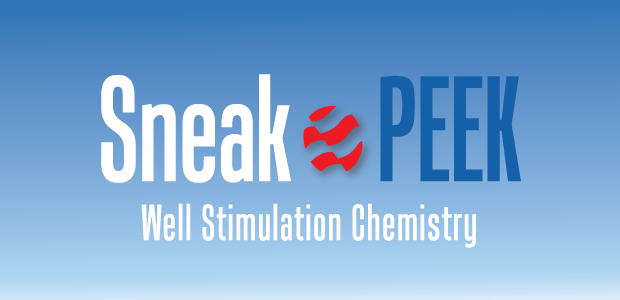
Novel Chemistries Increase Wells’ Output And Simplify Operations
By Colter Cookson
According to the Independent Petroleum Association of America, the United States contains about 1 million oil and gas wells, including 750,000 low-volume wells. With strong commodity prices raising the value of every incremental barrel of oil and cubic foot of gas, many operators are looking for ways to get more from these assets.
Oil field chemists are answering the call. By refining best practices for proven techniques and inventing new ones, they are helping operators turn old wells into big money makers. The emerging restimulation techniques frequently combine attractive economics with simple deployment processes that minimize equipment and labor requirements, as well as emissions.
There is plenty of upside to be found in mature fields, affirms Franz Ronnie, founder, chief executive officer and president of Merica Oil Co., a privately-held independent that works to acquire assets that combine existing production and infrastructure with strong growth potential. “We are seeing so many acquisition opportunities that we have had to slow down and turn even strong projects away,” he reports.
Merica owns wells in the Kansas counties of Barber, Rooks and Comanche and the Oklahoma counties of McClain and Garvin. Ronnie says the company is boosting cash flow from these wells through workovers. “I have been fortunate to gather smart individuals around me who have the experience to evaluate growth opportunities and the humility to question their assumptions,” he reflects, noting that these include engineers, geologists and operations experts from Devon, Shell and BP.
Embracing Technology
Merica is working with Green Horse Energy to restimulate wells by injecting the fertilizer anhydrous ammonia. “When the ammonia interacts with water down hole, it expands rapidly and creates microfractures that help oil flow to the wellbore,” Ronnie explains. “Even the first job with us delivered a remarkable production increase at a low cost. We are excited about the technology’s potential and plan to help Green Horse Energy perfect it.
“We are big believers in using digital technologies to reduce operating costs,” Ronnie adds. “We store information on the cloud and use the GreaseBook app to simplify pumpers’ work, and we are digitizing many of our tank batteries. The digitization will take time, but it should have tremendous long-term benefits.”
Ronnie says Merica looks at opportunities to mine cryptocurrencies such as Bitcoin and Ethereum. “If a well produces enough gas–say 500, 2,000 or 5,000 Mcf a day–it can make sense to connect that bad boy to a generator and set up computers to crank out crypto,” he relates. “This can increase revenue from $3-$9 an Mcf to $10-$50 an Mcf. It’s also amazing to help enable digital currencies and a modern way of conducting transactions.”
By applying workover expertise alongside emerging chemistries, the privately-held independent Merica Oil is boosting production from mature wells. Merica’s current assets are in Kansas and Oklahoma, but the company says it sees compelling upside potential in plays across the United States.
When wells age enough that they become candidates for plugging and abandonment, Ronnie recommends checking to see if they generate enough heat to be converted to geothermal service.
By combining technical expertise and meticulous evaluations with a belief in searching for and experimenting with new technologies, Ronnie says Merica hopes to grow exponentially. “My partners and I want to turn Merica into a massive company,” he says. “In 10 years, we would like to sit at the same table as Pioneer Natural Resources. Eventually, we want to become a global company.
“In every area we operate, we want to have a positive footprint,” he comments. “For example, we acquired several wells in Oklahoma. As our operations and revenue kick up, we plan to look for ways we can support the community, such as donating to local fire departments or the Chamber of Commerce.”
Ronnie points out that Merica has donated to the police department in Midlothian, Tx., which has a mental health crisis unit that supports veterans, police officers and civilians. “Helping people is personal to me,” he says.
Fertilizing Oil Production
One of the emerging technologies that is helping Merica Oil and other companies boost production from mature wells is a restimulation technique that involves injecting liquid anhydrous ammonia (NH3) into the reservoir, says Chance Bland, the founder and managing partner of Green Horse Energy.
“When NH3 encounters water, a chemical reaction occurs that generates heat,” Chance relates. “As the liquid ammonia heats up, it expands 30 times and generates enough pressure on the rock to create microfractures that give oil new pathways to the reservoir. At the same time, the heat and expansion pressures restore permeability in existing fractures by melting and breaking up paraffins, scales and emulsions.
