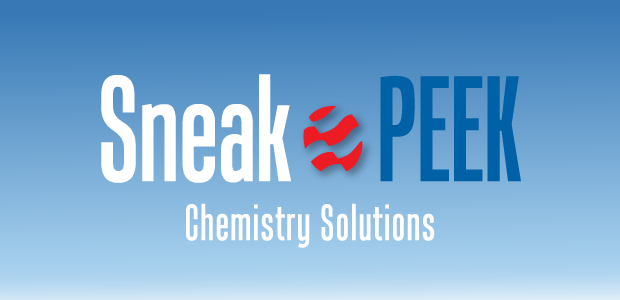
Novel Chemistries Combine Affordability With Huge Production Gains
By Colter Cookson
Throughout a well’s life, using the right chemistry can have a huge impact on near-term production, operating expenses and ultimate recovery. That is true whether the well is an aging vertical workhorse, a horizontal well that came on line two years ago, or a new well that is about to be completed.
In many cases, the best completion fluid for a well will use less chemistry, suggests Byron Cottingham, chief executive officer of Native Chemical LLC. “It can be easy to utilize a cookie cutter approach, completing well after well with a large chemical package designed to address many problems,” he says. “The repetition can provide some cost savings and efficiencies, but the overall cost and performance tend to be better when operators focus instead on optimizing the completion fluid for the application.”
That means conducting laboratory tests on oil, water and cuttings from the reservoir, as well as the source water for the completion.
Cottingham says the objective is to identify the most cost-effective surfactants, friction reducers, clay control additives, scale inhibitors and biocides for a given area. While performing such tests on every well may be unnecessary, he generally recommends testing at least one well from each drilling spacing unit.
“It’s hard to pin down how much optimizing chemistry affects a well’s performance, because there are so many knobs to turn during drilling, completions and production that also matter,” he acknowledges. “However, the type curves for the wells where we have done the analytics tend to be 5%-25% higher than similar wells in the same area.”
Over time, Cottingham predicts that tailoring chemistry will become even more effective. “As we do more testing in an area, we get a better understanding of each reservoir and target interval,” he says. “By our 15th, 20th or 50th well, we know more about the mineralogical interactions that are driving the performance and what may hinder production.”
In many wells, clay fines can be a major concern, Cottingham notes. “We are diving into migrating clays, which can create fines on the scale of 200 mesh to 600 mesh. Because the fines are smaller than most proppant, they can clog the fracture network. Having proper clay control that targets fines-generating clays rather than swelling clays can make a huge difference.”
To illustrate the potential extent of that impact, Cottingham cites a case study from the Eagle Ford that compared a fines-focused additive with potassium chloride, one of the most common tools for mitigating swelling clays. The new additive reduced turbidity during flowback by 350% and helped the well achieve higher production, Cottingham reports.
Scale Inhibition
Preventing or removing scale has been one of oil field chemistry’s major areas of focus for the past few years. “We are seeing huge improvements around scale inhibition,” Cottingham relates. “That is true whether the scale comes in the form of barium sulfate, strontium sulfate, calcium carbonate or siderite, which essentially is iron carbonate.”
Thorough testing can enable teams to tailor completion fluids to the application. Native Chemical LLC says this customization delivers huge performance gains, unlocking type curves 5%-25% higher than nearby wells with similar characteristics.
To decide which scale inhibition is best suited for a specific well, Cottingham says Native tests samples from offset wells, as well as the water likely to be used during fracturing.
“As always, optimizing the dosage is critical,” he comments. “We want to provide full scale control without any unnecessary expense.”
Maximizing scale inhibitors’ effectiveness often entails deploying them as solids that stay in the frac sand pack and gradually release their active ingredients. “We are seeing more companies adopt solid chemistries,” Cottingham says. “From residual testing at the surface, we know the treatments can stay effective for a long time.”
Depending on the application, the solids may be able to delay scale formation for three months or sometimes as long as 18 months. “Solid chemicals cost more than liquid equivalents, but the laboratory testing we have done and the results we have seen in the field suggest that the extra cost is worth it,” Cottingham says. “The savings from eliminating the need to pump inhibitors down hole early in a well’s life offset the upfront spending on the solid chemistry.”
Like clay and scale inhibitors, friction reducers are improving, Cottingham says. “There are many chemistry companies trying to tweak and modify polyacrylamide to simultaneously increase performance and minimize negative interactions with iron or other charged metals and clays,” he reports. “These interactions limit the friction reducer’s effectiveness. In extreme cases, they can create gummy bears that accumulate down hole or cause problems for surface equipment.
