub made up to frac pack extensions (internal and permanent components) along with wash pipe with pressure/temperature gauges;
- A mechanical sleeve shifting tool; and
- A frac pack service tool and packer setting tool (internal retrievable components).
Frac pack operations then began utilizing an offshore stimulation vessel to perform initial diagnostic circulating and injection rates. A prefracture stimulation was performed using a solvent system ahead of an organic/nonorganic acid blend, followed by an organic mud acid blend with an ammonium chloride overflush. All blends incorporated additives tested for compatibility and flowback properties.
During treatment, significant pressure responses were observed, indicating an effective stimulation. Immediately following the acid treatment, a minifrac was performed to measure formation properties, followed by a step-rate test to further evaluate formation properties, confirm the closure envelope and obtain treatment redesign parameters. The treatment schedule was based on modeling the observed formation responses and desired fracture characteristics. The frac pack was pumped at 18.5 barrels a minute, pumping a total of 65,194 pounds of 30/50-mesh neutral wettability LWC proppant, with a maximum concentration achieved through a ramped schedule of 10 pounds of proppant added per gallon.
Tip screen-out was observed with more than 650 psi of net pressure gained, although final wellbore screen-out was induced at 1 bbl/minute taking returns via the annulus and choke. The proppant placed into the formation was 1,116 pounds/foot measured and true vertical depth with 80 feet of excess blank height coverage in the wellbore. The excess proppant was reversed out and the service tool was removed from the well.
Completion operations then continued by installing the production packer and tubing with subsurface safety control valve, chemical injection mandrel and downhole pressure/temperature gauge assemblies. The tubing was landed in the horizontal subsea tree and tested. A total of 1,192 barrels of fluids was pumped during the prefrac stimulation and frac pack treatment.
Treatment Results
Once tubing was landed, the well was rigged up for flowback. Flowback data were recorded for more than 63 hours. Figure 4 shows water and oil recovery data. Water recovery increased for 14.3 hours and then plateaued. A total of 2,023.9 barrels of water were collected. After 11.2 hours of flowback, 1,192 barrels were recovered. The extra water recovery most likely was attributable to other fluids pumped and lost to the formation and water blocks that were opened.
FIGURE 5
Total Cleanup Time for Well using Neutral Wettability
LWC Proppant Versus Three Offset Wells
Figure 4 also shows the amount of cumulative oil recovered as a function of time. First oil was observed after 3.8 hours and continued to increase as more water was recovered. After 5.0 hours, oil recovery increased sharply. Both oil and water plateaued after 14.13 hours. During the job, it was observed that the flowback fluids were coming out of the well more quickly than normal for this field. In this area, the total stimulation fluid recovery time was approximately 24.5 hours using a rig.
Figure 5 compares cleanup time between the well that used the neutral wettability LWC proppant with three offset wells that used similar ceramic proppants in their native surface states. The well containing the neutral wettability LWC proppant cleaned up about 10 hours faster than offset wells containing similar proppants in their native states. Furthermore, in most cases, not all stimulation fluids were recovered from these wells, indicating that some fluids were still trapped in the proppant pack and creating some damage.
When the neutral wettability LWC proppant was used, data obtained from the deepwater well showed that all stimulation fluids pumped into the completion were recovered at the end of the treatment, which was a rare occurrence in surrounding deepwater fields.
In addition, more benefits were observed from shortening the cleanup time and first oil breakthrough. Since LLOG Exploration was using a rig for flowback, flowing back the stimulation fluids was quite expensive. This decrease in flowback time cut the period required to get the stimulation fluids back by 43 percent and enabled a much sooner breakthrough of first oil production. This created an economic benefit of saving 10 hours of rig time, compared with the three offset wells, and represented $438,000 in cost savings.
ERIK HOFFPAUIR is a completions engineer at LLOG Exploration. With 13 years of industry experience, he joined LLOG in 2012 as a completion engineer. He holds a B.S. in petroleum engineering from Louisiana State University and is a licensed professional engineer in the state of Louisiana.
NAIMA BESTAOUI-SPURR is product line manager, fracturing, at Baker Hughes, a GE company, and subject matter expert in proppants. Prior to this role, she served in research and development and technical services for proppants. Her recent work in new product development includes neutral wettability proppants, ultralightweight proppants and silica dust mitigation in fracturing. Bestaoui-Spurr has been with Baker Hughes, a GE company, for six years. She previously worked for a technology company developing new materials for a broad range of applications. Bestaoui-Spurr holds a Ph.D. in materials science from the Institute of Materials in Nantes in France.
DAVID STANLEY is a technical adviser for completion and stimulation pumping at Baker Hughes, a GE company. Before joining Baker Hughes in 2011, he held roles supporting completions for various service companies. He holds a B.S. in petroleum engineering from the University of Louisiana at Lafayette and obtained professional engineer licensure in 2016.
MARTY USIE is the engineering manager for the Gulf of Mexico pressure pumping production enhancement technical team at Baker Hughes, a GE company. He has 31 years of industry experience with a primary focus on production enhancement. Usie has served on the board of the Society of Petroleum Engineers Evangeline Section, and was a committee chair for the SPE International Symposium & Exhibition on Formation Damage Control from 2000 to 2014. He holds a B.S. in petroleum engineering from the University of Louisiana at Lafayette.
HANH NGUYEN is a research development and design scientist at Baker Hughes, a GE company. Hanh has 17 years of industry experience and holds a B.S. in biochemistry/biophysics from the University of Houston.
VANESSA WILLIAMS is a research and development manager in the pressure pumping international division at Baker Hughes, a GE company. With seven years of industry experience, she previously served as a product line manager for production enhancement, product development and portfolio manager for pressure pumping and upstream chemicals, and as information technology project manager. Before joining Baker Hughes in 2010, Williams worked in engineering positions at National Instruments. She holds a B.S. in biomedical and electrical engineering from Vanderbilt University.
For other great articles about exploration, drilling, completions and production, subscribe to The American Oil & Gas Reporter and bookmark www.aogr.com.