“The chemical reaction that produces these effects transforms the NH3 into ammonium hydroxide,” he adds. “When ammonium hydroxide mixes with hydrocarbons at a molecular level, it can break down the acids they contain to make a surfactant that will help the hydrocarbons move out of the well.”
The first well Green Horse Energy treated produced only nine barrels of oil and 10 Mcf of gas when it came on line in 1984. In the three years before receiving NH3, it made less than a barrel of oil and no gas each day, Bland describes. In the 15 days following the treatment, he reports, it produced 168 barrels.
This data comes from one of the first wells treated with liquid anhydrous ammonia (NH3). According to Green Horse Energy, the production gain occurs because NH3 heats up and expands when it encounters water, allowing it to remove paraffins, scales and emulsions while generating microfractures.
The company’s second job targeted a 75-year-old well in Creek County, Ok., that produced 2.5 bbl/d and 5 Mcf a day. “The treatment caused oil production to hit 35 bbl/d,” Bland reports. “Even after four months, which included some downtime from lightning striking the tank battery, production was still twice what it was before the treatment.”
As of early July, Green Horse had treated four wells with NH3. “The flush production from the treatments is strong enough to pay for the costs within a month,” he says. “This was true even for the treatments we did last year, when prices were lower.”
Bland attributes the process’s rapid payback in part to the speed at which it is deployed. “To put the ammonia down hole, we pump a scale inhibitor or oil pad, the ammonia itself, a second pad of oil or scale inhibitor, and finally a water tail. The pads keep the ammonia from reacting with water in the formation prematurely, while the tail pushes the ammonia into the formation,” he describes. “From setting up the pump to rigging down, the entire process takes about four hours.”
Noting that the pads and ammonia can be pumped down hole with a 600-horsepower triplex pump operating below capacity, Bland says the process produces minimal emissions. He mentions that most of the jobs involve about 10 tons of NH3, each of which is equivalent 557 horsepower hours.
The idea of using liquid ammonia to boost oil production came to Bland as he was thinking about ways to reduce emissions. “I worked in regulatory compliance for SandRidge Energy, Devon Energy and Ascent Resources long enough to predict that emissions limits would get stricter with time, so as I was driving to my parents’ house, I was asking myself how the industry could produce more with fewer emissions. Then I looked out the window and saw a farmer fertilizing his field with anhydrous ammonia.”
Because his father and grandfather owned a company that manufactured equipment for applying NH3 on farms (which involves injecting it below the surface so it bonds with the soil rather than evaporating), seeing the farmer at work was enough to spark an aha moment. “From growing up around the factory, I knew NH3 expands and heats up when it encounters water. At the surface, keeping water away from NH3 is vital. But down hole, the same reaction could be beneficial,” Bland relates.
He points out that ammonia is made in the United States using water, air and natural gas. While ammonia can corrode brass, copper, and galvanized steel, it is noncorrosive to the stainless steel, plastic and rubbers often used in oil wells, Bland says.
“When a well is treated with NH3, the water it produces contains ammonium hydroxide, one of the cleaning agents in Windex®,” Bland mentions. “When an operator decided to inject the produced water into an on-site saltwater disposal well, the water cleaned out the well and reduced injection pressures from 17 psi to a negative number. In other words, the SWD became a vacuum, which meant the operator could inject water with less pump time, wear and tear, and energy.”
Blocking Water
As oil prices have risen, so has interest in using polymer gels to improve production, reports Randy Prater, founder and CEO of Polymer Technologies. “We are living in exciting times,” he assesses. “At today’s prices, even some of our largest water shut-off jobs sometimes pay off in days. If not, they will pay off in only weeks.”
According to Prater, water shut-off jobs owe their strong economic benefits to advances in chemistry and expertise. “In 1989, when I first became involved in using polymer gels to control water cuts, less than half the jobs succeeded,” he recalls. “Today, the success rate exceeds 90%. Almost every job yields incremental oil production while reducing water production 70%-90%.
Using polymer gels to create barriers that block water can boost wells’ hydrocarbon production and minimize water production. According to Polymer Technologies, typical water shut-off jobs reduce water cuts 70%-90%.
“Over the past year, we have been pumping chemistries during water shut-off jobs that change the formation’s wettability to release oil droplets from the formation’s surface. This improves oil production once the water pathway has been blocked,” Prater mentions. “Add in other improvements, and a typical shut-off treatment will deliver 25,000 barrels of incremental oil within the first year and cut saltwater production an average of 80%.”