“Native is working on a few FRs that use less polymer,” Cottingham adds. “They perform well at reducing friction, but they also have a much higher iron tolerance, which should minimize negative interactions.”
Past the completion stage, Cottingham says the company is experimenting with ways to enhance acid treatments. “For example, we have been playing with the rate we pump the acid down hole and using new diverting agents to distribute the acid across stages more effectively.”
Sand Consolidator
For Amr Radwan, co-founder and chief technology officer of TenEx Technologies, nanomaterials have been an endless source of joy. “No matter how much we learn, nanoparticles still surprise us,” he marvels. “We can have the exact same material, but if we change the particle size from 60 nanometers to six, we see different behavior. By studying that behavior, we often come up with novel ways to solve problems.”
He encourages researchers to have fun in their pursuits instead of focusing on specific business objectives in a way that clouds their ability to see anything else. “One of our most exciting new technologies, a low-cost sand consolidator, came 100% through discovery,” he relates. “We were mixing chemicals for something else, then noticed unusual interactions and tried to figure out what was going on.”
That curiosity ultimately led TenEx to develop a treatment for unconsolidated sand that Radwan calls so easy to deploy it can be applied to wells that only produce five or six barrels a day, if that. “We have treated some wells that were scheduled to be plugged, because every time the operator tried to bring them on line, sand would fill the wellbore to the pump within three days,” Radwan recounts. “Today, those wells have gone from being a liability to producing 600-700 barrels of fluid a day with a strong oil cut.”
A nanoparticle-based sand consolidation treatment has proven extremely effective in both the lab and the field, TenEx Technologies reports. The company adds that the treatment excels at reviving marginal wells because it has low costs and few risks.
Some of those wells have produced continuously, while others began making sand after a few months and had to be re-treated, Radwan relates. He says the economics hold up either way. “The treatment is rigless, so in many cases, operators get their money within a week,” he says.
The treatment works by mixing an atomized aluminum dispersion with water and pumping it down hole. “The aluminum deposits on the surface of loose material, which can be proppant or unconsolidated sand. We send activators with or after the atomized aluminum dispersion to oxidize the aluminum in situ and trigger a reaction that causes the loose material to bond together,” Radwan describes.
According to Radwan, this approach is less risky than using traditional sand consolidators, which generally rely on sticky resins. “Resin likes to coat everything,” he observes. “Even when the job goes smoothly, it can get into the formation and significantly reduce permeability. If something happens and the resin sits in the well, the damage could be so severe that the well is lost.
“With the atomized aluminum dispersion, the consolidation takes some time to occur,” he contrasts. “If the job has a hiccup, we can simply wait to deploy the activator or circulate the materials out of the well before it consolidates. And if we overtreat the well and lose too much permeability, we can pump down chemicals to reverse the bonding process.”
Radwan adds that the sand face does not need cleaning ahead of treatment, which helps reduce costs. “The other major advantage we are excited about is that the aluminum can work in almost any temperature,” he details. “It can withstand more than 1,600 degrees Fahrenheit, which is higher than the melting point of the proppant. The high temperature tolerance will let operators in hot plays go from removing sand with expensive mechanical treatments to consolidating it with chemistry.”
The aluminum-based sand consolidator is new, Radwan notes. “We started doing field trials in California, an area where many wells see massive sand production. We also are treating tight sandstone wells in Louisiana and mature wells in Canada, and we are just beginning to pump in the Permian Basin,” he reports.
Eventually, TenEx hopes to deploy the technology in horizontals, Radwan indicates. “We are in talks with several operators about applying the technology to their new fracs as a way to limit proppant flowback,” he says. “In laterals, the key will be figuring out how to place the chemistry. If we can get it to the right area at an affordable cost, it should work well.”
Experimentation
Radwan expresses appreciation for operators that encourage their engineers to test new ideas and have the patience to develop them. Even with rigorous lab testing, he says no solution works optimally during the initial deployment.
“We want purchase orders as much as any business, but we get far more when we are honest about a technology’s limitations and risks,” he reflects. “In many cases, the smart engineers on the other side of the table respond to that transparency by working with us to come up with solutions.”
Research and development can slacken when prices fall or activity heats up, Radwan acknowledges. However, he says the long-term benefits of maintaining it can be impressive.
As a case in point, Radwan cites a slurry containing tiny fragments of glass-quality microsilica that helps prevent screen-outs during completions. “When the slurry hits the perforation, it acts like a scouring agent,” he describes. “It makes the perforation easier to enter by eroding irregularities and reduces near-wellbore fracture tortuosity, which lets the pumps get to rate more quickly and improves cluster efficiency.”
In one study, the microsilica saved an average of seven minutes a stage and cut screen-out risks from 2.9% to 0.7%, Radwan recounts. Across a year, he estimates its use saved each frac crew 20-30 days.
Solid Chemistry
Scale inhibition is only one of many applications for solid chemistry, says Troy Todd, segment director of the Enduro-Tech chemical manufacturing segment of Energy & Environmental Services (EES). However, he acknowledges that it is one of the most important.
“In the Mid-Continent, operators’ most common question is what we can do about scale,” he relates. “Once scale forms, it can be a major pain. With barium scale, the only real way to remove it is to do something mechanical, which is expensive.”
These buckets contain solid chemistries that gradually release their active ingredients down hole to provide lasting protection, Energy & Environmental Services describes. The rate of release varies based on several factors, such as the solid carrier and the environment, but the company says its scale inhibitors usually last 10-18 months.
To address barium and many other scales, Enduro-Tech offers a BHMT phosphonate scale inhibitor that Todd describes as effective. “It does a great job of handling a range of situations, especially in the Permian,” he says. “Under certain conditions, it will prevent barium formation.”
In its solid form, the inhibitor can provide lasting protection, Todd adds. “A solid scale inhibitor generally lasts 10-18 months, but we have seen some go as long as two years,” he clarifies. “The longevity depends on several factors, such as the inhibitor, downhole temperatures, oil composition and water composition.”
Paraffin inhibitors and demulsifiers tend to release more quickly, Todd continues. “They usually last four-eight months, but again, we have encountered certain wells where we continue to see residual chemicals 12 or sometimes 14 months after the treatment.”
The technology underlying the gradual release is sufficiently flexible to work with many chemicals, Todd mentions. In fact, he says operators occasionally ask EES to solidify a liquid chemical that works well in their field so they can benefit from the slow release.
By volume, solid chemicals have a lower activity level than their liquid counterparts, Todd notes. “Depending on the carrier we are using, our activity runs somewhere between 60% or 73% of the liquid chemical’s activity,” he details. “That is almost double what many solidification techniques can achieve.”
Novel Frac Job
Even without such high activity, Todd indicates solid chemistry can offer meaningful logistical advantages. That is one reason an operator asked EES to perform two frac treatments last summer with completion fluids made almost entirely of solids, he recounts.
“We provided the surfactant, scale inhibitor, clay stabilizer and demulsifier as solids,” Todd describes. “The operators’ engineers had us design the surfactants to come out gradually rather than immediately covering the formation, as they believed the slight delay would help protect the formation face.”
The completions did use a liquid biocide, Todd says, but that was only because none of the registered biocides could be adapted into a solid without voiding their registration. Both completions went well, Todd reports. Although one well had unrelated surface equipment issues that limited its production, he indicates the other is delivering strong performance a year later, with minimal production service required.
“The solid frac jobs’ success is very exciting,” he says. “We sell liquid chemicals, so I know how much volume has to be shipped to a traditional frac site. Today’s laterals may require 25,000 gallons of surfactant, enough to fill five ISO tanks. The other additives also require tanks to be pulled in and out of location.
“With a solid chemistry, we can replace each tank with six-eight pallets that are much easier to ship and handle,” Troy contrasts. “For some wells, an operator may be able to fit every pallet necessary into a single box trailer. That reduces costs and shrinks the on-site footprint.”
During winter, solids eliminate the need to add methanol or other antifreezes to the chemicals, Todd mentions. In addition to reducing costs, he says this change can improve health and safety.
“With a solid, spills are easy to clean up,” he continues. “All someone has to do is sweep it up and put it back in the drum. Unless it happens to land in a stream or puddle, it is not going to start releasing, so there is no need to stop the operation or call a Hazmat team.”
Next Steps
While he expresses pride in today’s solid chemical capabilities, Todd suggests they still have plenty of room for improvement. He says EES is in a good position to unlock some of that potential thanks to a change in management.
“In July 2024, we had a complete turnover in upper management. Our new board of directors and CEO, Gerald “Jerry” Eaton, are bringing in intellectual property to enhance our capabilities and helping us broaden sales areas,” he explains. “Jerry has more than 40 years of experience in the oil and gas industry and is a leading authority on pipeline drag reducers. He has several patents on these products and is bringing this technology to EES.”