These benefits are attributable to the fact that blocking water-bearing zones allows bottom-hole pressures to act on other areas and mobilize bypassed oil. Water shut-off jobs work best in wells with a strong water drive and enough original oil in place for accessing new areas to be worthwhile, Prater advises. He points out that polymer gels also can be used to control water’s flow and mobilize bypassed oil in waterfloods, and to repair casing leaks.
Performing a water shut-off job involves several steps. “We need to isolate the formation we want to block,” Prater begins. “On a producing well, operators will bring a pulling unit or workover rig on site to pull the downhole pump assembly, rods and tubing, test the tubing, and clean the bottom of the hole to make sure there is no silt or iron sulfide packing off the formation from which they are producing. Then they will run back in with a retrievable packer on tubing to isolate the water-bearing formation.
“We almost always recommend a pre-polymer acid stimulation,” he continues. “The goal is to clean the channels where we expect the polymer to flow. If those channels are blocked by oil, water or scale, the polymer can end up hardening in other areas, including productive zones.”
Prater adds that the acid can boost post-treatment production by fracturing the rock. He says most pre-polymer acid jobs involve pumping 3,000-5,000 gallons of acid at a high rate.
“After the stimulation, we will inject polymer for four or five days,” Prater says. “A typical Kansas Arbuckle well will take 6,000-8,000 barrels of polymer. We used to inject much lower volumes, but over time, we have discovered that the further we get the polymer from the wellbore, the more drainage area it will affect and the more oil we can recover.
“In Kansas, for every barrel of polymer pumped, the operator recovers 10 barrels of oil,” Prater estimates. “If we pump 8,000 barrels, the customer could potentially recover 80,000 barrels of additional oil from that treatment.”
After several years, the water cut often returns to its pretreatment level, Prater notes. “As oil exits the wellbore, water often fills the pore spaces it leaves behind,” he explains. “Eventually, the well will produce that water unless we isolate it by adding another gel barrier.”
In wells targeting larger, thicker formations, including some in Kansas’ Bemis-Shutts Field, water shut-off jobs have unlocked additional oil even after five or six repeat treatments, Prater says. In thinner formations, the treatments may only work two or three times.
Unlocking Residual Oil
While water shut-off jobs have a long history, Prater suggests their potential remains largely untapped. He says one of the most intriguing applications involves residual oil zones (ROZs) in Wyoming, which the University of Wyoming’s Enhanced Oil Recovery Institute has found contain bypassed pay. “The oil saturation in these zones is low, but the intervals have a huge vertical extent,” Prater describes. “Across the nation, ROZs could hold millions or billions of recoverable barrels of oil.
“In the past, no one wanted to touch these zones because they knew they were going to produce a lot of water alongside the oil,” Prater recalls. “Today, we can handle the water. We have clients in Wyoming who are using polymer treatments to limit water production and unlock intervals full of mobile oil that are up to 600 feet long.”
According to Prater, West Texas offers similar opportunities. “There is renewed interest revisiting conventional wells to recover oil from the ROZ,” he says. He adds that Polymer Technologies is helping West Texas operators reduce water cuts in wells targeting the San Andreas, Grayburg and Ellenburger formations, to name a few.
To capitalize on growing interest in polymer gels, Prater says the company is expanding its fleet through acquisitions and newly built units. “We are building state-of-the-art equipment with automation that should give us greater control over polymer hydration and gel formation,” he details. “This equipment should increase efficiency during the job and help us ensure the gel has long-term stability once it is down hole.”
Some of the new automated units will be small enough to be placed on a trailer and moved with a half-ton pickup, Prater reports. “These small units are targeting applications in eastern Kansas,” he says. “Treatments there do not increase production enough to justify bringing a crew and high-capacity equipment on site. Using automated, smaller-scale equipment and having one person monitor several jobs remotely will let us bring costs down enough to make treatments attractive.”
These low-cost treatments will yield huge dividends, Prater predicts. “Historically, water shut-off jobs have been successful in eastern Kansas,” he says. “The slam dunk jobs increase production from half a barrel a day to 15 bbl/d.”
Prater points out that many Kansas wells produce a few barrels of fluid a day, too little for even a low-volume water shut-off treatment to make sense. He says emerging nanofluid technologies may be able to improve these wells’ economics.
“Because of paraffin and asphaltenes, some of these wells have to be periodically pulled and cleaned,” he notes. “To keep paraffin from forming and mobilize more oil, we are seeing a movement toward injecting nanochemistries into the formation to alter its wettability. The goal is to remove paraffin and improve wettabilities to release more oil from rock surfaces so it can be produced.”
These nanochemistries are new enough that the results can be inconsistent, but in the right wells, Prater says they can be impressive. “I have seen wells go from 1.5 bbl/d to 3.5 bbl/d and sustain that production for months,” he illustrates. “For a treatment that only costs a few hundred dollars, that is a big deal.”
Nanotechnology
TenEx Technologies formed in 2016 to develop tailored nanoparticle-based fluids for improving oil field economics, says Amr Radwan, the company’s chief technology officer. TenEx’s products include nanofluids for remediating organic formation damage, such as paraffin and some forms of scale.
The fluid excels at removing paraffin and other organic damage because it combines chemical reactions with mechanical force, Radwan assesses. “The fluid contains nanoparticles as small as 3-11 nanometers. Through a process called Brownian motion, these particles vibrate and move around. As they do so, they pierce the organic material and dislodge it from the rock’s surface by applying disjointing pressure,” he explains.
These Berea sandstone discs were saturated with West Texas oil and kept inside Amott cells at ambient conditions for 24 hours. The one on the right shows how effective nanofluids can be at mobilizing oil, a capability that TenEx Technologies reports is delivering long-lasting production gains across the United States and abroad.
As it breaks up organic deposits, the nanofluid leaves behind a coating that keeps other deposits from accumulating, Radwan says. “The coating lasts long enough that we have had wells show almost no decline in production two years after we deployed the nanofluid,” he says. “This indicates the treatment not only removed the paraffin but kept it from returning.”
The coating alters the rock’s wettability to make it more attractive to water and less attractive to oil, Radwan adds. “In many wells, the more water-wet surfaces reduce water cut 2% or 3%, which is enough to change the well’s economics significantly,” he says. “The treatment also seems to keep the water cut from increasing over time, or at least slows the rate at which it increases.”
According to Radwan, the nanofluid has restimulated more than 200 wells. “In the United States, we have pumped the product in almost every basin, including the Williston, Powder River, Denver-Julesburg, SCOOP/STACK and of course the Permian. We also have run it in Canada, the Middle East and China,” he details.
The product shines in California, Radwan adds. “It’s a green, water-based fluid that can be pumped down the well’s backside using low-horsepower equipment,” he explains. “Usually, pumping only takes one or two hours. A long well may require four or five hours, but even then, the emissions are minor.”
The treatment can be pumped by itself if most of the damage comes from organic deposits or wettability issues. If the well also contains inorganic damage, Radwan recommends pairing the treatment with an acid job.
The payback from removing damage can be quick, Radwan assures. “In the best wells, payback can happen in a week or two,” he says. “In others, it may take two or three months to see clear evidence of the treatment’s benefits.”
Targeting Chemistry
According to Radwan, one of the keys to maximizing the nanofluid’s benefits is deploying it in the right wells and tailoring the formulation to the downhole environment. He says the slower paybacks generally occur in wells with damage the nanofluid is not designed to address.
“There is no silver bullet in oil field chemistry,” he stresses. “For chemistries to be effective, they need to be targeted at the problems a specific well is experiencing. Unfortunately, production engineers must often infer problems from conflicting signals. In the United States, most engineers oversee too many wells to dig deeply into the signals from one well.”
As interest in restimulating aging wells grows, Radwan predicts that tools for diagnosing issues will become more efficient. “This is an area where artificial intelligence and chemistry can go hand in hand,” he assesses. “If operators feed well data into an appropriately-built neural network, we may be able to predict which wells will have problems, when those problems will occur and what form they will take.”
The more information chemical providers have, the better, Radwan says. “When we know the problem we are trying to solve and the environment it’s in, we can run simulations in the lab and deliver a successful treatment almost 100% of the time,” he relates.
Radwan indicates TenEx plans to extend its nanotechnology beyond its current applications, which include stimulating wells and protecting parent wells from frac hits. “For example, we are investigating whether nanoparticles can augment corrosion inhibitors,” he says. “Most inhibitors work by coating the surface to create a barrier between it and the corrosive materials. If the inhibitors fail to bond with the surface, they will be ineffective.
“Many of our nanoparticles are magnetic, so they may be able to help inhibitors attach to metal surfaces,” he suggests. “In lab tests, we have even seen cases where the nanoparticles coat the surface and provide corrosion protection by themselves.”
The company also is looking at using nanoparticles to remove wax and paraffin from tubing rather than targeting the formation, Radwan shares. “In the second half of the year, we hope to introduce a water-based nanofluid that dissolves paraffins and wax inside tubing, then coats the tubing to keep them from resolidifying,” he says. “We think it will be a game changer, because it will offer a safe, environmentally friendly, and long-term solution to a common problem.”
For other great articles about exploration, drilling, completions and production, subscribe to The American Oil & Gas Reporter and bookmark www.aogr.com.