The new team is investigating how to mill solid chemical carriers in house, Todd says. “This will let us experiment with different types of carriers, then mill the finished product down to exactly the particle size we need,” he enthuses. “That should improve the activity level and consistency.”
In the past, Todd says, the company had to buy materials from other industries and settle for substances that approximated its parameters. In some cases, it abandoned otherwise promising material because of size limitations.
“Particle size can be significant,” Todd emphasizes. “In a completion application, our solids go in with the sand and water. If they are too large, the sand will crush them, but if they are too fine, they will fall before they reach the perforation.
“With more control over particle size, we should be able to engineer the solid chemicals to reach the perforation and travel as far back into the formation as possible,” Todd illustrates. “As the treatment releases, it will interact with the formation rather than washing over a specific point, which should enhance its effectiveness.”
Augmenting Acid
When wells age or fall short of expectations, it can be tempting to try restimulating them with hydrochloric acid, says Michael Lantz, co-founder and president of Kairos Energy Services. After all, HCL has a long history of success in vertical wells, where it can increase permeability by dissolving carbonates and scale.
To restimulate wells, Kairos Energy Services says it augments traditional acids with chemical blends that target several production impediments. This graph tracks production from a 2018 well in the Denver-Julesburg Basin that received a treatment designed to improve relative permeability, restore conductivity and remove scale. According to Kairos, the treatment paid for itself within four months by boosting both oil and gas production.
But in many shale plays, Lantz cautions, traditional acid treatments deliver inconsistent results. Acid excels at dissolving carbonates and some scales, but often has a limited effect on formations that are made from other minerals. When reservoirs do contain carbonates, the sheer volume required to contact them can add too much cost for acid to be economic, he explains. To improve consistency in shales, Lantz recommends pairing a much smaller amount of acid with a chemical blend that is designed to address multiple damage mechanisms.
“With this approach, operators often see a 30%-60% increase in production rates and an uplift in estimated ultimate recovery around 30%,” he reports. “On average, payback occurs in four months.”
According to Lantz, the treatment works by achieving several goals simultaneously. “First and foremost, we utilize surfactants to alter wettability, improve relative permeability to oil and gas, and clean up the fractures,” he begins. “In many wells, we also try to deal with gummy bears, scale or paraffin.”
To maximize the chemistry’s effectiveness, Kairos relies on diverters, Lantz notes. “We can distribute the treatments across fractures by pumping higher volumes, but that is costly, especially in a long horizontal,” he says. “Diverters let us contact each frac stage more efficiently and reliably.”
Diversion can be so impactful that Lantz indicates Kairos is refining its approach. “Previously, we used polylactic acid-based diverters by themselves,” he recounts. “PLA diverters are rigid particles of various sizes. For them to work well, the sizes need to be almost perfectly distributed. That is hard to do, so we often saw leakages through the diverter pack.
“As a next step, we decided to a mix PLA with a swellable polymer. As the polymer swells, it becomes deformable and malleable, which lets it fill in the gaps between the PLA particles,” he describes. “Meanwhile, the particles provide mechanical strength. After more than 100 drops in the field, we know this combination leads to more consistent diversion.”
Getting Past the Wellbore
While reliable diversion can enhance chemistry’s effectiveness, that chemistry still needs to be pumped at a meaningful volume to address problems beyond the wellbore, Lantz reflects. “By looking at the amount of proppant that was pumped, we can estimate the frac pore volume that remains open ahead of a treatment,” he says. “For a relatively normal modern completion in the Eagle Ford, there is enough space that it will take at least 10,000-15,000 barrels of fluid to fill it.
“That is prohibitively expensive with a treatment composed almost entirely of hydrochloric acid. Even 1,000 barrels of HCL perfectly distributed across the wellbore would only contact about a tenth of the propped fractures,” he says. “By using more affordable chemistry, we can pump 15,000 barrels of fluid. This allows the treatment to contact the propped volume and forces some fluid into the rock matrix.”
To demonstrate the possibilities associated with efficient chemistry, Lantz points to gummy bears. “It’s common to try dissolving gummy bears by combining HCL with citric acid,” he says. “As we have worked to optimize our treatments, we have discovered alternatives. Instead of paying for 10% citric acid, we can use a different chemistry at a concentration of only half a percent and still dissolve and disperse the same solids.”
In the past three years, Kairos has treated more than 65 wells. According to Lantz, most of those wells are in the Denver-Julesburg Basin, the Mid-Continent and the Eagle Ford, though the company entered the Permian Basin in the second half of 2024. Because deploying the treatments usually only requires two 2,500 horsepower pumps and a blender, he says they are extremely economic.
Leveraging Hydrocarbons
Many common damage mechanisms can be remediated by pumping a mixture of liquid hydrocarbons and chemicals down hole, says Tadd Wallace, president of C3 Oilfield Services. “We are doing jobs to clean out paraffin, remove condensate blockages and force water out of swelling clays,” he illustrates.
Depending on the well, the mixture can contain propane, butane or even heavier natural gas liquids. “For clay swelling, we often use propane with an added surfactant mixture,” he notes. “This mixture will liberate the water from the clay. The surfactant coats the surface to keep the clay from swelling again.”
By pumping a mixture of liquid hydrocarbons and chemicals down hole, C3 Oilfield Services says it can address paraffin, condensate blockages, clay swelling and other issues. Because the treatments work well and consist largely of hydrocarbons that can be resold, C3 reports they provide quick returns.
To explain why hydrocarbon-based fluids work on paraffin, Wallace compares them with xylene. “Propane, butane and natural gas liquids are solvents, so like xylene, they can solubilize the paraffin that has crystalized in the wellbore,” he says. “However, we are getting much longer-lasting results. With xylene, it may cost $3,500 or $4,000 to pump five barrels down hole. For the same price, we can pump 50 barrels of our fluid with paraffin inhibitor chemistry.”
The extra volume sends the treatment into the formation, Wallace says. “In the process, the hydrocarbon-based fluid breaks up the paraffin that already has crystalized,” he details. “Once the paraffin is in solution, a wax crystal modifier additive prevents it from precipitating out again. The modifier works so well that instead of doing a paraffin treatment every month, we may only need to come out every six-12 months.”
In some wells, visiting more often may be worthwhile, Wallace mentions. “For example, we are developing a treatment for horizontal Austin Chalk wells with wax issues,” he says. “They produce enough oil to potentially justify going back to the same well more frequently.”
Even treatments on more modest wells can deliver fast paybacks, Wallace relates. “On average, a treatment will pay for itself in 30 days, with some customers seeing their money come back within the first week,” he details.
The rapid return is partly attributable to low costs. “For about $20,000, we can treat four wells a day,” Wallace says. “The beauty is that half the cost is for the hydrocarbons we are pumping down hole. When those hydrocarbons come back up, the operator can sell them to recoup part of the cost.”
To ease that process, Wallace says C3 tailors its fluids to each site’s production facilities. “For an oil well that does not have a gas sales line, we will use a condensate so heavy that it is almost oil,” he details. “This gas will expand inside the tanks once it returns to the surface, but not enough to create pressure issues.
“For wells with gas sales lines, we can pump a propane or butane,” he continues. “These lighter gases have a lot of energy to lift liquids out of the well.”
In late September, Wallace said C3 had treated 10 wells in 2024. For the fourth quarter, it has 110 wells on the schedule. “We are building a track record, and as people become more comfortable with our technology, the work has accelerated,” he reports. “We have two new units rolling out, which will let us go up to three crews.”
Safe Equipment
When operators consider C3’s technology, Wallace says they initially voice safety concerns. “We have never had a safety incident,” he assures. “That comes from the emphasis we put on training and understanding the fluids we work with, as well as the way we design our equipment.”
Each fleet contains trailer-mounted triplex pumps, a tank for the fluid and a high-pressure injection line that connects the pumps to the wellhead, Wallace describes. The crew consists of three people: an operations expert who monitors the entire job, a driver who switches to optimizing performance during the job, and a second operator who manages the equipment as its pumping. Noting that these workers tend to be former fracturing crew hands, Wallace says they control the entire job from an explosion-proof cabin.
“To detect leaks, we put gas sensors around the well, along the fluid transfer lines and on the pump. We also have a thermal camera watching the pump to detect any propane or butane mist,” Wallace details. “If something happens, the system automatically stops the job. It activates valves to isolate the wellhead from the chemical supply line, shuts off the pumps, and even kills the tractor’s engine.”
Although most of C3’s treatments so far have been in vertical wells, Wallace says it has seen promising results in horizontals. “We are working on refining the technology for horizontals,” he says. “The main challenge is figuring out how to surgically place the treatment in each perforation so we can keep the fluid volumes down but still get the treatment into the formation where the damage is.”
For other great articles about exploration, drilling, completions and production, subscribe to The American Oil & Gas Reporter and bookmark www.aogr.com.